New or upgraded machinery capabilities are making possible injection molded automotive parts that advance light-weighting or new material combination trends. Servo technology continues its charge into new machinery configurations designed to handle new types of auto parts. Molders looking for space-saving presses that handle larger tools yet use less energy, or allow for new arrangements for multi-shot molding, are driving the newest machinery developments.
HAITIAN GOES LARGE, COMPACT AND CAPABLE IN THE SAME UNIT
Absolute Haitian Corp., Worcester, Mass., now offers its all-electric Zhafir Venus series in a 730-ton model for the production of automotive, electrical and white goods. It delivers high precision at low injection speeds and offers an injection compression function standard for in-mold decorating.
The new Venus VE 6500 II 720-ton model, the largest in a range which begins at 44 tons, will be available for North American molders in the second half of the year.
The second-generation Venus series replaces the original Venus line launched in 2007. Features of the new presses include tie bar spacing of 1,080mm by 1,080mm, and a choice of four injection units offering shot sizes from 25.4 to 75.5 ounces. The series features an updated, more compact injection unit capable of injection speeds up to 350mm per second in a response time of 35 milliseconds, depending on the injection unit. It also has an optimized five-point toggle clamp that increases the platen intensity, reduces platen inertia and joint stress. It boasts a twin ball screw for the ejector balance speed and torque for high acceleration and precision, says Glenn Frohring, president of Absolute Haitian Corp.
Changeover times are shortened with a swiveling injection unit, an encoder for mold height adjustment and a rapid release coupling for the ejector bolt connection. Zhafir Plastics Machinery Co. Ltd., a subsidiary of Haitian International Ltd., says the sensitivity of the clamping unit coupled with the ability to operate production functions in parallel allowed it to mold an 1,800-gram vegetable bin container for a refrigerator from PC in 23 seconds, a cycle time much shorter than the 75 seconds required to mold the same part on a similar sized servo- hydraulic machine. Although not specific to an automotive application, that was one important test.
In a second test, a customer molded an automotive interior part from PP decorated in leather using an in-mold decorating process. According to Zhafir, the customer was better able to regulate both temperature and pressure with more precision than when running the part at low pressure on a hydraulic machine.
A NPE, Haitian demonstrated the all-electric model in a high-speed configuration. It was a 427-ton Venus II/p with a shot size of 2.54 ounces.
Haitian also announced the availability of two new injection units for the Venus II series. A 160 injection unit offers shot sizes from 1.83 to 2.47 ounces (52 to 70 grams); a smaller 50 injection drive has shot sizes as small as 0.39 ounce (11 grams) for molding micro parts.
As reported previously, (PMM February, page 36) Haitian expanded its Jupiter II servo-hydraulic two-platen line with six new model sizes that include clamp tonnages of 506, 618, 730, 844, 1,069 and 1,214 tons.
The Jupiter II line, which now ranges from 506 to 4,496 tons, is offered in standard, mid-level and high-performance (II/h) configurations, which vary by tie bar spacing and mold thickness limits. Molds up to 33 percent thicker can be used on a high-performance press compared to a standard Jupiter II with the same clamping force. Large automotive parts are ideal for the line.
The Jupiter II series utilizes a newly developed and patented servo motor and gear pump design; higher response 75 kilowatt and 110 kilowatt servo drive units incorporated into the closed-loop, simplified hydraulic system; and Keba control systems for reduced energy consumption. It features four clamping cylinders on the fixed platen to quickly build clamp force, while large moving platen supports ensure high platen rigidity during movement with high mold weights.
A 41.55-ounce automotive part made from 20 percent talc-filled PP was molded on a 33-second cycle with a 730-ton Jupiter II at the show. All Jupiter models will be manufactured at a 1.6 million-square-foot facility in Ningbo, China, slated to open in June.
ENGEL REDESIGNS MODEL FOR
DIVERSITY OF APPLICATION
NPE was the North American debut of Engel Machinery Inc.'s redesigned Duo two-platen series (385 to 6,050 tons) for large part molding, featuring a lower operating height for easier access to the mold and nozzle, a new roller rail system for the moving platen, and elimination of a central lubrication system that results in a cleaner mold area, says Joachim Kragl, director of advanced molding systems and processing for Engel, York, Pa.
A 660-ton Duo at the show combined Engel's MuCell-based Foammelt technology and the variothermal injection molding process from RocTool SA, Le Bourget du Lac, France, in the production of an automotive center console component. The PC/ABS component was molded into a lightweight, thin-walled, high surface quality part in a single-cavity RocTool mold in 57 seconds in a single injection molding step. Tool temperature varied from 68 degrees Fahrenheit to 288 degrees Fahrenheit each cycle.
