Blow molding, which produces everything from tiny bottles to large industrial and automotive components, is a relatively mature process, but exhibitors at NPE proved that they were not resting on their laurels.
Incremental improvements were pursued with vigor in nearly every conceivable category: all-electric machines, higher speed, lower energy consumption, ease of maintenance, rapid mold changeovers, simpler controls, materials flexibility and training.
This report emphasizes the blow molding machine itself. Future coverage will put greater focus on machine controls, blow molds, preforms, hot-runner systems, product handling systems, and retrofits.
Electric machines
and extrusion blow machines
Bekum America Corp., Kautex Machines Inc., and Meccanoplastica Srl represented the all-electric part of the spectrum, and other exhibitors showed partially electric, or electric/hydraulic hybrid machines.
The first Bekum U.S.-manufactured Eblow 607D, the all-electric version of the earlier Hyblow 607D, debuted at NPE. Martin Stark, Bekum America Corp. chairman, told Plastics Machinery Magazine that the Williamston, Mich., company has had good experience in building its machines in the United States and is committed to continuing to do so.
The all-electric version maintains the direct mold closing system with the patented C-frame system, using no toggles or cantilevers. This allows for high-tonnage, variable mold-opening control and direct clamping-force control. The Eblow 607D is an extension of Bekum's 07 range of machinery, which includes both hydraulic- and electric-driven variants. The double-station Eblow 607D machine produced twin-parison 10-liter containers from a sugar-cane-based "green HDPE" with full automation.
Historically, all-electric, shuttle-type blow molding machinery designs were geared toward simple bottle production applications utilizing lighter clamp tonnage closing systems, says Bekum's Gary Carr. The Eblow 607D, however, with a mold width of 700mm, mold daylight of 380mm, and a closing force of 27 tons, can produce large handleware bottles with extensive flash-removal requirements.
Several mechanical characteristics give rise to the effectiveness of the machine. With the C-frame closing system, the mold guidance is isolated from the closing forces, yielding precise mold guidance, high tonnage with uniform clamping force distribution, and, ultimately, extended mold longevity. Also provided by this direct-acting closing system are the benefits of variable mold stroke capability for differing mold thicknesses, reduction of opening stroke for cycle time optimization, and reduced maintenance requirements due to the elimination of complex toggle or lever-based closing systems as commonly associated with servo-actuated clamps.
Kautex Machines Inc., North Branch, N.J., which makes extrusion blow molding machinery, said the all-electric KBB machine displayed at NPE was not previously shown in the United States, but had its European introduction at K 2013 in Düsseldorf, Germany. Kautex said it wants to focus attention on sustainable production solutions for the packaging market.
A KBB60D machine with a 2-by-12 head configuration demonstrated the production of 24 milliliter bottles for the hotel industry. The all-electric KBB machines feature short cycle times and low energy costs. Quick change systems allow fast product changeovers and reduced downtime. These electric machines also meet regulatory requirements for cosmetic and food products.
Meccanoplastica, Florence, Italy, which is represented by Kautex in the U.S., also exhibited with Kautex. The company showed its Jet120 machines in action, representing its portfolio of all-electric machines. This effectively adds injection and stretch blow molding machinery to the Kautex portfolio.
Tech-Long Inc., Commerce, Calif., introduced the G5, a new generation of rotary stretch blow molding machinery. The G5 operates with 6 to 32 cavities, delivering outputs of up to 2,400 PET bottles per hour, while reducing energy use by 10 to 15 percent compared to previous machines. Improvements in machine speed result from the use of servomotors instead of pneumatic stretch rods and an integrated gripper system for faster bottle discharge from the molds. Energy consumption is also reduced by using an independently controlled heater and an enhanced air circulating system.
Six valves are used for pre-blow, second blow, main blow, first cycle, second cycle and air exhaust. The machine requires no low-pressure compressed air. Further enhancements include improved linkage between the base and side mold, which increases stability and reduces vibration and noise. Mechanical seals replace previously used pneumatic seals, reducing air exhaust noise from 92 to 83 decibels.
Wilmington Machinery Inc., Wilmington, N.C., a builder of high-capacity rotary extrusion blow molding machines, introduced an in-line, multi-clamp intermittent reciprocating blow molder. The machine is for medium-volume production of industrial, agricultural, and other forms of rigid packaging. It can also be used for toys, automotive parts and other industrial products.
The machines produce medium- and heavy-wall parts at rates of up to 600 pieces an hour. Models are available for both monolayer and multi-layer products. The Wilmington in-line machines are single-parison for precise and repeatable moldings. Cycle times meet or exceed those obtained by other technologies such as shuttles, long strokes, conventional reciprocating and others, the company says. The combination of single-parison and parison programming contributes to the ability to blow mold high-quality parts.
Graham Engineering Corp., York, Pa., launched its Revolution MVP rotary wheel, the next generation of the flagship Graham rotary wheel extrusion blow molding technology.
It features a new modular clamp design as well as a variable pitch option to allow a range of package sizes to be manufactured on a single platform. The modular clamp enables offline maintenance, repair, or replacement of a single clamp station to minimize downtime.
