Thermoforming machinery makers hit the show floor at NPE with systems that boost productivity and consume less material. Companies have focused on reducing energy use and cycle times for lab style, roll-fed and cut-sheet pressure or vacuum forming machines.
TURNING UP PRODUCTIVITY
OMV Machinery srl, Verona, Italy, (represented in the United States by Polytype America Corp., Mahwah, N.J.), introduced a revolving mold (RM) thermoforming machine concept designed for high-output PP cup forming.
OMV designed its RM77 unit by completely rethinking an older, shuttle-style OMV machine, says Antonio Staffoni, CEO and president of OMV, which is a unit of Wifag-Polytype Holding AG, Fribourg, Switzerland.
"The design of the shuttle OMV model featured female and male mold halves that shifted linearly, keeping the material in contact with the tooling longer to enhance part cooling and final part quality. However, an acceleration/deceleration step was required to position the mold, which required time. The idea is to incorporate the mold in a block-style device that rotates instead of moving the mold halves linearly," says Staffoni.
The RM model utilizes a mold comprised of three semi-molds rather than two mold halves. The male half operates at full cycling speed (start position to end position and back), while the two female halves complete one circuit every two cycles of the male half. The formed material remains in the cavity for an additional cycle, which improves part quality, while having two cavity sets allows for the increase in production speed, says Staffoni. OMV integrated a simple stacking and part handling system into the new machine.
The RM77 unit, having a large forming area and a very high cycle speed, can produce 71mm-diameter PP drinking cups at a rate of 55 cycles per minute, or 175,000 cups per hour, says Staffoni. The production speeds achieved are a significant development when molding with PP. "It is the first machine to break 50 cycles per minute with PP cups," says Staffoni. The first RM77 unit is sold and will be delivered to a European customer at year's end.
LAB THERMOFORMING IN ZERO ATMOSPHERE
Zed Industries Inc., Vandalia, Ohio, launched an upgraded version of its L-3MA lab unit designed for trials of specialized, non-petroleum-based resins or multi-layer structures with varying softening temperatures, and for pre-production testing of new molds.
The company developed the lab scale unit in 2012 for sheet forming trials, adding servo control for all platen motions, clamp frame and third-motion plug actions, as well as a more responsive and precise PLC and tighter, full-temperature control in this new version, according to Peter Zelnick, CEO.
A key feature of the upgraded L-3MA form and trim-in-place, shuttle mold lab unit is the incorporation of "tunable" infrared heater elements that can be set to the electromagnetic absorption spectrum of the resin. Conventional quartz heaters tend to generate a broad spectral band of electromagnetic radiation, some of which is absorbed by the material, while other wavelengths are reflected off of the material surface into the forming area.
"Conventional heating elements need to run at high temperatures to deliver the desired wavelength, and the majority of that radiated energy is not at the wavelength desired. Much of the emitted radiation is either transmitted through the sheet, reflected or heats the air, not absorbed by the sheet," says Zelnick. To achieve a radiation wavelength of 1.3 micrometer for PP, a quartz element would operate at 1,100 to 1,300 degrees Fahrenheit. The infrared heating element Zed utilizes (a proprietary type designed by Zed in collaboration with an unnamed firm) achieves the majority of the emissions in the desired absorption wavelength with minimal reflected or emitted radiation, operating at 600 degrees Fahrenheit, says Zelnick.
In addition, the lab unit incorporates Zed's cool blow system, which purges and replaces air in the pressure box during the forming step, and can create a vacuum that evacuates off-gases and reduces sheet heating by convection.
"After the plastic contacts the mold, cooling is dependent on the tool's ability to pull heat from the sheet to get it down to a demolding temperature. However, in traditional molding, air in the pressure box gets trapped and becomes hotter and hotter as the process continues, making the mold less effective in drawing heat away. Air evacuation and swapping helps get the material temperature down quickly," says Zelnick.
