One injection molding machinery-maker from China is determined to gain significant market share in North America. The company is doing it through a unique business model with a U.S.-based injection molder and a chief engineer who has had a distinguished career with Who's Who of European machinery makers.
Tech Bole USA is the U.S. business owned and operated by Ken Parker and Brian Kress through which Bole injection molding machines are sold. Bole machines originate from Ningbo Shuangma Machinery Industry Co. Ltd., Ningbo, China, commonly known as Bole.
Parker and company have been working with Bole for about two years. Parker needed a couple of machines for Tech-Way Industries Inc., his molding company in Franklin, Ohio, that was profiled in "On the Factory Floor" in Plastics Machinery Magazine's July issue (Page 34). Historically, he would rebuild equipment. But he felt that was no longer the way to go.
"I needed to look outside the U.S. to see what was there," he says. "China has been improving their machines for several years, from what I had seen."
He had several of the HPM Universal machines, which at the time were supplied by Welltec Machinery Ltd. of Hong Kong, and he also had a Haitian. He did a search on global trade website Alibaba.com, along with sending an information request, to which he received 40 responses. Bole sent one of those responses.
"When I saw the clamp design, I began to ask more questions," he says of Bole's machine. "The clamp was similar to the original Newbury monotoggle clamps, which apply pressure directly behind the mold. As such, I was intrigued."
Parker's comfort with the Bole machine led to a partnership with the manufacturer and an agreement to become its U.S. representative. When Tech Bole USA made its debut at Plastec West in 2014, the company began a time of evaluation about what it could offer on machines in the U.S. The Bole machines are built in China, so they often had been made to the specifications for that market, including how the heaters are wired.
"At that point, we decided to take that machine back to our place and make recommendations to China," says Robert Jergens, sales manager at Tech Bole. "We wanted something that met our expectations and standards versus selling machines just to sell machines."
Officials made recommendations throughout late spring into early summer. That included establishing what it took to sell machines in the U.S. market. The presses needed U.S. standard platens, nozzles and voltage, among other specifications.
"We concentrated on what many people might think was nit-picking," says Parker, "but in a way, it can become a thorn in the side to many people. We've been through it and as a molder, I did not like waiting weeks for a special nozzle or tip."
By October, Tech Bole USA had machines that met Parker's requirements. Jergens emphasized that the machines had to be ready to go into production when their crates were opened in the U.S. upon arrival from China.
The barrel endcaps have been redesigned, for example, to accommodate the standard set of nozzles that many companies have. That way, if there is a need for replacement, there is no need to hunt for a correct nozzle.
"We don't do any modifications here. It's built in China and delivered," Jergens says. "When the machines came for NPE, they exceeded our expectations. We sold machines off the floor at the show."
The company currently has about 15 installations in the U.S., including some of those at processors that otherwise would have purchased used equipment. Parker estimates that a processor can purchase a Bole machine for about 15 percent less than a competitive model.
"When we took this on, one of the things we had committed to with respect to our customers was to be able to provide a good product for the U.S. market," Parker says. "What I told our people was that we wanted to have a molding machine which was approved by a U.S. molder for use by U.S. molders in the U.S. That is the simplest way I can state it to anyone."
Tech Bole's offerings including the EK Series, which ranges from 60 to 4,000 tons of clamping force and is built to SPI standards. The machines have Bole's center-clamping design, which increases clamp force and parallelism and a larger clamp opening with a longer ejector stroke. That clamping design is key, officials said.
"The uniqueness is that we use a center knuckle to link with the toggle, so by doing that we can give 100 percent tonnage directly behind the mold," explains Jergens. "So it kind of acts like a hydraulic machine, but we're using a toggle to achieve that. By clamping directly behind the mold, we can save up to 2-5 percent on material costs on 80 percent of the molds.
"With the toggle design, we can open up between 10-20 percent further because we're folding out versus folding in," says Jergens. This is known as the outcurve design and hence the marketing slogan, "Throwing a curve."
On tie-bar spacing, Bole machines are the same, or a little larger, than their competitors. The series also has energy-saving full servo-hydraulic pump technology.
