Injection molders have for years been able to collect data that shows exactly what is happening in real time during every step of an injection cycle. Thermoformers have mostly operated without that instant information, but a new monitoring system from ToolVu LLC is providing a peek into the process.
"This product takes the 'black art' out of the thermoforming process," says Ian Strachan, international business development director for ToolVu, Boca Raton, Fla. "The real-time information lets a user monitor the quality of the parts being made. That can be a game-changer."
Cost savings can be substantial, says Strachan.
The system works by adding multiple temperature sensors, plug mold and air clamp sensors, a tool-strain gauge sensor and others to an existing thermoforming machine and tool. Data from these sensors are compared against an "ideal" cycle and displayed on a monitor.
"Any deviation from the ideal cycle is seen on the monitor and can be corrected," Strachan says.
Factors that can be monitored include plug speed and distance, vacuum pressure, form air pressure, sheet temperature, ambient air temperature, tool temperature, tool strain, platen position, load cell, sheet sag and coiner/downholder pressure and distance.
During a demonstration at the SPE Thermoforming Conference in September, Strachan explained that the ideal cycle is determined during initial setup and the parameters are stored in the ToolVu system. The ideal cycle was shown as a set of lines on the monitor. All parameters were shown as lines on the same screen, and when one parameter deviated beyond a set value, an alarm sounded. Alarms can be set at multiple levels for each parameter.
Alarms also can be sent by email. Cycle parameters also can be monitored remotely from ToolVu's Florida office.
"This system does not eliminate the need for an operator," Strachan says. "But it lets the operator know when the cycle is starting to wander out of spec."
Strachan says thermoformers have typically measured their products for quality at the beginning and end of shifts.
The information gathered by ToolVu can shorten start-up times and scrap by as much as 50 percent, reduce risk of damage to equipment, and record forming and trimming cycles for tracking and audit. Analysis of the data can help reduce cycle times, optimize vacuum bleeds on deep-draw parts, monitor strain on trimming blades and indicate when preventive maintenance is needed to avert breakdowns.
Strachan says an average ToolVu system costs about $50,000, although that total can vary since all installations are customized for the processor. He estimates a return on investment of four months.
The ToolVu system originated in Germany four years ago and about 100 units have been installed in Europe. There it focuses on decreasing cycle time. Strachan acquired the rights to further develop ToolVu and sell it in all English-speaking countries. He opened a U.S. office and has continued to develop the product by adding more sensors to collect even more kinds of data. He has sold about 25 units in the U.S.
Strachan is also talking to some thermoforming machinery manufacturers to make ToolVu an option or a standard feature on new machines.
He says one processor has reported that he has made as many as 1 billion parts without a reject when using ToolVu.
Ron Shinn, editor
Contact:
ToolVu LLC, 561-674-9395, www.toolvu.com
Ron Shinn | Editor
Editor Ron Shinn is a co-founder of Plastics Machinery & Manufacturing and has been covering the plastics industry for more than 35 years. He leads the editorial team, directs coverage and sets the editorial calendar. He also writes features, including the Talking Points column and On the Factory Floor, and covers recycling and sustainability for PMM and Plastics Recycling.
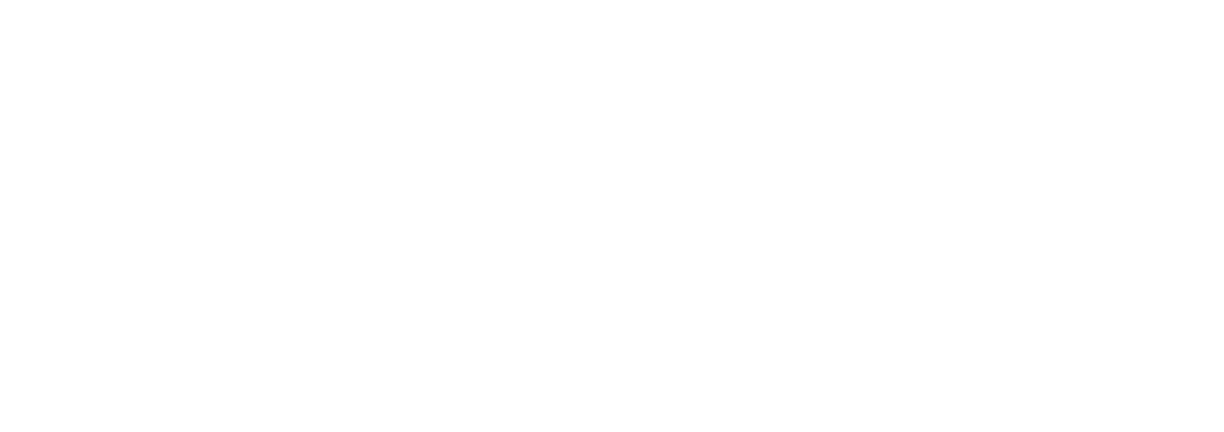