Equipment suppliers and plastics processors in February used the Plastec West and Medical Design & Manufacturing West shows in Anaheim, Calif., to tout their latest capabilities to a predominantly Western audience. Plastec West and MD&M West were co-located with six other shows, all with some degree of overlapping interest with the world of plastics processing. Here are some of the highlights.
3-D creates molds, not just parts
Diversified Plastics Inc., Minneapolis, saved 88 percent in prototype part development costs and 80 percent in development time for medical device maker Coloplast A/S, Humlebæk, Denmark, by using 3-D additive manufacturing to create injection mold components. Coloplast needed to produce prototype medical device parts from injection moldable TPE to accurately evaluate geometry, design and performance. Coloplast wanted to evaluate the feel of its new device and to analyze the durometer before proceeding to production.
Diversified recommended making the preproduction mold using additive manufacturing to save time and money compared to a soft-steel prototype mold. Using its Objet PolyJet printer from Stratasys Ltd., Eden Prairie, Minn., Diversified Plastics produced a highly accurate injection mold for creating prototype parts.
Once Coloplast's tool design file was prepared and loaded into the printer, it took 11 hours to build both halves of the mold and center core. Diversified's tooling department inserted the printed mold components into a mold base and the prototype thermoplastic parts were injection molded. The entire process, from initial discussions through mold production to final prototype, took just five business days.
Diversified also said it has added a 310-ton electric injection molding press from Toshiba Machine Co., Elk Grove Village, Ill., to its production facility. This machine replaces a similarly sized hydraulic press and is the fourth electric press the company has added in recent years.
"The new machine gives us the ability to produce larger parts than our other electric presses and it can operate in a clean or white room," said Mark Gremmels, director of operations at Diversified Plastics.
"You save close to half the cost of electricity of a similarly sized hydraulic press," Gremmels said. "Our new press requires an electrical load of 43 amps while the hydraulic equivalent would need about 75 amps of power. And, since there is no hydraulic oil to cool in an electric press, no oil cooling units are necessary. On a hydraulic press of this size about 6 [thermal] tons of cooling would be necessary, but with the electric press there is zero cooling," he said.
LSR innovation showcased
Silcotech North America, Bolton, Ontario, a molder specializing in liquid injection molding technologies, showcased its system with new Dow Corning technology for liquid silicone rubber.
Through a collaboration with Dow Corning, Silcotech developed a new multi-shot processing system capable of simultaneously molding nine discrete substrates or shapes incorporating a broad range of durometers, textures and colors, using Dow Corning's QP1 silicone elastomer materials.
Roger Hendrick, application engineer at Dow Corning Healthcare, said that close collaboration has enabled high-output molding of intricate medical device designs.
Silcotech's multi-shot silicone system simultaneously molds nine discrete shapes, while maintaining costs comparable to a single-shot system. Silcotech's technology minimizes processing costs due to fast cure and easy processing. Silcotech produced multi-durometer cellphone covers at its booth to demonstrate the technology, identifying different grades of material by using nine different colors. The company molded the LSR cellphone covers on an injection press from Arburg Inc., Newington, Conn.
The potential combinations for designers is nearly infinite, says Michael Maloney, president of Silcotech.
Maloney told PMM that the multi-shot process is the result of proprietary knowledge, and that he does not plan to apply for a patent, as that would require disclosing too much information to Silcotech competitors. Maloney says he intends to operate Silcotech as a custom molder using the technology, and does not intend to sell the equipment or technology to other molders.
High-speed medical packaging
GW Plastics Inc., Bethel, Vt., has entered the high-speed medical packaging market and anticipates strong growth in its medical device business. GW has added two 240-ton Netstal injection molding machines to support a major award of business by a Fortune 500 customer and expand its capabilities in the high-volume disposable medical device market. GW also made recent multimillion-dollar expansions in its Tucson, Ariz., and Dongguan, China, facilities to support this growth. GW is a custom molder that also performs other manufacturing services, including quality control via metrology as well as molded product assembly.
John Silvia, VP of manufacturing engineering and Bethel plant manager, says that the competitive nature of the high-volume medical packaging market requires manufacturers to run multiple-cavity molds at cycle times of less than seven seconds. The new machines will operate in a Class 8 clean room. Production will include the installation of high-speed robotics, end-of-arm tooling and equipment for parts handling, automated packaging and metrology.
Medical disposables
Mack Molding, Arlington, Vt., and its medical products group MackMedical are investing $2 million to expand clean room molding and assembly capacity to handle significant growth in the medical disposables market, according to President Jeff Somple.
Somple said that "while we've been involved in orthopedic disposables for some time, this marks our first foray into high-volume, single-use components for a Class III medical device. It's a critical step that will open up a whole new market sector for us."
To accommodate the work, Mack is building its third molding and assembly clean room at its headquarters plant in Arlington, which will house four electric presses from JSW Plastics Machinery Inc., Corona, Calif. This brings Mack's clean room press total to 11. The 3,500-square-foot clean room will be certified to meet Class 100,000 (ISO Class 8) standards. It is scheduled to be certified by April 1, at which time Mack will begin validation runs.
