As much as any machinery category at NPE, materials handling in general and drying technology in particular demonstrated an increase in technical sophistication, but not just to add bells and whistles. Every new dryer PMM saw, as well as improvements and upgrades to established lines, featured a list of customer benefits for each bit of new technology.
All about plastics,
emphasis on efficiency
ACS Group, Schaumburg, Ill., returned to NPE with new branding, including for its material handling products, all reflecting a renewed focus on plastics. Paul Grekowicz, the group's VP of marketing and product development, said it simply: "We are all about plastics." He said the company began a study about a year ago aimed at saving space and streamlining its internal working processes. As the resulting efficient, lean approach has proven to be successful at ACS, the company is extending it to customers, positioning products and services to effectively solve customer problems.
The AEC brand of the ACS Group showed a great example of increased efficiency with its MDB Series of desiccant dryers. Besides a choice of four models with material processing rates ranging from 50 to 450 pounds per hour, the dryers offer energy efficiency, easy service access, casters for easy portability and simplified expansion of as many as three drying hoppers. A dryer can be a stand-alone unit or part of a cart system and used with or without conveying options to serve multiple processing machines. The DryPro control has a 5.7-inch color touch screen with pull-down menus and pre-loadable drying parameters to simplify operation and avoid errors.
Parabolic regeneration chamber
empowers new dryers
At the heart of the new E-Plus dryers introduced at NPE by Dri-Air Industries Inc., East Windsor, Conn., is a parabolic regeneration chamber. At the show, Dri-Air President Charles Sears said the unique design sends air uniformly through the tower for maximum moisture pickup, and that, combined with a single-blower design, can save up to 50 percent on energy costs. Other upsides include ultra-low dew points and faster drying.
The dryer is fully enclosed and includes greater hopper insulation for further energy efficiency, even when handling challenging, hard-to-dry plastic materials. The design enhances the temperature profile inside the hopper and simplifies dryer cleaning in clean-room environments. It permits the three models of the E-Plus dryers (25-, 50-, and 100-pound-per-hour drying capacities) to be relatively compact. Sears describes it as "close coupled" with hose runs that are short. It's only about 6 inches from heater to hopper.
The E-Plus dryer comes with Dri-Air's proprietary new E-Plus dryer control, which features a large, bright display visible from 20 feet away or more. Service screens show internal temperatures and other parameters that help reduce maintenance times. Graphic screens show the location of a failed component as well as part numbers for reordering. Dri-Air's Dri-Link app allows dryer control and monitoring from a smartphone, tablet or other portable device, and drying data can be transferred to central monitoring and control systems. The optional hopper management system uses laser technology to constantly measure material levels and display them on the main control screen, which then can provide adjustable fill control and a low-material alarm.
Load cells in dryer increase
processor control options
Maguire Products Inc., Aston, Pa., demonstrated how the load cells it recently added to its patented VBD vacuum resin dryers give processors new ways to control and document their material use. The cells, which are in the vacuum chamber and the retention hopper of the VBD, enable continuous control of the resin level in those vessels.
Operating on a loss-in-weight basis, the load cells provide real-time data on material throughput, unaffected by variations in bulk density. According to Mike Gera, senior dryer product manager at Maguire, the cells achieve accuracy of plus or minus 0.5 percent. Gera credited the load cells with enabling the microprocessor in the controller to monitor, display and log throughput in real time, updating the rate once per minute.
Gera says the load cells also enable energy efficiency. Given the improved control, the throughput rate can be set to precisely match the process rate, saving energy and avoiding excess dried material at the end of a run. He notes that although the VBD dryer provides continuous flow for molding or extrusion processes, the load cells also let it run batches.
High-volume drying system
comes to America
Materials handling systems supplier Moretto SpA, Massanzago, Italy, had an eye-catching display of its high-end Eureka materials conditioning system in its booth at NPE, and also held a press conference to describe its already-begun program for increasing its penetration of the North American market. An American subsidiary, Moretto US, opened in October in Columbus, Ohio.
Paolo Gasparotto, Moretto's business development manager for North America, said the American market is the biggest for a high-capacity system like Eureka, and his company has been developing an American presence for about three years. In March 2015, there were 58 Eureka systems installed worldwide and 26 more on order. In the American market, there were only four Eureka systems. Moretto is determined to grow that number, aiming primarily at medical, textile and PET processors.
What makes the Eureka system high-end? Moretto says Eureka is the only drying system that can process 22,000 to 26,500 pounds per hour of material for compounding, extrusion and PET processing, and according to system users, consume up to 56 percent less energy than traditional drying systems to do it. A Eureka system has three elements: the Flowmatik airflow management and distribution system, the OTX hopper/dryer, and the X Max dryer.
The X Max at Eureka's core includes a multi-bed, single molecular sieve desiccant system providing constant dew point from minus 85 degrees Fahrenheit to minus 121 degrees Fahrenheit. Twice the size of conventional beds, it needs no cooling water or compressed air for the changeover valve. There is complete energy recovery, with heat being recovered from cooling the bed during molecular sieve regeneration. Two to 10 X Max dryers can be combined, with airflow of up to about 706,000 cubic feet per hour with 10 units.
The Flomatik airflow control can stop one or more dryers if full capacity isn't needed and distribute the load across the others, and it can share air with as many as 32 OTX hopper-dryers. The OTX is available in 28 sizes and features internal geometry that ensures even flow of material and air for maximum drying efficiency. It is 40 percent faster and consumes less energy than traditional hoppers.
