Numerous packaging innovations, backed by new machinery technology, were launched or demonstrated at the triennial NPE show.
The high-output, fast response, multi-cavity, multi-material and multi-color conditions demanded by packaging applications were tackled in novel and efficient ways in numerous booths where suppliers demonstrated integrated molding cells dedicated to thin-wall or high-speed jobs.
MILACRON TAKES A 'CAN DO' ATTITUDE
Klear Can is a new multi-layer barrier packaging technology from Milacron LLC, Batavia, Ohio, designed as a transparent alternative to all-metal or glass food containers. Klear Can yields 14 ounce (410 milliliter) cans made with an EVOH barrier fully encapsulated within an inner and outer layer of clarified PP, which is crimp-sealed with a full-aperture, easy-open metal lid.
The multi-layer, multi-material, co-injection technology was developed by Milacron following its acquisition of Kortec Inc., a supplier of co-injection systems. Kortec is now branded as Milacron Co-injection. Klear Can packaging can be used in hot-fill, aseptic, pasteurization, sterilizing and autoclaving applications involving temperatures up to 266 degrees Fahrenheit, and provides up to five years of product shelf life, says Russell Bennett, director of sales and marketing, co-injection systems at Milacron.
The design of the Klear Can system is such that conventional and existing equipment for filling and sealing can be used. Approximately 50,000 filled cans are undergoing field testing and approval. Milacron anticipates the first products in Klear Can packaging will hit store shelves in 2016.
Milacron designed the Klear Can system with a high-precision, co-injection mold from StackTeck Inc., Brampton, Ontario, an integrated Milacron co-injection hot-runner controller; and a Ferromatik toggle press with an add-on unit mounted atop the main unit in a piggyback position. The system is designed to inject the PP and EVOH into the mold simultaneously. The process technology precisely controls the thickness of the EVOH barrier layer (0.001 inch), which represents 10 percent of the sidewall thickness, and ensures the barrier covers at least 99 percent of the container.
At NPE, Milacron produced the Klear Can with a 1mm side wall in a four-cavity mold on a Ferromatik 280 press in a cycle time under seven seconds. The primary unit delivered a 357 gram shot—split into two streams— while a secondary injection unit with barrier screw atop the machine supplied 17 grams of EVOH material.
The Ferromatik 280 Klear Can system shown at NPE is able to produce 12 million cans per year, while a 650-ton Ferromatik with a 32-cavity tool can mold up to 80 million cans per year.
Milacron, which operated the largest booth at NPE, also introduced a new Ferromatik 580 metric ton (638 U.S. tonner) to its line of toggle presses that can be specified for packaging. Eleven sizes now are offered (from the F50 through F650) in a series that can be specified with electric, hydraulic or hybrid drive systems (a servo-driven 5-point toggle clamp with an electric or hydraulic driven ejector).
Milacron demonstrated high-speed, co-injection capabilities of the Ferromatik 580 at NPE in the production of a 5-gallon pail utilizing 50 percent regrind HDPE in the core. The primary injection and piggyback secondary unit delivered a 950-gram shot to the single-cavity mold from Calframax Technologies Inc., Oldcastle, Ontario, whose mold cooling technology helped minimize cycle times to 13.9 seconds. This machine can be configured for conventional rigid packaging applications.
Milacron enhanced its line of two-platen machines with the introduction of its Maxima Performance series for large part molding, ranging from 310 to 950 tons. The new series incorporates a servo-hydraulic accumulator power pack for faster cycle times. Servo motor technology is combined with an internal gear pump to achieve operating efficiencies seen with an all-electric unit. The model requires no power to maintain clamp tonnage during machine operation, which helps to trim overall energy usage 70 percent compared to similarly sized fully hydraulic models.
