If suppliers of blown film lines seem positive and enthusiastic, they have good reasons. A new study from business researcher Freedonia Group Inc. says demand for plastic film in the U.S. is expected to grow 1.5 percent annually through 2018, when it will reach 15.4 billion pounds worth $24.9 billion.
That bodes well for the future but there are great reasons for enthusiasm here and now. The suppliers of blown film technology that recently spoke with Plastics Machinery Magazine said that the rate of sales and installations has been healthy, the current order rate is good, systems and components are being built on the shop floor and requests for new quotations keep arriving.
The supplier companies broadly agree with Cleveland-based Freedonia that the biggest driver of this growth is packaging, particularly high-barrier food packaging, with industrial, pharmaceutical and medical packaging also contributing. They also agree that NPE in Orlando should be a busy and productive event for the blown film sector.
In praise of flexible packaging
"There are very few industries in the world that are growing as rapidly as the flexible packaging market," says Gary Hughes, president and CEO of blown film technology specialist Brampton Engineering Inc., Brampton, Ontario. To emphasize the point, he adds, "While the industrial blown film market continues to grow, the packaging market soars."
Innovations and technological advancements are constantly revolutionizing the film and flexible packaging industries, says Hughes. In particular, consumer lifestyles that revolve around convenience continue to draw out new inventions and packaging solutions. The battle for shelf position in the store means the competition for desirable, standout packaging is always hot.
As a leading supplier of innovative blown film lines from three to 11 layers for high-barrier applications such as food packaging, Brampton says current drivers for packaging and film producers include packaging integrity, cost reduction and increased film attributes.
Hughes says the same factors driving flexible packaging innovation are driving innovation at Brampton. For example, given the many different substrates used in flexible packaging, Brampton relies on its engineering and technical know-how to help processors create unique recipes and quickly change between SKUs to gain a distinct competitive advantage. Furthering that advantage is an improved return on investment (ROI) from higher-value films efficiently produced.
At NPE, Brampton (Booth W2626) is presenting technologies such as its SCD streamlined coextrusion dies; its nine- to 11-layer, air-blown AeroFrost lines; the newest Italycs-5 control software for full-line high performance and operator efficiency; and its versatile FlexWin gap turret winder.
Also at NPE, Brampton will have a prime example of its innovative focus: its AquaFrost water- quenched blown film coextrusion technology for seven, nine or 11 layers. Contrary to traditional blown film systems that blow upward from the die, the AquaFrost bubble is extruded downward, blown to the desired diameter and rapidly cooled by contact with chilled water in the water ring, minimizing crystal growth in the material. Continuing downward, the bubble is collapsed, randomized by a secondary nip, and wound into rolls.
The downward-extruded, water-quenched technology combines advantages of cast and conventional blown film processing. It retains the high clarity, thermoformability and reduced curl of cast film, while also keeping the balanced orientation and process flexibility of blown film. With AquaFrost, blown film processors can use less expensive resins while holding the same or superior properties.
Compared with conventional cast film, water-quenched AquaFrost film offers clarity and gloss, higher output rates, lower energy costs, softness, uniform interlayer thickness, reliable deep-draw thermoforming, puncture resistance, tensile strength, balanced orientation, tailored barrier properties and interesting economics. The line's footprint is about half that of a cast film line, output rates are higher and energy costs are lower. Studies on machines in use show an additional 10 to 18 percent ROI with AquaFrost over cast film.
There are 17 AquaFrost installations globally, many with two or three lines. Though Brampton pioneered water-quenched blown film technology, it remains a niche in North America.
High-barrier lines, affordable upgrades and retrofits
When PMM caught up with Carl Johnson, president of blown film supplier Gloucester Engineering Co. (GEC), Gloucester, Mass., he was heading for the Plastindia show in early February.
"The majority of the projects we're working on are high-barrier, seven- and nine-layer blown film systems," he says. "We currently have an incredible amount of inquiries from all over the world, including North America."
Johnson says that sector is very active — with seven-layer lines recently installed in Korea and Mexico — and that is particularly good for GEC's die technology. A die design just patented in January reduces possible stagnation of ethylene vinyl alcohol in the spirals of the channel.
