Six-axis robots have been around for a while, but the variety and complexity of these machines and the programming used for them is evolving as plastics processing markets mature. Stateside, the quest to manufacture efficiently can mean incorporating automation technologies even before a processor lands a contract. In fact, such automation may be necessary to land a contract. Companies profiled in this section offered updates on the evolution of how robots are designed and how the technology is applied.
WORKING WITHOUT A SAFETY FENCE
Fanuc America Corp., Rochester Hills, Mich., has introduced its CR-35iA collaborative robot, which it calls the industry's first 77-pound payload force-limited robot designed to work alongside humans without the need for safety fences.
Certified to meet international safety requirements for robots, it can perform many tasks alongside human workers, including tending machines, handling heavy payloads that require lift-assist devices or custom equipment, palletizing, packing and carton handling.
One application, which is already in service at General Motors Co., is to assist workers who are required to lift spare tires into vehicles on the assembly line. "The CR-35iA can work alongside the employees assigned to this task to help reduce injuries associated with repetitive or heavy lifting," says Greg Buell, Fanuc America product manager.
"The Fanuc CR-35iA collaborative robot allows shared workspace between an operator and the interactive robot," Buell says. "The highly sensitive robot gently stops if it comes in contact with the operator, allowing the robot and human to work side by side." The six-axis robot has a soft foam green cover that protects workers who are in direct contact with it. The robot's shell distinguishes the collaborative model from standard yellow Fanuc robots.
The Fanuc R-30iB controller uses high-performance hardware and network communications to deliver integrated motion-control functions, relying on a patented iRVision system to provide visual tracking. The R-30iB controller features Fanuc's iPendant touch color interface, which allows easier setup and troubleshooting.
Based on the latest Fanuc Series 30iB CNC controller, the R-30iB robot controller is compact, providing customers a significant space savings. The R-30iB controller is also energy efficient, requiring less power consumption than previous models, and is available with an optional power regeneration feature.
AUTOMATING END OF LINE
Systems integrator Schneider Packaging Equipment Co. Inc., Brewerton, N.Y., was challenged by a plastics processor in the Northeastern United States to upgrade and modernize a plastic bottle packaging line. The manual palletizing of the old system meant line pressure would be concentrated at the point of contact between adjacent cases and product backups could create a jam or push the cases off of the conveyor. Pete Squires, Schneider VP, identifies several factors that had to be considered, including product quantities, clearance, handling requirements under the U.S. Food and Drug Administration, product behavior and bulk consolidation.
Officials decided that a robot was the answer after an analysis of running times and product quantities because repeatable runs are a key factor in robotic efficiency, and the factory had routine run times and quantities. The company chose Schneider's most portable option, the
Robox. This system integrates a six-axis Fanuc robot with over 70 pounds of lifting capacity.
One of the significant costs in operating such a production is the purchase of corrugated cardboard containers that are used to pack the empty bottles for palletizing and shipping to the end customer for bottle filling.
Because the Fanuc has a highly rigid arm and advanced servo technology, the processor could consider packing in much larger containers than had been possible using manual labor. The new system allows the bottles coming out of the production conveyor to accumulate in large quantities. A specially designed end-of-arm tool (EOAT) on this system picks 36 bottles at a time and deposits them in a large plastic gaylord. The gaylord measures 50 inches wide by 50 inches long and holds the equivalent of eight corrugated cardboard containers. The base allows four-way forklift access and filled containers are stacked up to three high fully loaded with lids. Additionally, the EOAT design provides more sanitary packing.
The plastic gaylords have a 1,200-pound capacity and are made with durable rotationally molded linear PE, are water- and rust-proof and UV treated for strength. The end users either recycle or return the gaylords to the bottle maker. The switch from corrugated cardboard containers to plastic gaylords has delivered substantial cost savings.
The automated end-of-line system has allowed the line to run at an even pace on each shift. In only one year, the company says it has been able to cut out overtime while filling orders more quickly.
SPECIALIZING A SIX-AXIS
Because of the increasing demand for automation, robots are becoming more specialized. Within the last year, Denso Robotics, Long Beach, Calif., added a six-axis, compact, high-speed, VS-050 aseptic robot to its product line. It has an ISO 5 clean-room rating and a specially designed coating for applications that require sterilization using hydrogen peroxide and UV light.