Other features of the Ferromatik Performance series include a compact footprint with the injection unit on linear bearing guides to minimize friction during movement; separate linear position transducers for accurate injection and ejector position control; and a new Windows-based Mosaic+ control with a 21.5 inch multi-touch screen. A Maxima P 500 unit produced spray nozzle container caps from PP in a 24-cavity mold with a collapsible core in 9.5 seconds.
HAITIAN HARNESSES SERVO-ELECTRIC POWER
NPE marked Zhafir Plastics Machinery GmbH's North American debut of the new Zhafir Zeres series servo-electric injection molding press, designed with integrated hydraulics for the ejector, carriage movement and core pull functions.
Machinery from Zhafir Plastics Machinery, a division of Ningbo Haitian Machinery Co. Ltd., Ningbo, China, is sold and serviced in the U.S. and Canada by Absolute Haitian Corp., Worcester, Mass.
The Zeres series is identical in construction to the Venus II larger tonnage all-electric series, but is distinguished by the integrated hydraulics, controlled with a variable pump. The Zeres is currently offered in seven clamp tonnages ranging from 45 to 259 tons. Inclusion of an integrated power pack reduces the machine cell's overall footprint and trims its price approximately 15 percent compared to the Venus II, says Glenn Frohring, president of Absolute Haitian.
Two integrated hydraulic core puller interfaces are installed on the moving platen and provide increased and adjustable flow and pressure compared to an external power pack. The integrated hydraulics drive carriage movement and nozzle touch pressure are adjustable on the control with a two-step setting.
Other features include a matching servo motor and servo drive for injection that delivers injection speeds up to 350mm per second (up to four injection units are available for each clamp size). A servo-electric drive operates the five-point toggle clamping unit, which has been redesigned to reduce platen inertia and joint stress for reduced dry cycle times.
A 135-ton Zeres press at NPE molded a 131-gram donation box from crystal PS in a single-cavity tool in a 35-second cycle. The demonstration showcased the unit's core pull sequencing with the integrated hydraulics, in production of a rigid consumer part with high dimensional stability, low shrinkage and low water absorption and clarity.
ENGEL ENHANCES ENERGY EFFICIENCY
Engel Machinery Inc., York, Pa., rolled out its new 720-ton hybrid e-speed toggle unit featuring a new servo-electric drive concept on the clamping unit that stores the braking energy from the platen movement and either transfers the captured energy back to the motor or feeds excess energy back into the grid. The new flywheel design helps to avoid power peaks when short cycle times are combined with high clamping forces, resulting in a lower and constant connected load, says Joachim Kragl, director of advanced molding systems and processing.
The new model incorporates the all-electric aspects of Engel's e-motion and e-cap models with the high performance of the Engel speed series for high injection speeds with energy efficiency. Plasticizing and screw recovery are driven electrically while injection, with speeds up to 800mm per second, is partially hydraulically driven. At the show, an e-speed 720/90 US model molded thin-walled 1.5-liter ice cream containers from PP in a four-plus-four cavity tool from StackTeck in 6.5 seconds.
KRAUSSMAFFEI FOCUSES ON COMBO
TECHNOLOGIES AND THIN-WALL PARTS
KraussMaffei Group USA, Florence, Ky., expanded its AX line of all-electric toggle machines with a 505 tonner and 618 tonner. At the show, an AX 180-750 unit within a molding cell that featured KraussMaffei's MuCell-based CellForm process produced a lightweight panel for coffee machines from a PC in a 36-second cycle time. The MuCell reduced part weight, while inductive dynamic mold heating from RocTool Inc., Charlotte, N.C., produced the high-quality part surface, says Paul Caprio, president of KraussMaffei Corp., a subsidiary of KraussMaffei Group.
KraussMaffei's sister company, Netstal, demonstrated a relatively new thin-wall centering concept in the production of 44-ounce thin-wall stadium cups with an in-mold label on an Elion 3200-900 unit. With thin-wall packaging, the ratio of the flow path to the wall thickness indicates a higher level of molding difficulty as the ratio increases. For the 44-ounce cup, the ratio is 300:1.
