1Blow produces PET bottles on machine that combines linear, rotary functions
PET reheat stretch blow molding machine design is taking a new turn with models that combine rotary wheel and linear functions for process flexibility and high production.
The two common types of PET reheat stretch blow molding machines — rotary and linear — are cost- and/or performance-prohibitive at production rates of about 4,000 to 8,000 bottles per hour (BPH), according to 1Blow, Boissy-l'Aillerie, France, a 5-year-old manufacturer of blow molding machines (NPE Booth S34091).
In a rethinking of design, 1Blow has developed a series of compact, all-electric stretch blow molding machines that use both linear and rotary functions to produce PET bottles from 200 milliliters to 20 liters (5.3 gallons) with neck finishes from 20mm to 70mm. Production rates are from 500 to 8,000 BPH. The patented design streamlines mechanical functions for greater efficiency while offering the flexibility to use blow molds from competing manufacturers, including KHS Corpoplast, Krones AG, Sidel and Sipa SpA.
In addition, 1Blow's near rotary blow molding units are offered with six different technology kits that expand the bottle design and functional possibilities, from offsetting the neck for trigger-spray bottles to a diaphragm base that allows heat-set bottles for hot-fill projects that don't want to use vacuum panels, says David Batten, the Duluth, Ga.-based sales manager for 1Blow in the U.S. and Canada. The open architecture of the molding machine allows all of the technology kits to be factory installed or retrofitted in the field.
Key developers and owners of the 1Blow technology have 180 years of combined stretch blow molding experience. The company has sold 30 machines globally since beginning operations in 2011, with three installed in North America last year, and a fourth recently sold. Four units are operating at molding firms in Germany producing tight-tolerance technical blow molded bottles, says 1Blow President and Managing Director Benoit Sanchez.
TARGETING LOW CAVITATION WITH HIGH OUTPUT
Rotary wheel stretch blow molding machines can be fitted with up to 34 mold cavities to produce PET bottles at rates of 68,000 BPH or more.
"The rotary wheel is an efficient design because preform-to-bottle operation occurs in a gentle and continuous motion from one position to the next," says Batten.
However, at or below production rates of about 15,000 BPH using eight cavities, wheel designs can be a tougher sell. The primary mechanical component in a wheel machine is the rotary union or blow wheel, which supports and indexes the blow molds around its circumference, says Batten.
"The rotary union is a highly complex, high-precision component that houses critical utilities for the machine, such as low-pressure air, high-pressure air, mold-cooling water, electrical controls, recovery air and hot oil, and the blow wheel requires energy to spin," says Batten.
A rotary wheel becomes less efficient and more expensive at lower production levels because the rotary union has to rotate farther to get the next mold into the molding station, says Batten. A 20-cavity rotary unit positions each mold around the wheel at an equal distance, 18 degrees from the next mold. An eight-cavity unit locates each mold 45 degrees apart around the circumference of the wheel, while a two-station rotary tool would place molds 180 degrees from each other for balance.
"The time the heated and conditioned preform exits the oven and enters the mold for blowing should be kept short, otherwise the PET preform will cool, which is detrimental to final part quality," says Batten.
In addition, the rotary union has to rotate without leaking air, water or oil, and could become a maintenance issue, due to the complexity of design. The potential inefficiencies of linear-type reheat stretch blow units lie in their operating motion.
"Linear does its work on the advance motion, where it accomplishes tasks such as moving the preform forward or opening a mold. However, a nonproductive return stroke is required in order for that component to be in position to repeat its task. In some ways linear motion is only 50 percent effective," says Batten. He added that there are some companies that have found a way to carry out a function during the recovery stroke, but overall the return stroke is a nonproductive step.
IN-LINE ROTARY
With 1Blow, 11 key motions are required to move the PET preform through the process to result in a finished bottle. Competing stretch blow units have as many as 16 or 17 steps to produce the bottle, with several extra motions needed for their transfer and return mechanisms.
"Some of the actions involve the handling and transfer of the PET preform from the oven to the mold, and from the mold to the exit of the bottle from the machine. In our system we did not integrate those five or six additional steps, we eliminated them through design," says Batten. However, all of the required mechanical functions are incorporated into the unit.
Nine of the 11 functions in the 1Blow line use rotary (circular or wraparound belt-style) devices while the final two steps of the process, preform into the mold and blown bottle out of the mold, are non-rotary, linear actions, says Batten. The 1Blow design does not include a rotary union so the molds do not move through the machine. Instead, molds are stationary at the clamping/blowing point and only open and close. PET preforms enter the system by the elevating conveyor, move to the preform orientation device — a dynamic roller — and static-rail preform feeding device. Although the preform advances in a straight-line fashion from one device to the next, the specific component within each piece of equipment that engages, supports and then disengages the preform during transfer wraps around in a vertical rotary style, where the return is underneath the operational side of the device. A star-shaped in-feed wheel transfers the oriented preform to a carousel-style rotary reheat oven, where the preform revolves on spindles as it traverses the heating unit. 1Blow's oven design features three banks of adjustable infrared (IR) heating lamps, which provide 50 percent greater oven capacity than competing machines. This added heating capacity is needed for challenging bottles that have difficult shapes, heavy walls, opaque colors or all three features, says Sanchez.
