With advanced manufacturing accelerating in the wake of the economic recovery, it is encountering a severe shortage of skilled labor. This is being keenly felt in the plastics processing industry: As plastics processors fill their order books, many are finding that there are simply not enough trained professionals to bring the jobs to completion. People who are trained in designing and using machinery and equipment are particulaly needed by industry.
The skills gap is a concern across all processes and this story highlights what one molder is doing, particularly with providing a good grounding in machinery and equipment education. Essentially, the industry stands to gain because any errors with machinery can be costly so workers trained with the basics become a long-term investment.
Intertech Plastics Inc., a Denver-based injection molder, sponsors apprenticeships and training programs for younger workers. The goal of the company's training program is to build a technical foundation for new workers. "We want critical, fundamental skills to be well-taught," engineering manager Tim Ruybal says. With such skills, workers can learn to troubleshoot and solve problems, as well as run machines.
Intertech Chairman and CEO Noel Ginsburg is such an advocate for vocational outreach, he has become involved in efforts to build partnerships between schools and the manufacturing industry. That includes a pilot program formed by the state government and state educators called Business and Schools in Collaboration, or BASIC.
Ginsburg believes preparing people for manufacturing is a task that schools cannot fulfill on their own. As part of its internship program, Intertech has developed a curriculum that applies what students are learning in the classroom with what they are doing on the factory floor. "For example, when you have to blend color to make a particular part, how do you do the ratios; how do you do basic programming on a five-axis robot? They actually do it, and that gives them hands-on experience," Ginsburg says.
Ruybal gives three examples of why a good grounding in the basics should not be overlooked:
Mold making: In injection mold making, precision surface grinding is crucial both at the beginning and the end of the mold-making process, Ruybal says. Apprentices are trained in safe operation and machinery setup of manual surface grinder machines. Those skills remain relevant for experienced mold makers, who use manual grinding machines that are often the primary piece of equipment during the final fit of the mold components, with components ground to tolerances as tight as 0.0005 inch.
Process engineering: As with mold making, apprentice process engineers are trained in the fundamentals of how a mold is set up and how it runs. They also learn its running characteristics. Apprentices are taught how to check for venting issues, lubricate leader pins and parting slides and make sure that the water is set up for good turbulent flow for efficient heating and cooling. They also learn how changes in temperature and humidity affect the molding process.
These early lessons are crucial to an experienced process engineer who develops the standard process for the injection press, cycle time and timing for getting the part out of the mold. For apprentice technicians, one key takeaway is that if the process varies too much from the standard, it's necessary to go back to the original standard, Ruybal says.
Automation: Once the parts are made, the automation engineer determines the type of end-of-arm tooling that will be required to remove the part from the mold. "You have to have a mathematical background to figure out the distance of the mold opening, the method you are going to use to grab the part," taking into consideration the stroke of the robot arm, the mold opening and the clearance needed to get the part out of the mold, Ruybal says. "You have to determine all that at the beginning," he says. Once the mechanical parameters have been established, the robot must be programmed to perform the tasks.
Those tasks require a basic understanding of how robots work and robot programming, as well as knowledge of the space limitations on extracting the part. "All of these things tie in, and as you progress through the apprenticeship, you can diagnose and troubleshoot as you go," Ruybal says. He cautions that lost revenue, lost machine time and, in some cases, a damaged robot could result from taking shortcuts on worker training.
Ginsburg says that the labor shortage has impacted both the top and bottom lines.
Business demand "is growing fast, and ensuring we have enough tool makers and technicians has been a very difficult challenge," he says. "Although we have apprenticeships running, it takes five years to [train] a tool maker."
In Ginsburg's view, people in the manufacturing industry must work together to train a new workforce — and in the effort, break away from the long-standing practice of poaching skilled workers from each other.
BASIC: AN APPRENTICESHIP MODEL
Ginsburg is betting that BASIC is a way forward for Colorado plastics manufacturing companies to successfully address skilled labor shortages as an industry.
