Blow molding machinery maker Bekum America Corp., Williamston, Mich., is using a spiral sleeve extrusion head to create a triple-layer bottle for a household cleaning product. The target for thickness on the middle layer is 0.008 inch in a mix of post-consumer resin (PCR) and calcium carbonate (CC). The unique challenge in this application is to form an inner, barrier layer of only 0.002 inch, or 10 percent of the total thickness of the bottle, so that the middle layer's PCR content can be maximized. The total bottle thickness is about 0.02 inch and uses virgin resin on the outer and inner layers.
This represents a step forward in Bekum's technology and a new benchmark for the company. It is the first time Bekum has used the spiral sleeve technology in a triple-layer packaging application with such thin layer requirements. A new customer in Mexico presented the challenge. On a 1-liter round bottle, for example, the goal was a weight of 40 grams.
PCR and CC can be blended in a monolayer bottle, which is what that particular blow molder was doing previously, but there are processing issues that tend to hurt production efficiencies, says Joe Slenk, applications engineer with Bekum, who co-presented the technology with Miguel Vivas, Bekum regional sales manager, during the SPE Blow Molding Conference held Oct. 12-14 in Pittsburgh.
"By burying it [the PCR and CC], you have a virgin outer layer and a virgin inner layer so you have virgin material properties kind of sandwiching the inconsistencies between those," he says. "It helps out the process and then the consumer and your product never touch anything that is post-consumer. This customer is very proud of their brand so that if they load up more PCR for their cost savings they still have virgin material in contact with their product."
In Mexico, PCR is significantly cheaper than in the United States, Vivas and Slenk say. A pound of virgin resin can cost as much as 49 cents more than a pound of PCR. But the benefits extend beyond cost savings.
"The middle layer is PCR, so this usually is considerably cheaper than virgin," says Vivas. "With calcium carbonate usage, you add additional rigidity to the container. There are additional resin savings. Of course, there is the corporate image that you are environmentally friendly, that you may be doing something that the other companies are not."
To be clear, it is the extrusion head technology that is the first of its kind, emphasizes Gary Carr, Bekum America's national sales director. Using trilayer to incorporate PCR is not new. But there were limits on the thinness that could be attained while achieving uniformity and color distribution. This impacts what a blow molder can put into the middle layer and how much PCR can be incorporated. The business proposition for Bekum was to create a bottle that had a layer thickness distribution of 50 percent for the outer layer, 10 percent for the inner, barrier layer and 40 percent for the the middle layer, where all PCR would be used. A more traditional tri-ex application would have a thicker middle layer to load more PCR, however, a 50 percent outer layer was needed for proper color coverage, which requires a minimum of 0.01 inch thickness.
"We also needed to take flash into consideration," says Slenk. "We want to be able to use the excess material generated from the process. So that has to go back into the bottle as well. It's kind of a balancing act as to how much of each type of material can be put into the container."
HEART-SHAPED CURVE VS. SPIRAL HEAD
The most common type of extrusion head for co-extrusion is the heart-shaped curve. With that, the material is split, then reknit on the other side. In the spiral sleeve design, the material is split into several melt channels, then runs through a series of spirals that actually become smaller and smaller. The material overlaps on itself the further it travels down the extrusion head. For extrusion blow molding of bottles, there are no weld or knit lines and there is excellent layer thickness uniformity.
"So, we designed this head with this technology to help give us better layer distribution in the container and to achieve the really thin layers necessary," says Vivas.
Bekum's results from testing achieved a 40-gram net weight for the bottle and 49.5-gram gross weight. The actual flash was 19.2 percent of total extrusion on a 12-second cycle with an output of 2,400 bottles per hour. For the outer layer extruder on which a 70mm grooved barrel was used, pressure was 4,600 pounds per square inch (PSI) at 24 revolutions per minute (RPM). The middle layer extruder used a 70mm grooved barrel, achieving 5,800 PSI at 31 RPM. The inner layer extruder with a 38mm grooved barrel achieved 3,400 PSI at 18 RPM. The PCR and CC extruder was equipped with a screen changer.
"With this system, we did see very constant throughput," says Slenk. "One issue with PCR processing is that the inconsistency of the material can cause some output fluctuations for the extrusion systems. That can be problematic, constantly having to make changes, so with that buried in the middle and with the grooved barrel extruders, we saw a very constant output. We didn't actually have to adjust it. We did a factory acceptance test around a four-hour run and never touched the machine once."
In terms of auxiliary equipment, the requirements are different in this machine configuration, which used two four-compartment blenders. It stands to reason. The process requires additional loaders and blenders.
Officials reached their target, producing a trilayer bottle with a 0.002-inch-thick middle layer of PCR.
The first Bekum blow molding ma- chine incorporating this technology is an H-155 from Bekum's H Series shuttle machines. The model has four parison heads and 100mm centerlines and uses grooved barrel extruders to compensate for high pressures. At the time this article was written, a second machine was being built at Bekum's North American site and was going to the same customer. The extrusion heads are being built by Bekum Europe.
While the initial investment may be higher, officials say that it pays off in the long run. Carr estimates roughly 40 percent higher investment over the monolayer process. But processors that make a lot of bottles will achieve savings from resin costs.
Bekum performed a product cost analysis on a 1-liter container processed via monolayer versus trilayer extrusion on the H-155. With tri-extrusion, all other inputs being equal, there was a per-pound savings of 20 cents on HDPE resin. This is on an eight-cavity machine with an estimated cycle time of 13 seconds at 1,994 parts per hour and 90 percent molder efficiency.
"When we first looked at this project, we were questioning ourselves," Carr says. "How much could we truly get in, and would it be worth doing it in trilayer? The technology worked beyond our expectations."
Angie DeRosa, managing editor
Contact:
Bekum America Corp., 517-655-4331, www.bekumamerica.com
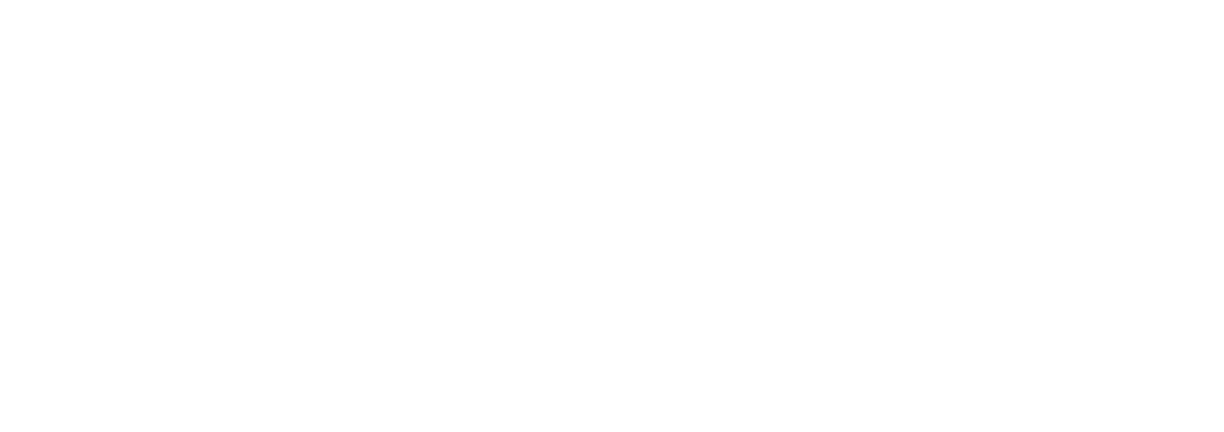