Novatec, Prophecy team up for wearable sensors that head off equipment failure
At a carefully executed NPE launch last month, thousands of attendees were able to ask questions about how, exactly, vacuum pumps and dryers now can be part of the Internet of Things, with data collected and analyzed to predict maintenance issues.
Rather than accept a traditional "run to fail" mentality, Novatec Inc. is offering wearable technology that allows for predictive maintenance. Novatec, Baltimore, has partnered with Prophecy Sensorlytics, Columbia, Md., to put wearable sensors on certain equipment.
Why bother? It is far more than a gee-whiz trick of connecting one more moving part on the factory floor to a phone. The answer lies in preventing a catastrophic failure of often overlooked equipment in a plant.
Novatec's initial release of the technology will be on vacuum pumps for conveying systems for belt tension, oil levels and viscosity, and temperature, and then extended later this year to rail-car pumps. Central dryers (the internal blowers and heaters) are targeted in initial release, as is downstream extrusion (vacuum pumps and water pumps) for vacuum sizing tanks and water cooling tanks.
With many years of use, industrial sensors have become proven technology, says Conrad Bessemer, Novatec's president and managing partner. But the cost and ability to monitor 24/7 wasn't there. The opportunity now, he says, is for a processor's IT, production and maintenance groups to come together in a single, universal approach to improve machine utilization, productivity and profitability.
Think Fitbit for a machine. The wearable sensor can attach to a motor or a gearbox and records data on a continual basis after a baseline has been established for the optimal condition. Motors, gearboxes, blowers and heaters largely have been unmonitored and undetected, says Bessemer. The machinery subsets are not being monitored. Rather, most companies monitor process conditions.
"Let's say you get a low temperature condition on a machine that's caused by a defect in some physical part of the machine," he says. "You can deduce from the process condition but it doesn't tell you what really happened. Also, it doesn't warn you when things are about to happen. A lot of stuff is hidden inside the bowels of the machine, so things happen and it isn't just detected through sound. There is temperature — if a motor temperature is rising, its surface temperature is rising, there probably is something going on and it is going to fail. What has existed in the industry for years is that it's either a 'yes' or 'no' condition. Either it works or it doesn't work, and when it doesn't work, it's catastrophic."
In the case of a vacuum pump, the data collected would encompass the functioning of bearings, belts, filters and oil levels. Sensors are capturing real-time data via Bluetooth devices to the cloud or directly by a ZigBee Ethernet device direct to the cloud.
The data being transmitted is not process or production data. What is being recorded is the output function of gears, blowers, barrels, heaters and the like, says Bessemer.
"In our mind, it is not sensitive data that can be linked to operating production or secretive process conditions that a user might be concerned about," he says. "In addition, we are not taking over the control of any machine or any component. We are simply reporting and recording and then interpreting data regarding vibration, sound, temperature and other aspects of the component being monitored."
A vacuum pump, for example, would have a device placed on its blower so sensors can tell what is going awry within the machine. Is it a bearing anomaly? Is there filter clogging? Abusive operation? Is there too little or too much oil? Human beings notoriously keep putting oil into this equipment. The sight glass on a blower, after all, is really small. But when you keep putting oil into the equipment, you risk an overfill, and an overfill is as bad as an underfill. It creates additional pressure on the bearings and can lead to premature failure. Loosened belts also can be detected.
Novatec is offering the technology at no additional cost on its equipment. The data is captured and represented in color-coded zones on a production graph. A green line, for example, would indicate the baseline normal oil level. A red line would indicate low oil level. An intermediate or yellow line could indicate that it's time to think about preventive maintenance.
"We're making the dumb machine into a smart machine," says Biplab Pal, co-founder and chief technology officer of Prophecy Sensorlytics. "This was not even possible two years ago. This is the right time."
Bessemer agrees. Now, especially, the plastics industry doesn't have the experienced maintenance personnel that it had in prior years. This even predates the Great Recession."
You'll find, in many cases, you only have a few maintenance people and they're just all over the plant. They're trying to keep things running. This way it really gives a plant manager the chance to monitor all those factors and fix them when they're off-line," says Bessemer.
The "vital signs" are monitored so that if one parameter is in a yellow zone, the plant manager or engineering manager can be warned that he or she has a certain amount of time to fix the problem. Novatec, for its part, can schedule a service trip to fix the situation before there is a failure. The manager has real-time access to the data.
The industry can thank the sensor trend in the marketplace, especially among consumers with products like the Fitbit and within the automotive market. Ten to 15 years ago, the average car had 20 sensors; now it has 100. Because the cost for raw sensors is currently so low, sensor technology is making its way into other areas.
Bessemer sees wearable sensors being taken into other areas of plastics manufacturing, for example, chillers and processing equipment. "That is the real promise of the future," Bessemer says.
Prophecy is seeking additional development partners in these areas.
CASE STUDY:
Manufacturing Analysis
A major paper manufacturer took on the task of integrating sensors on its own, to the tune of $1 million.
Its plant was a $500 million operation and the company was able to improve production by approximately 10 percent.
Capturing and analyzing data on the plant's equipment, officials increased production by approximately $50 million, which generated about $7 million in additional profits.
Angie DeRosa, managing editor
Contact:
Novatec,
410-789-4811, www.novatec.com
Prophecy Sensorlytics,
877-460-1920, www.prophecysensorlytics.com
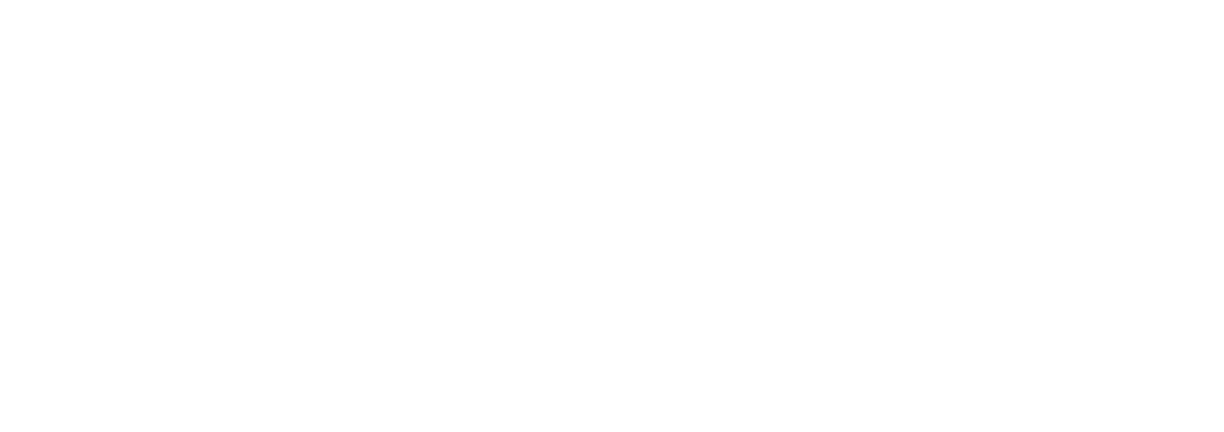