Germany's Fakuma show has always had a reputation as focusing on injection molding, but manufacturers of size reduction equipment roll out plenty of new equipment as well. That is certainly true at Fakuma 2015, which is this month in Friedrichshafen.
Here is a sampling of new products at the show.
Rapid Granulator
A new granulator series from Rapid Granulator AB, Bredaryd, Sweden, is designed for processing the waste produced by thermoforming or for applications that require a low base.
The Rapid LBB (Low Built Base) series is only 24 inches high. The series includes the LBB 300-90, LBB 300-120 and LBB 300-150. Corresponding widths are about 35 inches, 47 inches and 59 inches. The machine runs on motors with up to 30 kilowatts of power. Its maximum throughput is about 2,600 pounds per hour.
When used in a thermoforming application, the granulator can operate with either a roll feed unit synced to the line speed with a loop control or with a tray for skeletal frames falling from the line.
Dave Miller, Rapid Granulator's regional VP of sales at the company's U.S. office in Cranberry Township, Pa., says numerous options are available for the three models, including an extra flywheel, additional hoppers, integrated feed rolls, soundproofing and evacuation systems. The machines also can be used as sheet granulators as well as for the final granulation step under a shredder. Films and sheet up to about 0.3 inches thick are also suitable.
Rapid says it is easy to access the interior of the granulators for service because they use split screen boxes and split screens.
Lindner
Lindner reSource GmbH, Grossbottwar, Germany, plans to exhibit the Apollo 1900 single-shaft shredder designed for large pieces or baled materials and higher throughput rates.
The 1900, with a rotor length of 1900mm, or about 75 inches, becomes the largest in the Apollo series, which was launched in 2014. Other models are the 700, 1000, 1300 and 1600. All models have a 14.6-inch rotor diameter.
Lindner's profiled rotor is designed for molded parts, tubes, shapes or film, and a square blade rotor is available specifically for sheets and start-up lumps.
The hopper can be moved backwards hydraulically to provide access to the cutting chamber over its full length and width. Cleaning and blade changes can be performed without climbing into the hopper. The segmented bottom of the cutting chamber helps prevent jams and a modular screen system enables quick screen changes.
Harald Hoffmann, Lindner managing director, says the Apollo shredders have a relatively short payback period. "Their low energy demand helps to protect the environment and save operating costs," he says. "It was therefore an easy decision for us to launch the new 1900 model with a view to meeting the market's brisk demand for even higher shredder throughput rates."
Wittmann
Wittmann Kunststoffgeräte GmbH, Vienna, has added a screenless granulator designed to sit directly next to an injection molding press and grind hard and brittle pieces.
The low-cost Junior 3 Compact model is 30 percent smaller in size and weight than its predecessor, according to the company.
It can handle throughput of about 66 pounds per hour. The cutting chamber is about 9 inches by 18 inches.
Wittmann says it is ideal for granulating sprues that are delivered to it by robots or conveyors. It produces an extremely fine granulate and has a low rotor speed that minimizes the risk of thermal damage to the material. It is also easy to clean.
The Junior 3 Compact granulator will be available in the U.S. during the first quarter of 2016.
Tria
Two noteworthy new granulator models that are now available in the U.S. market are planned for display by Tria SpA, Cologno Monzese, Italy.
The TF 120-30 thermoforming granulator is the largest model in Tria's TF series. It is a compact in-line granulator for thermoformed film up to 50 inches wide. The feed opening is 50 inches by about 5 inches. There is also a manual feed hopper with dimensions of about 5 inches by 11 inches.
The machine, which has a rotor diameter of about 12 inches, runs at 420 revolutions per minute. Average production throughput is between about 1,500 and 1,800 pounds per hour.
Other key features include a small footprint (74 inches by 49 inches) and low overall height (52 inches). Tria GM Harald Nilson says it uses about 30 percent less power than comparable machines on the market.
Tria also plans to display its BM-K 90-42, which is a compact model in the 42 series. This granulator is designed for hollow or blow molded parts or bottles. Its cutting chamber has an opening of about 36 inches by 17 inches. The unit has a 30-kilowatt motor that provides a throughput of about 2,200 pounds per hour.
Both units planned for Fakuma are fully soundproofed.
