Two emerging mold technologies that improve the quality of an injection-molded part have come together through an effort organized by Crest Mold Technology Inc., Oldcastle, Ontario.
In what could be a developing standard in the industry, conformal cooling, a mold design approach in which the cooling channels follow the contour of the molding surface, is being coupled with dynamic mold temperature control, a material conditioning technique that heats, then rapidly cools the mold. Tying the technologies together yields far less stressed parts with a Class A surface finish while reducing injection pressure, clamping force and, in some instances, cycle times.
Conformal mold cooling channels can get closer to the inner contour of the mold than traditional straight-line, gun-drilled channels, while a rapid mold heating and cooling technique represents an option to conventional molding where the tool temperature is kept at a steady state. Both technologies share the goal of optimizing heat transfer between the mold and material.
The combined capabilities are being offered through partnerships announced during NPE earlier this year and at Amerimold, held in June. Crest Mold, a maker of two-plate, three-plate, multicavity prototype and production tools, is partnering with Contura MTC GmbH, Menden, Germany, a producer of core and cavity inserts for injection molds that feature conformal cooling channels; and Regloplas Corp., St. Joseph, Mich., a manufacturer of temperature-control units and chillers. The alliance offers a tooling cell consisting of the tooling, tooling inserts with contoured cooling channels and a temperature-control unit.
Crest Mold initiated the creation of the partnerships, and has established Crest Thermal Technology (CTT), a division within the family-owned and -operated tool-making firm that will serve the interests of the alliance. CTT will implement both technologies into a final working injection mold. Will Cipkar, technical sales for Crest Mold, heads up CTT and is in charge of "looking at programs and projects that can utilize conformal cooling with rapid heating and cooling, then working with the partnered members to bring the project to fruition." Crest Mold has been researching both technologies for more than a decade and has evaluated various versions as a fit for its high-precision tools.
There are numerous potential benefits for a molder using the combined technologies, says Kip Petrykowski, director of national sales for dynamic temperature and composites for Regloplas. Parts that respond best to rapid heating and cooling include heavy fiber-loaded parts where the filler must be buried within the part and the part surface is free of sink marks, weld lines or discoloration.
Molders that coat parts with chrome for automotive applications aim to produce blemish-free surfaces that exhibit a high degree of flatness without waviness. Makers of sunglasses, lenses or LED lights can produce optical parts with low molded-in stress, which improves the refracted index and clarity. Precise detail for long and narrow medical parts like catheters or pipettes can also be achieved repeatedly with rapid heating and cooling, says Petrykowski.
Traditional gun-drilled tools running cooling media at a set temperature are the mainstay of the injection molding industry in North America, says Cipkar. However, the application of contoured channels and dynamic mold-temperature control can be used on parts with hard-to-cool areas to help a molder meet appearance requirements, or to resolve mold filling or packing issues where molding in a thin-walled rib or preventing gate freeze-off is a problem. It is also a solution in projects where mold cooling is the bottleneck to higher productivity. By using conformal cooling technology alone and in its successful application, it can reduce cycle times by up to 30 percent or more.
COME TOGETHER
Crest Mold now is the North American representative for Contura MTC, which has produced mold inserts containing precisely designed and engineered cooling since 1989, and has more than 8,000 such inserts installed in Europe and Asia, says Cipkar.
Tooling with conformal cooling can be produced various ways. The most common type, vacuum brazing, is used by Contura. The key to its successful application is targeting the channel's geometry, distance to the mold surface and the proximity of one channel to another.
A conventional production tool will use channels that typically are five-eighths inch, three quarters of an inch, or one-half inch from the molding surface, says Cipkar.
"If it takes 16 seconds for the heat from the molding surface to get to a cooling channel that is a half-inch away, one would think that positioning the channel a quarter-inch closer would reduce the cycle to 8 seconds. But the math behind conformal designs is nonlinear and quadratic, so this change would actually reduce the cooling time to 4 seconds," says Cipkar.
The most common insert Contura makes is produced from a specially selected H-13 steel billet, into which a half or portion of the conformal channel is milled. The milled steel is then stacked together, then vacuum brazed. All of the design, development, manufacturing and brazing is done at Contura's facility. Contura also manufactures conformally cooled inserts in a second and separate approach, through a diffusion-bonding process it developed. No brazing material or brazing flux is involved, and it is a steel-on-steel approach. "After milling, the metal is placed inside of a specially designed hydraulic press which resides inside of a furnace. The process utilizes the high temperature of the furnace — up to 3,272 Fahrenheit — and pressure to bond the plates together without the appearance of a seam line, weld line or braze line," says Cipkar.
Contura also developed an additive manufacturing approach to produce a 3-D printed metal insert containing contoured channels. Cipkar says the 3-D printed insert provides more versatility in terms of design but also requires an extensive heat-treating step. Its brazing and diffusion-bonding techniques create a longer-lasting insert with greater structural integrity compared to the 3-D printed style, says Cipkar.
Contura has a service that can determine if a part lends itself to conformal cooling, based on a molder's information regarding the press, mold set-up and other process and production factors. This eliminates the need to conduct mold trials, which were previously required to determine if the tool can be or should be designed for conformal cooling. Using finite element method (FEM) analysis, proprietary algorithms and other calculations, Contura will guarantee the cycle time of the project or reimburse the client if the cycle time is not met, says Cipkar.