Zed has full temperature control in the pressure forming air. The unit can run hot air up to 700 degrees Fahrenheit, and cold air down to any desired set point, while delivering any pressure desired over the top of the thin sheet to achieve more than 100 psi of pressure. The precise machine controls allow a thermoformer to start with hot air then swap in cold air, or vice versa. This functionality results in what Zed calls modified or zero atmosphere control.
An adjustable clamp frame allows for the processing of materials in gauges from 2 mils to 0.5 inch. The L-3MA is used to determine processing conditions for a range of new or difficult-to-mold materials, including sugar-cane-based, fully biodegradable PET, polyesters derived from switch grass, or thin sheets of polyamide. Ideal processing conditions reached through testing with the lab unit can be saved on a thumb drive and uploaded to a production Zed unit.
TRIMMING CYCLE TIME DEAD SPOTS
Lyle Industries LLC, Beaverton, Mich., which exhibited at NPE with its partner Gabler Thermoform GmbH & Co. KG, Lübeck, Germany, demonstrated a new model added to its FM series of roll-fed, toggle thermoformers, upgraded with a new forming station design and related enhancements to reduce the amount of dead time in a cycle and raise productivity.
The new FM unit ushers in Lyle's new SS 454 forming station. The nomenclature stands for 'Super Servo' and features four servo drive motors and a 54-inch forming station, says Brian Crawford, Lyle GM. The platen and toggle movements are servo-controlled.
"The mechanism that drives toggle open and close has been upgraded to achieve faster opening and closing speeds by minimizing the time when the process is not on plastics," says Crawford. The FM unit has a stroke of 9 inches for both the top and bottom mold halves.
"Dry cycle speed with a traditional FM is approximately 41 cycles per minute with a tool installed. The new forming station delivers a dry cycle of 51 cycles per minute, driven by higher mold open and closing speed, which is about 20 percent better," says Crawford.
The opening and closing mechanisms of the toggle set are now driven from both sides of the machine rather than from one side, as is the case with earlier FM models.
"Forces generated by high-speed opening and closing of the mold can cause a side-to-side movement of the machine frame. Driving the mechanisms from both sides results in equal yet opposing forces that reduce vibration and movement of the station and the frame. Open/close actions are smoother, which reduces maintenance and extends the life for moving components on the machine," says Crawford.
The FM unit uses a new airflow control valve that provides higher airflow rates to enhance air evacuation from the mold, so that pressure and vacuum steps occur sooner. The higher air capacity minimizes non-productive time in the cycle, says Crawford. Lyle uses servo-driven roller screws rather than ball screws for plug plate actuation. Roller screws have a longer life cycle.
Other features include incorporation of the latest Mitsubishi 2015.1 PLC control system, and its virtual network computing remote server function that allows monitoring of the HMI from any tablet, smartphone or PC anywhere in the plant.
Lyle partners with Gabler for its in-line trimming equipment; Lyle produces off-line trimming equipment.
SHEET PUNCHING ACCURACY WITH LINEAR RAILS
Thermoforming Systems LLC, Union Gap, Wash., introduced the TSL Linear Rail 5.0 vertical press (LR5 VTS), made to pre-punch, pre-score or trim sheet up to 57 inches wide. The unit provides draw depth of 7.5 inches up and 5 inches down, handles tooling up to 4,000 pounds (2,000 pounds on the moving side) and delivers up to 45 tons of clamp tonnage, says Roger Moore, senior VP of sales.
"Linear rails, rather than standard round die post and bushing components, are employed for platen guidance, which improves the accuracy of tool movement, extending tooling life and trim press life," says Moore. Use of linear rail eliminates the 0.002 to 0.003 inch clearance required between the bushings when the round die post and bushing component are used, improving platen location. The linear rail is pre-loaded, hence it operates with virtually zero clearance. The 65mm/45mm linear rail and rail bearing system handles load carrying and precision platen location required in the trimming and punching of heavy-gauge plastics. This NPE marked TSL's first showing of its linear rail system, which it has had for about two years, says Moore.
