At NPE, several companies announced enhancements to existing equipment for the blow molding process. This includes a foam extrusion head for three-layer production; leak testing; automated takeout systems for shuttle blow molding; and an automated blow molding management system.
Foamed middle layer
with no chemicals
The latest enhancement for blow molding from W. Müller USA Inc., Agawam, Mass., is a foam extrusion head for three-layer production, with die diameters of 35mm and greater. Pictured at the left, this head is available in single- or multi-cavity versions, including a control unit. It can be integrated as a retrofit to many existing blow molding machines, says President Wolfgang Meyer. Nitrogen gas is injected in the dynamic mixer and the mixer is adjustable, independently of screw speed. The cellular structure is affected by the dynamic mixer speed.
Multi-layer blow molding with a foamed middle layer uses no chemical additives and has advantages over chemical foaming. Talc is used as the only foaming agent, so food packaging is possible, as the contents are not susceptible to influence by chemicals.
Lowered processing temperatures can reduce cycle times. Foam quality can be influenced independently from the screw speed of the extruder. In addition, product weight reduction yields a savings in raw material costs.
Retrofitting is an option for manufacturers. As blow molded containers for food, beverages and fuel continue to be converted from mono-layer to multi-layer structures with barrier layers, the demand for multi-layer blowing equipment keeps growing. New equipment requires substantial investment and demands long lead times that can stand in the way of rapid market introduction. In many cases, existing machines can be retrofitted with complete multi-layer extrusion systems economically within a few months.
At first glance, the time required to design and install a retrofit, and integrate controls of a new co-extrusion system into an existing machine could appear prohibitive. W. Müller makes the case, however, that retrofitting multi-layer co-extrusion systems is an efficient strategy because retrofits consist of the same building blocks in every project: extrusion heads, extruders and controls.
Fitting all components into the available space is typically the biggest challenge. Unless drawings with accurate dimensions are available, W. Müller dispatches an engineering team to the buyer's site to discuss specific requirements and take inventory of the existing equipment.
With data in hand, the design process can start. Satellite extruders for the barrier and adhesive layers are positioned vertically on top of the co-extrusion manifold. The larger extruders for the outer, regrind and inner layers require additional space. In most cases, this means an expansion of the existing extruder platform. In addition to providing more space, the platform must be capable of supporting the weight of the added equipment. The design also makes allowances for easy height adjustments. Platforms are designed with access stairs and safety railings. Secondary platforms are provided for safe access to the vertical extruder hoppers.
An independent control system specially designed for retrofits includes operation of all added extruders as well as temperature control for the extruders and the extrusion head. The retrofit system works alongside the existing machine controls via an interface, so it does not interfere with how operators have been accustomed to using the controls.
"Because the HMI (human machine interface) is individually configured for each retrofit, operation is made easy and convenient," says COO Christian Müller. "To support installed systems, we offer remote troubleshooting and the installation of upgrades via modem and Internet."
Multi-layer co-extrusion systems are completely assembled prior to shipment from W. Müller. This allows installation and startup of most retrofits within a week, reducing potential downtime.
Leak testing
and product handling
Proco Machinery Inc., Mississauga, Ontario, a specialist in industrial automation equipment, has made modifications and enhancements to two systems specific to blow molding, the Ultratest leak tester and the Robopik line of automatic takeout systems.
The Ultratest leak-testing system, first introduced in 2006, has been completely revamped and redesigned. ULT4 is the new design. It includes all-new high-speed controls, including a more robust pressure transducer that provides a higher pressurization tolerance. It also features an upgraded HMI along with operator-accessible controls and display screens, which results in a more user-friendly interface. The system can handle cycles up to 120 containers per minute with one test head and up to 300 containers per minute with multiple heads, says Proco sales manager Siva Krish. Various configurations allow the multi-head system to be integrated into challenging manufacturing situations such as wheel machines and dairy lines.
The ULT4 model can be supplied with up to six heads for higher throughput. The control panel is mounted under the conveyor, providing more room for expandability as more test heads are added.
Setup is straightforward. Once the test-head height is adjusted and the photo eyes set, the system calibrates itself as the first few containers pass by. Ultratest calibrates the full cycle. It then simulates a leak, calibrating the leak portion of the test cycle, and narrows the test window to the most sensitive range possible. A manual sensitivity adjustment is also provided for special situations that require technician input. The system also periodically self-tests the calibration and alerts quality control personnel if a deviation is detected. The control console is fixed at eye level regardless of conveyor height.