HOT OR NOT
"The secret to repeatable production of defect-free, high-quality parts is to get the material close to its glass-transition [TG] during mold filling; rapid heating and cooling optimizes tooling temperature for optimized part temperature control," says Petrykowski.
Gate freeze-off can be a common issue if operating a mold at a steady, uniform temperature, causing a skin layer of material to develop upon contact with the tooling surface. Freeze-off requires higher injection pressures and velocities to push material to the end of fill in a mold. "Instead of shearing that material by jamming it into a cold tool, dynamic temperature cycling allows for a hotter mold temperature, which lets the material flow into it. This makes a huge difference as to how the material sets up," says Petrykowski. Cooler water is rapidly introduced into the tool, purging the hotter water.
Regloplas also discovered that not all tools are suited to rapid heating and cooling. "The temperature swing can be so great that it can cause components in the tool to bind," says Petrykowski. "Crest Mold has developed methods of removing these heat-related issues from molds, making it so components aren't subjected to the heat sent to the molding surface," says Cipkar. Regloplas as well has developed its own set of algorithms and calculations to determine if a tool can be utilized for dynamic temperature cycling. The development of the company's algorithms for calculating optimal cooling channel position and dimensions, overlaid with numerous selected process and production parameters, allows Regloplas to minimize or eliminate the need for mold trials, says Petrykowski. A rapid heating and cooling circuit can be designed just for regions in the tool where the molder is having an issue, which minimizes design costs by retaining traditional gun-drilled channels in areas that mold well.
Regloplas offers a wide range of pressurized water temperature-control units and chillers that can deliver the cooling medium in a range from about 65 degrees Fahrenheit to 400 Fahrenheit. Regloplas will introduce a unit next year that will deliver water up to 428 Fahrenheit.
The more common configuration of the rapid heating and cooling cell consists of two identical temperature control units, one for hot water and one for cold. A specially designed hydraulically actuated valve station developed by Regloplas connects the thermolators. The valve simultaneously opens the circuit to the mold for one volume of pressurized conditioned water while closing off the other based on a user-selected signal. This arrangement allows the molder to use each temperature-control unit on different machines with different molding projects when not running a rapid heating and cooling application. A special double-bypass valve station closes mold access to both water circuits, which allows water already within the mold to sit for a time before a switchover, if required.
"Molders have to dial in the optimum temperatures and switchover points to the part and process. It is possible to cool too fast or heat too fast … the molded part may not like it," says Petrykowski.
INVESTIGATING RELATED TECHNOLOGIES
Crest Mold also is becoming skilled at producing conformal-type cooling channels with gun-drilled methods. In this approach, channels do not follow the dimensions of the mold surface, but are machined to be closer to the mold surface.
Crest Mold also is investigating rapid heating with pressurized steam. The process is quite common in Japan and is offered there by Matsui.
"The process works well, delivers steam up to [356 Fahrenheit]; however, tooling shops and molders in Japan have been acquainted with the technique and the components for years, while there is much less infrastructure for it here," says Cipkar. "At present, there are too many variables to consider it as a viable choice in North America, but we will continue to investigate it as another option."
Mikell Knights, senior correspondent
Contact:
Contura MTC GmbH, 49 23 73 396 4650, www.contura-mtc.de/mold-temperature-control.html
Crest Mold Technology Inc., 519-737-1546, www.crestmold.com
Regloplas Corp., 888-799-4110, www.regloplas.com
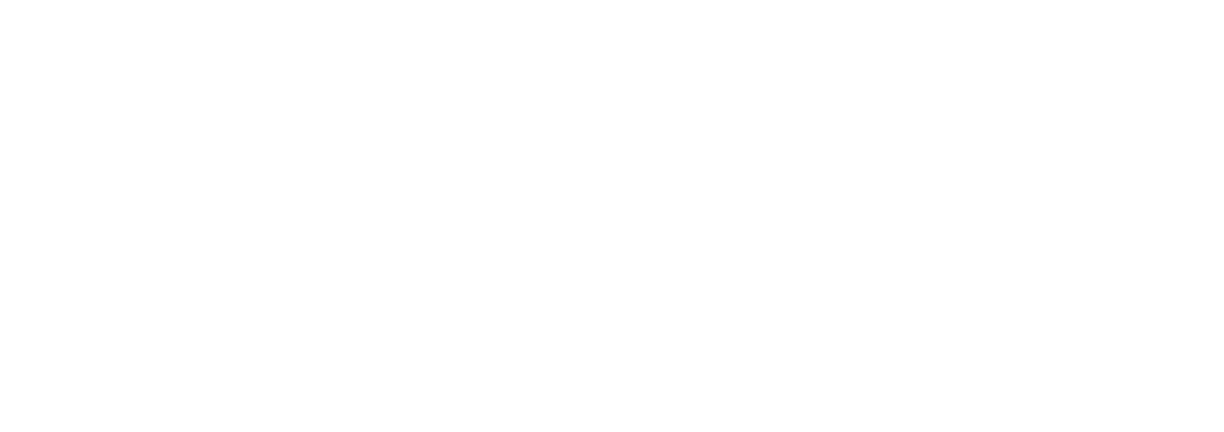