The boys are back in town and they've brought a few friends from China. That town is Marion, Ohio, and the company is injection molding machinery maker HPM North America Corp., the latest iteration of Hydraulic Press Manufacturing Co., which began in 1877 in nearby Mount Gilead, Ohio.
"This is our effort to relaunch HPM," said John Beary, HPM's general manager of sales and marketing. "We think we have a very strong product. We're really trying to get aggressive from a marketing standpoint."
As part of that outreach, HPM held an open house in early December, inviting 50 companies to Marion, Ohio, roughly 20 miles west of Mount Gilead, where HPM first began making presses for the extraction of apple cider. At the new facility, officials have one of the original presses and a bowl of Granny Smith apples sits as the centerpiece on a conference room table — an homage to HPM's history. Its marketing and advertising materials carry a picture of an apple and the playful line, "It started with an apple."
Step into the factory and the apple press is seated near a table of mixing screws, the Double Wave and Triple Wave designs invented and patented by HPM. The company still is offering those products. Though the patents have expired, the trademarks still hold.
The men running the company talk about how important it is for the industry to know that HPM is very different today in terms of the technology it provides. These injection molding machines are not general purpose. They are customized, energy efficient, expertly engineered. An HST 80-ton press on view in the factory is equipped with a controls system from Eurotherm and programmed by DL Hubbell Controls Inc., the result of HPM's recent acquisition of that company. Eurotherm controls are standard on HPM machines.
"For HPM North America, the control system is vital to the machinery," said Bill Flickinger, HPM president, "being user friendly and certainly meeting North American standards. Also, HPM offers options to our customers."
On that HST 80, officials changed nozzle tips from metric — the parts for these machines were built by parent company Yizumi in China. Yizumi will build the machines to specs and officials at HPM will do the programming. The HST series goes from 60 to 650 tons and the line has been on the market for the last nine to 10 months. Its newest line, HS II, officially was introduced at the open house. That new two-platen machine, which features an AC servomotor and new clamping mechanism, will be spotlighted at NPE 2015.
Both lines offered are designed to be energy efficient with a combination of electrical and hydraulic driving technology. On the HST series, the clamping unit has an optimized platen design with high rigidity and enlarged space between the tie bars; it is an SPI-based platen layout. There is a new ejection system design with longer ejection stroke, and also bigger space and better rigidity. There is a hydraulic-driven gear-type mold height adjusting mechanism and a relocation of mechanical safety interlock for easier operation. Standard features on the injection unit include a bimetallic barrel; proportional back pressure control; a nozzle with a half-inch radius and one-eighth-inch orifice, with three-eighths-inch penetration past the mold mounting surface of the stationary platen; a general-purpose screw with a 20-1 length-to-diameter; and a check-ring-type non-return valve. Sprue break, hardware and circuit allow the nozzle to retract from the sprue. The fully enclosed unit itself has a new screw design with a better plasticizing and mixing effect; a magnet beneath the hopper protects the screw from metal damage.
"You cannot expect people to buy machines out of nostalgia," says Beary. "We have to be better than we were in the past."
Flickinger had spent 33 years with the former HPM. Dave Hubbell, who had owned DL Hubbell, also had worked for HPM years ago. He now is general manager of HPM Control Retrofit Group. New to this group is Nicholas Zeng, who is HPM business manager in the global business development department for Yizumi. That is, Guangdong Yizumi Precision Machinery Co. Ltd. of Foshan City, China, which purchased HPM in 2011. The purchase included patented technology of HPM's injection molding machines, die-casting machines for aluminum and magnesium alloy, global brand names and trademarks, a global supply system, global customer resources and partial production facilities.
This year Yizumi expects total corporate sales of $200 million, including $90 million in sales of injection molding machines.
"We have a very strong owner that is committed," says Flickinger. "We have a five-person engineering department but then we're backed up by a group of about 20 engineers in the die-cast engineering department and about 30 engineers in the injection molding engineering department at Yizumi."
Zeng proudly showed a video of Yizumi's facilities in China. The campus holds multiple facilities. Parts are produced in China, then they are shipped to HPM to be built. Yizumi itself is experiencing massive growth; this month, its planned IPO is expected to raise $60 million.
