This class of robots is able to work alongside humans without safety guards. It is one of the fastest growing areas, according to the Robotic Industries Association, Ann Arbor, Mich. With innovative force-sensing technology, these robots will stop operating if they come into contact with a human.
DO YOU HEAR WHAT I HEAR?
Hearing aid components are becoming smaller as users seek greater comfort and more discreet devices. For producers of these components, two- or three-axis robots once met manufacturing needs. With the reduction in size, the job has become more demanding, making robotic flexibilty more important.
Hearing aid maker Oticon Inc., Somerset, N.J., which has been using robots for a decade, just upped its game with a six-axis collaborative robot from Universal Robots USA Inc., East Setauket, N.Y. This is the U.S. arm of Universal Robots A/S, Odense, Denmark.
Arne Oddershede, group leader of the maintenance unit at Oticon's test and production center in Thisted, Denmark, says the company's production process can't be performed manually.
"The parts for modern hearing aids are getting smaller and are often only a millimeter in size," Oddershede says. "We looked for a solution that can suction small parts out of a mold. This was impossible manually. We needed a more flexible solution that would also be economically viable for smaller production runs."
There are many challenges for a robot that wants to be effective in this line of work. Within the fast-paced world of medical engineering, processes are constantly changing. Robots need to be precise and have intuitive user guidance. Because of a broader range of hearing aid models, they also need to be able to handle decreasing batch sizes.
Armiga A/S, Thisted, a systems integration specialist, identified the UR5 as meeting Oticon's needs. The six-axis articulated robot arm from Universal weighs only 40 pounds and has a payload of 11 pounds. This robot can pick and place and has a working radius of 33.5 inches.
"We realized that two- or three-axis robots were not suitable for the job," says Lars Gasberg, sales manager at Armiga.
ALL IN THE DAY'S WORK
It took just one day to install the UR5 for its new task in Oticon's molding shop, where the company handles components such as wax filters with dimensions of less than 0.04 inches. These are fitted to the inside of the hearing device to protect the electronics from wax buildup in the ear.
The robot is mounted firmly to the injection molding machine so that it can position itself over the mold and suction the parts using a specially designed vacuum system. This suction tool can accommodate up to four tiny components simultaneously. The UR5 has been programmed to engage the suction mechanism only when the mold is open. Once it has taken the parts out, the robot gets out of the way. The injection molding machine can go on to the next cycle.
If more complex parts are being molded, they are handled with pneumatic gripping tools. Because of its six axes, the UR5 is very maneuverable and can rotate or tilt the parts in order to lift them quickly out of the mold. The robot works in 4- to 7-second cycles, depending on the size of the production run and the component.
Oddershede emphasizes the accessibility and logical design of the UR robots.
"Since we produce different batch sizes and components when developing new products, it must be possible to easily reprogram the robot," he says. "With a traditional robot, this involves a computer and requires specially trained staff, typically a programmer. But with the UR5, any member of the technical staff can literally grab the robot and show it the motion sequence using waypoints."
TACKLING IN-MOLD LABELLING IN CHRISTCHURCH
Talbot Technologies Ltd., Christchurch, New Zealand, is a processor that serves myriad industries through its thermoforming and injection molding operations. The company traditionally has relied heavily on manual handling of products although in some cases it had used fixed-rail robots. But Talbot had to streamline production after a period of growth. A fixed-rail robot would not have the capacity or versatility to achieve the needed results.
UR10s have been put to work on complex tasks, moving between in-mold labelling, transfer molding and co-molding. This model from Universal Robots can move up to 22 pounds and has a reach of up to 51 inches. A graphical user interface offers a teaching function, which allows the operator to grab the robot's arm and show it how a movement should be performed.
"The UR10s have enabled us to combine functions — helping us to better streamline the process flows," says Steve Wilson, executive director of Talbot.
Merle R. Snyder, senior correspondent
Contact:
Armiga A/S, 45 9798 2518, www.armiga.dk
Oticon Inc., 800-526-3921, www.oticonusa.com
Talbot Technologies Ltd., 64 3 338 9084, www.talbottechnologies.co.nz
Universal Robots USA Inc., 631-610-9664, www.universal-robots.com
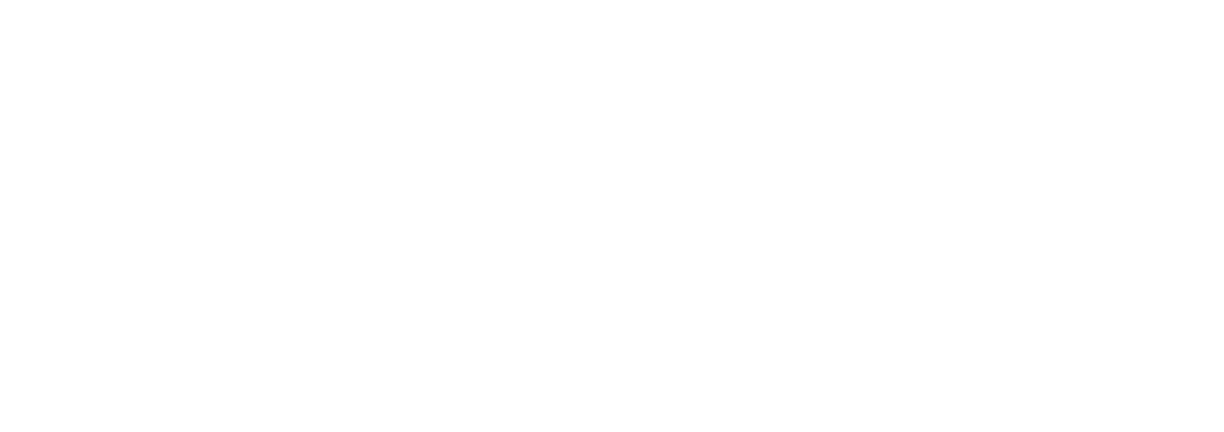