Extrusion die technology at NPE was as varied as extrusion itself, and there were many examples of innovation ranging from simple features to complete new tooling technologies.
Dies for medical
and other tubing
Guill Tool & Engineering Co. Inc., West Warwick, R.I., has developed lines of extrusion tooling for a broad range of applications, from automotive hoses to wire and cable to multiple strand dies for pelletizing, but at NPE the company was featuring its line of crosshead and inline tubing dies for single or co-extrusion applications.
The dies are designed to process all compounds and include features such as Guill's spiral flow distribution system and its patented precision FeatherTouch concentricity adjustment, which, when combined with its SealRight system, eliminates polymer leaking, according to the company. All the company's tooling is produced using rigorous computer simulation that includes computational fluid dynamics programs to achieve optimal flow uniformity with no weld lines.
The highlight of Guill's booth was the introduction of the next generation of the Guill Series 800 two- to six-layer extrusion tooling. The dies are designed to produce top-quality tubing with 0.125- to 6-inch outer diameters with the highest material efficiency for automotive, medical and industrial applications. Their low volume minimizes residence time to maintain quality.
William Conley, sales manager of Guill's extrusion division, says the redesigned Series 800 dies yield flawless multilayer tubing with excellent layer definition in fluoropolymers and other materials for any fuel-line structure, as well as for cross-linked PE pipe and drip irrigation products. The Series 800 die can hold layer thicknesses as thin as 0.02mm, and Guill's split-feed, balanced flow enables the extruder to run a fixed center with concentric walls at all speeds.
The compact Series 800 design features replaceable spiral flow inserts, internal heaters for an even temperature profile and a rotary design that optimizes polymer integrity for thin-wall, high-strength tubing. It works equally well in corrugating applications. The quick-change features reduce downtime and a dual-head configuration can double production. Eight sizes are available. Dies for conventional plastics are made of tool steel or stainless steel, while dies for fluoropolymers are made using alloys such as Monel, Inconel or Hastelloy.
Reducing changeover time
from hours to minutes
NPE marked the first time the four polymer processing brands of Nordson Corp. — Nordson Extrusion Dies Industries LLC, Nordson BKG, Nordson Xaloy and Nordson Kreyenborg — exhibited together. Nordson, Westlake, Ohio, which began acquiring those veteran brands following NPE2012, noted that its display combined more than 200 years of polymer processing technology.
Each of the four brands was showing cool new technology, and that most definitely included flat-die specialist Nordson EDI, which introduced its SmartGap system for sheet dies. As Sam Iuliano, the brand's chief technologist, says, "We believe SmartGap to be the first real breakthrough in sheet die technology since the start of this century."
The SmartGap system's big benefit is that it drastically reduces the shutdown times, generally two hours or more, needed to change over to a new job. With SmartGap, says Iuliano, changeovers are reduced to a few minutes. SmartGap provides a single-point adjustment that changes the lip gap and simultaneously modifies the length of the lip land, which is the final gap in the dies that forms the lip exit, to provide the best conditions for the adjusted thickness of the sheet exiting the die.
Iuliano said SmartGap will particularly benefit custom sheet houses that supply multiple customers with multiple products, which can result in several changeovers a day. The system also overcomes previous limitations on the range of sheet thickness caused by the complexity of die modification. SmartGap handles die gap adjustments across a range of 0.4 inches.
To use SmartGap, an operator initiates a thickness change by using an adjustment mechanism at the end of the die to set the new lip gap. Simultaneously, the length of the lip land automatically changes as needed. For thin sheets, the lip land is short to help control backpressure, reduce deflection and lessen the need for drawdown. For midrange sheets, the lip land changes to medium length, providing enough pressure for effective adjustment of the flexible die lip and helping to reduce swelling of the extrudate. For thick sheets, the lip land extends to full length, increasing backpressure at large lip gaps and helping to reduce extrudate swell.
SmartGap, which is available only on new dies, brings benefits beyond avoiding extended shutdowns. Since setting smaller lip gaps is easier, the processor does not need to draw down as much to achieve target gauge, which means less orientation of the sheet and fewer shrinkage problems. With appropriate lip land lengths for small and large lip gaps, using the flexible lip to fine-tune gauge profile is more effective. The proper lip-land-to-lip-gap ratio prevents extrudate swelling that can cause visible corrugation defects and streaks.
Iuliano noted that the competitiveness of today's market means quality standards that governed the sheet industry as recently as a decade ago are no longer acceptable. This is why, he says, "Nordson EDI has developed the SmartGap system as a means of eliminating the uncertainties and compromises that have often accompanied significant changes in thickness."
Surpassing strength expectations
by interweaving layers
Approaching the NPE display of Alpha Marathon Film Extrusion Technologies Inc., Woodbridge, Ontario, it was hard not to be attracted by the company's 2X Nano-Layer Die. Not only does it stand 6 feet tall, the machine has an annular ring structure unlike any traditional blown film die. But the company's real news was its newly patented Alpha Layer Sequence Repeater (LSR) die technology, which constituted the structure of the production die on display.
