Seeing the incredible number of mold components offered at NPE, one might be reminded of Michelangelo. As impressive as the seemingly endless stream of innovative products flowing to mold makers from suppliers is, perhaps more impressive is that they are available with one click of a mouse. Compare that with how Michelangelo worked.
Because he was a perfectionist — like a mold maker — Michelangelo made the chisels he used to sculpt masterpieces such as his famous "David." For the same reason, he mixed the pigments that today illuminate the ceiling and altar wall of the Sistine Chapel. Just imagine how many more wonders he could have created if someone else supplied the tools of his trade. The booths of the mold component suppliers in Orlando, Fla., certainly help explain why mold makers enjoy a high level of productivity.
From a toolmaker's bench
to worldwide mold monitoring
Progressive Components International Corp., Wauconda, Ill., and its sister companies, AST Technology North America Inc., Roehr Tool Corp. and ToolingDocs LLC, rolled out a slew of new products aimed at making life better for makers of production tooling.
AST Technology, Wauconda, announced new enhancements to its CVe Monitor v2 and accompanying OnDemand software that make it easier to track a mold's performance and activity. Sujit Sheth, GM of AST's monitoring division, says that when the CVe was first introduced it let the user program initial preventive maintenance (PM) actions and a regular schedule.
"Now it's all customizable, whether incremental or absolute," he says. "Users can specify the timing and type of PM required." Each scheduled protocol has a custom checklist of procedures that can be checked off, signed and stored as a report.
Another new feature, CVe Live, enables real-time monitoring of mold activity on any press, in any plant around the world. Data from a small module at the press is collected by a gateway device that accesses the Internet and sends the data to a secure website. It offers secure access for molders and OEMs, a dashboard with information that can be drilled down for specifics on each tool, and a variety of charts and graphs for at-a-glance looks at mold efficiency, actual versus theoretical production, asset tracking for relocated molds and more.
Apart from its control and monitoring products, Progressive rolled out a number of new mold components. For example, the company introduced a lifetime guarantee for its patent-pending Z-Series alignment locks. An independent firm that tested various alignment locks found that Progressive's alignment locks showed no wear after more than 2 million cycles, while others often fail after 40,000 cycles.
Progressive also featured new wear plates. Ken Rumore, senior design engineer, says the company analyzed wear plate sizes and screw locations with input from many mold designers before using the particle rings and material treatments used in the Z-Series alignment locks.
"Many customers using our Z-Series alignment locks are experiencing incredible performance. Whether in an independent lab or in the field, we haven't been able to cause wear, whatsoever," he says.
The wear plates' thin, 0.25-inch profile leaves more room for waterlines and other mold features. Progressive says the wear plates are competitively priced and available in 10 sizes, starting at 0.5 inch by 0.5 inch. Multiple pads can be used for large areas and custom sizes are available. The company offers 2-D and 3-D CAD geometry on its website to make it easier to incorporate the new plates into the mold design.
Mold maintenance and training specialist ToolingDocs, Ashland, Ohio, added mold-maintenance benches used in its maintenance training center to its product line. Operations manager Steve Johnson says the company got many compliments on the benches and people asked how to buy them. The bench design is based on the company's employees' long toolroom experience. Johnson says that in ToolDocs' training, "We've preached the advantages of having a well-equipped work area and bench, not least of which is increased efficiency and cost savings."
Optimized for mold assembly and disassembly, the bench features a convenient working height, storage shelf, 3-foot-by-12 foot work area, 0.625-inch ground steel work surface for easy positioning of mold plates, knee-protecting corners and all-welded construction. Pre-drilled holes and repositionable pegs allow organized storage of tools. Options include water manifold and flow meter, air manifold and electrical outlets routed under the bench.
Roehr Tool Corp., Hudson, Mass., announced it has engineered more sizes of its sub-10mm Dove Tail (DT) Cores for molding such parts as very small threaded medical devices and electrical connectors. GM David Helenius says Roehr now stocks blanks for DT cores between 7mm and 10mm, adding, "This speeds delivery times by three to four weeks."
