There was a plethora of robots at NPE, many of which were designed for removing parts from injection molding machines, the subject of this report. Other automation applications will be addressed in a later report.
However, the flashiest demonstration was not for part removal as such, although it could have been adapted for that purpose. Yushin America Inc., Cranston, R.I., showed a double-arm unit with both arms mounted on a single track. The system alternately manipulated a bowling ball, held by and between the robot arms, and, in a second demo, lined up a series of blocks with letters on them to spell "Yushin."
The Yushin system appeared readily adaptable to a variety of packaging or assembly operations, but was presented as a concept robot that was not for sale. However, the components can be configured into a salable product, says Ronald K. Bryant, manager of equipment sales. Yushin also had ready-for-market robots at other booths.
Yushin balanced this developmental approach with exhibits of robots on injection machines, some shown in operation, from a wide variety of suppliers: Boy Machines Inc., Exton, Pa.; Sumitomo Demag, Strongsville, Ohio; Fortune International Inc., Somerset, N.J.; JSW Plastics Machinery Inc., Corona, Calif.; Toyo Machinery & Metal Co. Ltd., distributed by Maruka U.S.A., Pine Brook, N.J.; Niigata Machine Techno Co. Ltd., Wood Dale, Ill.; Nissei America Inc., Anaheim, Calif.; Toshiba Machine Co. America, Elk Grove Village, Ill.; and Woojin Plaimm Inc., Norco, Calif.
In the JSW booth, a Yushin RCII-150 was mounted on a JSW J85AD press. Medical filters were molded and placed on a Yushin belt conveyor within custom Yushin safety guards.
A Yushin YC-series robot was mounted on a Boy 35E injection machine. The single-cavity mold produced silicone wrist bands for a charitable organization. A custom end-of-arm tool removed the wrist band from the core with a series of orchestrated robotic movements.
Cartesian vs.
anthropomorphic
There is seemingly no end to the urge to modify, enhance and improve upon the basic Cartesian robot design, which consists of three arms, one each for X-, Y- (kick) and Z-axis movements, plus whatever capabilities that are built into the end-of-arm tooling.
The other basic robot design for plastics processing is the six-axis, or anthropomorphic design, so called for its ability to essentially replicate the capabilities of the human arm and wrist. A Cartesian robot, if programmed for simultaneous multiple-axis movement, or fitted with multi-action end-of-arm tooling, somewhat blurs the lines between the categories, but any direct observer is unlikely to mistake one from the other.
Robots built in Asia and Europe have dominated the North American plastics processing market for decades, but now Ranger Automation Systems Inc., Shrewsbury, Mass., says it is bringing to the market completely U.S.-built models.
Ranger's Ultra-Compact robots are for molding machines with tight overhead clearances in which conventional robots won't fit. Designed with a triple-stage arm, the robot can extract parts as tall as the available space from the top of the press to the crane or ceiling limitation. The compound action of the arm provides up to 50 percent faster take-out speed, as compared to alternative approaches, along with extended stroke for lower part release on large-tonnage machines. The Ultra-Compact series is available in three- to six-axis configuration, with A-, B- or C-axis servo wrist rotations.
The Ranger RTA Robots come standard with features that are options on so-called low-cost robots. Powered by Allen-Bradley controls and drives, standard equipment includes: two pressure circuits; two vacuum circuits with confirmation sensors; tool-less, quick-change, end-of-arm-tooling clamp; touch-screen pendant control; digital program backup; and a custom engineered mounting riser to fit any molding machine. The RTA robots are available in five sizes to fit machines from 50 to 1,500 tons.
A number of injection machine builders have begun supplying their own robots with their machines or, alternatively, integrating other robots with their machines.
Arburg Inc., Newington, Conn., put on a show of robotic capabilities to accompany its injection machine and additive manufacturing exhibits. Following injection molding of a small toy, a Multilift Select robotic system performed handling and assembly of the toy, and removed it from the machine via a chute for inspection and coding operations.
In a medical molding cell, 64 pipette tips were molded in a cycle time of less than five seconds, and removal was performed by a robotic system from Hekuma GmbH, Eching, Germany.
During overmolding of continuous-fiber-reinforced thermoplastic inserts, a six-axis robotic system picked up two sheets of different thicknesses from a magazine. The flat inserts were heated using a heat source in the gripper system and transferred at a precise temperature for forming. The resulting composite part illustrated the potential of the process for the automotive industry.
Negri Bossi North America, New Castle, Del., exhibited four injection molding machine models highlighting robots from its Sytrama USA brand, also of New Castle. A Vesta All Electric VE330-1580 machine running a four-cavity coat hanger mold with gas assist featured part removal by the new Sytrama robot Model S9-L.
An Eleos 65-210 machine ran a single-cavity sunglasses case with living hinge. This two-platen machine used the new Sytrama One-L Model robot to demonstrate automation of a standard injection molding process with the robot configured for clamp-end deposit of the molded part.
The Canbio Evolution e300-2100 machine was using a specialized microcellular foam injection molding technology with the new Sytrama Model S9T-L robot.
A Canbimat Multi-Material e210-850h-320v injection machine with rotary mold table produced a two-color decorative container. A Sytrama Model S7-L robot including special gantry mounting provided parts handling.
Some injection-machine builders integrate brand-labeled robots with their machines. Personnel at the Milacron stand said it is not necessary for Milacron to make robots, as good options are already available on the market. Milacron showed robots from Sepro America LLC, Warrendale, Pa., in its booth, although neither Milacron nor Sepro would officially confirm a brand-labeling relationship.
