Controllers, input/output (I/O), drives and human-machine interface (HMI) stations provide both the brains of machine control systems, as well as the way for operators to harness their intelligence. Technology suppliers serving all types of plastics machinery have launched new components, created to ease connectivity or improve efficiency.
Suppliers of PC-, PLC- and Linux-based machine control technologies say connectivity to all the components related to a process, and the ability to view and control those manufacturing cells remotely, are as important as high performance.
Processors ordering a new machine want a control package tailored to their needs, while those updating the machine controls of an existing machine seek more reliable operation or improved control of critical manufacturing points. This report highlights several developments in the HMI, controller technology, drive mechanics, motor design, I/O devices, real-time industrial Ethernet connectivity platforms and related software.
Thomas Kosthorst, business development manager-plastics for Beckhoff Automation GmbH & Co. KG, Westphalia, Germany, says the next step in data transfer, besides the development of standardized protocols for real-time industrial internet communication, will be the continued emergence of machine-to-machine intelligence. Intelligent algorithms will analyze more details about the process and prompt optimization algorithms to help manufacturing processes operate more efficiently.
"For example, a plastics machine will communicate to a robot that the delay time is too long, and will determine how much sooner the automation can enter the clamp area. Updated machine controls will analyze all aspects of the manufacturing sequence and adjust automatically without operator intervention," he says.
PERFORMANCE AND CONNECTIVITY ENHANCEMENTS
Demand for higher performance and more connectivity mark the two biggest trends, says Mathias Radziwill, business development manager, plastics, at Siemens Digital Factory, Norcross, Ga.
Siemens has developed another open digital controller option. This year it released its new Simatic ET 200SP open controller, which is configured with a new PC-based central processing unit (CPU 1515SP PC).
It comes pre-engineered with the Simatic S7-1500 software controller and communicates with distributed I/O modules through a Profinet or Profibus connection. The PC-based platform allows for special automation functions to be integrated into the system for control by means of C or C++ programming languages. HMI functionality with pre-installed WinCC Runtime Advanced visualization software enables control and visualization in one device.
The latest iteration of the Simatic S7-1500 PLC controller now features diagnostics built into the hardware framework and firmware rather than in the software, which minimizes downtime. Faults such as a wire break on an I/O card, an unplugged communications cable or a power loss generate a message in plain text that appears on the CPU HMI display with details pinpointing the location of the error. The built-in diagnostics eliminate programming and monitor drives and central or remote I/O racks. The controller now has a full complement of CPUs to provide versions with a range of processing speeds and memory capabilities, says John Wilhite, PC-based automation product manager, industrial automation at the Siemens Digital Factory. Siemens also updated the capabilities of its Totally Integrated Automation engineering platform that provides an emgineering environment where users can configure, analyze and test customized machine control systems.
WHAT DRIVES YOU
Updating any aspect of the machine control goes a long way toward increasing productivity and energy efficiencies, says Jonathan Bullick, sales manager, KEB America Inc., Shakopee, Minn.
The company recently released an air-cooled version of its Combivert H6 multi-axis drive, suited to high-performance, all-electric injection molding machines. It joins a liquid-cooled version and is designed for input powers up to 225 kW. A new H6 offering for smaller powered axes are modules that contain dual independent outputs as a way to increase power density while reducing the overall cost of the unit. It can be used to drive servo, linear, torque and induction motor types. The platform uses a common DC bus connection, which saves energy and allows single- or double-axis modules to be added as needed. An EtherCAT bus system is used to communicate between the modules.
The F6-K is KEB's newest single-axis drive platform, used to drive injection molding and extrusion machines. Available in up to 1,200 horsepower, the drive comes standard with three analog inputs that can be used to control advanced equipment, such as a hydraulic pump servo motor. Processors can use it to handle pump control through the drive rather than rely on an external PLC.
The R6 Regenerative drive from KEB is used in downstream extrusion winding torque control applications, such as web handling, to return current to the power grid. It relies on advanced processing hardware and a proprietary algorithm KEB calls Natural Current Modulation to return current to the grid.