Roehr also offers pre-engineered DT cores in 0.5-inch to 3-inch National Pipe Thread Taper (NPT) standard and British Standard Pipe Taper (BSPT) thread sizes for molding threaded parts for plumbing, irrigation and water or other fluid transport products. Roehr is expanding the overall number of standard sizes of its pre-engineered DT cores from four to 23. By doing that, Helenius says, "We're able to take two weeks off the build cycle."
DME mold bases go larger
with quality, fast delivery
It's not news that the product line of DME Co., Madison Heights, Mich., the Milacron LLC unit supplying mold components and other mold-related technologies, is vast. Displaying all of it could have filled a lot more of Milacron's 25,000-square-foot NPE display than it did, but Milacron's injection, extrusion and auxiliary machinery needed space, too.
DME featured a new product that also is impressively large. DME mold bases now are available in sizes notably bigger than the company's previous offerings. Mold base plate lengths now can be as great as 90 inches, a big jump from the previous 66-inch limit. Maximum plate widths now are 60 inches, up from the previous 54 inches, and maximum plate thickness has increased markedly from 13 inches to 39 inches. The company underlined that the new larger mold bases are very high-quality and explained why.
DME has been expanding its machining capabilities significantly, making a multi-million‑dollar investment in high-performance machining centers in its North American manufacturing plants: Windsor, Ontario; Youngwood, Pa.; and Greenville, Mich. The result, says DME, is that customers gain a competitive advantage from high quality, tighter tolerances and quicker delivery of the mold bases, including the new larger ones.
To make this possible, DME concentrated its technology investments on leading-edge machining equipment, bringing in the fastest and most powerful machines in their classes to provide a combination of top quality, closer tolerances and faster delivery. Larger work zones on the new machining equipment accommodate tapping, chamfering, spot facing, counter boring, slot-cutting, face milling, compound thread milling and other processes on the larger mold bases. Just as beneficial, the consistently high-quality finishes provided by the new high-end machining equipment significantly reduce the need for manual polishing and rework.
A major part of DME's identity rests on its innovation of the standard mold base more than 70 years ago. The current expansion of mold base sizes continues that innovation, says a company spokesman, adding that this means mold makers that have been creating large mold bases in-house now can receive high-quality bases with rapid delivery as a standard order from DME. That will save the mold maker time, and just as important, enable the mold maker to manage and use its in-house machining capability more efficiently.
The DME quality management system is based on having the entire business operating on the stringent ISO9001:2008 standard. It requires the company to review, improve and document each of its processes on an ongoing basis, thereby ensuring that customers consistently receive only high-quality products. Quality Magazine has recognized DME in its Quality Leadership 100 list, with the company taking the No. 2 spot in 2013.
Three tools for implementing SMED
in injection molding
Burger & Brown Engineering Inc., Grandview, Mo., knows how serious injection molders are about shortening mold setup and changeover time. Its strategy is twofold: Convert internal operations, those that must be done when the press is idle, into external operations that can be done while the machine is running; and use proper tools to reduce time needed by internal operations.
At NPE, Burger & Brown marketed three products in its Smartflow line as one solution that will help make possible the single minute exchange of die (SMED) in a molding operation. The Duoflow manifold, Smartflow swap valve and FasTie quick ejector tie-in let molders take a very big chunk out of their setup or changeover time on an injection press.
Mounting a Duoflow manifold to a mold connects all cooling-water circuits to the externally mounted manifold. Water hookup is then reduced to seconds by using one connection for supply water and one connection for return water with quick-disconnect fittings on the ends. The robust, extruded aluminum Duoflow is anodized red and blue to protect against corrosion and to identify the return and supply functions. The Duoflow's shorter length allows easy mounting on injection molds, even where space is limited. Inlet sizes are 0.75-, 1- or 1.5-inch National Pipe Thread Taper Fuel (NPTF) standard, and port sizes are 0.25-, 0.375- or 0.5-inch NPTF standard.