Una-Dyn's line offers
dryers for low throughput
Universal Dynamics, Woodbridge, Va., showcased several technologies, including its new all-electric Vantage series line of dryers. The key advances and innovations in this line include the Vantage rotary air distribution valve for positively ported and proofed air control. That means no seals or gaskets, which results in flat-lined process temperature and dew point performance. No compressed air is required. Officials touted the high performance and simple user interaction, which make the line a solution for low throughput. It features the Focus touch screen control, which is Una-Dyn's family of touch screen controllers for its entire drying line. Data is displayed on an HMI main screen with setup, data logging and deep diagnostics on demand.
Officials have focused on the energy savings of the PCT³ product, calling it one of the most energy-efficient dryers available on the market. PCT³ generates a dew point down to minus 100 degrees Fahrenheit. It has minimal moving parts, self-adjusting drying and steady set point temperature throughout the drying cycle. The standard throughput range for the PCT series dryers is 300 to 3,000 pounds per hour with temperature range from 120 to 375 degrees Fahrenheit.
More automation,
less operator intervention
Wittmann Battenfeld Inc., Torrington, Conn., promised to demonstrate its full lineup of materials handling and auxiliary equipment at NPE, and indeed it seemed that all of the company's many lines of auxiliary products were present. However, you easily could have missed one in a very busy booth that exhibited a number of the company's injection molding machines and even a team of robots demonstrating their qualifications for work as a race car team's pit crew.
Michael Stark, the company's divisional manager for material handling and auxiliaries, said that automation at Wittmann is not just about the company's robotics products. It applies to auxiliaries as well in the sense of automating functions and reducing the need for operator intervention. For example, Wittmann's FC plus module introduced an option for the company's Drymax battery dryers that extends the functionality of these frequency-controlled dryers.
An FC dryer can automatically adjust the dry air volume to the throughput requirements of each drying battery without any need for the operator's intervention. Stark said that if there is any reasonable way that Wittmann can automate a function, it will. The FC plus module also enables more efficient configuration and operation of drying systems. It can automatically shut off dryers with low demand and put them in standby mode to save energy. It can automatically register an increase in material consumption and reactivate the dryer.
Wittmann also was showing its new Aton plus segmented wheel dryer for the first time at a U.S. show. It's a new design and has a new touch-screen user interface with a graphical menu for easier operation. It also gives the operator an overview of all drying parameters as well as a way to visualize and control the material loaders. The various features on this dryer for saving energy include a weekly timer to control automatic startup and shutoff, optimizing the regeneration phase through the 3-save process and automatic selection of the drying method when in EcoMode. Energy savings with the Aton plus has been measured at up to 48 percent when compared to conventional wheel dryers.
ON-LINE TOOL MEASURES MOISTURE
Novatec, Baltimore, introduced its Moisture Master central PLC for processors to get real time moisture data of the resin leaving a drying hopper. The goal is to let the user know whether drying is satisfactory before a product is made. Moisture Master has a color touch screen and sensors to provide accurate, real time moisture measurements for as many as four hoppers at one time. Officials said it takes a sample every second.
Rob Neilley, senior correspondent
Contact:
AEC, 847-273-7700, www.aecinternet.comDri-Air Industries Inc., 860-627-5110, www.dri-air.comMaguire Products Inc., 610-459-4300, www.maguire.comMoretto US, 614-530-0440, www.moretto.comNovatec,410-789-4811, www.novatec.comUniversal Dynamics,703-490-7000, http://unadyn.piovan.comWittmann Battenfeld Inc., 860-496-9603, www.wittmann-group.com
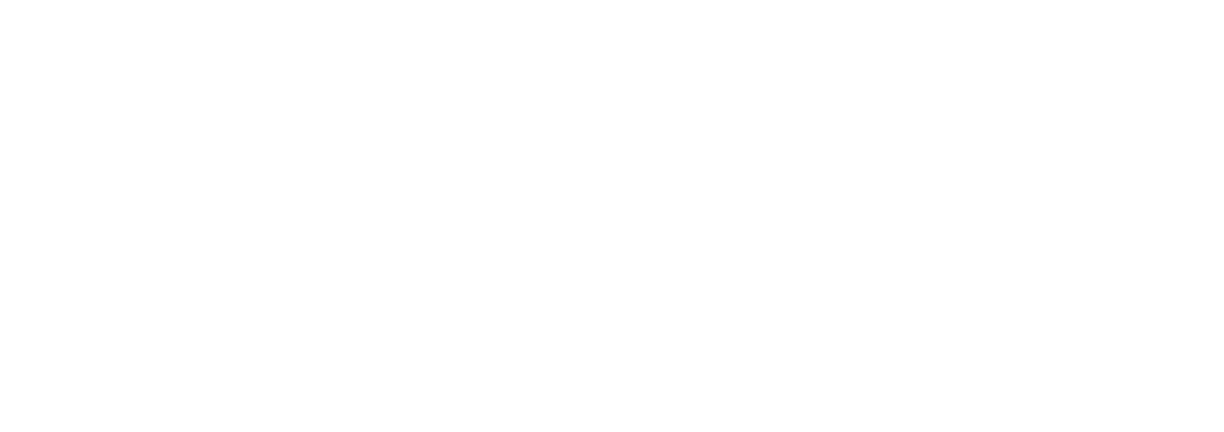