Suppliers of extrusion blown film equipment have developed improved dies for multilayer film, and updated related components.
ALPHA MARATHON
Alpha Marathon Film Extrusion Technologies Inc., Woodbridge, Ontario, has set up a pilot extrusion blown film line to demonstrate the wide processing capabilities of its 2X Nano-Layer blown film die technology, which it unveiled last year.
The 2X Nano-Layer circular blown film die incorporates the company's patented Layer Sequence Repeater (LSR) technology. LSR creates extremely thin, discrete layers that are interwoven throughout the structure of the film, which enhances its physical and mechanical properties, says Michael Taylor, director of sales and technical support in the U.S.
LSR comprises stainless steel laser-cut discs. Each disc serves a different function, including melt introduction, melt distribution and melt layering. Five discs are grouped into a module and multiple modules are installed in the die, says Taylor.
The technology makes it possible to create films with 25 to 200 layers, each less than 1 micron thick. The interwoven layers improve the film through quench-cooling and the integration of film properties. This allows users to downgauge 20 to 30 percent with no loss of mechanical properties, and to use less expensive polymers to cut costs 5 to 10 percent.
The ease of processing allows processors to raise throughput 15 to 25 percent while attaining blow-up ratios of 5:1 or 6:1, says Taylor.
LSR technology allows for the parallel flow of materials through the die at low pressures, temperatures and shear rates. The die is made with short flow paths that trim residence time and minimize melt degradation and can process polymers that vary widely by melt flow index (MFI) — from fractional to double-digit MFI. This includes recycled materials, says Taylor.
Processors can purchase a material based on its density or price rather than the grade. "I've produced blown films using 23 MFI grades designed entirely for injection molding. With this approach, the processor is not constrained by a particular grade," says Taylor.
The 2X die is offered in configurations up to a 26-inch diameter with layflat widths over 20 feet, and throughput rates of 1,000 pounds per hour. The 2X die can accommodate up to 12 extruders.
MACRO ENGINEERING
Macro Engineering & Technology Inc., Mississauga, Ontario, revamped its line of coextrusion dies for blown film and grouped the models into a single product line.
The new MacroPack blown film dies feature streamlined material flow passages that process a wider range of resins, while shortening purge times and resin transitioning. MacroPack dies can accommodate different layer thicknesses and have diameters of 3 inches to 80 inches. The dies can produce films 20 to 300 microns thick, in constructions of up to 11 layers, says CEO Jim Stobie.
The MacroPack series is composed of Macro's TP, CP, FP and MPC blown film coextrusion dies. The MacroPack-TP die is designed to be easy to clean and maintain for the production of smaller diameter films with three to 11 layers. With dies up to 500mm in diameter, it uses a proprietary technology that improves the material distribution for each layer. The die is suitable for use with double-bubble or three-bubble technology, as well as traditional blown film applications.
The MacroPack-CP die, formerly called CentroPack, is manufactured in diameters from 8 to 40 inches and produces films of up to five layers. MacroPack-CP has a reduced wetted-surface area for quick material purging. The absence of a feedblock minimizes pressure drops. The die is bottom-fed by extruders all positioned at the same height, says Stobie.
Macro's MPC die features a tapered mandrel and self-centering assembly for better self-cleaning, and uses fewer bolts than competing dies, for ease of assembly.
MacroPack-MPC is offered in 20-inch to 80-inch die diameters and produces films of up to 11 layers. The die can be side- or bottom-fed, and has a large area in the center that enables optimal air exchange for high-throughput internal bubble cooling (IBC) blown-film applications. It features a smaller wetted-surface area for fast product changeover.
The MacroPack series includes the FP coextrusion die with round channels that improve purge time and melt quality. The proprietary design prevents leakage. The die's modular configuration lets processors target specific melt flow channels for cleaning and maintenance. Processors can take apart one channel serving a specific layer, leaving the other layers intact, drastically reducing downtime, says Stobie. The die can produce multilayer structures containing barrier materials such as polyamide, ethylene vinyl alcohol (EVOH) and PETG.
Multiple layers can bring a processor added flexibility. Invos spol. s r.o ., Svarov, Czech Republic, which makes blown film, last year installed a new nine-extruder film and sheet line from Macro that featured several innovations. The 6-foot-wide blown film line produces food-packaging films and bags that incorporate barrier resins. The recent purchase is the third multilayer line Macro supplied to Invos.