Netstal's thin-wall centering practice minimizes core movement by means of rheological flow paths and varying melt pressure levels, which allows for high speed injection without core shift. Netstal demonstrated the turnkey molding cell, built for a U.S. molder, in the production of the PP cups with a shot size of 211.2 grams in a 7.8 second cycle time.
SUMITOMO SETS ITS SIGHTS ON
HIGHER CAPABILITY
Sumitomo Demag, Strongsville, Ohio, introduced its SE-EV-HD series of high-duty all-electric toggle machines designed for the production of thick-wall parts and complex parts with thin and thick walls. Use of a high-power injection servo system enables longer and higher pack and hold pressures that prevent cosmetic issues with thick-walled parts. Its high pressure capabilities allow the unit to deliver full pressure for up to 40 percent of the molding cycle while maintaining molding stability. Features include proprietary belted electric motors for plasticizing and ejection, a high-speed direct-drive motor for clamping, and a linear platen support system and rigid frame for mold linearity and parallelism, says Jeremy Krismer, sales representative.
The high-duty unit is ideal for processes with cycle times of 15 seconds and up, but the model is flexible enough for use in thin-wall molding applications as well. Sumitomo offers the new series in three clamp sizes of 112, 146 and 202 tons. An HD version that provides injection speeds up to 1,000mm per second is available.
A 202-ton SE180EV-HD model produced a unique IML soup/beverage cup featuring molded ribbing that protrudes from two opposing sides of the cup designed to protect the hands from the heat of the product in the container. The unit produced cups weighing 22 grams and 26 grams from PP in a two-cavity hot-runner, valve gated mold from K.M. Planning Ltd., Tokyo, on a 20-second cycle.
ARBURG PRESENTS
PACKAGING-SPECIFIC MODELS
Arburg designed a packaging version of its Allrounder series that combines its Hidrive clamping and Alldrive electric injection units. An Allrounder 630 H servo-electric toggle clamp model featuring a 265-ton clamp and size 1300 Alldrive injection unit produced 7.5 gram round lids from transparent PP that are labeled in-mold, in a four-cavity tool every 3.5 seconds, says Friedrich Kanz, president and CEO of Arburg Inc., Newington, Conn.
Allrounder H units designed for packaging optimize the relationship between the tie bars, clamping force and mold opening travel to achieve fast, precise and energy-saving movement. Arburg offers the packaging configurations in six clamp tonnage sizes ranging from about 143 to 506 tons.
TOYO UNVEILS ALL-ELECTRIC LINE
Maruka U.S.A., Pine Brook, N.J., the exclusive North American distributor of Toyo Machinery & Metal Co. Ltd. injection presses from Japan, introduced Toyo's new Si-6 series of all-electric injection presses to the U.S. market. The series is more compact and runs 33 percent faster than the Si-5 line due to a redesigned V- clamp unit and its new System600 control, which runs 10 times faster than the previous version while offering greater functionality.
The new series, available in 12 models from 55 to 1,050 tons, features Hitachi servos and redesigned injection units on the larger tonnage sizes. The controller has a 15-inch touch screen panel and incorporates a new HSP mold protection program and a mold condition analyzing function. At NPE, a Toyo Si-300-6 unit produced spoons in a 32-cavity mold in a four-second cycle time, two seconds faster than what was possible with the previous model, says Dale Bartholomew, product manager.
FCS TARGETS TWO-COLOR,
TWO-MATERIAL JOBS
Hydraulic and servo-hydraulic injection presses from FCS Group (Fu Chun Shin Machinery Manufacture Co. Ltd.) of Tainan, Taiwan, made their debut at this year's NPE at the booth of Maruka USA, FCS's new North American distributor. Maruka rolled out the 160-ton FCS FB-160 RSV, a two-color, two-material servo-hydraulic injection molding machine with a rotary table that is configured into a turnkey system by FCS for the production of 47-gram pet brushes, molded in a one-plus-one cavity tool from PP in a 35-second cycle. The rotary table is controlled by a servo valve driving a double servo power system to shorten turning time by 50 percent compared to hydraulic actuation, says Bartholomew.