The goal is to use the HPM technology that has been developed over the past 135 years combined with modern control technology to research, develop and manufacture injection molding equipment. HPM is offering service on legacy equipment, overseen by Randall Clements, GM of Bivouac Engineering & Services, which provides service and parts for legacy machines and modifications of new machines. There are some 20 to 25 Hemscheidt machines still in production in the North American market. The latest models of Hemscheidt were sold in North America up through the 2004-05 period. HPM's repair business ebbs and flows but officials are ready when a spare part is needed.
"If anybody loses a tonnage cylinder, we have a spare part," said Flickinger as he scanned the file drawers stacked on shelves at HPM's factory. The history is here; organized neatly are the service jackets back to the 1940s. Officials have received calls on some 60 machines.
On the floor is the latest generation of equipment offered from HPM, an HS II 1,100-ton two-platen servo hydraulic machine. Historically, HPM had offered two-platen machines in the lines Hemscheidt, Next Wave and Freedom Series. But the differences between those two-platen lines and the HS II are stark, Beary explains.
First, the HS II line uses an AC servomotor to drive a fixed displacement pump that supplies hydraulic oil for controlling the motion of the machine. By using an AC servomotor, the HS II machine can be extremely energy efficient because the system works to supply closed-loop pressure and closed-loop flow on demand. When the machine cycle does not require any demand from the hydraulic system, the motors are turned off.
"Our previous two-platen machines were supplied with hydraulic systems that used fixed displacement pumps that were driven by AC motors that were running all the time," Beary says. "The AC servomotor system that we use on the HS II series can offer customers an energy savings of up to 30 percent when compared to our older machines."
Then there is the design of the clamping mechanism. The former two-platen machines were designed so that all four tie bars retracted with the moving platen when the clamp opened.
"Although this was a great feature for providing easy access to the mold area, it usually created alignment issues between the tie bars and the locking mechanism," Beary says. Also, the pancake cylinders and locking bushings that developed tonnage on those legacy machines were prone to mechanical failure. On the HS II, all four tie bars remain fully supported by the stationary platen and moving platen while the clamp is opening and closing. Officials used a split nut mechanism that is attached to the rear of the moving platen to mechanically engage the tie bar threads when the clamp is closed.
"Once the threads are engaged, we energize four cylinders that are located behind the stationary platen to build tonnage," Beary says. "For access to the die space, we can offer a tie bar puller as a standard option."
At NPE, officials also will unveil a 260-ton all-electric.
Angie DeRosa, managing editor
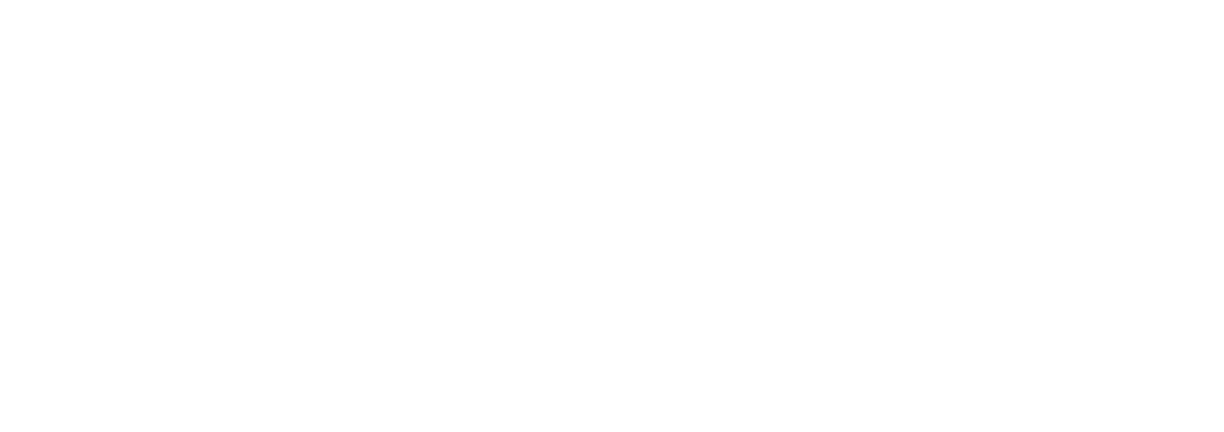