At NPE, Enercon Industries corp., Menomonee Falls, Wis., released its new series of blown arc and blown ion plasma treaters, each of which is available in a standard model or a higher-performance Pro Series model. Enercon says the blown arc series is ideal for improving surface energy of nonconductive surfaces to facilitate quality printing, as well as ensuring adhesion of labels and coatings. It works with extruded, pultruded, molded and formed PE, PP, PET, nylon, vinyl, PS, PC, PVC and many other thermoplastics and thermosets. It's effective for printing, painting, coating, bonding and labeling applications.
Enercon's proprietary blown arc technology forms plasma by blowing atmospheric air past two high-voltage electrodes that positively charge the ion particles surrounding them. By direct contact, these particles positively charge the treated area of the object's surface, making it receptive to any applied substance, such as ink. The treatment is simple to perform, highly effective and reliable.
Enercon's standard blown arc treater includes stainless-steel body construction; compact heads with single cable for easy setup; compressed air; rugged high-voltage transformer for continuous use; independent head operation; front panel controls and indicators; quick-start guide; and USB drive for downloading data and uploading software upgrades. Remote-control operation is optional. The Pro Series adds intuitive touch-screen control; remote control and monitoring; fully independent head operation and monitoring; advanced diagnostics and monitoring; compressed air shutoff; and onboard troubleshooting.
Enercon's blown ion plasma surface treaters improve adhesion by bombarding a surface with charged electrons. Their focused discharge provides high treatment levels in compact areas as well as hard-to-reach areas. The device's standard and Pro Series features mirror the blown arc system's options.
Mark Plantier, VP of marketing for Enercon, says corona treatment works very well for many applications. A separate treatment, which is referred to in some industries simply as plasma, applies gases, such as argon, nitrogen or even compressed air, to the process. It's useful with materials that don't respond to corona treatment, for example, fluoropolymers like Teflon. "What one person calls corona, others might call plasma," Plantier says.
Just before PMM spoke with Plantier, he met with a customer who brought in an application and said, "We want plasma for this." The client's reasoning was that plasma is very effective and the application called for excellent surface treatment. Enercon's lab tested both the plasma and corona methods and found that corona met all the requirements at a lower purchase cost and would have a lower operating cost because it didn't need gas. Plantier said, "Our general rule is, if corona can do it, use corona like our blown arc system."
Plasma treating system shrinks
footprint, raises line speed
The LT 2012 Lectro-Treat plastic surface treating system that Lectro Engineering Co. Inc., St. Louis, introduced at NPE takes 66 percent less floor space than the system it replaces, but will treat the same sizes of plastic parts at higher speeds. Like its predecessor, the LT 2012 is a self-contained plasma treating system designed specifically for 3-D parts. A continuous conveyor carries parts through a plasma tunnel at atmospheric pressure. Oxidized cold plasma is supplied as directional plasma in air, which allows complete treatment of each part on all sides to a level greater than 70 dynes.
The system arrives fully assembled. In operation, there is no heat to cause warping or crazing of the parts, even thin-walled ones. It runs at low frequency, so there is no electromagnetic interference. The conveyor belt is 12 inches wide like its predecessor, and extends 18 inches beyond the tunnel on each end. All Lectro-Treats have vertical and horizontal electron flow, and when the energy reaches a surface, it will not impinge on the surface as a flame- or corona-treating system would but instead wrap around all surfaces of the part.
See sidebar on plasma technology here.
The energy flow offers an unusual and fascinating visual effect. Greg Wood, president of Lectro Engineering, says the company has allowed filming of it at night several times. The phenomenon is what enables full treatment of all surfaces of a 3-D object, no matter the geometry. Wood says another reason the system integrates so easily into a production process is its safety. The Lectro-Treat can generate up to a million volts but there is little to no amperage. If someone put a hand into the tunnel (not advised), Wood says it might scare the person but not hurt him or her. Putting a finger into a corona, he adds, would probably kill the person. The system also won't interfere with computer and communications equipment on the production floor.
