Hardware developments from RJG (NPE Booth W1386) include the LYNX embedded sensor plate technology. Lynx digital sensors can now be built into the ejector plate for a clean, simple and robust installation. The sensor electronics and head are entirely buried and sealed, eliminating outside cabling and most of the causes of damage and problems. A single cable connection from the mold to the eDART can handle up to 30 sensors. When the tool is hung in the press all sensors are fully functional. RJG can preconfigure sensor names and pin sizes for easy setup. During mold maintenance, there is no need for removal and replacement of sensors and wires. The whole plate can be set aside while working on ejector pins.
Another solution for multi-cavity applications is the multichannel strain-gage system. It simplifies the installation of strain-gage cavity-pressure sensors in high cavitation molds. The adapter greatly decreases the footprint on the mold needed for multi-sensor installations. By moving the multichannel adapter electronics off the mold, this system increases reliability. Because the adapter can be used on multiple molds, it also reduces sensor cost. The multi-channel cavity-pressure solution, unique to RJG, allows injection molders to connect up to eight strain-gage sensors to one connection point on the mold. The Lynx four- and eight-channel piezo adapters provide users of piezoelectric cavity-pressure sensors with a convenient, simple interface to four- and eight-channel piezoelectric systems. This device will identify the mold when used with RJG's piezoelectric connector with Mold ID capability. Multiple devices can be daisy chained for molds with multiple connectors to utilize the eDART System's mold-identifying and job-startup features. Soon to be released: a smaller version of the adapter.
RJG's Version 10 software provides a much more user-friendly experience. The new software has touch screen functionality. New display screens let a molder view the status of the machine on the screen from 10 to 20 feet away. A single display screen shows the number of rejects made since the job started, the type of reject, and the number of rejects made within the last 20 to 40 shots. "The simplicity of the screens drives awareness of situations happening on the molding floor, allowing for better communication with team members that are off-site," says Chris Nomura, RJG consultant/trainer. RJG designed the interface to be more intuitive, requiring less training to understand how it works and what the data is showing.
IMPROVING SENSOR-TIVITY
RJG has developed several new products that will enhance the monitoring and control capabilities of the eDART System. A new strain gage sensor can measure mold deflection at different points in the molding cycle. "We can now see if the mold is opening during injection, which can be a cause of bad parts, including flash," says Nomura.
RJG offers two sensor installation choices, behind an ejector pin or a flush-mount sensor that can be machined to sit flush with the mold cavity. Pressure sensors are typically placed behind core or ejector pins, where they can monitor and leave little or no witness marks in the part. RJG's flush-mount sensors can be positioned directly on the cavity surface of the mold. "The sensors are installed flush to the contact surface of the mold. Cavity detail can be machined into the surface of the sensor to blend in with the mold," says Nomura.
Flush-mount sensors can be placed against a complex section, or in a mold area where a short shot might occur, or in a location where a cavity ID is, leaving no extra witness lines. Flush-mount temperature sensors are available with pin sizes down to 1mm. The flexibility to locate the sensor in the mold opens it up to use in tools that have a stripper plate rather than ejector pins, or for use in molds where only the absolute minimum witness line is acceptable.
The proliferation of servo drives and wireless devices on the shop floor increases the possibility of electromagnetic interference with monitoring systems. To reduce that risk, RJG now encases its machine monitoring modules in a more robust metal enclosure. The modules also feature shielded cables, making installation and troubleshooting easier while increasing immunity to interference. RJG's modules feature DIN rail mounting and easy-to-read status LEDs.
BETTER DATA HANDLING
RJG's eDART system manager is a virtual tool that provides a simple interface to access, support, and make adjustments to the jobs running on the plant floor. Users can configure the software screen to make a visual copy of the machines on the plant floor. This interactive screen allows users to make adjustments to any of the eDARTs networked on their plant floor from computers, phones, and other devices with access to the internet. Viewing overall machine status and part quality, arranging machines into groups or into layouts that match the facility, and receiving notifications of critical changes are just a few features of the new Web-based interface. Output reports of various types can be produced, saved and printed.
RJG is introducing a new sensor tester for tooling shops that will make it easier to determine if a sensor is installed correctly or damaged. The toolroom sensor tester provides tool builders and molders alike with a way to test up to 30 in-mold sensors at one time. Testing sensors prior to putting the mold into production can save a considerable amount of lost production and troubleshooting time. It can tell if a sensor is damaged, not responding to pressure variations, or if it is not communicating. "This will help spot potential problems before hanging the tool," says Nomura.
Mikell Knights, senior correspondent
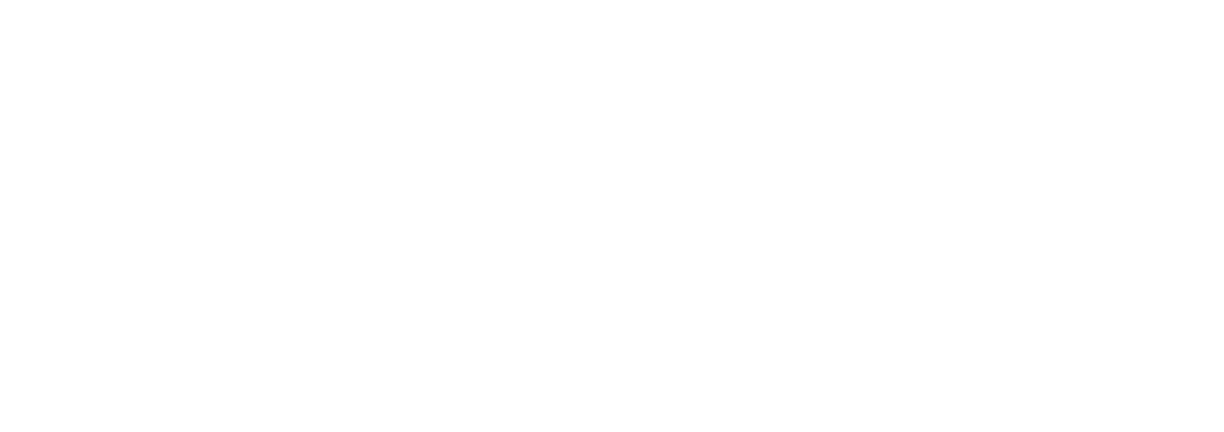