Nordson Xaloy Inc., New Castle, Pa., has expanded uses for its SmartHeat Coating technology, which replaces conventional heater bands with a heating system consisting of metallized-ceramic insulation material sprayed permanently onto the barrel, nozzle or melt pipe.
David Hotchkiss, global product manager for barrel products at Nordson Xaloy, says SmartHeat reduces maintenance downtime, is safer for operators and provides precise and rapid temperature control and energy savings of 30-60 percent compared to band heaters.
"SmartHeat gives a more uniform, stable heat control, which leads to more stable processing," Hotchkiss said during a presentation last month at the Extrusion 2015 Conference. "That significantly reduces material defects and scrap and improves part quality."
SmartHeat was introduced about three years ago for barrels and later was used for melt pipes. In recent months, it has been used for nozzles. It works on injection or extrusion equipment.
The patented coating can be applied to a new melt flow component purchased from Nordson Xaloy or retrofitted to existing components. The coating consists of two plasma-sprayed, metallized (aluminum oxide) ceramic layers with a nickel-chrome wire wrap between the layers. The electrically charged wire generates heat and the metal in the ceramic conducts it to the component being heated.
A conventional Teflon-coated thermal insulation cover completes the product. The coating, which is less than 0.08 inch thick, is guaranteed for the life of the component.
Since SmartHeat is a coating, there is almost no energy loss. All wiring is underneath the thermal coating and heat is conducted evenly throughout the ceramic material. The component is cool to the touch and no heat is lost into the plant.
The plasma-sprayed heater coating can withstand cleaning in fluidized beds or ovens to about 850 degrees Fahrenheit. Hardened resin pops off the surface.
SmartHeat uses standard thermocouples for easy installation.
Heater temperature can be uniformly maintained at approximately the process temperature. Band heaters generally require a heater temperature higher than the process temperature. SmartHeat works with the same controls as band heaters so temperatures can vary between zones.
Hotchkiss said that although band heaters are initially less expensive, tests run at users' processing plants show that the SmartHeat coating pays for itself in about 12-18 months, depending on energy costs and the region of the country.
He said the process has steadily gained acceptance since it was introduced. "It probably doesn't make sense on barrels that wear out quickly or where melt temperature is not critical," Hotchkiss said. "But it is a very good product for companies that run a quick cycle and where melt temperature is critical."
Ron Shinn, editor
Contact:
Nordson Xaloy Inc., 800-816-7711, www.nordsonpolymerprocessing.com
Ron Shinn | Editor
Editor Ron Shinn is a co-founder of Plastics Machinery & Manufacturing and has been covering the plastics industry for more than 35 years. He leads the editorial team, directs coverage and sets the editorial calendar. He also writes features, including the Talking Points column and On the Factory Floor, and covers recycling and sustainability for PMM and Plastics Recycling.
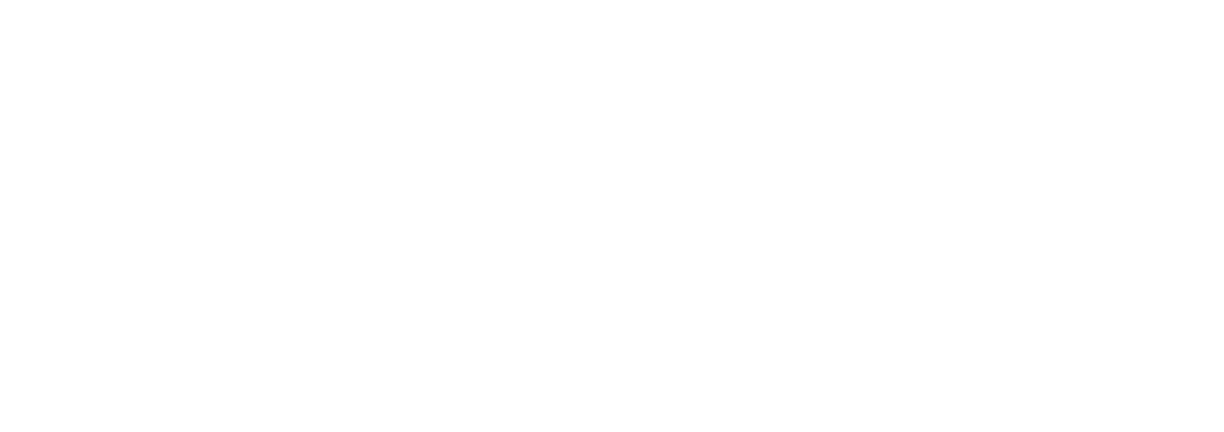