The PMM special report on energy management in our February issue included most of an extensive interview with global plastics processing consultant Robin Kent of Tangram Technology Ltd., Hitchin, England. Kent devotes a major portion of his work to maximizing energy efficiency in plastics processing shops — more than 400 of them so far. However, due to limited space, PMM barely touched on two strategies Kent especially likes. They deserve more attention.
Kent calls these two very different energy savers no-brainers, and it's because the reasons for doing them are so in-your-face obvious that little study is needed. Also, both are relatively easy to do. Each offers fast payback and significant energy savings — at least 25 percent and often more. The upfront investment for these energy savers is relatively low and the return on investment (ROI) comes fast. "A processor has to be crazy to not use them," says Kent, and the many processors that have begun using both technologies in recent years back up that statement.
Low cost, fast payback, major
ongoing savings … it's a wrap
The first of Kent's no-brainers, which he says combines low costs with exceptional ROI, is machine insulation. Wrapping a barrel and other system components will keep process heat where it belongs. Some molders say process heat can be used to heat the production area in cold weather. Kent strongly disagrees. His research shows that process heat generated from electricity is the most expensive way to heat a workspace. A heating/cooling system designed for interior space is much cheaper, especially now that North America is the world's leading producer of natural gas.
Insulating a plastics production machine is about as simple as buying the right size clothes. For example, Uni-Therm International Inc., Lewisville, Texas, supplies an array of shapes and sizes of insulation covers for injection machines, extruders, blow molders and more. Measure the machine, order the appropriate insulation, install and let the savings begin. UniTherm says its insulation systems will pay for themselves in a year or less, and that no other type of energy-saving product will pay back that quickly with so little upfront effort and investment.
For example, UniTherm says if manufacturers spend about 8.5 cents per kilowatt-hour (kWh) and operate 24 hours per day, five days a week, the payback time is less than a year. For a 500-ton injection machine operating 24 hours a day, five days a week, manufacturers could save more than $1,000 a year, after an initial investment of about $600 for insulation. UniTherm says this is a conservative estimate.
UniTherm modified its business model in recent years to make insulating machinery easier and faster. For more than 20 years, the company made custom, reusable insulation covers for process machinery. More recently, the company gave its products a universal design that features standard, off-the-shelf components, which can be configured for virtually all types of processing equipment. Now customers can purchase UniTherm products online, avoiding the cost and time typical of a custom cover. If needed, custom covers are still available.
Machine insulation offers
more than energy efficiency
Insul-Vest Inc., Tulsa, Okla., which supplies a full line of high-temperature machinery insulation and related products, was founded in 1979. That year a friend in the plastics extrusion business called Gordon Pendergraft at his industrial supply company in Wichita, Kan., to say that employees were getting burned around the machines. He wondered if Pendergraft could develop something to insulate extruder barrels and dies.
Using high-temperature materials, the first blankets were made and installed, not to save energy but for safety, which is still a great benefit of machine insulation today. Four months after installing the blankets, Pendergraft's friend called again. During the previous quarter, his company had a large drop in its energy usage — 60 percent. He wondered if the safety blankets could be the cause. Tests showed that the insulation was indeed the cause of the energy savings. That set in motion the creation of Insul-Vest and a totally new energy-efficiency technology.
John Pendergraft, the current president and CEO of Insul-Vest, told PMM that it took a number of years to get a foothold in the plastics industry. During those years, Insul-Vest ran many energy audits on working machines to show real-world results to molders and extruders. The energy savings are undeniable and substantial, the insulation is easy to order and install, ROI is notable and the insulation protects employees. Pendergraft says the idea is pretty well-accepted among plastics processors today. Reflecting that acceptance, Insul-Vest has developed a broad line of products to insulate virtually every type of plastics processing machine, as well as components such as extrusion dies, compression molds and hoppers.
Big injection machines can
enjoy big energy savings
Kent's other no-brainer is retrofitting a variable-speed drive (VSD) to regulate the speed of the pump motors on higher-tonnage (500 tons or more) conventional hydraulic injection molding machines. The induction electric motors used on virtually all conventional hydraulic machines are durable, reasonably priced and easy to maintain, but they run at a fixed speed as they drive the hydraulic pumps. During most of a molding cycle, the machine does not need all the oil from all the pumps.
