Wittmann Battenfeld's Cellmould driving foam injection molding innovations
Wittmann Battenfeld GmbH, Kottingbrunn, Austria, has reported several innovations for foam injection molding with its Cellmould process and technology as the basis for development.
According to a technical report released by the company in June, foam injection molding can bring more benefits than just light weight.
Chemical and physical foaming polymer processing has been in use for at least 40 years as a way to increase the accuracy of the final part while reducing sink marks and warpage due to material shrinkage, says Wolfgang Roth, head of application technology at the injection molding machinery maker.
The process is experiencing a renaissance, says Roth, driven primarily by end markets like automotive that are increasingly embracing the benefits of lighter weight, low-cost, high-performance parts.
Wittmann Battenfeld, working with Schaumform GmbH, a technology company based in Hutthurm, Germany, has found ways to create a foamed part with a high-quality, high-gloss surface. Their work has led to a way to produce that part — made with a compact/solid outer skin and foamed core segments — all in a single molding step. Another promising development emerging from Wittmann Battenfeld's collaboration with Schaumform could extend foam injection molding's potential applications to thermoplastic elastomer (TPE) processing.
Updates to Cellmould machinery components, tooling enhancements and other Wittmann Battenfeld technologies produced the new capabilities, says Roth.
Foam injection molding suppliers' technology is very similar, says Roth, although technical designs differ.
Wittmann Battenfeld's aim is to reduce the complexity of the Cellmould system while making it more reliable. Wittmann Battenfeld's foam injection molding developments are founded on technology developed by its predecessor company, Battenfeld Kunststoffmaschinen GmbH, Kottingbrunn. "We have designed our Cellmould foam injection unit to come as close as possible to the standard injection unit. A Cellmould injection unit operates with a 20 length over diameter (D) standard screw, which has been extended at the front by adding a 5 D mixing section," says Roth.
The 5 D mixing section has a cylindrical barrier design on the Cellmould screw, rather than two sleeve-type check valves, to separate the plasticizing and gas injection sections of the screw. Check valves are used in competing foam molding approaches. "The effort involved in adjusting two check valves to the operating conditions in every application to make them wear-resistant or fail-safe motivated us to seek a simpler solution. We found it in the cylindrical barrier design, which eliminates wear without having to compromise gas density," says Roth.
The Cellmould system features a 25 D barrel with a 20 D three-zone plasticizing screw and 5 D gas injection and mixing zone. It has a gas injector, gas flow-control module, injection accumulator and a central nitrogen generator combined with a compressor unit. It can supply one or several plasticizing units from a single nitrogen generator.
Liquefied nitrogen is pressurized up to 300 bar (4,351 psi), then added to the mixing section of a Cellmould plasticizing unit through an injector during a metering stroke, where the gas diffuses into the melt. Wittmann Battenfeld says nitrogen distribution is intensified by dividing the melt flow into separate currents. A needle shut-off nozzle keeps the melt and gas mixture under pressure inside the plasticizing unit. The Cellmould equipment package also features a control unit that ties into the Unilog B6 machine controls. Cellmould is available for the entire portfolio of Wittmann Battenfeld machines.
CREATING STRUCTURE
The formation of the foamed structure depends on particular conditions of the injection process — such as viscosity, injection speed and degree of foaming. Molders can mold foamed parts two ways: by injecting an under dosage of material into the closed cavity and allowing the expansion of the material through foaming to fill the cavity, or by completely filling the cavity with material and opening the mold with a pre-set high precision clamp stroke.
Wittmann Battenfeld says its Cellmould process can be used to generate a sandwich-like foamed part in a single molding step. "The formation of foam in the outer shell of the melt is largely suppressed due to its contact with the cooled cavity wall, while the hotter core area favors the formation of the cell structure. In this way, sandwich structures are formed consisting of covering layers with a high density, and core parts whose bulk density is 5 to 20 percent lower than the covering layer," says Roth.
Wittmann Battenfeld says that foamed products show a higher expansion rate when exposed to the same load and break under a lower maximum load. Added to this are notching effects caused by foam cells close to the covering layer. The decline in tensile strength invariably is at least equal to the reduction of part weight. "Under bending load, the absolute values of flexural resistance and flexural strength are also reduced. However, since sandwich structures are much more resistant to this type of load, the loss of flexural strength is significantly less than for tensile strain. In other words, it is possible to realize rigid components with a lower weight," says Roth. Testing documented an instance where foaming to a degree of 15 percent yielded an increase of 4.8 percent in rigidity in relation to weight compared to a part without foam.
HIGH-GLOSS FOAMED PARTS
Foamed parts with a high-quality surface have always been difficult to achieve, says Roth. Lightweight foamed parts often show characteristic striations or fogging on the surface. This is due to the gas bubbles penetrating into the flow front of the melt during the injection process. This gas-infused melt flow front solidifies when it contacts the cooler cavity wall, and subsequently remains unchanged. Molds with highly polished surfaces, which are typically used in the production of high-quality parts, are not recommended when foam molding.
