A novel monitoring and control system for plantwide or turnkey injection molding cells highlights a range of high-value ancillary technologies coming to the Americas from a South Korean OEM.
Yudo Group, Incheon, South Korea, known in the Americas primarily as a supplier of Yudo hot-runner systems and Yudo-Suns take-out and Cartesian robots, is establishing its first technical development center in North America to promote its diverse range of products, including its real-time, plantwide monitoring and control system, newly available in the U.S. and Canada. The Concord, Ontario, center will be completed in January.
MONITORING FROM MOLDING CELL
TO PLANTWIDE
Yudo Group last year launched Consilience, a production monitoring and control technology developed in-house that ties communication involving all equipment in a work cell into a single platform. Processors can use the technology to identify and eliminate process or production bottle-necks. Target applications include the electronics and automotive industries, micro-engineering, packaging and PET preform molding.
Consilience can keep an eye on a single work cell or monitor every molding machine and the ancillary equipment related to each press on a plantwide basis. "Consilience is about harmonizing the communications between existing components at work in a molding cell. It is a capable management tool where one can view the status of any individual component in the work cell, to discover problems or dial in the most efficient overall operating parameters," says Stefan von Buren, GM-technology development, who works at the development center.
The Consilience technology can be linked with any injection machine of any size, age and configuration, but, more importantly, it also works with upstream and downstream equipment that competes with Yudo's products. "It is not necessary that a customer purchase or have any equipment of any kind from Yudo in order to operate the Consilience technology. Any piece of equipment from any manufacturer can be tied to it," says Rick Unterlander, GM-process development, who works at the center.
Data relating to the status of an injection molding machine as well as information about molds, hot-runner systems, temperature control, materials-handling devices, automation and critical equipment off the production floor (like inventory or factory automation areas), are collected to generate user-customizable reports. Any device relating to processing and production can be monitored and controlled with the software system, says Unterlander.
GET TO KNOW IMC
The engine driving the Consilience technology is the result of a combination of proprietary software and select hardware that Yudo calls Integrated Monitoring & Control (IMC). The IMC system collects data from sensors and interfaces placed on each piece of equipment in the molding cell. That information is pulled by a network hub into a computer server that is part of the hardware package. Information is distributed wirelessly to the machine operator via a display screen integrated into the molding machine or a standalone unit, and to computer screens and mobile devices used by management, says Unterlander.
Users organize and evaluate the data to detect supply chain faults before operation (for example, empty material silos); view machine set-up, start-up and operating status; simplify production scheduling; minimize cycle time and machine downtime; and establish indicators of productivity by tying into an Enterprise Resource Planning (ERP) system, says Unterlander. Yudo's IMC technology is offered in the IMC M version for plastic part production and manufacturing applications, as well as the IMC A version for metalworking and machine tool making, says von Buren.
Yudo has six commercial, plantwide installations of the IMC-based Consilience technology in South Korea and Vietnam, says Unterlander. Because each system is customized to the processor's needs and level of production manipulation required, Yudo cannot discuss the productivity gains a processor can expect if it invests in the technology.
The Consilience technology follows a steadily intensifying industry trend in which suppliers are offering technology that opens pathways of communication between different types of equipment operating in a molding cell, which inevitably brings about process and production efficiencies.
These approaches are employed as predictive maintenance tools that collect and analyze data from a host of devices. The effort to pull data from every device in such an unprecedented manner for process and production efficiency and predictive maintenance is described as the Internet of Things (IoT).
In the past year, new monitoring and control systems have been announced by non-machinery OEMs, including materials-handling supplier Novatec Inc. and RJG Inc. Injection molding machinery suppliers that offer a range of related ancillary equipment also launched new monitoring systems, including Engel GmbH and Wittmann Battenfeld and Milacron LLC.
