Mechanical and chemical purging formulations are more versatile and better remove a wider range of polymers that build up on primary machinery components.
Commercial purging compounds are formulated to clear contamination within injection molding, extrusion, blow molding and compounding equipment. The goal of purging is clean production components, allowing for perfect part production regardless of the polymer type or part dimensions. The compounds are tailored to remove material buildup on metal surfaces, reduce material and color changeover times and minimize scrap, carbon buildup and surface defects. They can be used in low- and high-cavitation tools.
Purging compounds are finding increased use as an alternative to purging with virgin resin or regrind, which do not have detergents or cleaning agents. Processors utilizing purging compounds report fewer process/production glitches and more uptime, with scrap rates reduced up to 50 percent and changeover times trimmed to minutes.
New purging grades have been developed to address an array of issues. Some have been made to clean areas with minute clearances such as hot-runner gates and extrusion dies, or to better purge engineering resins that are temperature- or sheer-sensitive. Some formulations have been designed to flow more easily within the carrier material, or to replace the role of glass fibers in the compound, enabling its use in a broader range of applications. Formulations have also been designed to minimize the generation of a haze or odors during purging or to maintain thermal stability at high processing temperatures. A continuing trend in purging compound development focuses on formulations that can be used in the machine as well as the tooling, and recipes that allow a processor to use the same compound in different plastics manufacturing processes.
ASACLEAN GAINS TWO PURGING GRADES
Sun Plastech Inc., Parsippany, N.J., recently developed two purging compounds for high-temperature engineering resins.
ASACLEAN PF is a non-glass-filled purging compound ideal for cleaning engineering resins such as polyphenylene sulfide (PPS) and polyetherimide (PEI) from thermoplastic injection molding machines and extruders. It is suited to purging hot runners at high temperatures, or for purging during color changes or material changes. It can also be used as a sealing material during machine shutdowns. The compound can be used at temperatures from 535 to 790 Fahrenheit. Sun Plastech says the compound has superior cleaning power compared to the Asaclean SX grade, which is designed to purge PPS, PEI, PEEK and liquid crystal polymer (LCP) from injection presses and extruders.
The Asaclean PF grade can clean hot-runner gates and extrusion dies but requires 0.02 inches of clearance in the tooling for successful purging. With injection molding, the company suggests the use of short, high-velocity shots to purge carbon or color deposits from nozzle hang-ups or for cleaning of the check-ring. In extrusion, the PF grade works best if the screen packs are removed. However, a maximum 100-mesh screen size can be used if screen pack removal is not possible.
Sun Plastech also rolled out Asaclean PX2, a glass-filled purging grade that cleanses PEEK, PPS, PEI, LCP and other engineering resins from primary processing machinery while generating low levels of haze and odor. Sun Plastech says the new grade is an improved version of the PX formulation, offering greater cleaning power and the possibility for processors to reduce the amount of purging compound required for a cleaning task. It is designed for color changes, material changes and the eradication of carbon or color contamination or the remnants of high-temperature resins. Asaclean PX2 has an operating temperature range from 535 Fahrenheit to 790 Fahrenheit. Sun Plastech says Asaclean does not work by chemical reaction, so no soak time is required for an effective purge.
Sun Plastech is a subsidiary of Asahi Kasei Chemical Corp., Tokyo. In June, it announced an acquisition of purging compound maker Novachem, Bridgeport, Conn. The acquisition further expands Sun Plastech's position as a provider of purging compounds in the plastics industry, and adds chemical purging compounds to the company's product line, according to the company. Novachem manufactures the SuperNova and Novapurge line of chemical purging compounds, as well as the InstaPurge line of mechanical purges.
ULTRA-X ENHANCES
ULTRA PURGE COMPOUNDS
Moulds Plus International USA, Santa Ana, Calif., this year launched Ultra-Purge 5150, an HDPE-based purging compound formulated as an evolution of the company's Ultra Purge 5050 grade, capable of dissolving colors and carbon deposits. It is suited for use in a wide range of primary plastics processing equipment, including injection molding, extrusion, blow molding, cast film and sheet extrusion.
