If robots are indeed taking over the manufacturing world, they will be aided by sophisticated end-of-arm tooling (EOAT). A key theme among the products profiled here is the sheer creativity and role of technology in making these tools more effective than ever.
EOATS PRINTED WITH 3-D TECHNOLOGY
ASS End of Arm Tooling Inc., Plymouth, Mich., has begun using 3-D printing to manufacture vacuum end effectors, devices used to suck out parts in injection molding applications. Custom-made gripping devices have been used by ASS to replace traditional EOAT components. The company says that other end effector manufacturers are also using 3-D printing to speed up the design-and-build cycle and believes that could be a trend.
Jürgen Kortberg, VP of North American operations for ASS, says the lightweight design of the 3-D-printed end effector is crucial due to the low-payload Cartesian robots often used in injection molding.
He says a unique feature of the EOAT is its hollow internal channel for the air and vacuum supply, so no external air hoses are needed. "We also manufacture standard off-the-shelf grippers using 3-D printers," says Kortberg. The company's IPG series grippers are made with a selective laser sintering (SLS) printer and expand within the inner diameter of a small opening in a part to grip it.
In order to automate one application in which the weight of the EOAT was a concern for a customer, ASS used its SLS rapid prototype machine to design a custom claw device. The claw is actuated by compressed air and is capable of grabbing a thin cell phone frame and nesting the part for secure handling. An EOAT constructed from traditional components would have been too heavy for a robot demolding cell phone frames. This EOAT is 70 percent lighter than an EOAT made of aluminum components.
In another case, a customer's specifications required a departure from traditional EOAT design because of the compact size and weight restrictions of the robot. In order to meet the specifications of demolding 12 parts, ASS designed a complete EOAT using a CAD program, from which the data was then loaded into an SLS printer. Compared to an EOAT made from aluminum components, the weight savings is 65 percent. Once an EOAT is designed, subsequent ones can be made very cost effectively because minimal human labor is required to manufacture them.
CARBON SPEICAL DESIGNS USED
AGS (Automation Greifsysteme Schwope) GmbH, Bergisch Gladbach, Germany, offers the PreciGrip system, which can be easily configured to meet a plant's needs, using an array of carbon fiber-reinforced attachments and fasteners, along with active elements, such as suction cups, sprue grippers or vacuum cups. The attachments provide stiffness and require only one tool for setup. According to the company, only the active element is adjustable, which reduces retooling time.
The system is compatible with all established EOAT systems, simplifying system changes for the user.
When purchased as a kit, the AGS system includes a number of active elements, including vacuum cups and clamps. One element available from AGS has been specially designed to address a common problem for plastics processors — dropped sprues. To deal with sprues, which can fall out of the tool and land in or next to an injection molding
machine, AGS offers the GZA-S-20-16-L-33 gripper. With a maximum opening of 34mm, the gripper can handle sprues with diameters between 4mm and 10mm with ease.
CREATIVE ARRANGEMENTS ENHANCE CARTESIANS
In a related story of this special report, Plastics Machinery Magazine covers the role Cartesian robots play at molder Vision Plastics Inc., Delavan, Wis.; EOAT perhaps could be named best supporting component. Here is how EOAT works in that Vision/Sepro process: An automated feeder orients brass sleeve inserts and then the robot goes to work. The EOAT on the vertical arm picks up eight sleeves and prepares to load them into the mold. When the cycle ends and the mold opens, the vertical arm descends and pulls two finished lenses out of the mold cavities. Then, the EOAT rotates 90 degrees, so that it can place the brass sleeves into the mold. As a new cycle begins, the robot offloads the finished parts.
Another Vision/Sepro cell eliminates operator involvement entirely by using a robot to position lenses in a mold, remove them from a mold and place the finished parts on a conveyor that transports them under a camera that verifies finished part quality. Meanwhile, the robot places the finished parts on a conveyor that transports them under a camera that verifies finished part quality.
Fipa releases a new seriesof round quick-changers
Fipa Inc., Cary, N.C., a manufacturer of EOAT, advanced vacuum technology, gripper systems, air nippers and tube lifters, has released a new series of round quick-change systems, which are used to attach EOAT on robots. The units feature a safe-lock mechanism, visual locking indications, always-aligned pneumatic air connections and robust construction. The quick-change systems, which snap onto EOAT systems, provide an easy way to change EAOT, as they can be pre-loaded with the appropriate tool and swapped out quickly.
Designed to withstand strong vibrations and rapid acceleration, the new SR Series quick-changers feature snap-on safe-lock mechanisms, color-coded locking indications (red for locked, green for open) and pneumatic air connections that are incapable of being misaligned, ensuring maximum reliability and safety.
"Thanks to the visual locking indication, operators can immediately tell whether our SR Series quick-changers are securely closed and ready for operation," President Rainer Mehrer says.
Made of high-strength, anodized aluminum alloy, SR Series quick-changers are available in diameters of 50mm, 90mm and 150mm. They feature repeatability accuracy to within 0.025mm. Lifting force, maximum torque and weight vary for each device, as does the bending moment, the amount of stress needed to make one bend. The two largest devices are compatible with both Fipa and third-party manufacturers' EOAT.
Merle R. Snyder, senior correspondent
Contact:
AGS GmbH, 49-2204-968-10-0, www.ags-automation.de/en
ASS End of Arm Tooling Inc., 734-542-4398, www.en.ass-automation.com
Fipa Inc., 919-651-9888, www.fipa.com
Sepro America LLC, 412-459-0450, www.sepro-america.com
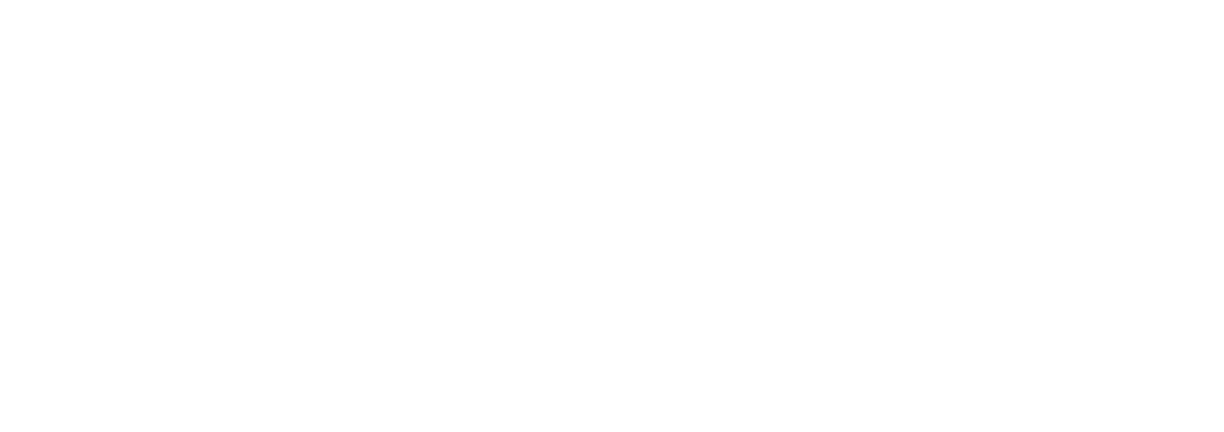