The Robopik EX2 line of automatic takeout systems for shuttle blow molding machines takes the container and transfers it directly to the deflasher where the tail and top flash are removed. After deflashing, a specially designed articulated vacuum conveyor extends into the deflasher and retracts with the container in an upright orientation. The integrated system uses only one tooling set, unlike the previous system, which used two sets. It also facilitates easy changeovers.
The EX2 is not limited by shape or size. It can handle bottle-type containers with any number of mold cavities. Container heights can range from 3 to 15 inches. The control system uses a color touch screen and can store job recipes for recall. An optional scrap conveyor collects both tail flash and neck flash. Conveyor height is 34 inches, for ease of integration with other equipment.
Pilot Profiler
gets new capabilities
Agr International Inc., Butler, Pa., added new capabilities to its Pilot Profiler with Process Pilot automated blow molding management system, which interfaces with the blow molding machine to provide precise material-thickness distribution management and defect detection for PET bottles while offering hands-off blow molding machine control.
The Process Pilot system helps bottle producers reduce bottle weight, while still distributing material appropriately. The Process Pilot system makes it possible to produce high-quality bottles consistently on a 24/7 basis regardless of operator skills, ambient condition changes or preform variations.
The demand for ever-lighter bottles can cause challenges regarding the shelf life of their contents. In particular, the loss of carbon dioxide and water is a concern. The Pilot Profiler can now predict shelf life at the point of production by incorporating a version of the M-RULE container performance model from Container Science Inc., Atlanta. The model is a Web-based tool that predicts the performance of plastic packaging under a broad range of environmental conditions. This provides plant managers with continuous information about the predicted shelf life, as well as the capability to proactively manage critical bottle parameters.
Wall-thickness data captured by the system is automatically entered into the M-RULE model. From this data, shelf-life performance is continuously calculated and presented for individual bottles or user-defined subgroups. Material distribution is maintained at a specified thickness to within approximately 0.01mm. This is accomplished by continuously monitoring every bottle for material distribution, analyzing minute changes and adjusting the blow molding machine controls to maintain pre-defined distribution levels. Unlike an operator, the Process Pilot can adjust one or all of the blow molding controls simultaneously to achieve the best possible material distribution.
The Process Pilot also can accommodate variations in preform preparation and storage conditions. Compensation can be made for temperature, moisture content and minor intrinsic viscosity changes of the preform to maintain a consistent process, within the smallest process window. This prevents the process from drifting out of control before the operator's next quality sample.
Agr also announced it is in the process of commercializing technology for managing PET bottle crystallinity and will market it under the name CrystalView. It will be incorporated into Agr's Process Pilot system. The new technology will allow production of PET bottles with consistent crystalline structure while maintaining desired thickness distribution, which can improve the bottles' resistance to stress cracking.
Merle R. Snyder, senior correspondent
Contact:
Agr International Inc., 724-482-2163, www.agrintl.comProco Machinery Inc., 905-602-6066, www.procomachinery.comW. Müller USA Inc., 413-787-0664, www.mullerheads.com
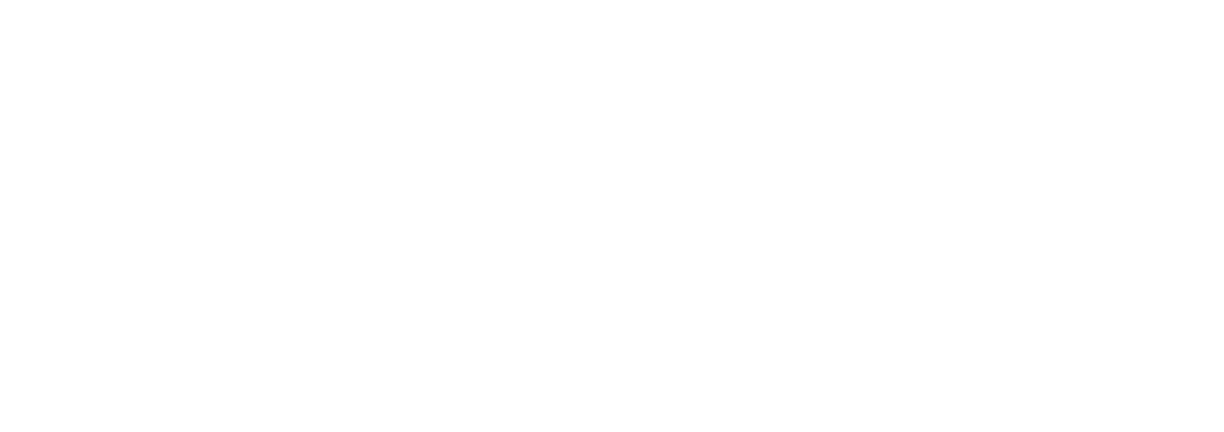