1Blow developed several additional hardware and software technology kits last year that add flexibility to the process.
Sure grip, a multi-stage mold insert system that allows production of bottles with a hyper-extended grip handle that 1Blow sales manager David Batten says cannot currently be produced with conventional stretch-blow molding. At the end of the stretch rod stroke, mechanical components in the mold actuate the handles inward to a distance within 12mm of each other.
Preferential and offset heating, designed to optimize production of oval or oblong bottles. Adjustable heating lamps in the oven can be arranged in an arc profile instead of directly in-line with the center of the bottle. At the same time, an additional oven, installed within the pitch-change device, supplies heat to the outside edges of the preform that allows the neck to be moved to an offset position (more than the 15mm limit of a traditional rotary system) while maintaining the uniformity of the wall.
Neck orientation uses the thread start on the preform to orient the neck finish, which is desirable for products molded with flip-top caps. Current approaches cut a notch or tab into the preform then use a device to locate the notch for orientation. 1Blow's approach eliminates the need for a special notched preform.
Base inversion is a multi-staged mold-base system that allows for base pushup of the blow mold for the creation of a diaphragm base on heat-set bottles. The diaphragm acts to absorb the vacuum created after the liquid contents in a hot-fill bottle cool. Converters can use this technology module combined with their patented bottle designs to create hot-fillable bottles that eliminate the need for vacuum panels.
Mikell Knights, senior correspondent
Related story: 1Blow produces PET bottles on machine that combines linear, rotary functions
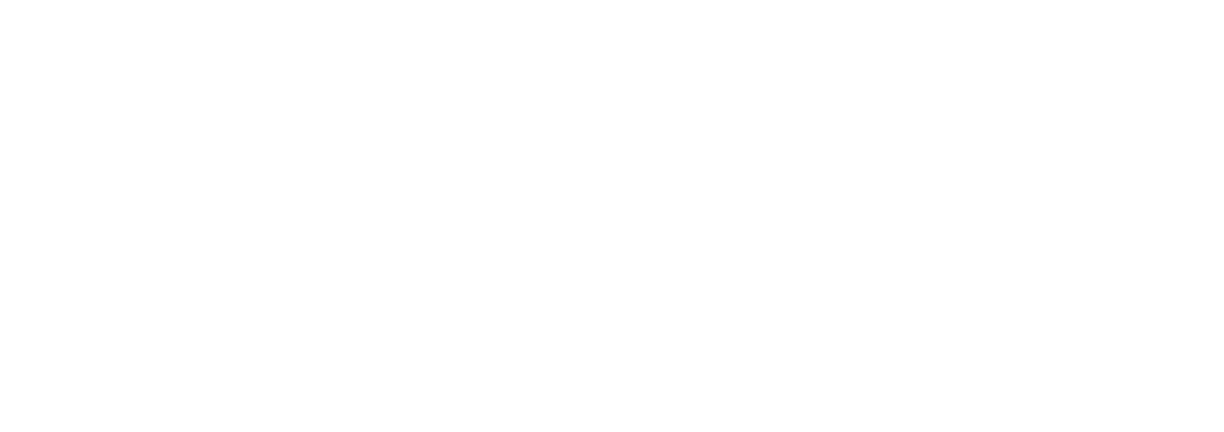