The accumulator head allows rapid color or material changeover. The spiral flow diverter head enables it to be lifted for easy cleaning. This allows color or material changeover to take place within one hour, saving material versus conventional changeover, which requires multiple, large shots, as well as valuable production time.
R&B Plastics Machinery LLC, Saline, Mich., launched the MAX mechanical wheel extrusion blow molding machine which it says is intended to meet the packaging industry's demand for high-volume applications. The system allows for the use of up to four parisons, according to Dave Corson, director of sales and marketing. The standard configuration of the machine has 16 stations and the ability to accommodate a range of mold lengths and widths.
Milacron LLC's M-300 PET system marks the company's re-entry to the preform molding market it left in the mid 1990s. It is a new servo-hydraulic system that contains Milacron's own machines, clamps, injection unit, end-of-arm tooling, hot runner, mold and robots. It operates with Milacron's preform tooling as well as legacy molds from other mold makers.
The M-PET 300 is based on the Ferromatik toggle clamp and newly designed two-stage injection units. The machine and post-mold cooling is driven by servo motors with hydraulics used only for ejection and injection.
The Milacron Uniloy IB 199-3 high-volume injection blow molding turnkey production cell includes a complete line of three-station injection blow systems with clamp forces from 49.5 to over 208 tons. Producing small to medium-size containers, the injection-blow process can use a wide variety of resins. Finished containers can be produced from 2 milliliters to 2 liters with precise neck finishes for child-resistant and tamperproof containers.
The injection blow process is scrap-free, matching the needs of pharmaceutical, medical, and food industries. Milacron, Uniloy's parent company, also can provide a kit to produce bacteria-free containers with high clean-room standards. Highlights of the system are the hybrid E-drive extruder, and the Mold-Masters Axiom hot-runner with iFlow technology.
Nissei ASB, Atlanta, exhibited the ASB-12M, which it described as a small, one-step, versatile injection stretch blow molding machine with servo-driven hydraulic pumps. The ASB-12M is an upgraded model of the ASB-50MB. The ASB-12M was demonstrated molding 20-ounce reusable and hot-fillable copolyester sports bottles with 50mm necks. A hydraulic pump driven by a servo motor has some of the advantages of both electric and hydraulic technology.
The machine reduces energy consumption by about 40 percent compared to the ASB-50MBv3. Noise and vibration also are reduced.
The Combox FC1 F12C6/720 from Serac Inc., Carol Stream, Ill., integrates an injection blow molding machine with a filler and a capper.
During NPE, Serac held live demos so attendees could view the process from preform through final product - a blown bottle filled and capped. The company has targeted this system toward high value-added products with medium size production runs.
Serac is a relative newcomer to blow molding machines, but comes to the field with an extensive history of loading and sealing existing blow molded bottles.
Merle R. Snyder, senior correspondent
Contact:
Bekum America Corp., 517-655-4331, www.bekumamerica.comGraham Engineering Corp., 717-848-3755, www.grahamengineering.comKautex Machines Inc. (and Meccanoplastica, represented by Kautex)908-252-9350, www.kautex-group.comMilacron Uniloy, 513-536-2000, www.milacron.comNissei ASB Co., 404-699-7755, www.nissei-asbus.comR&B Plastics Machinery LLC, 734-429-9421, www.rbplasticsmachinery.comSerac Inc., 630-510-9343, www.serac-usa.comTech-Long Inc., 562-928-7755, www.tech-longusa.comWilmington Machinery Inc., 910-452-5090, www.wilmingtonmachinery.com
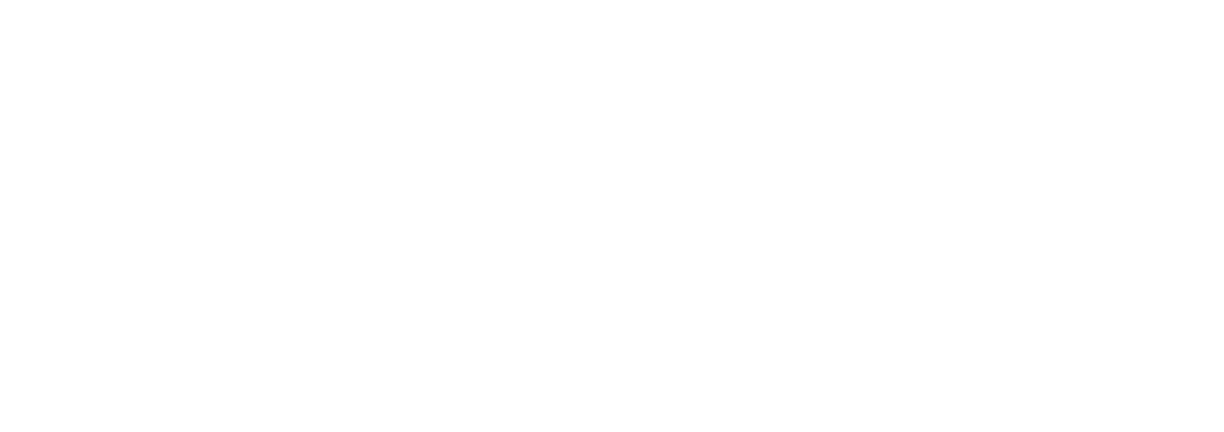