SPOTLIGHT ON CONTROLLER TECHNOLOGY
Recent developments from Beckhoff include its new multi-axis AX8000 servo system designed to meet high control speed and positioning accuracy requirements. The system can be configured with single- and dual-axis modules and features multicore ARM processors. Control algorithms with multichannel current-control technology enable sample and response times of less than 1 microsecond for current control and velocity control cycle times as low as 16 microseconds. Kosthorst also notes that the integration of a brake resistor, brake chopper and mains filter minimizes the requirement for external components while simplifying inventory management and logistics. A One Cable Technology (OCT) connects the motors and drives, reducing cabling by 50 percent. AX8000 is EtherCAT-enabled and has TwinCAT runtime integrated in the system.
Beckhoff also introduced the CX5100 embedded PC Controller, designed as a mid-range multicore controller that delivers high performance at a lower cost versus a traditional PLC and motion-control system. It can operate as a single hardware platform for plastics machinery and is suited to machine automation, motion or temperature control and can simultaneously run HMI software. It is equipped with the Intel Atom CPU processor in single-, dual- or quad-core arrangement. Another embedded PC, Beckhoff's CX8091 compact controller is an entry-level system that can be used for connectivity in cloud-based enterprise systems that allow for the secure, encrypted sharing of data and communications. It is designed for simple processes within a distributed control system. It features OPC-UA (open platform communications, unified architecture) technology for secure and reliable exchange of data in industrial environments. Beckhoff also developed a multi-touch machine controller that combines a multi-touch display with a high-powered processor for factory machinery. While serving as the HMI, the CP32xx Panel PC series can perform all automation and control programs on a machine. The controller is optimized for Beckhoff's TwinCAT software which provides the universal programming environment and runtime for all automation tasks.
LEVERAGE CONTROL, MOTION
AND SAFETY TECHNOLOGY
Eurotherm by Schneider, Ashburn, Va., says the current development focus for its flagship Maco Compact series is to leverage the technology know-how of parent company Schneider Electric for safety devices, biometrics, logic and HMI programming and communications with Eurotherm's proven algorithms regarding motion, pressure, temperature and parison control. It will further integrate or incorporate Schneider's scalable, open architecture into its products, which can deliver responsive (less than 100 microseconds) and repeatable I/O data transfer.
Eurotherm also is continuing development of simple graphics-based process management tools that assist machine control operations locally or remotely, says David Spahr, director of engineering for all Maco products. These tools improve energy management while minimizing cycle time, and enhance tracking and logging of all control parameters.
Mikell Knights, senior correspondent
Contact:
Beckhoff Automation LLC, 952-890-0000, www.beckhoffautomation.com
Eurotherm by Schneider Electric, 703-724-7378, www.eurotherm.com
KEB America Inc., 925-224-1400, www.kebamerica.com
Siemens Industry Inc., 800-743-6367, www.usa.siemens.com
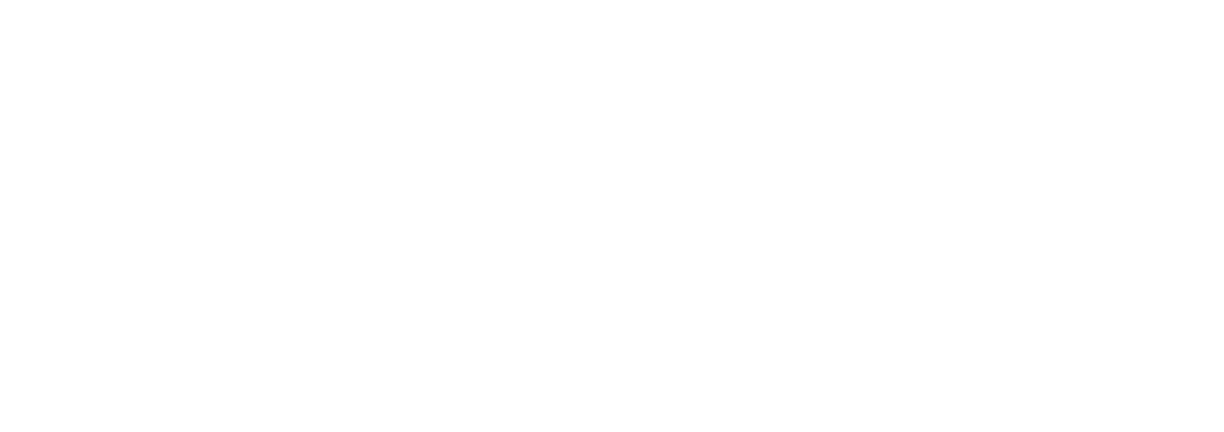