Plastics Machinery Magazine recently spoke with Fraser Reid, who heads up Beier America Inc., Exeter, N.H. PMM was curious about the market for big pipe extrusion technology, one of Beier's specialties.
Reid discussed Beier's new BRD Series extruders, single-screw machines that are feeding lines making HDPE pipe with diameters up to 2,500mm, or about 8 feet. The company has developed a lot of technology to get more than 2,500 pounds per hour of throughput from a 90mm screw. Reid made it clear this development did not begin in the lab or engineering department; it began in the market.
Beier's long-term and largest client, the Moscow-based Polyplastic Group, was extruding a lot of pipe up to 1,500mm in diameter, but its customers were asking the company to go larger. So about eight years ago, Polyplastic asked Beier what could be done. Reid said Beier's top diameters had stabilized around 1,200mm for a while, but the demand for larger pipe was building, especially in developing countries that needed infrastructure.
The development project that would take almost five years to complete was done at Beier's 430,000-square-foot headquarters complex, which opened in 2008, with the cooperation of Polyplastic. The decision was made to start from scratch, to not scale up or modify existing designs.
As the Beier engineers dug into the project, a key question emerged: How do we get more material into the extruder? They knew they had to increase the amount of material going in to get larger pipe out of the other end. What eventually emerged was what they call an eccentric design for the feed throat. In short, it's bigger on the bottom than on the top, with the result being more material can flood into the extruder barrel in a given amount of time.
Most extruders now have the grooved feed throats that were introduced a few years ago. Beier created feed grooves to handle the increased input it wanted, making them larger and also rectangular. Because extrusion lines are systems, that naturally led the engineers to redesign the screw, the barrel and the heating/cooling technology to accommodate the increased material volume. Reid said controlling the heat exchange in the barrel became a critical design goal for the system, and it ultimately led to the development of a brand-new water-cooling system.
Reid said that during the development period, the market was energizing further. Developing countries in South America, Africa and Southeast Asia, along with Middle Eastern countries, began demanding larger pipe. They went from wanting 1,200mm to 1,600mm to 1,800mm, and the trend wasn't slowing down.
The BRD Series extruders entered the market around five years ago, and they have been well-received. Reid said they not only achieve the needed throughput, they deliver a high-quality, homogeneous melt to the die. He adds that one thing that helped Beier to market these larger systems was its policy of always setting up and running a complete line in-house before shipping it to the customer.
Fraser says that's a huge job because the machinery, especially the downstream equipment, which Beier also supplies, is both large and very heavy. And not only does the company run it, it runs actual production as Beier's customer will run it, using the customer's material. It's a massive undertaking that can take months to set up and complete. That could explain why most of the Beier headquarters is given over to manufacturing, including dedicated production test bays.
The fine-tuning resulting from production-level trials has helped define the second and third generations of the machines. Reid said that's one of the main reasons the company does production-scale testing. An equally important reason is that Beier is able to make any adjustments needed in its facility. The customer receives a system already proven to perform and can get it up and running quickly.
Beier, which is part of the global extrusion machinery supplier Beier Machinery Co., Zhangjiagang, China, has its extrusion lines in 70 countries. Reid said business is good in mining areas and where desalination systems are being implemented. The 1,800mm size is currently most popular but the larger lines are also in demand. The company recently shipped all the downstream equipment for a 2,500mm extrusion line to a customer that already had a Beier extruder that could feed it.
Reid said this year saw the first shipment into the U.S. of a four-up — a 90mm conical twin-screw extruder feeding four dies — for extruding PVC conduit. It's a full line, with all the downstream equipment included. It too was fully set up and completely tested at Beier's headquarters with the customer's representatives there to check it out. Beier has been doing high-speed PE dual lines for a while, said Reid, who added that this kind of innovation is virtually always customer-driven.
Beier makes conical and parallel twin-screw extruders for PVC, and Reid said the demand doesn't come solely from pipe and conduit markets. The market for corrugated PVC roofing panels is very big in South America as well as other parts of the world. The top layer is ultraviolet-light-stabilized through sun exposure and the sheet is colored red to resemble traditional terra cotta tile.
Rob Neilley, senior correspondent
Contact:
Beier America Inc., 773-234-3795, www.beieramerica.com
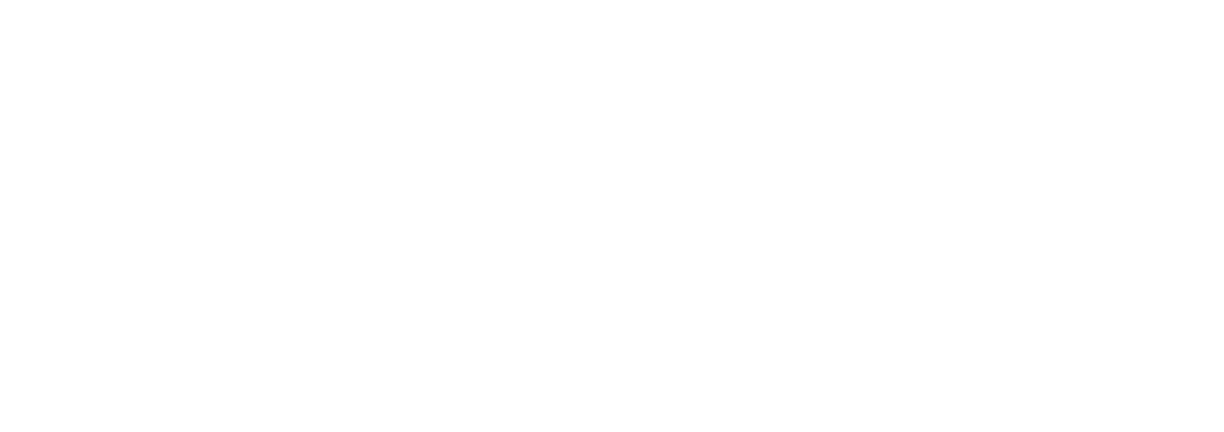