Engel demonstrated the enhanced merits of injection molding thermoplastic materials with thermoplastic sheets in a new one-step process that produces automotive brake pedals in series production that are 30 percent lighter than conventional steel pedals without impairing load-bearing capacity.
Engel also demonstrated its Organomelt process in the production of a composite brake pedal produced from a pre-cut composite fabric sheet that was heated press-side in an Engel-designed infrared oven, then placed in an injection mold and over-molded with a 60 percent glass-filled polyamide 6.
A 220-ton Engel 1050H/230 vertical insert injection unit with an Engel easix TX-90 five-axis robot integrated into the control unit of the press produced the brake pedal in a single cavity in a 57-second cycle. The integration of the robot control allows the gripper to enter the mold with the pre-heated sheet during the opening movement for reduced cycle time. The composite brake pedal is produced in collaboration with car parts maker ZF Friedrichshafen AG, Friedrichshafen, Germany.
KRAUSSMAFFEI'S RANGE OF TECHNOLOGIES ASSISTS AUTOMOTIVE
KraussMaffei Corp., Florence, Ky., expanded its GX line of mid-sized hydro-mechanical two-platen presses with two new clamp sizes and several variants when a second injection unit is added for multi-component or multi-shot molding. NPE marked the U.S. premiere of KraussMaffei's new 990-ton GX 900-8100 model, and it introduced an 825-ton GX model (not at the show), which overall broadened the machine line range from 440 to 990 tons, says Paul Caprio, president of KraussMaffei Corp.
The modular GX series can be configured with an additional injection unit positioned in parallel, vertical, piggyback or lateral horizontally (non-operator side) to the primary injection unit, as well as a GXW configuration where the company's new SpinForm servo-electric rotary table technology is integrated into the clamping platen for fast rotation with high mold weights. Up to four different components can be processed and combined when molding with the GX series, allowing for rigid-flexible parts or soft-touch surfaces. At the show, the new GX 900 model, integrated with the company's LRX 350 linear robot, manufactured a large transport crate from PP with a shot size of 45.5 ounces in a cycle time of about 25 seconds.
A GXH 550-1400/1400 unit featuring a second injection unit in parallel with the primary unit and its new servo-electric rotary table produced automotive fog light covers from a clear and black PC in a 42-second cycle, using a mold from Proper Group International, Warren, Mich.
KraussMaffei used a fully automated form of its FiberForm process on its small CX 300-1400 two-platen hydro-mechanical press to produce airbag housings with a shot size of 350 grams in a 45-second cycle time. FiberForm combines injection molding with thermoforming of composite sheets. The part is 40 percent lighter than its metal competitor, and emerges from the mold ready for use, demonstrating the ability of the technology for large series production.
KraussMaffei also introduced its MC6 Multitouch control system and Adaptive Process Control (APC) machine functions to the North American market.
The new MC6 control features a larger 24-inch screen that allows operators to control multiple actions simultaneously. A simple split-screen display allows users to control complex production processes through finger gestures.
A SlideX guideway, ground into the glass of the control monitor, allows users to control all axes on a machine without looking at the screen. The guideway keeps the user's finger in the right path; the further the operator moves the finger to the left or right, the faster the movement of the operation. A robot also can be integrated to move the axes using the SlideX function. Users can configure their own preferred screen display to show pages from the injection machine or robot, or a live picture from a camera.
KraussMaffei's new APC automatically adjusts the injection molding changeover point and holding pressure profile in each cycle to the current melt viscosity and flow resistance in the mold, making it possible to compensate for fluctuations in the manufacturing process in the same shot. External factors that create process deviations, such as changing temperatures, climate conditions or material batches, can be accounted for.
APC also detects the extent that material viscosity has changed during machine downtime, and can compensate for signs of screw or barrel wear, or the closing behavior of a non-return valve, which can lead to processing irregularities. Adjusting to these deviations results in minimal- to zero-defect molding and faster startup. APC is standard on all of KraussMaffei's injection molding units.
NIIGATA ADDS WIDER PLATENS
Niigata Machine Techno Co. Ltd., Wood Dale, Ill., rolled out wide-platen versions of its large tonnage MDS6000 series. A 600-ton wide platen, commercially available this year, will be followed by a 720-tonner and 950-tonner. The large tonnage models feature two servo motors and dual-ball screws for injection, one servo for screw recovery, two servos for clamping and one servo for ejection.
HPM'S BACK AND BUILDING LARGE PRESSES
HPM North America Corp., Marion, Ohio, showed its new HSII line of hydro-mechanical two-platen presses in seven models ranging from 900 to 3,500 tons. Officially introduced at an open house last year, the new line is designed as a general-purpose model targeting automotive or houseware applications, featuring a compact footprint that assumes less floor space than a comparable three-platen model. Use of an AC servomotor driving a fixed displacement pump supplies pressure and flow in a closed-loop circuit on demand, which trims energy consumption 30 percent compared to conventional hydraulic machines. Eurotherm controls are standard on all models.
