Mid-level machine controls for extrusion are delivering top-end capabilities, including a central, single-point of control and remote access to data.
Dialing in the optimal operating parameters for each piece of equipment in an extrusion line for the highest quality part production, and being able to remotely access, manage and archive this data from the production cell can help a processor better schedule operations, track problems and improve efficiency.
Formerly, these abilities were not readily available in a standard control because the extrusion line primarily relied on discrete controls and relays for each component on the line. Discrete controls perform independently. Data was known in the moment but not captured. The operational settings for each component had to be tuned each time a particular product was run (or re-run).
Processors seeking more consistent part production have been moving away from discrete controls that isolate aspects of the extrusion process. They are adopting new controls that tie together the complete extrusion line. Other new controls connect downstream and upstream equipment. The drive for higher-quality parts has sparked the need for better data collection, report generation and remote access to the machine and its related data. Two suppliers serving the extrusion market have recently rolled out control advances.
ICT AllOWS USERSTO LEASE HIGH-END CONTROL
When it comes to controlling their equipment, plastics manufacturers have two general options. They include lower-cost discrete controls that display the setting and performance of a single component in operation, or higher-end systems that incorporate advanced diagnostics, data collection and remote connectivity.
Unfortunately, until now, the second option was either not available or unaffordable, says Dan Barlow, VP at Integrated Control Technologies (ICT), Coppell, Texas.
The challenge of moving forward with more advanced controls always left the processor with a dilemma. One option is to purchase a new extruder, but this can be cost-prohibitive and overlook the value of the existing system, leaving one to consider a retrofit. Many manufacturers will offer this service, but it is typically limited to their specific make, and is often relatively high-priced even for discrete solutions. An alternative is to seek a systems integrator, but this requires a detailed scope-of-work analysis and can result in inconsistencies from one machine to the next. It also involves taking a gamble on the integrator's experience and capabilities.
ICT, which offers its Tempcom series of full-feature machine controls, has encountered numerous processors with older extrusion equipment looking for a control upgrade but limited by budget constraints.
This month, ICT is launching Revisor, a simplified machine control system that allows processors to upgrade to a central machine control system more cost-effectively. ICT offers Revisor as a lease-to-own program to minimize the capital investment typically required when updating to machine controls with these types of advanced features. "At the end of a two-year lease, the molder owns the system for one dollar," says Barlow.
Revisor, a part of ICT's Tempcom series, "is not a PLC or PC but a hybrid system designed with a PLC operator interface with PC characteristics. It is PLC-based but runs ladder logic, and this allows for ease of installation, setup and use," says Barlow.
In its initial form, the system targets simpler extrusion operations that do not require more than eight barrel zones and eight die zones, for a total of 16 temperature zones of control, says Barlow.
Revisor is composed of a single machine panel with a 15-inch color touch screen mounted on a steel plate. The user can replace the previous machine control on the extruder with this unit. All existing wires from the single-loop controllers and discrete controls are tied into removable terminal blocks on the back of the unit.
Revisor has a built-in graphical user interface and programming developed in-house that allow the processor to enter data about the extruder quickly during setup. Machine programming knowledge is not required.
A program ICT calls Flex Builder technology leads the molder through setup. Users can select the number of barrel zones, die zones, drive type and operating pressures. A starter screen allows the user to tie components like pumps for water or oil to a particular drive, so that when a barrel zone is turned on, the water pump associated with it will also activate.
Once the set-up parameters are entered, the Revisor system is initialized. Processors now see all data from all relevant devices on the extruder and can create a recipe for each product run, which discrete systems cannot accomplish. Revisor captures all of the data generated by the machine, so processors can keep track of the recipe being run, personnel logged into the machine, alarms and other operational data points.
Revisor's production-monitoring function gives an at-a-glance view of the machine status. The program features diagnostic functions that prevent a cold-zone start and signal if there is an open heater, a shorted-out solid-state relay or high cabinet temperature. In addition, using Revisor, processors can view on-screen manuals, wiring diagrams and help videos. Its multilevel security program provides five levels of access to the machine controls to prevent unauthorized machine changes.
Like the higher-end machine controls, Revisor allows the processor to configure and access logged and archived data remotely. Extruder data is stored to a CSV file that keeps tabular data in plain text. The operator screen can also be accessed remotely through a computer or mobile device, says Barlow.
Revisor comes with numerous features to enhance extrusion. One feature allows the processor to set an action at a specific time.
"The processor can schedule the day and time after the operator leaves when all heat zones are shut off, or can input a time Monday morning before the machine operator arrives when pre-heating can begin," says Barlow.
Processors can move the Revisor unit from one machine to another. The system is reset, all data is removed and the unit can then be reconfigured for the next machine. Next year, ICT plans to offer a version of Revisor for coextrusion.