Sepro robots were also seen in the exhibits of several injection molding machine manufacturers: Sumitomo; Absolute Haitian Corp., Worcester, Mass.; G. Pernoud North America Inc., Rochester Hills, Mich. (with Billion SAS, Bellignat, France); Stork Plastics Machinery B.V., Hengelo, Netherlands; and Maruka/Toyo.
Sepro used NPE to introduce three new lines of robots for injection molding machines with clamping forces between 700 and 5,000 tons. The new large robots are successors to the Sepro Generation 4 line. In general, the new S7 line three-axis robots and 7X line five-axis robots have longer kick (Y-axis) strokes, longer vertical (Z-axis) strokes and can handle larger payloads than their G4 predecessors. The Strong line is a range of universal robots that make the speed and precision of full-servo actuation available to molders who have applications that require simple pick-and-place functionality and simple downstream operations.
In the Sepro booth, the new robots were represented by a five-axis 7X45 model, which combines the same three-axis platform as the S7 robots with a two-axis servo-driven wrist developed in partnership with Stäubli Corp., Duncan, S.C.
Unlike pneumatic wrists, which can only move to set positions at zero degrees and 90 degrees or zero degrees and 180 degrees, the 7X wrists can move from zero to 180 degrees and from zero to 270 degrees or anywhere within that range with absolute precision. Injection molders are choosing five-axis robots because the servo wrist gives them accuracy and flexibility to handle technically demanding parts, with lower tooling costs, less maintenance, cleaner operation and faster mold changes, says Jim Healy, Sepro's VP of sales and marketing.
Wittmann Battenfeld Inc., Torrington, Conn., presented a molding cell with a MacroPower 650/8800 B6P molding machine with a clamping force of 650 tons. The press molded a specialty box with a one-cavity mold. Automation was via the W8437X45 pro robot, part of the new W8 pro robot series.
Engel Machinery Inc., York, Pa., introduced the e-pic robot with linear movements and a swivel arm for use with both Engel and other injection machines with up to 220 tons of clamping force. The compact design is adaptable for either vertical or horizontal part removal. The weight of the moving parts is minimized to reduce both take-out times and energy consumption.
Shini Plastics Technologies LLC, Suwanee, Ga., offers its ST3-MT and ST3-LT robots for medium and heavy loads, respectively. They are specifically designed for use with two-plate molds for hot-runner systems and use magnesium alloy materials to minimize weight while maintaining rigidity for reliable operation.
Kuka Robotics Corp., Shelby Township, Mich., simulated loading and unloading of an injection molding machine to demonstrate its KR Agilus 6 R700. The KR Agilus is a six-axis robot with universal mounting for fixing to the floor, wall or ceiling. Models available are the KR6 R700, KR6 R900 and the KR10 R1100.
Merle R. Snyder, senior correspondent
Contact:
Arburg Inc., 860-667-6500, www.arburg.comEngel Machinery Inc., 717-764-6118, www.engelglobal.comHekuma GmbH, 49-8165-6330, www.hekuma.comKuka Robotics Corp., 866-873-5852, www.kuka-robotics.comNegri Bossi North America/Sytrama USA, 302-328-8020, www.negribossiusa.comRanger Automation Systems Inc., 508-842-6500, www.rangerautomation.comSepro America LLC, 412-459-0450, www.sepro-america.comShini Plastics Technologies LLC, 770-831-5959, www.shini.comStäubli Corp, 864-486-5455, www.staubli.usSytrama USA, 302-328-8020, www.sytramausa.comWittmann Battenfeld Inc., 860-496-9603, www.wittmann-ct.comYushin America Inc., 401-463-1800, www.yushinamerica.com
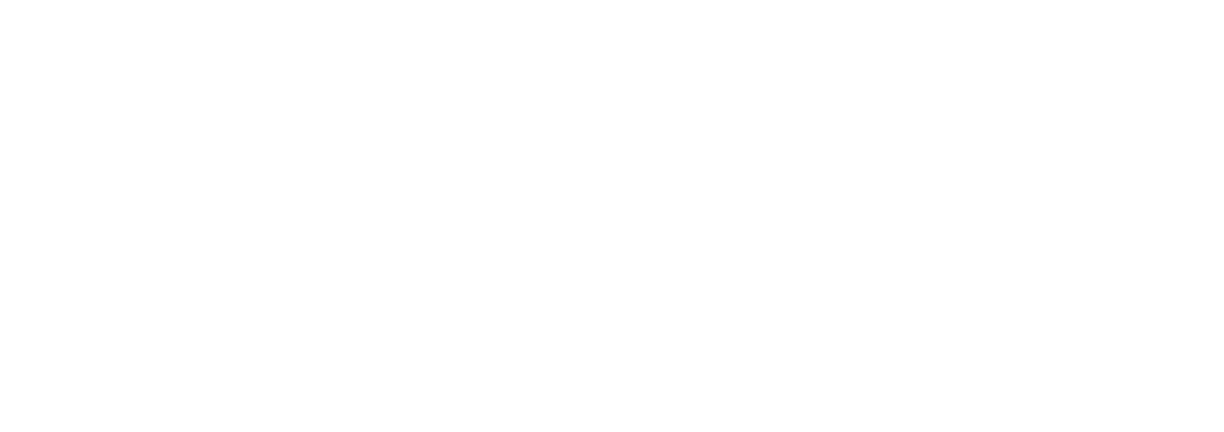