Lectro Engineering was founded on plasma surface-treatment technology and its technology development has concentrated on 3-D objects. However, it also has systems on sheet and film production lines using the technology of its sister company, Kalwar Group, Halle Westfalen, Germany. The company was founded in 1965 by Klaus Kalwar, who Wood says invented corona-treatment technology for plastic. The second generation of the family business continues to develop corona technology, recently introducing an aerosol-misting device that works in conjunction with corona treatment and is available through Lectro Engineering.
Plasma technology for
lightweighting composites
Plasmatreat North America Inc., Elgin, Ill., has a broad line of atmospheric pressure plasma-jet technology. At NPE it added a new surface-treatment device to address the accelerating growth of lightweighting projects in an assortment of industries. The new Openair RD2005U device was developed to treat plastic substrates such as sheet molding compound (SMC) and carbon fiber-reinforced plastics, which are increasingly being used to cut weight from body panels and other components.
Andy Stecher, president and CEO of Plasmatreat North America says, "The new device offers an enhanced variety of treatment nozzles, treatment speeds, and treatment distances — all connectable to established Plasmatreat power supply options. This makes it easy for customers to integrate this advanced technology into existing factory automation."
Other features of plasma treatment pertinent to lightweighting applications include increased safety, environmental sensitivity and reasonable cost. Energy usage is low and no solvent-based or mechanical surface preparations are used.
Underscoring plasma's energy efficiency, Stecher says he could leave a treatment device turned on 24/7 for a year and the energy bill would be less than $200. He says the company is focusing on composites because of their increasing use. Everyone thinks first of the automotive sector when lightweighting is mentioned, but Stecher says the approach is spreading into many other sectors, such as the aerospace industry and technologies for solar and wind energy.
Stecher says surface treatment has always been a niche business and perhaps always will be, but there's growth and better recognition. He is very positive about plasma's ability to be part of process automation. "Getting the plasma system set up correctly takes some work," he says, "but once it's dialed in, it simply runs, unless the process is changed. It's process-specific and can treat every component fully and consistently, even when the line moves at 50 feet per minute."
Rob Neilley, senior correspondent
Contact:
Enercon Industries Corp., 262-255-6070, www.enerconind.com
Lectro Engineering Co. Inc., 314-567-3100, www.lectroengineering.com
Plasmatreat North America Inc., 847-783-0622, www.plasmatreat.com
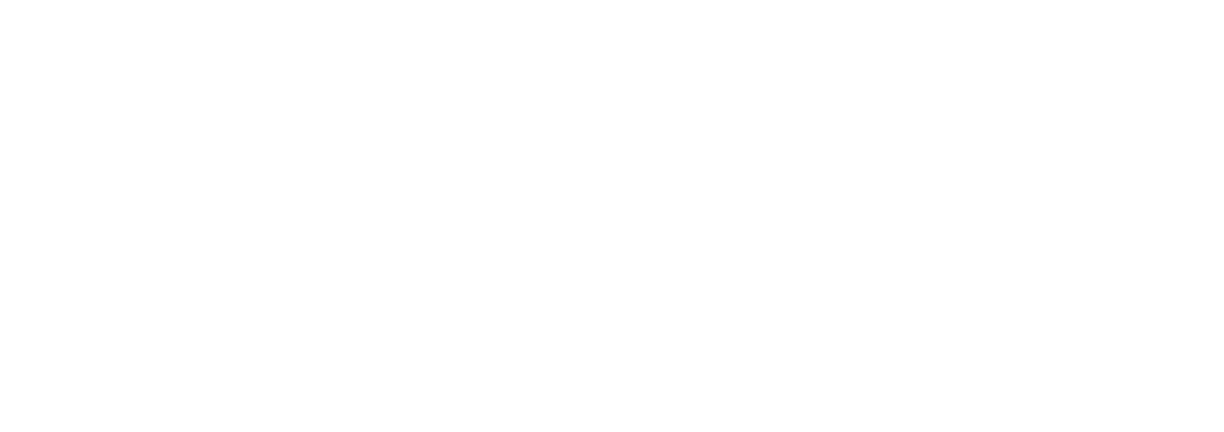