Through BASIC, manufacturing companies will play host to students, who will receive experiential, work-based learning and training that complements their classroom work.
The key to BASIC's approach is close integration between the state's schools and industry. Ginsburg says the U.S. manufacturing industry should adopt the apprenticeship model from Switzerland. He notes that the Swiss apprentice system is market-driven. "This system is not about philanthropy or giving back; the system pays for itself, essentially. It's not a government program," he says. "If I spend $100,000 over four years with an apprentice, I will have made back that investment by the time they graduate, but now I have a trained employee."
Ginsburg sees the Swiss system, and by extension, a comparable U.S. apprenticeship program, as a way to build business and competitiveness on a world-class basis.
For Ginsburg, the mission of preparing young workers is very personal. Twenty years ago, he helped found the Colorado I Have a Dream Foundation, Denver, which works with disadvantaged children from the third grade until they graduate, making scholarships available to them. He brought one of those students into his business. That employee started out in the print shop, progressed through several areas of the business and now runs a $10 million division in the company.
"The greatest challenge is stepping away from the business and thinking strategically as an industry to invest in this type of systemic change and participate," Ginsburg says.
FINDING PARTNERS
Currently, the BASIC organization is in the pre-launch stage. Next year will see the implementation of a structured internship, or residency, which will align the student's interests with a specific curriculum in the workplace.
Companies that participate as Certified Centers for Learning will learn how to work with apprentices, develop a curriculum and test that against what will ultimately become an ISO standard.
"This becomes a building block for what we ultimately want to be doing in that shared workspace, between three days in the workplace and two days in the classroom," Ginsburg says.
Ginsburg acknowledges that the goals of the BASIC program are daunting, but a collective effort is necessary. He thinks it will take a decade to reach critical mass in the state, but the payoff will be worth it.
"Ten or 15 years from now, when we look back and see an unemployment rate for our youth at 2.4 percent, which is where it is at in Switzerland, we will have done something meaningful for our state and our country," Ginsburg says.
John DeGaspari, senior correspondent
Contact:
Intertech Plastics Inc., 303-371-4270, www.intertechplastics.com
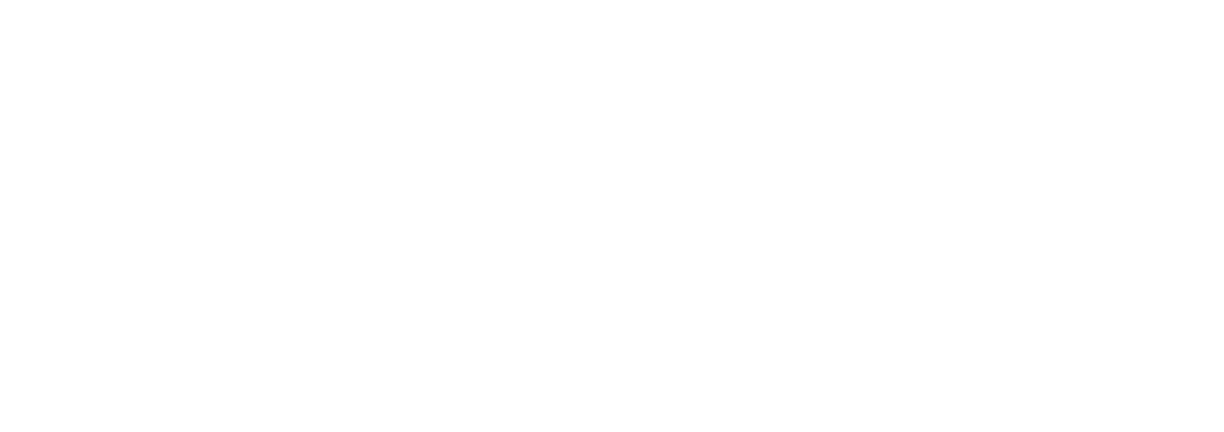