HPM HERALDS HIGH-SPEED CAPABILITY
HPM North America Corp., Marion, Ohio, showed its HST line of hydraulic-servo toggle injection machines designed for high-speed packaging and cap and closure applications. Initially, 10 models ranging from 60 to 650 tons will make up the line. A new screw design enhances plasticizing and mixing and a new five-point linear position toggle clamping design with a simple lockup mechanism uses an optimized and highly rigid platen configuration. The line has a new ejection system that provides a longer ejection stroke, as well as an automatic mold height adjustment system and automatic central lubrication system. Energy savings are derived through the use of Yuken servo-hydraulic power systems, according to John Beary, general manager, sales and marketing.
HPM also rolled out a new smaller tonnage all-electric line. The HSE series comes in four models ranging from 60 to 260 tons and uses Keba controls. Belt and ball screw servo-drive systems are employed for the primary machine motions including clamping and part ejection.
JSW UPGRADES ALL-ELECTRIC LINE
JSW Plastics Machinery Inc., Corona, Calif., introduced a 496-ton model in its J-ADS series of all-electric, servo-drive, double-toggle presses. The new unit is the largest in the series, with three smaller models ranging down to 242 tons. The J450ADS model features a newly designed, 28 percent smaller diameter barrel mated with updated screw technology to improve plasticizing and injection while trimming energy requirements 15 percent, says Robert Columbus, marketing and regional sales manager.
Lightweight, highly rigid clamping is designed to extend mold life and reduce grease use for a cleaner machine. The platen is about 4 inches wider than prior designs to accommodate larger tools or additional cavities. The moving platen rides on linear guide rails. A hydraulic power pack (hydraulic pump and cylinder configuration) is integrated into the unit, increasing nozzle touch force to 4.4 tons. A new Syscom5000i Multi-touch panel controller with a 15-inch touch screen brings swipe and pinch-to-zoom functionality to the controls and replaces the previous controller. The unit accommodates mold heights up to 900mm and has a tie-bar distance of 900mm by 810mm.
GLUCO UNVEILS CHINA-MADE
SERVO-HYDRAULIC PRESSES
Gluco Inc., the North American representative for China-based injection molding machine maker Chen Hsong Machinery Co. Ltd., now offers the Jetmaster Ai series of three-platen servo-hydraulic toggle presses, ranging from 98 to 228 tons. The unit meets all SPI protocols. It features a servo-hydraulic circuit that reduces energy demand by 80 percent compared to conventional hydraulic models, says Ryan Pysarchik, general manager.
STORK DELIVERS PAIL-MAKING UNIT
Exhibiting at its first NPE, injection molding machine supplier Stork IMM B.V., Hengelo, the Netherlands, demonstrated its hybrid Stork Pail line 4400, which produced 0.5 gallon 90 gram round pails in two cavities in 6.5 seconds. This machine is targeted toward containers for the food industry and can be lubricated with food-grade oil or lubricants.
Stork's Pail line comes in toggle clamp tonnages ranging from 220 to 2,000 tons, or special electric clamp up to 660 tons. Standard screw geometries of 25 and 27 length to diameter provide high-quality mixing. Features include an electric screw drive for plasticizing with a servo-accumulator drive system and variable displacement pump for injection and other functions. Each machine is custom built but features a 19-inch Linux industrial control system with a touch screen panel. Stork builds the controller.
NEGRI BOSSI ENHANCES ITS
SMALL AND MEDIUM MACHINES
Negri Bossi North America, New Castle, Del., demonstrated a developmental version of its EOS series of small, two-platen hydraulic injection molding machines, this one in a servo-electric/hydraulic configuration. The 71.5-ton El EOS model at the show featured a long opening stroke and long ejector stroke, and produced sunglass cases.