Enhancements to the proprietary MacroPack- CP die design allow Invos to produce 18-layer films with the new line. "It is a proprietary technology that doubles the number of layers for a given die. It can be used with production lines designed for fewer material layers," says Stobie. Macro also recently installed a new die designed to generate products with 24 layers. The development is separate from the layer-doubling technology and is being used in a special application in North America, says Stobie.
Other features of the blown film coextrusion line include new extruder screws designed to process a wide range of materials. This eliminates the need to swap the screw when switching from a commodity resin to an engineering material.
The control system on the new line has a ReadyRun feature that allows the processor to capture, store and retrieve settings for a range of components on the blown film line. The parameters for each piece of equipment in the production line, such as the bubble cage adjustment or the air ring cooling setting, can be stored. "With a press of a button, the system returns to the desired setting," says Stobie.
The control system also allows processors to view their lines' energy consumption. With the feature, processors can see the energy required to manufacture a product. The processor can either use the function to optimize energy consumption during the heating and cooling steps or to determine which products are produced most efficiently, says Stobie.
The new multilayer line also has a Macro high-performance surface winder, featuring roll starts with zero fold-back; automatic cut and transfer in both directions; automatic shaft and roll handling; and automatic shaft extraction.
GLOUCESTER ENGINEERING
Gloucester Engineering Co., (GEC), Gloucester, Mass., acquired in September by Davis-Standard LLC, Pawcatuk, Conn., recently received a patent for a spiral die to process high barrier resins such as EVOH for blown films, says Carl Johnson, VP of sales at GEC.
The geometry of the spiral die minimizes dead spots, says Johnson. Customers testing the die find they can operate for longer periods before the barrier material degrades, and transition more quickly from one high barrier resin to another. The die joins GEC's line of spiral mandrel die designs.
Davis-Standard's acquisition of GEC increases its blown film capabilities substantially, while GEC gains a wider range of design, process engineering and aftermarket capabilities, and a large customer base. The acquisition has created complementary technologies. GEC's OptiFlow concentric manifold center-fed die for multilayer blown films is joined by Davis-Standard's Centrex (center-fed) and Vertex (binary split-flow distribution) die technologies. Johnson expects the OptiFlow and Centrex designs to merge eventually. Vertex adds a higher IBC capacity die design to the GEC line.
Other synergies between Davis-Standard and GEC are coming. GEC's UltraCool Series III air ring technology, introduced last year to improve bubble control and output, is being evaluated with the UpJet design from Davis-Standard. GEC is eyeing the potential use of Davis-Standard's DS Barrier III high-output, low-shear screw technology in its blown film systems. This newest generation of feedscrews can potentially generate 25 to 30 percent more output at a lower temperature than with the current screw design used by GEC, says Johnson. Most importantly, the two companies are working to devise a control system with the best features and functions of GEC's controls in a Davis-Standard Epic 3 PLC-based controller.
D.R. JOSEPH
D.R. Joseph Inc., Arlington, Texas, has incorporated two new features into its third-generation automated IBC control system for blown films.
The system improves production rates 25 to 50 percent when it is added to a blown film line without IBC control, and delivers 8 to 15 percent more output versus competing systems, says marketing manager Michael Pilolli.
The system, designed to provide extremely tight layflat film control and optimize airflow, features a new Bubble Break function that alerts the operator or shuts the extruder down if the bubble collapses. Ultrasonic sensors that are already installed as part of the IBC are used to detect the bubble. A beacon installed on the IBC warns of an impending shutdown if the bubble is not detected. Users can configure the IBC controller to stop production if the bubble is down, which can reduce scrap generation, says Pilolli.
The IBC controller also has a new feature to measure and maintain neck height on bubbles with high stalks. The capabilities join existing functions in the controller, including D.R. Joseph's automatic blower balance, layflat controller, automatic cage controller and auto valve calibration. The system also features integrated cooling air control, cage height adjustment and configurable alarms, says Pilolli.
D.R. Joseph also developed an all-in-one controller that allows the processor to switch from producing large geomembrane films to agricultural and construction films with large blow-up ratios, on the same line. The Tri-Mode Control system allows users to switch from IBC control to non-IBC layflat control to geomembrane/agricultural film IBC control.
