Injection molding machinery supplier Arburg GmbH, Lossburg, Germany, marked its 25-year presence in the U.S. last month with the inauguration of a new building in Rocky Hill, Conn., that will serve as its U.S. headquarters.
Arburg moved operations from a building it has leased in Newington, Conn., since 1990, to Rocky Hill, roughly 4 miles southeast of Newington. Significant improvement in the U.S. and global business climate are behind the construction of the more advanced, 27,000-square-foot facility, Arburg officials say.
"North America is Arburg's largest foreign market, in which we have installed more than 12,000 machines," says Michael Hehl, managing partner and spokesman for Arburg's management team. In addition to the Arburg Inc. subsidiary, founded in the U.S. in 1990, the company also has Arburg Technology Centers in Irvine, Calif., and in Elgin, Ill.
The centerpiece of the new facility is the showroom, which can accommodate seven Allrounder injection molding machines for testing or training purposes. Ample space in the showroom and warehouse also allows for the setup and dismantling of complete turnkey systems, which Arburg says are experiencing increasing demand in the U.S.
For the open house, Arburg configured a lab that is home to its Freeformer additive manufacturing unit. The unit, which made its U.S. debut at NPE, now is commercially available. In addition to administrative offices and meeting rooms on the second floor of the two-story glass and steel building, the site also has a 38-ton gantry crane, a spare parts store and a warehouse area that allows for machinery customization.
To mark the anniversary, the company announced a special 25 percent discount on the purchase of its Allrounder Golden Edition line of general-purpose injection molding machines. The Golden Edition series is offered in five models (270 C to 570 C) with clamping forces of 44 to 220 tons. The discount is available through the end of 2015. This model, introduced in 2006, is Arburg's most popular injection molding unit in terms of U.S. sales.
More than 200 customers and guests, as well as a delegation from the parent company and members of the plastics industry, attended the ceremony. Bill Carteaux, CEO and president of the Society of the Plastics Industry (SPI) gave the keynote address detailing the contributions made by SPI and the plastics processing industry to the U.S. economy. Other Arburg officials spoke about the advantages of various injection and clamp drive technologies, processing technology approaches to lightweighting parts, and the technology and benefits of the Freeformer.
Arburg operated five demonstration molding cells during the two-day event. An Allrounder 570 S produced a suction cup made from a two-component self-adhesive silicone overmolded with polybutylene terephthalate; an Allrounder 520 A molded medical pipettes with a 64-cavity tool; an Allrounder 630 H demonstrated in-mold labeling with an integrated robot for fast part handling; and an Allrounder 820 S produced a lightweight automotive brake pedal in a long-glass-fiber direct molding process. An Allrounder 370 E manufactured and assembled a toy car and incorporated Arburg's Industry 4.0 telecommunications technology to retrieve and impart data regarding part production; personal data, like a name, could be printed on a single part during production, while production data could be accessed from a QR Code printed on the part. In addition, Freeformer units in the lab produced a bellows and a can opener.
Mikell Knights, senior correspondent
Contact:
Arburg Inc.,
860-667-6500, www.arburg.com
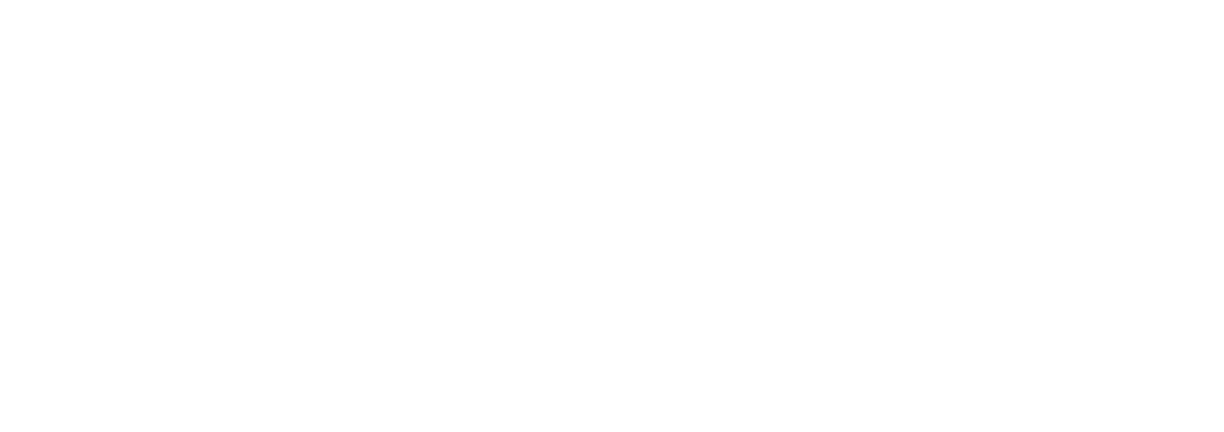