LARGE TOGGLES TO OGLE
Ube Machinery Inc., Ann Arbor, Mich., rolled out its new Servomax line of large tonnage machines, available in a toggle clamp design (Servomax US) with forces from 1,000 to 2,500 tons, and in two-platen configurations (Servomax UU II) from 2,750 to 7,000 tons. The unit has closed-loop pressure control and a multi-servomotor gear pump drive that pares energy requirements by 70 percent compared to traditional hydraulic machines, while improving repeatability. A Servomax 1,000-ton unit, exhibited for the first time at NPE, operated in a four-second dry cycle time, says Dave Bernardi, senior sales and marketing manager.
Tech Bole USA, Franklin, Ohio, the U.S. and Canadian distributor for Ningbo Shuangma Machinery Industry Co. Ltd., Ningbo, China, debuted the Bole EK servo-hydraulic double-toggle line. The Bole EK series, ranging from 160 tons to 2,100 tons, is manufactured with a patented central clamping double-toggle design whereby the opening stroke has no relationship to the distance between pivots of the links, so that the force that focuses on the platen is parallel. The out curve toggle mold opening design allows larger molds that require an increased opening stroke of 10 to 20 percent to be installed without platen or mold deformation during injection, says Robert Jergens, sales manager.
Features include high quality hydraulic/servo pump technology that delivers energy savings between 30 and 80 percent, while the overall machine design helps to reduce material consumption by 2 to 5 percent for 80 percent of the molds used. A 500-ton BL500EK was shown at NPE.
GLUCO OFFERS TWO-PLATEN PRESSES
FROM CHEN HSONG
Gluco Inc., Jenison, Mich., the North American representative for injection molding machinery maker Chen Hsong Machinery Co. Ltd., Hong Kong, now offers the Supermaster TP line of two-platen servo-driven presses, which are available in clamping forces of 700 to 6,500 tons. The line features an additional temperature control zone for feeding, a nozzle tip that can be moved by as much as 300mm beyond the fixed platen, and platen and knock-out patterns that conform to SPI standards. The SVP/2 power pack combines a hydraulic gear pump with a high precision servo motor and proprietary servo drive, which allows for faster clamp up speeds.
Mikell Knights, senior correspondent
Contact:
Absolute Haitian Corp., 508-459-5372, www.absolutehaitian.comEngel Machinery Inc., 717-764-6818, www.engelglobal.com/usGluco Inc., 616-457-1212, www.gluco.comHPM North American Corp., 740-382-5600, www.hpmmachinery.comKraussMaffei Group USA, 859-283-0200, www.kraussmaffei.comNiigata Machine Techno Co. Ltd., 630-875-0202, www.niigata-us.comUbe Machinery Inc., 734-741-7000, www.ubemachinery.comTech Bole USA, 937-475-7797, www.techboleusa.com
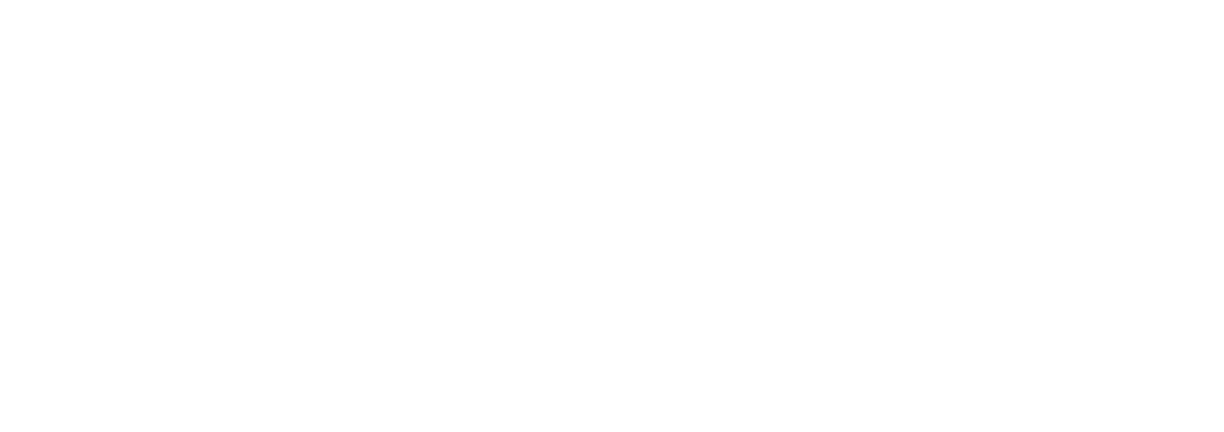