The LR5 VTS pre-punch function punches holes in the base or side walls of ventilated containers such as berry baskets, or it can be used as a scoring press to create a tamper-evident container, says Moore. Pre-counted stacks of parts are evacuated from the trim tool by a vertical elevator then pushed onto a conveyor for delivery to a packer or automation system, reducing labor for retail count packages, says Moore.
Features include a push/pull system that controls the indexing of the sheet through the trim station. Four independently controlled 2.2-kilowatt servomotors each drive mechanisms that grip the corners of the sheet. The pushing action occurs pre-mold while the pulling action occurs simultaneously from a post-mold point, says Moore. The push/pull feature was launched on a horizontal trim press model at the previous NPE. This is its first use on TSL's vertical trim press.
TSL also discussed development of enhanced features within its machine control that aims to ease process setup and troubleshooting. The new machine control capabilities will be an option when integrated into the HMI of the control later this year. Installing different sensors, transducers and strain gauges mounted on the machine and in the tooling allows the upgraded machine control to provide feedback torque control, says Moore.
FORCE BALANCED FORMING STATION
The Dynamic Servo Inline thermoformer series from Monark Equipment Technologies Co., Auburn, Mich., highlighted a technology design update for the form station platen drive system, says Steven Clark, president.
The form-and-trim stations feature push button adjustment of the platen's closed daylight dimension. It is accomplished using pre-loaded head adjusting nuts and an AC variable speed drive that allows for adjustment ranging from 1 inch to 5 inches, says Clark. This approach eliminates the use of jam nuts, which can be difficult to tighten and can lead to premature wear when platen daylight is adjusted.
The design and construction of the form-and-trim stations are statically and dynamically balanced, where static balancing of the platens eliminates use of air-assist balance cylinders, providing energy savings, while dynamic balancing of the platens neutralizes the force required for acceleration/deceleration of the platen and tooling during production. Dynamic balancing is achieved through use of new counter-rotating, symmetrical platen drive assemblies that provide a balanced closing force that does not impose lateral forces on the platen guide posts, says Clark.
LARGER PRESS, HIGHER PACKAGING PRODUCTION
Kiefel Technologies Inc., Portsmouth, N.H., launched the Speedformer KMD 90 pressure former model, the largest in its KMD line of high-speed, roll-fed in-line thermoforming units. KMD 90 handles tools with a maximum dimension of 35 inches by 37 inches, and can handle sheet widths up to 36.4 inches in its 34-inch by 36-inch forming area, says Steven D. Hoenig, president and CEO of Brückner Group USA Inc., which owns Kiefel.
The larger forming area allows this KMD model to accommodate larger tooling designed for other domestic thermoforming units. "For processors with an older unit, this machine provides an opportunity to move their existing tooling into a higher performing machine," says Hoenig.
The new unit is manufactured for high-speed, high-output, low-waste processing of a wide range of materials, including PET, polylactic acid, crystalline PET, oriented PS, PP, PE and PVC grades. The incorporation of efficient black ceramic heating elements in the upper and lower heating stations provides fast sheet heating, and closed loop temperature control, says Hoenig.
Dry cycle speeds of 40 cycles per minute are achieved with the all-servo unit. It utilizes centric toggle-lever drives in the forming and cutting station and features an independent servo-plug drive for the upper and/or lower table.
"The third-motion plug assist option allows processors to downgauge the material uniformly by controlling the material at critical locations," says Hoenig. The unit generates 72.5 psi of pressure.
New machine models like the KMD 90 now use the Simotion touch screen control system from Siemens AG. A special teaching program configures all machine settings automatically, based on minimal input information from the operator, says Hoenig.
Other developments include a tool changing station placed between the forming and cutting station that handles both tool halves in one block, and a servo-driven part stacking station that can be configured as a down-stacker, offering an unloading height of 39 inches. The KMD 90 produced PET food trays at NPE and was sold to Display Pack Inc., Grand Rapids, Mich.
