WM Thermoforming Machines, Stabio, Switzerland, incorporated last year in the United States as WM Thermoforming Machines Inc., has developed a new line of single-screw extruders as an upgrade to standard equipment for its Intec systems combining in-line extruders and thermoforming machines.
The new N.EXT extruders are designed to deliver more production and processing benefits compared to the extruders in the Intec series that they are replacing, says Luca Oliverio, sales director.
The Intec systems are designed for the high-speed production of disposable thermoformed products such as cups, plates, yogurt containers and tubs. "The Intec series is not a sheet line but a complete system featuring the extruder and thermoforming system," says Oliverio. (At present, N.EXT extruders will be available only with the Intec series.)
SCREW DESIGN A KEY UPDATE
Initially, screw diameters of 45, 75 and 90mm, each having an L/D ratio of 36-to-1, will be available in the N.EXT line. A key development is the new screw design, which allows the machine to process PP at rates ranging from about 990 to 1,980 pounds per hour.
The screw for the N.EXT extruder has a smaller diameter and therefore requires less energy to power than the previous screw designs and is run at higher speeds for increased output. In addition, the design of the screw allows the machine to melt the material better. WM Thermoforming devoted particular care to the screw profile to achieve optimal material homogenization and plasticization.
"An older 120mm extruder that processed 650 kilograms of material an hour will be replaced by a newer, smaller 75mm extruder that can process 750 kilograms an hour and can handle material formulations containing up to 50 percent regrind," says Oliverio.
The updated screw design also does a better job of self-cleaning, and processes materials containing a higher percentage of regrind, says Oliverio. All screws and cylinders are made of nitride steel, with special versions made of bimetal and Stellite available.
All N.EXT extruders are operated by water-cooled AC motors for energy efficiency and low noise. Other standard features include a hydraulic screen changer now driven by an AC motor rather than by an air-cooled DC motor, used in the prior configuration. "An AC water-cooled motor provides a better environment by not moving air and dust and requiring less maintenance," says Oliverio.
The N.EXT extruders for WM Thermoforming's Intec in-line series feature a gear pump system that eliminates pulsing during operation for consistent polymer processing. The result is homogeneous melt quality for uniform feeding to the extrusion flat die head, says Oliverio. The extrusion flat die head has a flexible lip that allows for sheet thickness adjustment through nuts that are pulled or pushed automatically. Sheet width is adjusted manually using deckle bars.
The Intec system also includes three chrome, mirror-polished calender-roll cylinders installed on a vertical axis that are individually driven by means of a servo motor. Hydraulic pistons control the opening and closing of the gap between the upper and lower cylinders. Each calender roll has a specially designed spiral cooling circuit that maintains an ideal calender-roll surface temperature for uniform cooling when contacting the extrudate. The vertical calender rolls are available in different versions to match extruder size and output requirements.
A motorized system provides the correct positioning (to the extruder die) during the operating cycle. The calender-roll system is completed by a draft gear, a two-roller system that ensures tension on the extruded web as it passes through the calender system. The rolls are on a vertical axis; the motor-driven lower roll has a chromed surface and is driven by a motor, while the upper roll is rubber coated and has no motor. Pneumatic pistons perform opening and closing operations. WM Thermoforming says that all calender systems are supplied with a central thermoregulation unit with three independent circuits.
All machine parameters are entered and displayed on a touch-screen panel from Bernecker + Rainer Industrie-Elektronik GmbH, Eggelsberg, Austria, which has U.S. offices in Roswell, Ga. A USB port on the operating panel allows users to store and recall data.
The company played host to Thermoforming Technology Days at its facility at the Elkhorn Tech Center, Elkhorn, Wis., last year, but has since sold the equipment at that location and does not have a new facility yet. "Right now, we are working with our sales representatives and their service engineers to serve the U.S. market. When we plan to [develop] another testing machine, we will define the right location for it," says Oliverio.
In addition to its Intec series, WM Thermoforming offers high-speed, roll-fed thermoforming technologies not connected to an extruder. These include its FT line of forming and punching thermoforming machines featuring a tilting lower platen for product trimming and part ejection that pivots 75 degrees. The company also offers its FC line of vacuum- and pressure-forming roll-fed machines and its PH line of preheating ovens.
Mikell Knights, senior correspondent
Contact:
Contact: WM Thermoforming, 41-91-64-07-050, www.wm-thermoforming.com
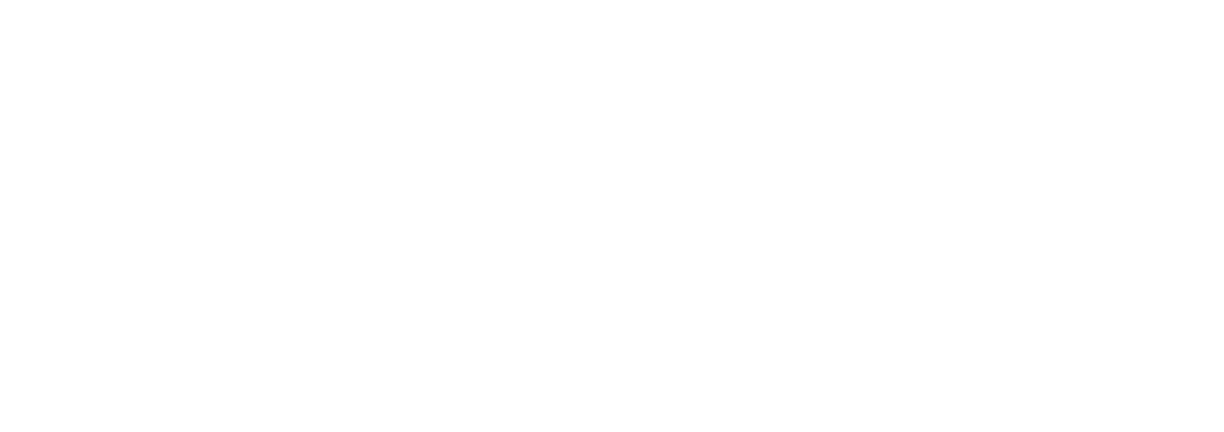