Negri Bossi is in the process of updating the entire EOS hydraulic line. Former clamp tonnage sizes of 55, 71.5, 88, 121 and 132 tons will be resized into three models of 77, 121 and 198 tons initially. The newly designed EOS hydraulic models still feature twin injection cylinders with a very large part-drop area.
Negri Bossi also offers the EOS SE (Smart Energy) version it introduced in 2012, featuring servo-pump technology that operates on an on- demand basis to reduce energy consumption by up to 40 percent versus standard hydraulic units. It has a two-platen, cantilever design combined with twin injection cylinders for a compact footprint.
Negri Bossi is also upgrading its Vesta line of all-electric machines, which range from 88 to 475 tons, for higher performance and greater operating efficiency. The line is enhanced with more generous tie bar spacing, wider platens and greater shot weight capacity.
Vesta features direct-drive, servo-electric actuators for screw rotation and mold clamping functions, as well as twin, heavy-duty NSK injection ball screws and Heidenhain drives that handle higher forces and provide longer operating life. The regenerative clamp drive system recovers braking power, says Tony Firth, president.
Mikell Knights, senior correspondent
Contact:
Absolute Haitian, 508-459-5372, www.absolutehaitian.comArburg Inc., 860-667-6500, www.arburg.comEngel Machinery Inc., 717-764-6818, www.engelglobal.com/usGluco Inc., 616-457-1212, www.gluco.comHPM North America Corp., 740-382-5600, www.hpmmachinery.comJSW Plastics Machinery Inc., 951-898-0934, www.jswpmi.comKraussMaffei Group USA, 859-283-0200, www.kraussmaffei.comMaruka U.S.A., 973-487-3800, www.marukausa.comMilacron LLC, 513-536-2000, www.milacron.comNegri Bossi North America, 302-328-8020, www.negribossiusa.comStork IMM B.V., 31-74-2405-000, www.storkimm.comSumitomo Demag, 440-876-8960, www.sumitomo-shi-demag.eu
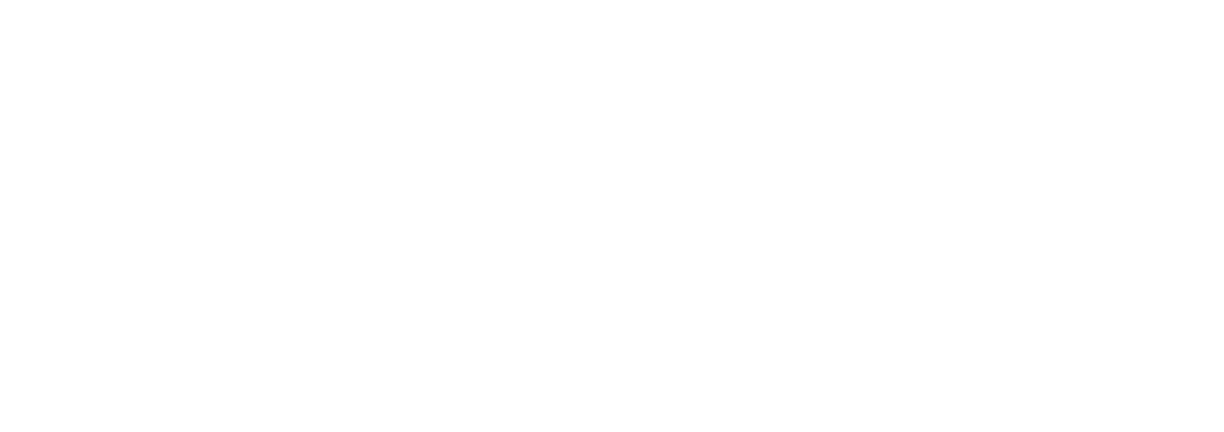