LINE CONTROL FOR ANY EXTRUDER
R&B Plastics Machinery LLC, Saline, Mich., a manufacturer of extrusion blow molding machines, single-screw extruders, feed screws and trimmer systems, launched its new Max Extrusion Control system at NPE. It says the system is a cost-effective alternative to higher-end Supervisory Control and Data Acquisition (SCADA) software systems that can monitor and control every device on a machine, as well as upstream and downstream equipment.
The Max system can be retrofitted to any make or model of extruder. The system not only provides monitoring and control of the extruder itself but all components upstream and downstream for full line control, says sales manager Ken Caryl.
"An extrusion line may have six, seven or eight pieces of downstream equipment attached to it, with each piece of equipment designed by various manufacturers. Extruders are looking to get away from running up and down the line to each piece of equipment when they look to make an adjustment. With the Max system, the control of each piece of machinery in the line can be accessed from one station, on one display," says Caryl.
The Max system is a PLC-based extrusion control system that incorporates, in its base form, a simplified yet robust Windows CE HMI platform — which runs on either the Panelview Plus from Allen-Bradley or the ComfortPanel from Siemens, says Jack Losee, manager of electric controls.
As long as each piece of downstream equipment is compatible with the open architecture of the PLC, the Max system can incorporate it into overall line control. Use of the Windows CE human-machine interface with off-the-shelf components results in a system that delivers performance and features similar to a higher-end SCADA system at a price close to that for discrete control setups, says Losee.
The independent, autonomous nature of discrete controls makes it difficult for a processor to create and store machine parameters that are ideal for a job, which prompts the user to continuously adjust the devices to control the system.
"Discrete controls also prohibit communication of process and production data, and do not easily allow for data collection, recipe storage, alarm history or trending reports," says Losee. R&B says its controls business was split evenly between lower-end discrete controls and high-end machine-control systems just a few years ago. However, the company has not sold a discrete system in three years, says Caryl.
For an extruder undergoing a retrofit, R&B will rip out the old control panel and mercury relays, and install the new Max control package with PLC and solid-state contactors.
The Max system provides integrated line control for a wide range of extrusion applications, including pipe, profile, tubing, sheet, reclaim, compounding, fiber and film, and is also suited for use with extrusion blow molding applications in accumulator, wheel and shuttle styles, says Caryl. The look and feel of the system is similar regardless of machine type or line complexity, says Losee.
The Max system has a 15- to 21-inch touch screen where processors can set, monitor and control system temperatures, speeds, amperages and pressures. The configurable screens can show equipment layout or other specifications. Melt-pressure transducer calibration is achieved with the press of a button. Run data is presented in real time, and the Windows CE-based HMI can log up to 100 variables to a USB stick. Using the Ethernet IP and a remote connectivity system, the Max system can perform as a protection device to the machine network, while isolating it from the Internet, says Caryl.
Mikell Knights, senior correspondent
Contact:
Integrated Control Technologies, 972-906-7445, www.integratedcontroltech.com
R&B Plastics Machinery LLC, 734-429-9421, www.rbplasticsmachinery.com
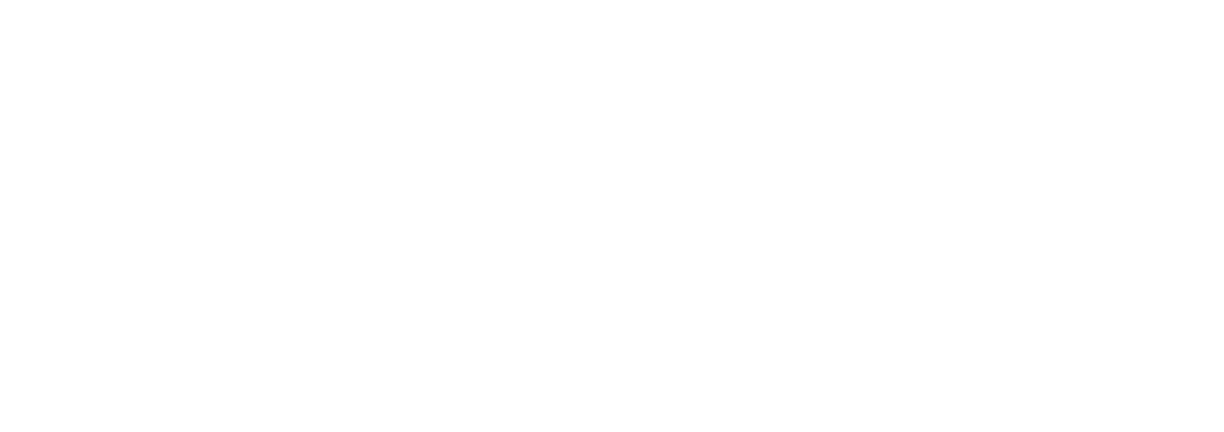