Special Report: Priamus uses tighter monitoring to banish faulty parts
A primary question that process and production monitoring answers is: Why, despite the highest levels of quality involved in the manufacturing of the materials, machinery and molds, are bad parts still being produced?
"The dynamic nature of the molding process, as well as numerous variables that are non-constant influences can change a good part to a bad part," says Marcel Fenner, technical manager at Priamus System Technologies LLC, Brunswick, Ohio.
These influences can range from differing material batches to environmental conditions in the plant, seasonally or daily, says Fenner.
"For this purpose, the molding process needs a quality assurance system to recognize these fluctuations, a first step in process compensation," says Fenner.
DATA COLLECTION AND PRESENTATION
Priamus developed a data export function last year for use with its FillControl product line. For the first time, it allows molders to select a range of molding cycles and displays an overlaying of those cycles, as a simple and direct way to determine process stability.
All of the measuring data is captured in real time, from the quality or state of the devices and the controllers used as well as their actual and set values.
Generic trends relating to melt viscosity, clamping movement or switchover from pack to hold can be discerned through analysis of the overlay of the data points gathered from cycle to cycle. Users can select a reference curve from the selected cycles being compared by overlay, or view curves stored in memory. Users can capture data from specific points in the process. Users select the number of cycles to be compared.
The data export function can store all the details in CSV or Excel format for process analysis. It is an additional feature of the Priamus FillControl system for monitoring and controlling the injection molding process.
Priamus also has developed a new user-management production-monitoring tool designed to prevent unauthorized access and changing of an optimized process. User levels are given to different personnel, only allowing those with clearance to make changes to the process or production. The system keeps a detailed log of all changes. A user database can be generated on any FillControl system. A database created from data collection from one project is accessible only to specific groups of personnel, allowing multiple proprietary projects to be run at different times with confidentiality using the same press. Accessibility can be configured for individual applications, says Fenner.
Priamus also updated the event log function last year that documents user activity. The traceability of personnel logged in is a step important to more and more medical molders, says Fenner.
A cavity-pressure sensor launched last year that is designed with a harder sensor front for long use when abrasive, highly filled and chemically corrosive plastic materials are being processed is now offered on cavity-pressure sensors from Priamus, as well as cavity-temperature sensors. The sensor front is comprised of a patent-pending ceramic and metal injection shielding.
Alternative methods to extend sensor life, such as titanium nitride or chromed surfaces, were not able to withstand the process environment, or after application the sensor front was not fulfilling the very tight dimensions needed for installing the sensor tip into the bore, says Fenner.
MEASURE YOUR VOLTAGE
Priamus developed a voltage module a year ago that allows the molder to link it to machine signals to determine whether the machine is doing what it should do and then compare it to what is occurring in the mold. "The voltage module allows you to measure hydraulic pressure, screw speed or screw position, any force. Then you can compare it to a pressure curve or a temperature curve," says Fenner.
The functionality of the voltage module proved to be a huge benefit for a U.S. molder that beta tested the module. The molder is developing in-house specially configured vertical injection molding presses for an insert-molded optical part for an automotive application. "The molder was having trouble validating if critical functions of the specialized injection machines occurred consistently cycle to cycle," says Fenner.
The voltage module helped the molder determine if factors such as clamping pressure arrived when they were supposed to, or if the signal for switchover to holding pressure is ideal. The voltage module relates a voltage signal into a position, then the molder compares it to the pressure and temperature curves generated in each tool cavity. Part quality and process consistency are further linked.
Mikell Knights, senior correspondent
Contact:
Priamus System Technologies LLC,
877-774-2687, www.priamus.com
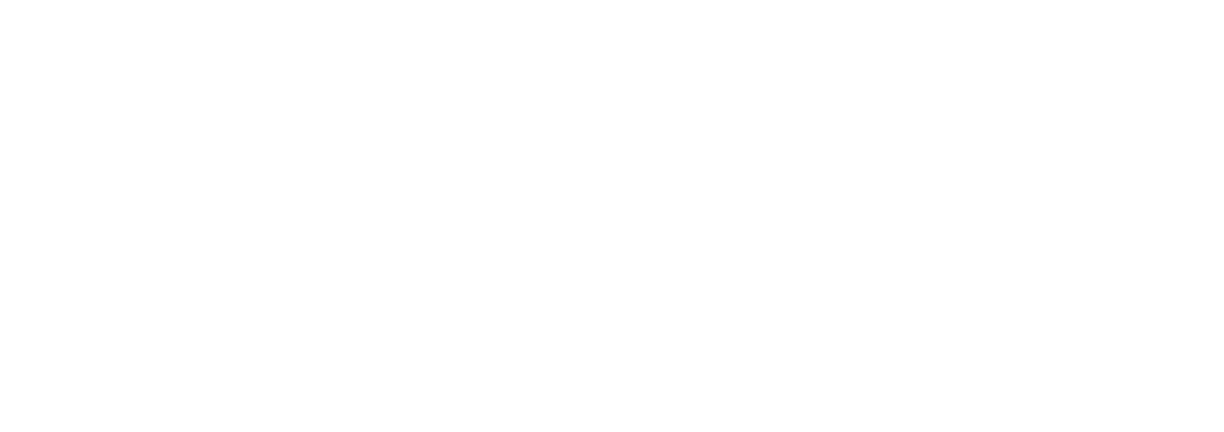