"We're excited about how well it works and we'll be talking about that at NPE," he says.
GEC (Booth W6744) has several new technologies to present at the show, but he also emphasized that the company is focused on upgrading existing lines and technology. One example of that is GEC's new ExtruTouch blown film control system. As a retrofit it can be used to upgrade any existing GEC blown film line as well as any other make or model of blown film system.
The ExtruTouch is built on a PLC platform and the human machine interface is an industrial PC. The big change for GEC is that it runs on third-party hardware and third-party input/output. There is no proprietary hardware or I/O on the system, so the processor will have the option of maintaining the ExtruTouch itself, which Johnson says "seems to be something everybody out there wants."
The ExtruTouch is based on B&R's latest X-20 generation PLC, and its 22-inch touch screen is not only large but uses intuitive, easy to understand graphics. The system includes multi-language capabilities, remote access, easy interfacing with other Windows-based applications and open process control compatibility for connectivity with common third-party analysis tools.
The new control architecture also lets GEC offer a stand-alone automatic profile control system for lower cost than in the past. Johnson notes that there are a lot of older mono- and three-layer lines out there with older controls. The ExtruTouch will be offered as a retrofit, and then a processor can consider upgrading blenders, screw drives or other line components, and it will all be linked with two new bubble-cooling products that will debut at NPE.
The UltraCool 3, which is GEC's new generation of air ring technology, includes an internal air ring and an external air ring. Johnson says a processor can expect about a 10 percent performance improvement by upgrading the external air ring. With the full UltraCool 3 package, an external air ring and a new internal air ring with multiple outlets, the processor will see about a 20 percent improvement.
At NPE, Gloucester will have the internal and external UltraCool 3 Air Rings, an ExtruTouch control system, a gauge and a blending system running so attendees can get a feel for how they operate.
"Five is the new three" and lines made for resin bags
Steve DeSpain, president and GM of blown film supplier Reifenhauser Inc., Wichita, Kan., says this is definitely an exciting time.
"The market is turning up," he says. "Overall demand level is up, and I think a lot of it is pent-up demand being released."
He sees a bunch of good things happening at once: The U.S. economy is good, the dollar is strong, gas prices are down and all that gives people confidence, which then relates back to the plastics machinery business.
For DeSpain a couple of things in the North American market stand out. First comes the activity in the FFS — form, fill and seal — market: heavy-duty shipping sacks for, of all things, resin. There's a lot of buzz, a lot of quotations and some actual lines going in as well. It seems related to the shale gas phenomenon, and downstream to the anticipated growth of the PE market, with North America likely to become a net exporter of resin at some point.
Second comes the standard polyolefin market, which is still showing good demand for typical three-layer film structures. In addition, some Reifenhauser customers already have switched to five-layer lines to give them more flexibility. Others are thinking about switching and getting quotes on five-layer lines. There's general demand in the packaging film sector, such as film for stand-up pouches, a growth market, and to replace films using nylon where the heavy barrier isn't needed. They realize they can go to a five-layer polyolefin line, lower their costs and make a 100 percent recyclable film.
The switch from three-layer to five-layer largely is in non-barrier films. DeSpain says, "Five is the new three." In effect, it gives the processor a significantly more flexible three-layer system. There is more room to play with structures and materials either to downgauge without losing properties or to take cost out of the final product by substituting cheaper materials in certain layers and using performance materials only on the skins.
"Everybody's crystal ball is cloudy, so anything that lets processors see where they're going to be six months or a year from now helps," he says. "Five over three layers means flexibility now and a year from now when something in the market changes, for example, price shifts in the materials market."
For the three-layer heavy-duty shipping sacks, Reifenhauser has a blown film line designed specifically for that product. DeSpain says that's because even though it is a demanding product to make, and the 55-pound bags can't break when dropped, it's also a price-sensitive commodity product in the market. Throughput is critical to the processor's bottom line. That's why the rate for a Reifenhauser Evolution Ultra Cool FFS line running a resin-sack type of recipe is 450 to 500 kilograms per hour (1,000 to 1,100 pounds) out of a 175mm die.