When equipped with three LSR 50-layer modules, a die can produce film structures with between 25 and 200 discrete layers. When a die produces a typical 30-micron film with 150 layers, each layer is only 200 nanometers thick. And that's just the tip of the iceberg of benefits and advantages the LSR-made film brings to film processors and converters, and, ultimately, to packaging suppliers and film-consuming OEMs and brand owners.
The magic is the LSR technology's ability to create and interweave layers less than a micron thick that acquire exceptional physical and mechanical properties, even when using lower-cost commodity resins and/or reprocessed or recycled materials. Michael Taylor, Alpha Marathon's director of sales and technical support, says the melt rheology tolerance is so broad that films can be made from virtually any resin or resin combination.
Taking advantage of the strength and toughness of film made using LSR technology, overall film gauge can be reduced by 20 to 30 percent with no loss of mechanical properties, and throughput can be increased by 15 to 25 percent, according to the company. The interweaving layers create an I-beam structure that considerably strengthens the film, which also exhibits increased puncture and tear resistance and better dart drop values. The high melt strength of the material allows both higher output and thinner films. Film as thin as 2.5 microns has been made.
Many processing advantages of the LSR technology result from its parallel melt flow, including low pressure, low temperature, low shear and a broad acceptance of varying melt flow indexes (MFIs) both in the base resins and in the MFIs of adjacent materials. A short flow path means low residence time and reduced melt degradation, leading to increased shelf life for the finished product. There is a tolerance for unmelted pellets that favors use of reprocessed materials and reduces the chance of bubble failure. Low pressure means the base gauge variation of material exiting the die is as good or better than with high-quality spiral dies. Polymer layers leaving the die have maximum alignment for extensibility.
The Alpha 2X Nano-Layer Die is available in annulus diameters up to 20 inches, and with blow-up ratios possible up to 5.0, it can deliver films with lay-flats up to 12 feet wide. The 2X die is rated for up to 1,500 pounds per hour of output.
The logical target market for this technology is packaging, and Taylor confirms that is the biggest segment. Another segment with high interest in this technology is battery manufacturers. If produced with Alpha's LSR technology, the film that divides battery components could be much thinner than what is currently used and still provide excellent performance. There are also opportunities in barrier films, as well as from processors who could use LSR technology for their non-barrier products and enter the barrier business doing nothing more than changing the materials in their extruders.
Taylor says Alpha, like other extrusion system suppliers, traditionally has done business mostly with processors. However, at the last two NPE shows, visitors to the booth increasingly included people from OEM and brand owner companies. It should be noted that NPE show management has been supporting OEMs and brand owners, providing facilities for companies that send groups as large as 30 or 40 people. Taylor says those companies generally have internal R&D operations and it's those people who are coming to shows looking for technology — tech scouting. Alpha Marathon has begun joint R&D projects with some of them and more may be coming as a result of contacts at NPE.
Rob Neilley, senior correspondent
Contact:
Alpha Marathon Film Extrusion Technologies Inc., 905-265-2055, www.alphamarathon.com
Guill Tool & Engineering Co., 401-828-7600, www.guill.com
Nordson Extrusion Dies Industries LLC, 715-726-1201, www.extrusiondies.com
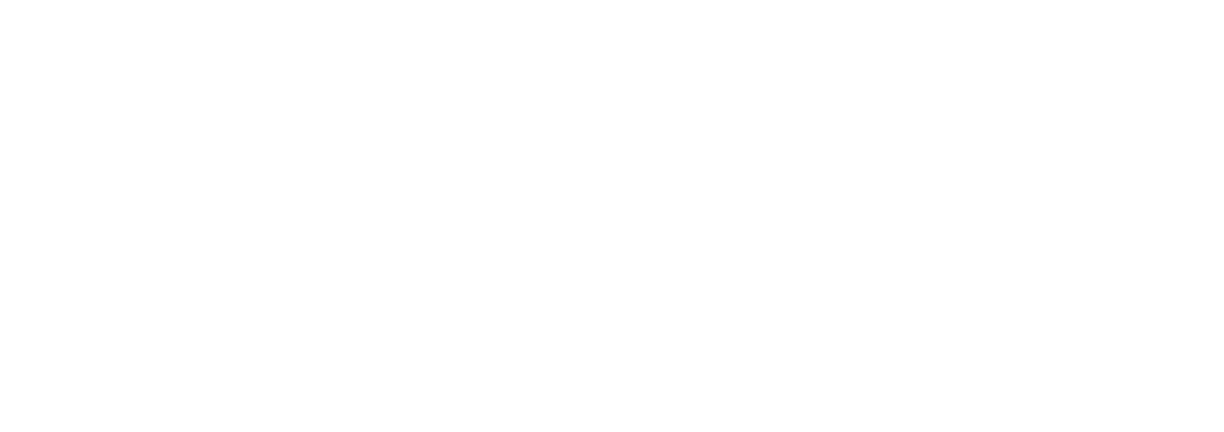