One KMD 90 is currently in production at a U.S. thermoformer, a second will be installed in April, and two other units have been ordered, says Hoenig.
VACUUM UNIT ADVANCES
Formech Inc., Chicago, launched its Series 2 HD automatic vacuum forming machine, created for prototyping, testing and production applications, says Nic Neath, head of sales. The sheet forming unit is offered in an HD686 Series 2 model with a 25.5-inch by 24.5-inch forming area, and the HD750 Series 2 model, with a 27.5-inch by 19.7-inch forming area. Both models provide 16 independently controlled zones of heating delivered by quartz heaters, and they handle sheet up to 0.25 inch.
Improvements to the line, first introduced in 2002, include the Formech Cycle View (FCV) control interface with a 10-inch high-resolution touch screen with an improved graphic user interface that displays machine cycle status and allows for machine monitoring from a remote location via an Ethernet connection. The unit also comes with pneumatic heater drives and a pneumatically powered clamping frame and pneumatically operated table with regulator, says Neath.
Formech also launched its new TF Series 2 automatic in-line thermoforming machines that process reel materials up to 1.8mm and sheet up to 0.25 inch. The TF686 Series 2 has a forming area and heating zone configuration similar to the HD686 unit, while the new TF750 Series 2 has a forming area and heating zones similar to the HD750 Series 2. The TF models deliver draw depth of 7.8 inches and have key features similar to the HD Series 2. The TF line also incorporates the new FCV interface, and produces products ranging from trays to automotive interiors. This is achieved by utilizing quality components such as Weintek HMI's, Becker vacuum pumps, and quick response quartz elements.
Mikell Knights, senior correspondent
Contact:
Formech Inc.,
312-396-4072, www.formech.com
Kiefel Technologies Inc./Brückner Group USA,
603-766-6350, www.brueckner-usa.com
Lyle Industries LLC,
989-435-7717, www.lyleindustries.com
Monark Equipment Technologies Co.,
989-662-7250, www.monark-equip.com
Polytype America Corp.,
201-995-1000, www.wifag-polytype.com
Thermoforming Systems LLC,
509-454-4578, www.tslusa.biz
ZED Industries,
937-667-8407, www.zedindustries.com
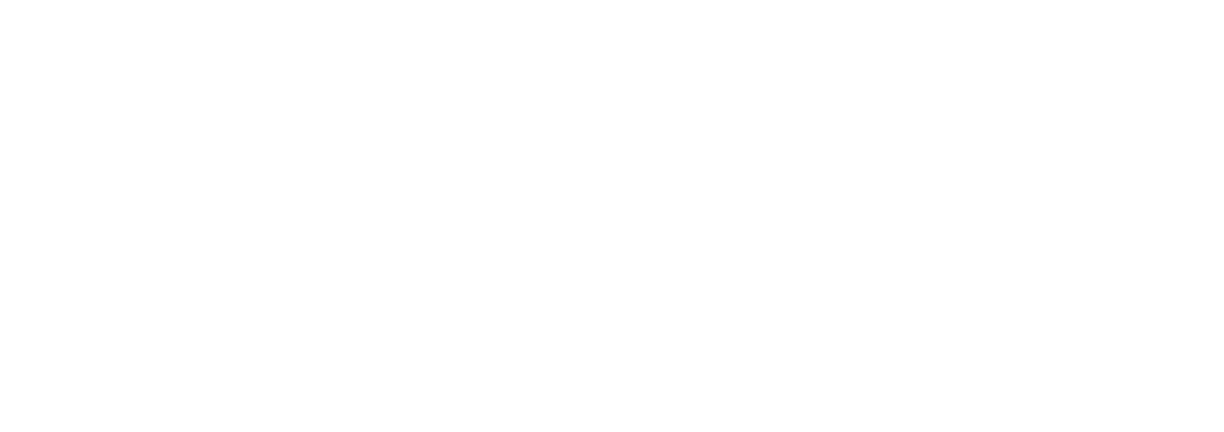