A Smartflow swap valve reduces the time needed to evacuate the cooling line during mold changes to seconds and, as a bonus, helps keep the shop floor clean. In operation, 5 to 20 minutes of downtime becomes productive time and the valve helps protect tools from corrosion by evacuating water from a tool before it goes into storage. The valve handle has three positions: water, purge and vent. A check valve that is provided should be installed in the return line downstream from the return manifold to prevent backflow. Its full-port design permits maximum flow of cooling water at minimum pressure drop. Typically, it's mounted on the press frame or safety doorframe, but also can be on a platen, mold or manifold stand. The swap valve shuts off water conveniently near the machine control.
By tying the mold ejector plate to the press ejection system, the FasTie quick ejector tie-in dramatically reduces mold change time, with the biggest savings being in presses where space is limited and the ejector system is difficult to tie in using solid knockout bars. The FasTie coupler can be permanently mounted to the press ejector plate. During mold installation, the quick-connect locking mechanism in the coupler snaps onto the mold-mounted stud. To release the ejectors, shop air is applied to the coupler, which opens to release the stud, disconnecting the press and tooling ejector plates. The coupler remains in the open position, ready for the new mold. FasTie couplers are available in three sizes: 1 inch, 1.375 inches and 2 inches.
We all know about scientific molding, but do you know scientific cooling? Aware that cooling takes 70 to 80 percent of injection molding cycle time, Burger & Brown decided to provide practical help. Its two-day scientific cooling courses cover energy principles of specific polymers; how heat transfer and energy flow affect part quality and cycle time; coolant delivery and distribution principles; water chemistry's influence on cooling; and much more. Hands-on exercises reinforce the learning.
HOt-runner system
offers easy maintenance
PCS Co., Fraser, Mich., introduced its Emerald thermal gate hot-runner systems. Available with eight or fewer drops, the systems are designed, built and heat-tested to ensure performance. All Emerald systems are fully balanced with nozzle heaters and thermocouples designed for easy maintenance. PCS provides technical service and application engineering from project launch through startup, as well as ongoing tech support and parts inventory. Thermal gate systems are available as a complete hot half, pre-wired or as manifold and components.
Rob Neilley, senior correspondent
Contact:
AST Technology North America Inc., 847-487-1000, www.asttech.com
Burger & Brown Engineering Inc., 816-878-6675 www.burgereng.com
DME Co., 248-398-6000, www.dme.net
PCS Co., 586-294-7780, www.pcs-company.com
Progressive Components International Corp., 847-487-1000, www.procomps.com
Roehr Tool Corp., 978-562-4488, www.roehrtool.com
ToolingDocs LLC, 419-281-0790, www.toolingdocs.com
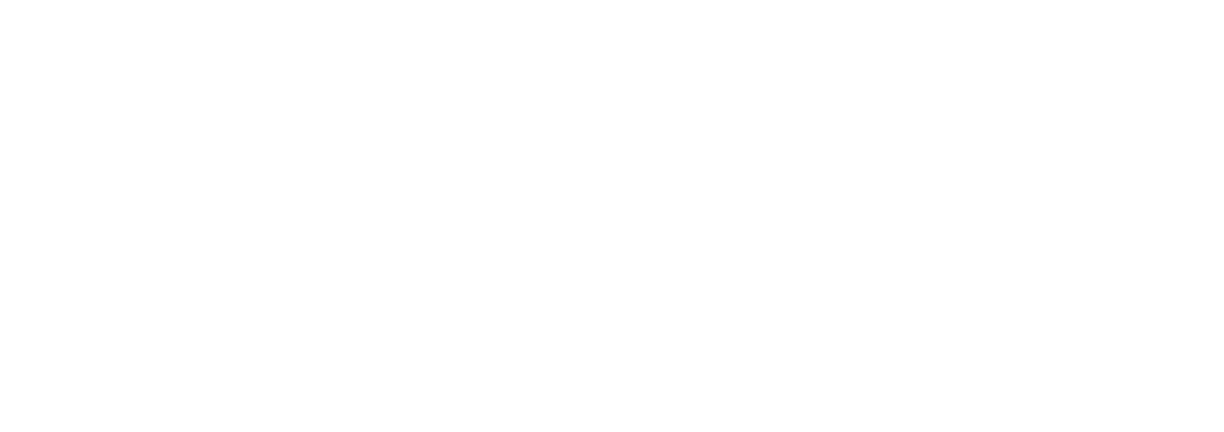