Wittmann Battenfeld found that the negative impact of gas bubbles on the surface of a part could be virtually eliminated if its Cellmould process is combined with cyclical, dynamic mold tempering. Employing dynamic mold heating and cooling rather than maintaining the mold temperature at a steady state significantly influences the quality of the part surface, says Roth.
Wittmann Battenfeld combined the Cellmould system with its Variomould system, which uses hot and cold mold temperature controllers that rapidly raise or lower the mold temperature, to provide fast thermal changeover. In this system, the cavity wall of the mold is heated immediately before injection of the gas-infused melt. "The material does not come into contact with a cold cavity wall at first, which allows the melt front to form a closed surface at the end of fill before the melt solidifies. Excellent surface quality can be achieved," says Roth.
Wittmann Battenfeld also incorporated its BFMold technology in its research. BFMold uses the entire volume of space below the mold cavity and typically consists of a valve switching unit and the company's Tempro plus D Vario 180 pressurized water-tempering unit (designed for BFMold). Water conditioned by the tempering unit floods the space behind the mold cavity for rapid heating and cooling.
FOAMING ELASTOMERS
One intriguing development involves the foaming of TPEs. According to the technical paper, "while good foam structures can be achieved by chemical or physical foaming of materials such as polypropylene and polyamide, our test series have revealed that most types of thermoplastic elastomers can only be foamed by physical foam injection molding." Roth says that only TPEs based on thermoplastic polyester show acceptable results in terms of foam structure, fineness of cells and uniformity or evenness of foaming throughout the part. "Tests have shown that the softer the TPE formulation, the more strongly surface problems will show up," says Roth. TPE part surface problems are more likely to occur if the mold cavity is draw-polished or high-gloss polished, says Roth. Wittmann Battenfeld says air trapped in the mold can become trapped between the cavity wall and molded part. This can lead to surface imperfections. However, the surface problems with foaming of thermoplastic elastomers can be significantly reduced by using medium to low injection speeds of the gas-infused melt, says Roth. Equally positive effects can be obtained by applying a textured, bead-blasted or grained surface to the cavity wall. "This allows gas or air bubbles to escape through micro-venting channels milled into the mold contact surface," says Roth.
Striations on the surface of a TPE foamed part caused by gas can also be minimized with the use of dynamic mold tempering around the contours of the visible side of the part. Roth says TPE foam injection molding with dynamic mold tempering can be further enhanced through the use of a high-precision mold-opening movement. In this approach, the mold cavity is filled completely with the gas-infused melt, then the mold is opened at the same rate of foaming in the part, using a pre-set high-precision stroke of the injection machine. Wittmann Battenfeld says this multi-technology concept can produce various high-end items at low-cost, including high-quality soft foam padding for vehicle armrests and shock absorbers for hand-held appliances.
Roth says foaming elastomer could have potential in automotive taillight housings that have special rubber foam seals. TPE could replace the rubber in that application. "It could be a two-step process where the housing is molded in the first step, followed by overmolding of the foamed TPE, if bonding between the two materials can be achieved," he says.
Mikell Knights, senior correspondent
Contact:
Wittmann Battenfeld GmbH, +43 2252 404 0, www.wittmann-group.com
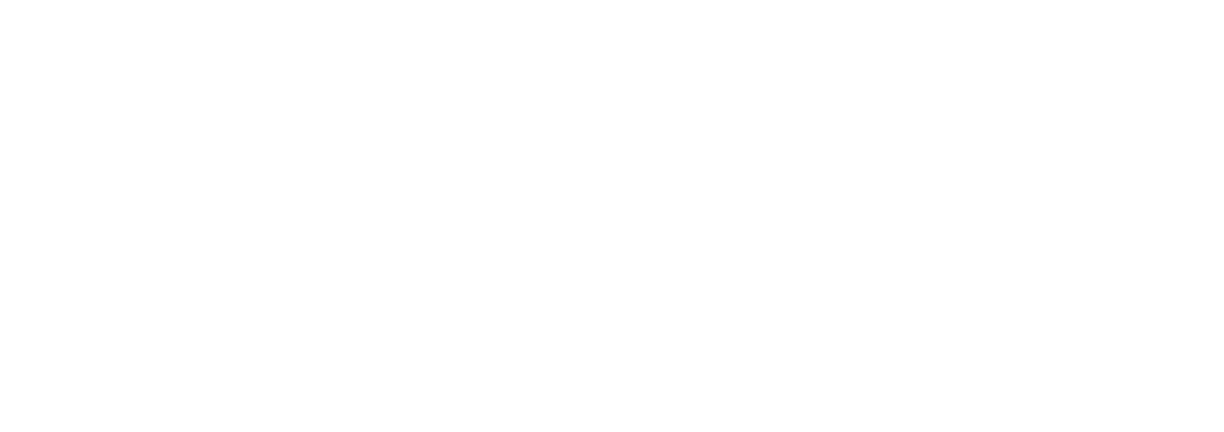