When Reifenhauser (NPE Booth W3551) did a demo of the line during the 2013 K show, it ran at 400-plus kilograms an hour, and improvements made since then have increased the rate.
Interestingly, although FFS film generally has been three-layer, processors also are going to five layers. (Yes, resin producers want their resin bags downgauged to use less resin.) DeSpain says resin companies and analysts agree that resin usage is on the rise, which means more film and more bags will be needed.
Typically, these lines are very dedicated. They run resin bags year-round, usually 24/7.
The latest enhancements to this line — screw design, die design, and the UltraCool IBC system — arrived about a year ago, and it's the combination of those that enables the new, higher rates. Reifenhauser has supplied numerous lines of this type around the world.
Two newer Reifenhauser products will be introduced to the North American market at NPE, both of which work at the top of a blown film tower. The Ultra Flat is an oscillating haul-off that serves to iron out the inherent bagginess of film at the top of the tower. It pulls the film tight, anneals it and locks in the results. It doesn't make the line run faster and the roll doesn't look prettier. The results show up when the processor uses that film in-house or sells it to a secondary market like a converter. The flatter film enables higher speeds on downstream equipment such as a printing press, bag machine or form-fill-seal system. If that sounds like a machine direction orientation (MDO) unit, it's not, but Reifenhauser also has one of those for the top of the tower.
The Ultra Stretch follows the same idea as the Ultra Flat and adds more rollers and different drives to create an actual MDO unit atop the tower. A processor can do any stretching there, rather than on a separate MDO unit. Having this function on top of the tower obviously helps with floor space. It also lets the haul-off use the heat still in the film at that point. No oil heating system is needed, which means it's cleaner, and it is more energy efficient than doing MDO off-line.
DRIVING FORCES
Current drivers for packaging and film producers:
• Packaging integrity: barrier layer integrity, consistent layer structure, repeatable processes and processing complex structures to extend shelf life.
• Cost reduction: downgauging to reduce the material used, flexibility for changing SKUs, consistent output and reducing waste from scrap.
• Increased film attributes: optical properties, barrier, formability, sealability, puncture resistance and physical integrity.
Source: Brampton Engineering Inc.
Rob Neilley, senior correspondent
Contact:
Brampton Engineering Inc.,
905-793-3000, www.be-ca.com
Gloucester Engineering Co.,
978-281-1800, www.gloucesterengineering.com
Reifenhauser Inc.,
316-260-2122, www.reifenhauserinc.com
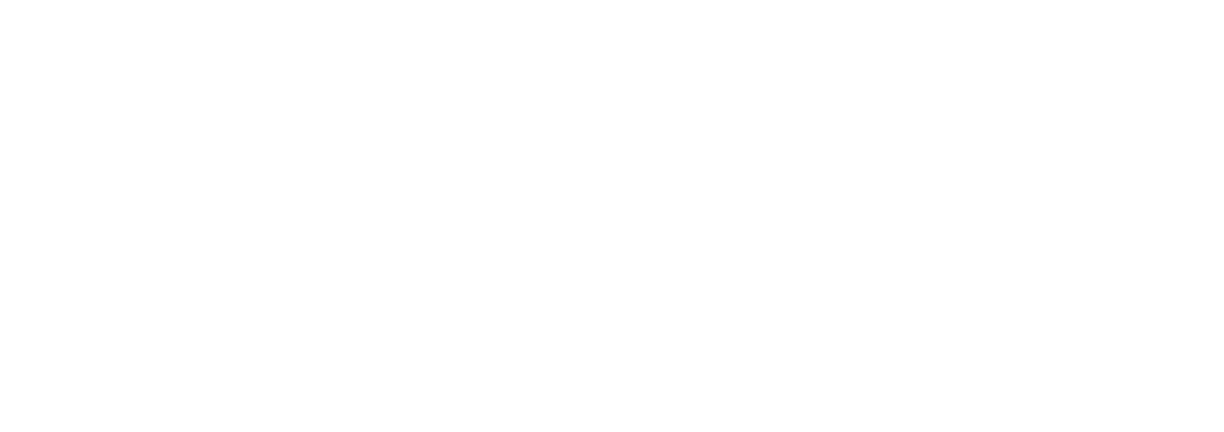