PLC technology advances adjustable barrier for extrusion screws
A retrofit to extrusion and injection screws allows molders to process a wider range of recycled material on a single screw.
Robert Dray, president of R. Dray Manufacturing Inc., Dallas, has designed and manufactured thousands of screws for extrusion and injection molding applications for nearly a half century. Dray has had some level of involvement — from inception or product line growth — with many current or former screw design houses, including Spirex, New Castle and NRM. He was the founder of Feedscrews Inc., now Nordson Xaloy.
Dray is the inventor of a technology add-on to extrusion screws used to reprocess scrap materials for pelletizing or compounding operations. The design allows processors to make an adjustment to the flow geometry of the screw themselves. It includes a slot where an adjustable dam can be placed to control the flow of material through the screw's primary channel. By raising or lowering the dam, using a key-type tool, molders and extruders can control the pressure and flow of the material, forcing more or less material across the barrier flight.
The technology has been patented since 2006, but Dray is anticipating a major advancement. He has built a version with a programmable logic controller (PLC) to handle the process, according to melt temperature or melt pressure variations. He says he plans to apply for a patent for the new PLC capability soon.
The dam, which can be adjusted within a thousandth of an inch, addresses a common challenge for extruders and molders reclaiming scrap plastics — the wide variability of materials contained within recyclable feedstocks. "The post-consumer or industrial scrap materials recyclers are processing into pellets isn't all the same. Customers encountering feedstocks that vary in material composition have to halt production and change the screw to one that processes that material at a desired throughput and quality," says Dray. This means screw changes can be frequent, leading to a loss in uptime and the possibility the screw might not process the scrap material perfectly, which can hamper throughput and productivity. A processor may also have to set aside space to house its growing inventory of screws.
INEFFICIENCIES
INSPIRE CHANGE
Typical screw configurations have zones or sections for material feeding, material melting and metering/conveying. The melting section of the screw is distinguished from the feeding and metering sections. The melting section of the screw is distinguished from the other two common design sections with the incorporation of an auxiliary or second "barrier" flight. The barrier emulates the progression of melting in a conventional square pitch screw design — in which the pitch between successive turns of the flight is the same as the diameter of the screw shaft, says Dray.
The barrier element on the screw in the melt section creates primary and secondary channels; solid unmelted pellets or powder accumulate in the primary channel, while molten material flows in the secondary channel. Barrier screws designed where the primary channel is longer and wider than the secondary channel have a higher melting efficiency, while screws with a more prominent secondary channel are more efficient for melt conveyance, says Dray.
The primary channel typically decreases in width near the end of the melt section, and the secondary channel increases in width to accommodate a larger pool of melted polymer.
The melting section containing the barrier screw technology is where major processing problems can occur. "Controlling the pressure in the primary channel of a barrier screw is paramount to successful plastics melting," says Dray. Forcing material together under pressure makes the product denser and creates higher heat transfer. Processors swap screws because of inefficiencies in controlling the pressure, flow rate and quality of polymers.
DRAY'S DESIGN
Dray's removable/adjustable dam technology consists of a mechanism installed on the back end of the gearbox of the extruder that connects to a rod installed through the center of the screw. The rod extends to the end of the primary channel of the screw (under the feed section) to the last flight in the melting section of the screw where the barrier flight ends. The rod connects to a movable, steel piece (the dam) installed at the root of the screw between the first and second turns of the flight in the melting section.
"The barrier member extends radially from the surface of the screw shaft and generally transversely between the turns of the flight," says Dray. Changing the height of the dam modifies the pressure on the material, which impacts melting, viscosity, flow rates and processability.
Dray has sold at least 30 screw designs with adjustable dams since introducing the technology. One of the early successes was seen in the processing of a fractional melt HDPE from recycled milk jugs.
System pressures, temperatures and product throughput rates were measured on the conventional line using transducers in the barrel and a thermocouple in the melt stream to monitor processing conditions. When the adjustable dam was installed and its height adjusted, throughput increased from 200-300 pounds an hour to 600 pounds per hour while pressure variation changed by less than 50 pounds per square inch and temperatures showed just 1-2 degrees of variation at the center of the melt, says Dray.
St. Joseph Plastics, St. Joseph, Mo., a dealer of ground polyolefin products and full-service recycler that provides size-reduction services and toll grinding, added a removable dam system to a Davis-Standard single-screw extruder it recently refurbished, says Douglas King, a consultant to the company.
"With the changeable dam, technicians at St. Joseph can pull the screw, change the height of the dam and re-install the screw in about two and a half hours, instead of shipping the screw out of the shop for design adjustments that can take weeks," says King. "The adjustable dam allows us to use ageneral-purpose screw and we can change the mixing and compounding ability of the screw by just changing the dam height." The dam allows St. Joseph to run a range of materials on one screw rather than use several screws, each for a different material, says King. St. Joseph uses the dam to achieve maximum throughput while ensuring proper venting. The machine running with the dam technology is helping St. Joseph complete jobs more quickly.
Mikell Knights, senior correspondent
Contact:
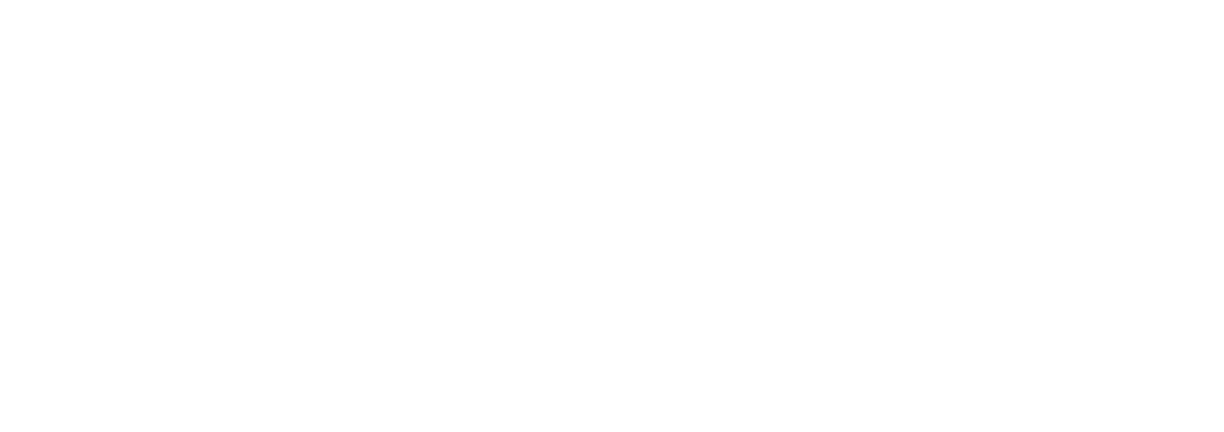