When the preform exits the oven it is transferred by an out-feed device to a proprietary gripper and pitch-change device. In the oven the preforms are rotating on spindles and have a pitch (center to center) spacing of 60mm; however, in the mold the pitch distance is typically 120mm to 160mm, depending on machine brand, says Batten.
"Somewhere between the oven and the mold the pitch has to be expanded. 1Blow designed grippers that are unique in that the pincers can open up 180 degrees, which allows them to completely clear the neck finish of the preform," says Batten. Enhancing the functionality of the grippers is simpler than a myriad of more complicated mechanical solutions created by competing manufacturers to change pitch distance. The grippers handle the preform at the neck finish, then traverse a proprietary servo-driven linear system to transfer the preform from the pitch-change unit to the mold.
"In competing systems, the gripper has to get out of the way before certain operations can be carried out, then the grippers come back to pick up the next preforms, moving out and back. Our grippers take the preform into the mold and the blown bottle out, moving in one direction to bottle exit and then return along a linear track back to preform pickup," says Batten. Except for the rotation of the IR oven, 1Blow systems handle the preforms and bottles in the neck-up position.
1Blow has offered one-cavity and two-cavity units for several years, adding a four-cavity model in 2013. A six-cavity standard unit and a model for production of wide-mouth bottles are in development. Each system is designed to be compact while delivering high output rates.
1Blow has sold two of its four-cavity 1Blow systems to a bottle producer for Coca-Cola. At NPE 1Blow will produce bottles at a rate of 2,000 bottles per cavity, per hour on a 2L unit. The 1Blow units incorporate control technology and six servomotors from Bernecker + Rainer Industrie-Elektronik GmbH, Eggelsberg, Austria. The servomotors are looped together so that energy saved by a braking servomotor is passed forward to the next step in the process.
"For example, when the mold closes, that motion is profiled to slow before reaching its final position. A generator captures that residual energy (about 3 to 5 percent of energy used in the process) and sends it to the stretch rod. When the stretch rod nears the end of its stroke, that energy is again captured and delivered to the mold-open operation," says Batten.
1Blow designs block molds that are adjustable, where the cavity inside the mold can be moved to accommodate center or offset neck finishes while keeping the same blowing position.
"This is a huge benefit. Molds for conventional rotary systems are fixed," says Batten.
Other standard features include a high-pressure air-recovery system, Internet-ready connectivity, an on-board technical and maintenance manual, an internal voltage modulation/regulation system that eliminates the electrical transformer, and compliance with UL standards.
Mikell Knights, senior correspondent
Contact:
1Blow, 678-417-0050, www.1Blow.com
Related story: 1Blow adds hardware. software
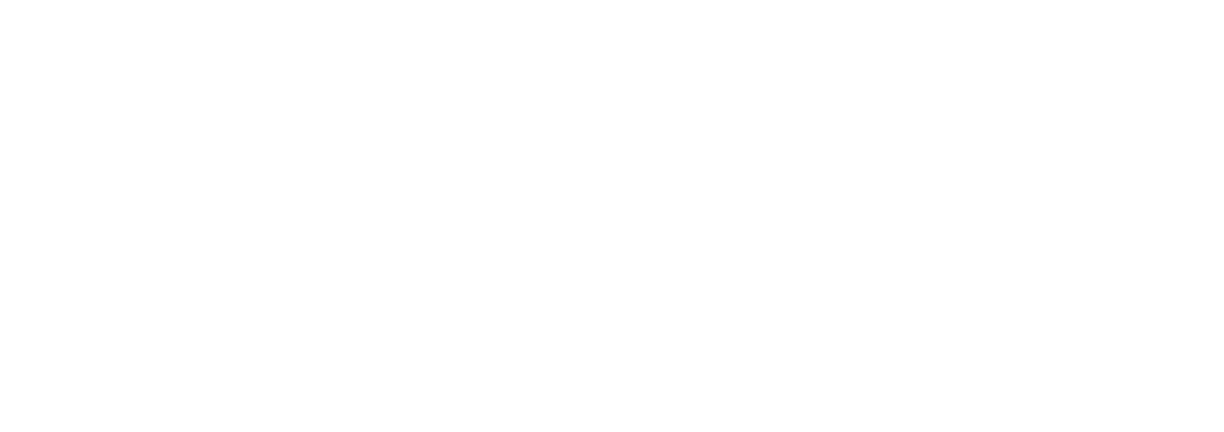