One interesting development at NPE was how many equipment suppliers were just as ready to talk about retrofitting or rebuilding existing extrusion systems and individual machines as they were to talk about their latest gear.
Several extrusion suppliers displayed rebuilt machinery in their NPE booths right alongside their newest machinery. However, you might not have thought you were looking at rebuilt machines. That is because the rebuilt machines look like new, current-generation equipment. Suppliers say that when rebuilt machines are equipped with current technology, they perform at or close to the level of a newer machine, and definitely better than when the machine was originally built.
Considering how far plastics production technology—extrusion in particular—has evolved and advanced over the last few decades, that's understandable. Take a well-built machine from the late 1990s, substitute servomotors for old drives, and then equip it with today's electronics and a powerful control system with a touchscreen human-machine interface (HMI). You have a rebuilt machine that is better than when it was new.
A key issue, of course, is the value proposition. Although the cost differential between a rebuilt and a new machine varies with the type of machine, and for a retrofit it depends on how many components of a machine or production system are replaced with newer technology, the suppliers say a rebuild and retrofit virtually always costs significantly less than buying a new machine or new line.
Javeed Buch, vice president service/multiwall technology of global flexible packaging systems supplier Windmöller & Hölscher Corp., Lincoln, R.I., says retrofitting blown film lines is a growing market for W&H. It was always there, he says, but was a bit of a stepchild. "Now retrofitting is a distinct department in the company and has been for over six years," he says, adding that until recently the company has been concentrating on its large installed base of blown film lines.
Buch says that being a systems company, W&H thinks in terms of improving a total system, extending its productive life and improving the quality and quantity of its output. Therefore, it wants to retrofit the older line with the most advanced W&H technology. "That way," says Buch, "when the processor invests in a new system, the technology will be the same." He says W&H's system-thinking fits well with the modular nature of blown film lines, allowing them to do only what is needed.
W&H retrofitted a blown film line—not one of its own—that was having film gauge and width variations. The problem was resin feed separation and the solution was to use new gravimetric metering technology that improves accuracy, especially when feeding small quantities. On another non-W&H line the company used its Procontrol TS (touch screen) control system to combine the functions of several operator terminals into one, which helps operators avoid errors and lets them consistently produce better products.
Blown film system supplier Gloucester Engineering Co. Inc., Gloucester, Mass., which provides an extensive array of retrofitting and rebuilding services, alerted show attendees to that fact with a new-looking rebuilt bag machine on the aisle side of its booth. The machine is part of a multiple rebuild order from a customer, but was not one of the more than 5,000 GEC bag machines out in the world. Post-rebuild, however, it has a GEC engineering serial plate and the warranty coverage of a new machine.
Laurent Cros, president of GEC's Aftermarket and Service Division, says the bag machine's upgrade included, among other things, replacing hydraulic drives with servo technology, adding a touchscreen HMI and rebuilding it to as-new condition, which can be seen in the "after" photo. Its output is now 10 to 15 percent higher than originally. GEC also rebuilds dies, rotators, gearboxes, winders and other components, both its own and ones from other manufacturers.
GEC says that since many machines in its installed base of blown film systems can operate at full capacity for 30 or more years, it is rebuilding many components to extend those life spans. It will also retrofit those older lines with its current technology, such as the new ExtruTouch control system and the UltraCool III bubble cooling technology. Bill Hellmuth, product group director for blown film at GEC, says retrofit costs vary but a rule of thumb is that performance of the existing line can be increased up to 20 percent for about half the cost of a new line.
Extrusion and converting technology supplier Davis-Standard LLC, Pawcatuck, Conn., had a rebuilt 60mm Thermatic extruder in its booth, and it looked as new as the actual new extruders near it. Between the before and after photos, extruder retrofits can include replacing the barrel, feed section, screw and breaker plate, new controls, length-to-diameter conversions and more.
Davis-Standard was also showing an upgrade of its older CMR control to an Integrator Pro, the system that replaced it, and an upgrade of DC to AC drive conversion packages that can yield energy savings of up to 20 percent. The company will also rebuild and upgrade other process controls, gear cases, dies, heads and more at a fraction of the cost of full replacement.
Rob Neilley, senior correspondent
Contact:
Davis-Standard LLC, 860-599-1010, www.davis-standard.comGloucester Engineering Co. Inc., 978-282-9383, www.gloucesterengineering.comWindmöller & Hölscher Corp., 401-333-2770, www.whcorp.com
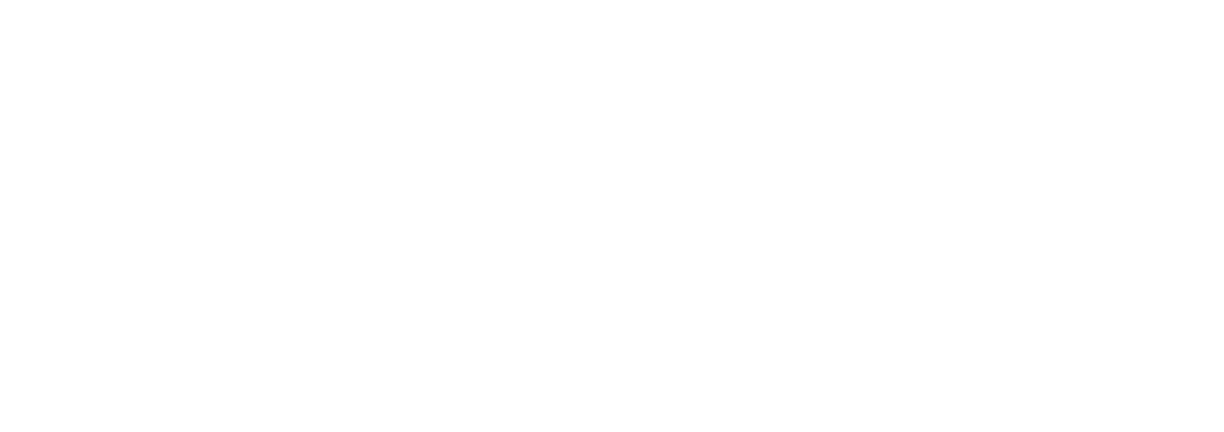