OTHER CAPABILITIES
Technology from all of Yudo Group's divisions will be present when the company completes construction and furnishing of its 13,000-square-foot development center, Yudo ValuePro Lab. The center will include a showroom equipped with two injection molding work cells. The smaller-tonnage injection press will be used for development activity, while a large-tonnage unit will support customer runs and demonstrations, says Unterlander.
The Yudo Co. division of Yudo Group produces a range of hot-runner temperature controllers, electrical servo-valve cylinders and sequencing timers, in addition to an extensive lineup of hot-runner system products that are already sold stateside through Yudo Inc., Livonia, Mich.
The Yudo-Suns division has two automation units. They include a take-out robot unit that produces ultralight, traverse, side-entry and swing-type servo-driven Cartesian robots suited to injection molding presses with clamping tonnages from 33 to 11,000 tons. The second automation unit handles factory automation, producing specialized six-axis and beam-type robots that are designed to be application-specific, targeting car manufacturing, optical equipment, in-mold labeling, cell phones and home electronics production, says von Buren.
Lesser known in the U.S. are Yudo-Suns' process-control products, which consist of heating and cooling systems, including chillers, air coolers, steam controllers and mold-temperature controllers; and materials-handling products, such as resin dryers and vacuum loaders, says Unterlander.
The Yudo PET One division manufactures molds for medical, packaging or PET preform applications, generally designed with two to 96 cavities and available in hot or cold halves, says Unterlander.
Yudo-Robotics is the division least known outside of Asia. It manufactures robotics for the metal machining industry and supplies equipment that supports factory operations, such as gantry loader systems and automated guided vehicles.
In addition to its divisions, Yudo operates ValuePro lab as a separate business that provides consulting, research, engineering and design services to customers. Engineers from each Yudo business sector work through the ValuePro Lab to analyze the customer's injection process for ways to optimize operations, says Unterlander.
Yudo also operates Mote, its Molding Technology Center that tests and researches the company's products in a specialized process and production environment. Another Yudo unit, the Floway Lab, provides a melt-flow analysis service as well as concurrent engineering that shortens the time between design and manufacturing, says Unterlander.
Mikell Knights, senior correspondent
Contact:
Yudo ValuePro Lab Canada Inc., 905-669-1110, www.yudo.comYudo Inc., 734-744-8120, www.yudo.com
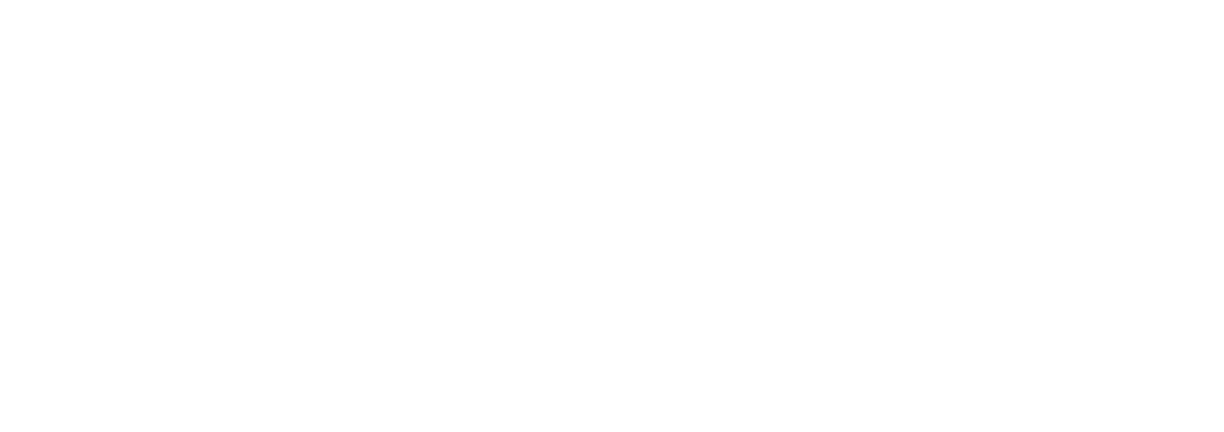