During Chinaplas 2015 in Guangzhou, Bole had its booth equipped with a prototype of its DK Series, a two-platen injection molding machine that will be on the market toward the end of this year. Its IMC injection molding compounder is in development and the first prototype will be ready at the end of this year.
DK Series is the next machine style that Tech Bole will offer. The series ranges from 650 to 6,000 tons of clamping force and has a pure two-platen design. Its ball-screw-driven servo motor is used for high-speed platen moving. It has a high-rigidity, sliding-pedal structure, and the bearing capacity for the mold is increased greatly. A four-clamping cylinder works synchronously, offering uniform force for the mold. The machine is designed for quick mold changeovers. It has fewer moving components and less lubrication points for additional savings on maintenance.
The key official behind some of these designs is Hans Wobbe, chief engineer with Ningbo Shuangma Machinery, who was on hand during Chinaplas. Wobbe is well-known as an injection molding machinery expert and has held key positions with many European machinery firms: head of development at Werner & Pfleiderer GmbH, Stuttgart, Germany; managing director of technology at KraussMaffei Kunststofftechnik GmbH, Munich; and chief technology officer responsible for development and production at Engel Holding GmbH, Schwertberg, Austria, for all plants in Asia, Europe and North America.
Since 2014, he has been recognized in China as a foreign expert by the State Administration of Foreign Experts Affairs. When prompted for an interview for a profile during Chinaplas, Wobbe responded that the employees of Bole are the people who carry out the work and should have the credit. Still, he did respond to some specific questions about his goals as chief engineer for the acceptance of the machines in the North American market.
Essentially, Bole wants to achieve a significant market share for large injection molding machines. That is to be accomplished with state-of-the-art machine design with performance characteristics similar to European-made machines.
"China machine manufacturers are in the Western world known as cheap with low [technology] and minor quality," he says. "To improve the situation, you have to improve quality, performance, but stay with low prices. That is the Bole product strategy."
Jergens says that Tech Bole will focus on service above all else.
"We're taking the extra day or two with start-up and training," he says. "We're saying, 'Give us your nastiest, most difficult job and let's run it.' It gives us a chance to verify other sequences and core pulls."
Jergens said the U.S. market is only beginning to see the influx of Asian equipment, and as such, service will be the key to sales.
Angie DeRosa, managing editor
Contact:
Tech Bole USA, 937-475-7797, www.techboleusa.com
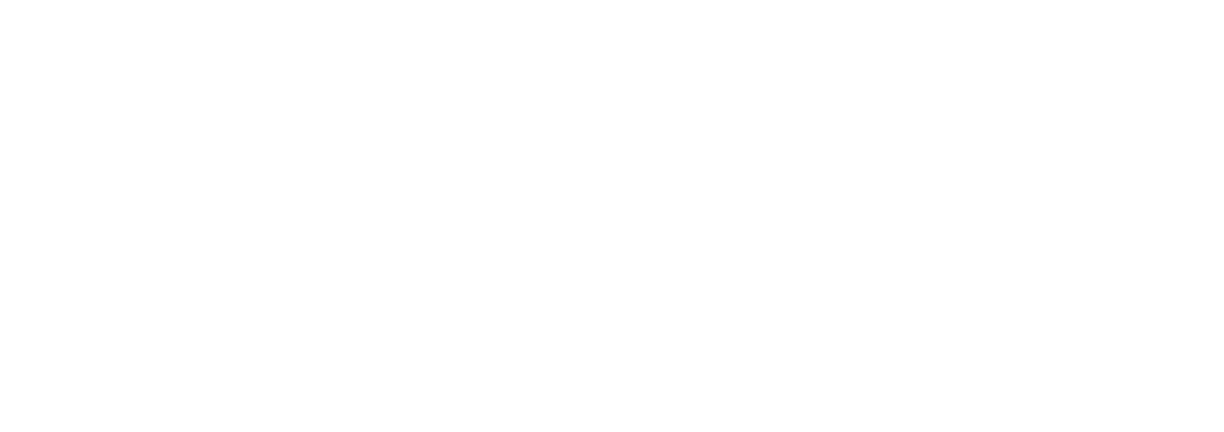