Designed to work safely alongside humans, this model meets the IP65 rating for protection against dust and water. This standard is published by the International Electrotechnical Commission.
Denso is seeing demand from the medical devices, pharmaceutical and life sciences markets, says Peter Cavallo, robotics sales manager with Denso Products & Services Americas Inc. Processors with sterilization requirements can benefit from VS series' high speed and other features. This particular model has a cycle time of 0.37 seconds with repeatability of plus or minus 0.02mm. Its reach is 20 inches with a payload capacity of 8.8 pounds.
"It's a very special robot that is designed specifically for the hydrogen peroxide environment," says Cavallo. "It is made specifically to live in that environment. It is super clean."
The applications for this robot include machine tending, inspection, assembly, dispensing, material handling and packaging. The technology inside the arms involves extensive flexible printed circuits. There is through-the-arm wiring with no exposed wires in the clean-room chamber. Speed of the arms and quietness were at the forefront of the design.
Denso, an automotive parts manufacturer, began making robots for use in its own factories. It has been making six-axis models since the 1970s and is on its seventh generation. It has over 20,000 robots installed at its own factories.
"So we've refined the field on that," says Cavallo. "We do a lot of work in that area. The VS-050 is a specialty robot, it is not high volume. You've got to need one to buy one."
SEPRO SEEING INCREASING INTEREST
IN 6-AXIS ARTICULATED-ARM ROBOTS
Since introducing its 6X Visual line of six-axis articulated-arm robots in 2012, Sepro has seen a steady increase in interest in these robots.
"We're seeing a lot more requests for six-axis robots these days," says Jim Healy, VP, sales & marketing for Sepro America, Warrendale, Pa., "They are being used in many different applications. Some processors use a six-axis robot in combination with a Cartesian unit for insert staging, downstream operations, palletizing and so forth but, they are also used for basic side-entry part removal, primarily when overhead clearance is limited. In all cases, however, what customers love is the simplicity of the control."
At a consumer-products molding plant in Illinois, a Sepro 6X-60 articulated-arm robot is working together with a Sepro three-axis Cartesian robot mounted axially on a 550-ton molding press. Two molding cells are installed in the plant; one produces a part with eight metal inserts and the other involves four inserts, but the processes are otherwise the same, says Scott Collins, Sepro's spokesman.
The six-axis robot is positioned in an enclosure at the clamp end of the press along with a bowl feeder that dispenses the inserts. The six-axis robot picks up the inserts one at a time and places them in a staging array. The Cartesian, a Sepro S5-35 model, is mounted in an axial configuration, which means the horizontal beam runs parallel to the centerline of the molding press so that it can pick up the inserts and deposit finished parts at the clamp end of the press.
A major concern about using articulated-arm robots in injection molding has always been the complexity of their programming and control systems. Even straight-line movement of an articulated-arm robot requires coordination of several articulated joints. Some molders feel they need specially trained personnel to handle the programming and maintenance of these robots. Those concerns no longer apply when it comes to the Sepro 6X Visual articulated-arm robots, which use the same control systems as the company's Cartesian robots.
The 6X Visual robots, which are available in five models to be used with injection molding machines from 20 to 4,000 tons of clamping force, were developed in partnership with Stäubli Corp., Duncan, S.C. The technology combines a Stäubli multi-axis robot with the Sepro Visual 3 control.
With Sepro's Visual Control system, the Sepro six-axis robots can be programmed using either the Cartesian coordinates that molders are familiar with or circular coordinates typically used for articulated-arm robots. Operators can also use the pick-and-place programming that Sepro has been using on its Cartesian robots for many years. To do so, the user must identify step-by-step the different points and positions in the robot cycle, such as picking, unloading and stacking. Then the operator manually "teaches" the robot the path between each point, and the trajectory — either straight-line or curvilinear — is automatically computed.
INTEGRATING ROBOTS
AND MOLDING MACHINES
The Motoman Robotics Division of Yaskawa America Inc., Miamisburg, Ohio, has introduced an optional, icon-driven pendant interface that allows users to program its robots simply. A setup wizard leads users through a series of configuration options for robots, conveyors, de-gating stations and other equipment.