Ultra Purge 5150 uses Ultra-X technology — a proprietary technology commercially introduced by the company with this new compound, that enhances the performance of the Ultra Purge active purging ingredients that are part of the formulation. Ultra-X contains mineral fillers and foaming agents and allows the Ultra Purge ingredients to reach an optimal level of expansion necessary for the purging compound to reach into hard-to-clean areas, says sales manager Andrew Reeder.
The incorporation of Ultra-X enhances the cleaning power of Ultra Purge 5150 up to 30 percent compared to the 5050 grade. Glass fibers are not incorporated into the formulation due to the presence of the Ultra-X, which helps the carrier material keep its hardness and consistency while allowing the carrier material to expand, says Reeder.
Ultra Purge is a hybrid compound with mechanical and chemical purging characteristics — it scrubs and works at a physical level like a mechanical purging agent, and also promotes a chemical reaction that breaks polymer bonds and increases the melt flow index of the residual resin, says Reeder.
The compound fluidizes residual polymer, allowing the purging material to flow through valve and thermal gates as small as 0.2mm. At the same time, the scrubbing power of the purging compound loosens contaminants without harming the screw, barrel or hot-runner components. The compound is certified for food contact.
Ultra Purge 5150 is available in a ready-to-use form that processors can use to mold parts or in a concentrated form. The material is designed for purging screws and dies that are used for compounding masterbatches, as well as screws, barrels and hot runners. The purging compound works in a temperature range from 374 to 662 Fahrenheit.
Parts made from Ultra Purge 5150 can be recycled, and in some cases reused to make parts, says Moulds Plus. Ultra Purge 5150 is suited for use during machine start-up/shutdowns, material changes, carbon removal and color change tasks, says Reeder.
Moulds Plus also incorporated the Ultra-X technology into Ultra Purge 5160, a new styrene-based compound designed to purge amorphous materials. It is also offered in ready-to-use and concentrated forms, and can be used with a wide range of materials, including ABS, acrylonitrile styrene acrylate, polyamide, general-purpose PS, HIPS, PC, styrene acrylonitrile, polybutylene terephthalate and PET. Ultra Purge 5160 operates in a temperature range from 374 to 608 Fahrenheit.
DYNA-PURGE OPERATES
IN TIGHT TOLERANCES
The Dyna-Purge division of Shuman Plastics Inc., Depew, N.Y., last year released Dyna-Purge D2, its newest mechanical purging formulation developed for color changes, resin changes, shutdowns and start-ups and preventive machine maintenance use. The material cleans and removes contaminants, impurities, colored resin and black specks from the screw and barrel as well as the tool and die, says VP Tim Cutler. It can purge injection molding cold runners or hot runners, compounding and blow molding machinery and extrusion systems designed for profile, sheet or cast-film processing. It is excellent for purging injection molding and extrusion system components that have a minimum clearance of 0.025 inches.
The purging compound is formulated from several materials, including a proprietary, highly shear-tolerant material that creates a more viscous flow to the boundary layers. A second proprietary material in the formulation acts as a pressurizing agent that allows the purge to reach stagnation points within the machine or tooling. A third material in the formulation targets carbonized and degraded material adhering to the surface.
The safe, non-hazardous ingredients in the purging compound are FDA-compliant. Only a small quantity of material needs to be used to be effective, and the material is easy to use, requiring no processing adjustments or mixing. The compound consists of nonmelting scrubbing granules.
Dyna-Purge D2 can process all types of resins and works in a wide temperature range, from 350 to 625 Fahrenheit, says Cutler. Odor creation is minimal, and the material is less sticky for easier cleanup after use.
The Dyna-Purge division also recently has launched Lava-Shield, a purge guard that captures molten plastic purges while protecting employees and equipment. In development for two years, Lava- Shield dissipates heat quickly, says Cutler.