Weima
Weima Maschinenbau GmbH, Ilsfeld, Germany, plans to show the WLK 1000, a single-shaft shredder suitable for a wide range of materials, including thermosets and elastomers. It works well as a preliminary unit integrated into a two-stage operation.
The unit has a hydraulic drive that produces 22 kilowatts of energy. Weima claims it boosts the energy efficiency per ton of processed material and still operates continuously at high torque values.
The WLK 1000 can operate in harsh conditions, including outdoors. Counter knives are adjustable. Screens can be changed easily. Options such as the innovative V Rotor with adjustable counter knife allow for optimum shredding results, while a variety of other options, such as a gearbox limit switch, reverse counter, hydrodynamic clutch and safety switch, provide additional safety features.
The shredder can be filled via conveyor belt, forklift or manually. It has a 14.5-inch diameter for high output. The hopper opening is about 39 inches by 57 inches.
Erema
Erema GmbH, Ansfelden, Austria, introduced its Intarema RegrindPro, which is especially suited for processing thick-walled packaging, waste electrical and electronics equipment and automotive materials.
The unit is designed to handle materials with high bulk density, high moisture content and varying compositions. It also can accommodate a wide variety of impurities, such as rubber, silicone, wood, paper and foreign polymer contaminants.
The combination of an optimized preconditioning unit and the new gentle universal screw is a new feature. Regrind particles are warmed in the preconditioning unit. Compared to other Intarema systems, this step involves slower turning of the patented rotor disc and a longer dwell time. This allows material to melt in the extruder with minimal shearing forces, while leaving impurities in the melt large enough to be filtered out efficiently by a high-performance filter.
This provides a high degree of flexibility and high throughput. The same system can process regrind with varying viscosities, while the high-performance filter systems ensure high throughput and high melt quality.
Ron Shinn, editor
Contact:
Erema North America, 978-356-3771, www.erema.net
Lindner America LLC, 919-783-7719, www.lindner-resource.us
Rapid Granulator Inc., 724-584-5220, www.rapidgranulator.com
Tria America Inc., 704-716-0060, http://triaamerica.com
Weima America, 803-802-7170, http://weima.com/usa
Wittmann Group Inc., 860-496-9603, www.wittmann-group.com
Ron Shinn | Editor
Editor Ron Shinn is a co-founder of Plastics Machinery & Manufacturing and has been covering the plastics industry for more than 35 years. He leads the editorial team, directs coverage and sets the editorial calendar. He also writes features, including the Talking Points column and On the Factory Floor, and covers recycling and sustainability for PMM and Plastics Recycling.
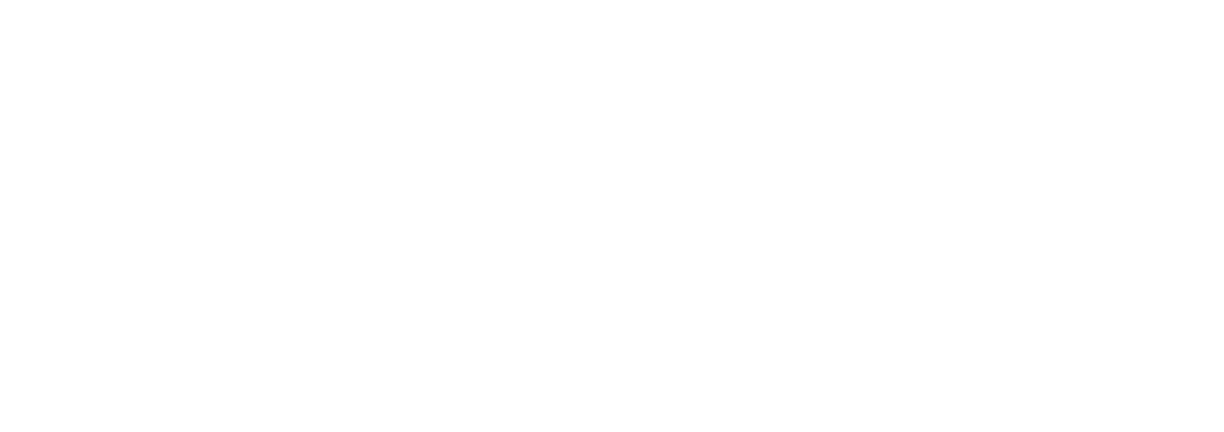