The interface allows operators to interact and control the robot by defining each of its actions using language that is familiar to them. For example, instead of using computer code to tell the robot when to perform an action, the interface can present options to the operator like, "Wait for mold open."
By looking at the robot program as a sequence of actions, operators are better able to understand and modify it as needed. This puts the focus on improving the tending operation, rather than programming, says Motoman.
Once a list of robot actions is complete, the interface generates a robot program in Yaskawa Motoman's Inform computer language. The interface supports both the EuroMap 67 electrical interface standard, as well as the older EuroMap 12 format. Hardware interfaces, which allow the operator to electrically connect the robot to an injection molding machine, are optional. The unit can be customized.
The interface supports multiple robots, external axes, grippers, conveyor/drop locations and de-gating stations. Features include a production data screen, built-in mold warm-up option, part stacking option and three levels of security.
The interface may be used with select Motoman DX200 robots. The DX100 controller is also compatible with a pendant upgrade.
Stäubli touts versatility
of 6-axis units
Stäubli Corp. reports that six-axis robots have great versatility for a variety of applications and end markets. Within the plastics industry, these models conduct high-speed demolding, two-shot molding, in-mold decoration and labeling insert loading, control environment molding, product assembly, gluing/sealing, testing and packaging. In particular, testing of the molded component increasingly is becoming a prerequisite, says Stäubli. Its robots can perform the testing that is required within the cycle time of the injection molding machine.
Stäubli's 6-axis series robots are available in payloads of 1.1 pounds to over 176 pounds. In an example of the speed of the robots, a Stäubli six-axis has a demold time of 0.8 seconds inside a 4-second cycle. Its software is VALplast, which standardizes programming for reduced integration time and integrators can manage software evolution and compatibilities so that the molder is aware when updates are released.
Merle R. Snyder, senior correspondent
Contact:
Denso Robotics, 888-476-2689, www.densorobotics.com
Fanuc America Corp., 888-326-8287, www.fanucamerica.com
Motoman Robotics Division of Yaskawa America Inc., 937-847-6200, www.motoman.com
Schneider Packaging Equipment Co. Inc., 315-676-3035, www.schneiderequip.com
Stäubli Corp., 864-433-1980, www.staubli.us/en/
Sepro America, 412-459-0450, www.sepro-america.com
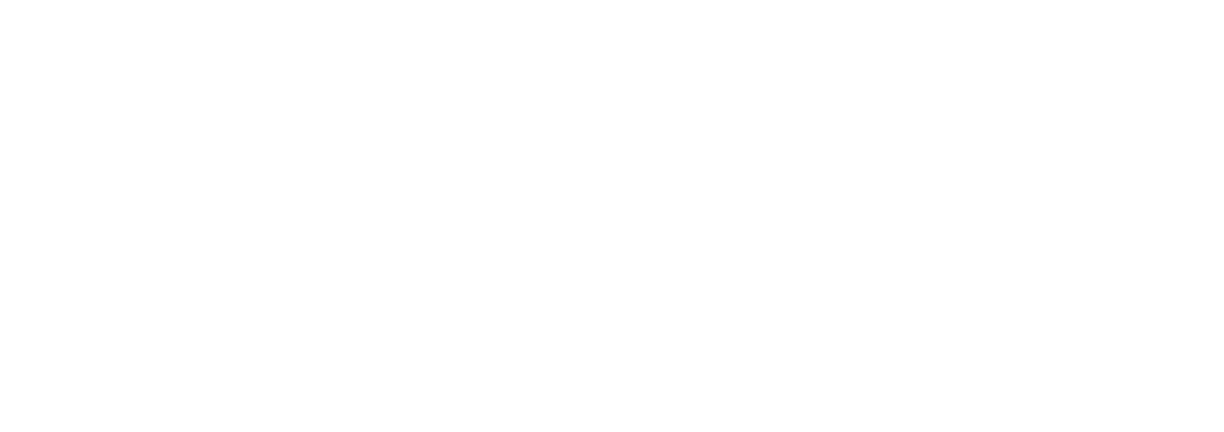