The guard is designed to replace more common purge handling approaches, which include shooting onto cardboard or grabbing the purging by hand with a glove or rag. The guard has quick-release properties that keep purges clean. When the purge cools, the special nonstick surface releases the purge, free from contamination. The purge can be reused, says Dyna-Purge.
Lava-Shield is customizable and can be cut, folded and shaped to fit a specific purging need. It is made with up to 30 percent recycled content, and can be reused up to five times. The purge guard is recyclable and can be placed among plant and office waste paper for processing.
PURGEX'S PROGRESS
A new purging compound designed to work with all polyolefin applications has been added to the Purgex Plus line of purging compounds from Neutrex Inc., Houston. This compound also works specifically with thermoplastic olefins and thermoplastic elastomers. It will be officially released later this year.
The new Purgex 742 commercial purging compound is comprised of nontoxic, nonabrasive active ingredients with a PE carrier, says Ken Haag, operations/technical manager. The ready-to-use blend, in development for two years, removes contamination from the screw, barrel, check ring and hot-runner systems featuring thermal gates or valve gates that are 0.03 inches or larger. It can also be used with extrusion/compounding and sheet-extrusion applications, says Haag.
The material works at temperatures ranging from 375 to 475 Fahrenheit. With regular use, 742 forms a temporary barrier that protects the steel surfaces, extending the effectiveness of the cleaning process. One of the key benefits is that the purging compound is itself easily expunged from the system using the next production resin.
The dual cleaning action of the carrier and active ingredients is designed to reduce the standard amount of purging compound used, while reducing purging time. The company says customers making large automotive parts needed only three or fewer runs with the purging compound to change from dark to light colors.
All Purgex compounds come in pellet form, which allows processors to handle the material without special equipment, as could be required with liquid purges. Blends come pre-mixed and are ready for use right out of the box.
Mikell Knights, senior correspondent
Contact:
Dyna-Purge, division of Shuman Plastics Inc., 716-685-2121, www.dynapurge.com
Moulds Plus International USA, 714-708-2663, www.ultrapurge.com
Neutrex Inc., 800-803-6242, www.purgexonline.com
Sun Plastech Inc., 800-787-4348, www.asaclean.com
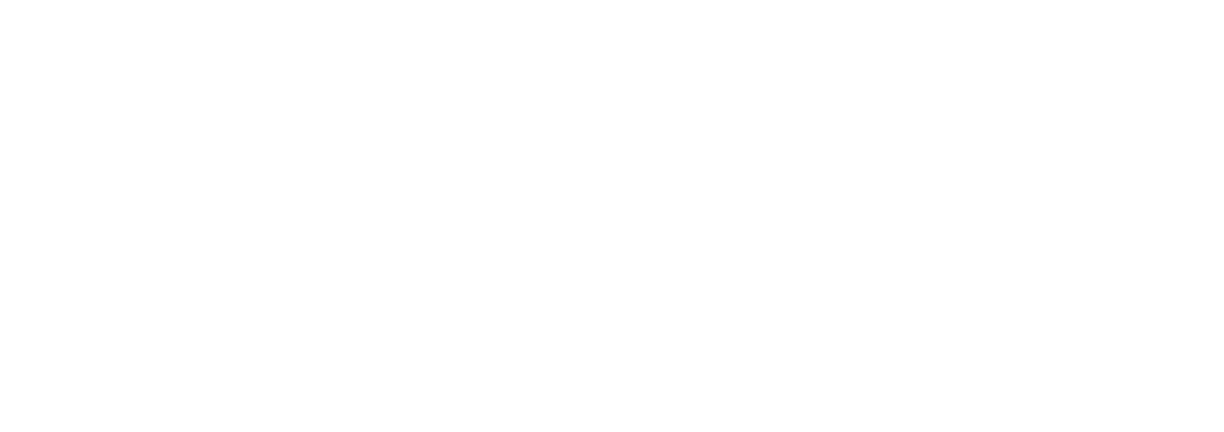