Injection machine makers manage the excess oil in various ways to return it to the oil reservoir. By contrast, VSDs, which were introduced in Europe in the late 1990s, continuously regulate the speed of the electric motor so that the pumps supply the correct volume of oil when it's needed and slow down when less oil is needed. Obviously, this reduces energy usage. You may encounter three other names that also are used for a VSD: variable frequency drive, adjustable frequency drive and inverter — different names, same device.
Kent says even though one can buy a VSD with the intention of installing it on a hydraulic injection machine, that's not something he recommends. The interface between the VSD and a specific injection machine and its control system is critical and requires specific hardware and software. Kent has worked with a number of molders that have had success with the SyncroSpeed Energy Saving System developed and made by CCS Technology Ltd., Coventry, England, and distributed in the Americas by SyncroSpeed North America. He says the company is especially adept at connecting the machine and the VSD.
SyncroSpeed is a retrofit control system that is designed specifically to improve the energy efficiency of conventional hydraulic injection machines by regulating the speed of the pump motors. The company says it achieves savings of 25 to 45 percent, depending on the specific machine, part and material. In some cases, savings have exceeded 70 percent.
Robert Knaster is the CEO and president of PlasticMetal USA, Huntington Bay, N.Y., the distributor for SyncroSpeed in North America and elsewhere. He has documented the savings for many types of machines and companies.
"We analyze all the factors and make a proposal that includes a performance guarantee for a specific level of savings," he says. "In many cases, we exceed it." Recently, a three-motor SyncroSpeed system was retrofitted to a 1,100-ton HPM machine in Vermont. An independent control strategy was created for each motor and when the system was turned on it reduced the total energy draw by 48.8 kW, a 53 percent savings that beat the 35 percent performance guarantee. Those results were scrutinized by Efficiency Vermont, a program that facilitates energy efficiency across the state. Among the many examples shown on the company's website, payback time is generally less than 18 months.
Knaster says a SyncroSpeed system often is eligible for subsidies, rebates or credits from government agencies and utility companies looking to reduce energy consumption. The credits can cover a major portion of the investment. A Wisconsin custom molder recovered almost 40 percent of its project cost from state and utility programs. Knaster says Canada's energy-reduction grants can cover from 30 to 80 percent of the project cost, and SyncroSpeed bears the stamp of approval from the CSA Group, which verifies compliance with Canadian environmental standards. For companies looking to shrink their carbon footprints, Knaster offers the example of a molding company with six injection machines that reduced its carbon footprint by 4,740 tons over five years. That's in addition to annual saving of 2 million kWh worth around $1.2 million over five years.
Rob Neilley, senior correspondent
Contact:
Insul-Vest Inc.,800-447-0127, www.insul-vest.com
SyncroSpeed North America, 914-582-1848, www.syncrospeed.com
UniTherm International LLC, 972-436-1401, www.unitherm.com
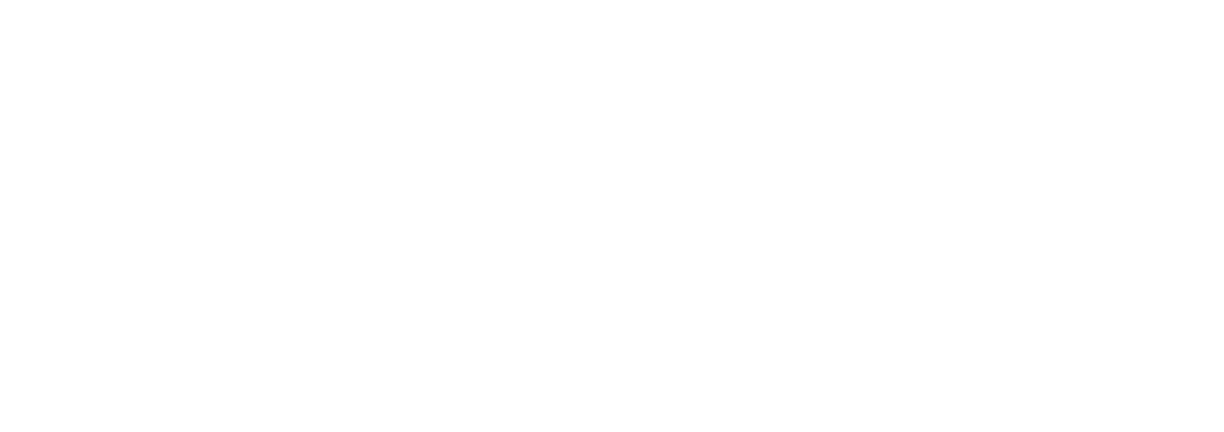