"We'll be shipping parts by the end of April," said plant manager Rich Hornby. The clean room will include space for conveying parts from an adjacent soft-walled clean room that will house a robotically automated 500-ton press. Servo-controlled radio frequency and ultrasonic welding systems will be included, as well as automated particulate, temperature and humidity monitoring.
Mack is adding four electric injection presses, including two 44-ton vertical machines and 60-ton and 199-ton horizontal presses. From JSW's Advanced Series, they feature a 62-microsecond servo control circuit. The presses will be vacuum-fed by a modular bank of dryers located just outside the clean room.
In addition to this investment, Mack has two other Class 100,000 clean rooms: a molding clean room with six electric presses, and an assembly clean room that is used for non-sterile packaging.
Robotics suppliers focus on
controls, high-speed part handling
Fanuc America Corp., Rochester Hills, Mich., demonstrated high-speed grouping of parts with its intelligent M-1iA parallel-link Genkotsu robot, and LR Mate 200iD mini-robot during the Anaheim shows.
The new M-1iA/0.5SL long-arm, four-axis robot used iRVision to pick random parts from a conveyor and arrange them in defined group patterns or lanes using iRPickTool software. Next, a Fanuc LR Mate 200iD mini-robot picked the entire group pattern and placed it on an outbound conveyor. The parts were circulated and the process repeated.
Fanuc's iRPickTool software simplifies setup for line-tracking systems and minimizes programming for customers with picking applications. The M-1iA intelligent Genkotsu robot is a lightweight and compact parallel-link robot designed for small part handling, high-speed picking, packing, kitting, and assembly applications. Fanuc said the robots are very easy to integrate into production lines, which minimizes downtime and maximizes output. The M-1iA is lightweight at about 26 pounds for a three-axis model; about 31 pounds for a four-axis model; and 37.5 pounds for a six-axis model.
More news
• Denso International America Inc., Southfield, Mich., has updated its West Coast training center in Long Beach, Calif., with new learning equipment and more course offerings. Classes cover the company's new RC8 control, vision hardware infrastructure for wireless operation, and workstations with dedicated roots and controls for hands-on training. Classes are still offered on the RC7M controller. The redesigned training center also offers online video training options, including real-time classes via remote webcast.
In addition to the new control, Denso's product line includes four-axis, five-axis, and six-axis articulated industrial robots for payloads up to 44 pounds. Denso provides clean room and aseptic robotics as well as standard industrial models.
• Aluminum Mould Set Ltd. Co. (Almo), London, exhibiting at Anaheim with DMS Inc., Oldcastle, Ontario, introduced an in-mold screw-tightening device. A range of standard worm-gear elements with a hexagonal key linking it to the cap screw secures the inserts in the cavity to the mold. To turn the elements, a detachable worm tool can be used at 90 degrees to the screw, enabling turning the screw for tightening or releasing while the mold is still mounted on the machine. The elements are precision machined and hobbed from phosphor bronze, and have a very good coefficient of friction to support them while installed between the steel mold plates. The units are small and allow high torque transfer by the worm tool wrench.
Merle R. Snyder, senior correspondent
Contact:
Aluminum Mould Set Ltd. Co.
44-20-3490-4693, www.almo.uk.com
Denso International America Inc.,
888-476-2689, www.densorobotics.com
Diversified Plastics Inc.,
763-424-2525, www.divplast.com
Fanuc America Corp.,
888-326-8287, www.fanucamerica.com
GW Plastics Inc.,
802-234-9941, www.gwplastics.com
Mack Molding,
802-375-2511, www.mack.com
Silcotech North America,
905-857-9998, www.silcotech.com
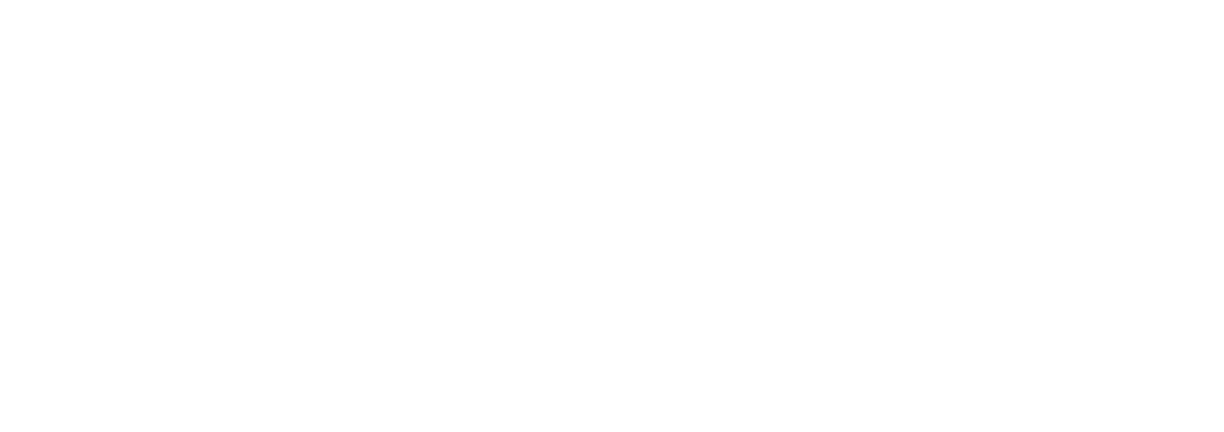