Sensors are used to calculate the bubble diameter of a geomembrane and layflat width depending on the unit's mode. In IBC mode, they also keep the bubble positioned, measure bubble diameter and calculate the layflat. The controller retunes the sensors to adjust bubble distance on the fly to ensure accurate production.
BRAMPTON ENGINEERING
To help manufacturers purge material more quickly, Brampton Engineering (BE) Inc., Brampton, Ontario, offers its Streamlined Coextrusion Die (SCD). Every die layer incorporates similar rounded and streamlined melt channels that are milled in two facing plates, which are bolted together, then stacked vertically. The flow paths have no dead spots and remain the same even as more layers are added to the die. The SCD has an air gap between each module, which thermally isolates each layer of material.
"There is a growing requirement that blown film processors making multilayer structures have the versatility to change over their products quickly, including changing the types of resins in each layer," says Laura Martin, BE's director of process and rheology. She says the SCD addresses these needs. "Core layers — including nylon, EVOH and tie resins — have up to 70 percent less wetted surface area than in the cylindrical die designs, which enables much faster material purging with SCD."
Martin says SCD users can schedule multiple changeovers per day because they can purge even complex materials in 20-30 minutes. That's compared to traditional designs, which have dead spots and large wetted surface areas that both contribute to purging times of up to 36 hours.
"We have several different coextrusion film technologies in our plant, and our Brampton SCD dies are by far the easiest and fastest for changing film structures, especially when changing into and out of barrier resins," says Jae Baik, R&D manager at Polytarp Products, Toronto.
In addition to the die design, BE says each extruder in a BE coextrusion line is mounted at the centerline height dictated by the corresponding module of the die, minimizing the resin flow path from the tip of the screw to the die lip. This eliminates the complex feedblock, which is difficult to purge and clean.
BE also offers FlexStack, a much shorter variation on the SCD. With this design, adjacent layers share plates, as well as temperature control zones, says Martin.
Mikell Knights, senior correspondent
Contact:
Alpha Marathon Film Extrusion Technologies, 905-265-2055, www.alphamarathon.com
Brampton Engineering Inc.,
905-793-3000, www.be-ca.com
D.R. Joseph Inc., 817-987-2030, www.drj1.com
Gloucester Engineering Co. Inc., 978-281-1800, www.gloucesterengineering.com
Macro Engineering & Technology Inc., 905-507-9000, www.macroeng.com
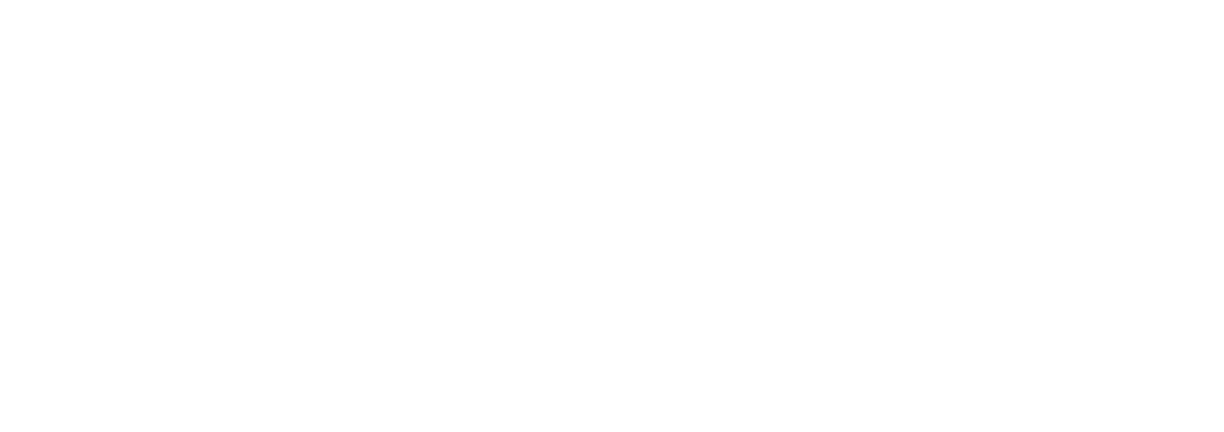