Machinery makers are addressing energy efficiency needs in many ways. This article showcases some of the more recent developments.
Injection machine energy choices abound
After decades of development, major manufacturers of injection molding machines are offering a variety of all-electric and hybrid injection presses for widely differing applications, and all delivering significant energy savings compared with hydraulic machines.
Milacron LLC, Batavia, Ohio, pioneered all-electric machines in North America by distributing Fanuc Roboshot machines from Japan. It still supplies and supports the Roboshot machines, which have been joined by three lines of all-electrics that Milacron has designed and developed.
The Elektron series (400-, 500- and 600-ton models) is made to support a broad range of applications and to provide value to its owner. An Elektron consumes about 60 percent less energy than a comparable hydraulic machine, and uses about 90 percent less water.
The F-Series features a modular design for easy customizing to a processor's needs, which can include servo-controlled hydraulics for ejection, carriage movement and injection; clamping and plasticizing are electric as standard. Aimed at consumer goods, packaging and medical applications, the F-Series offers 10 clamp forces from 50 to 650 tons.
Milacron's PowerPAK high-performance electric machines targeted at packaging applications offers five clamp forces from 440 to 1,125 tons and can achieve up to 80 percent savings in overall energy usage over comparable hydraulic machines.
The Fanuc Roboshot machines Milacron offers come in seven clamp sizes from 17 to 330 tons and reduce energy consumption from 50 to 80 percent and cycle times from 5 to 50 percent, compared with hydraulic machines.
Milacron says it designs energy efficiency into its injection machines from conception. Servomotors are optimized for each axis of its all-electrics and are used instead of conventional induction motors on its five lines of hybrid systems. Excess energy is recovered and stored and a standby mode supports energy on demand. As an option, Milacron's TCS (Thermal Control Solution) heater band system uses radiant heat that goes directly into the barrel. The system can reduce energy up to 50 percent.
Glenn Frohring, one of the owners of Absolute Haitian, says his company's Zhafir Venus II all-electric machines are very energy efficient, as well as precise, fast, quiet, clean and more. His Worcester, Mass., company is the U.S. and Canada partner of Ningbo Haitian Machinery of Ningbo, China.
But, says Frohring, great performers though they are, the all-electrics are just one of Haitian's machine platforms.
Servo-hydraulic machines like the Haitian toggle-clamp Mars II Series are another important platform for the company. Because the servo stops the pump from running when it is not needed, the energy efficiency is similar to a fully electric machine. Frohring said Mars continues to be Haitian's most popular machine series, with 100,000 sold worldwide since 2005. About two-thirds of machines sold in North America by Absolute Haitian are Mars models. Haitian's two-platen Jupiter Series also features servo hydraulics.
With four (costly) servomotors, fully electric injection molding machines of 500 or 600 tons have been called cost prohibitive, though Frohring thinks the tonnage ceiling might go a little higher. Also, many molders have molds with hydraulic core pulls, slides and ejectors. To run such a mold in an electric machine, a hydraulic power pack must be brought in, which adds footprint.
The servo-hydraulic machine has only one servo, which helps hold down the machine cost. Frohring says this type of machine was limited to 300 tons or less until Haitian found a way—patented in China — to couple the shaft of the servomotor directly to the gear pump. That meant the motor could be up to 128 kilowatts and servo-hydraulic machines could be up to 6,000 tons.
And the energy savings?
Frohring calls them phenomenal. He says a Haitian Mars (toggle clamp) or Jupiter (two-platen) injection molding machine with the servo system uses only about 30 percent of the power required by a 1,500-ton hydraulic press with a fixed volume pump or even a variable volume pump. Factoring that 70 percent energy savings into the return on investment may mean a quicker sign-off on equipment needed for a new project.
Haitian will showcase both its all-electrics and servo-electrics at NPE 2015. Making its U.S. debut at the March show (Booth West 3683) will be the Zhafir Zeres Series. Basically it is an all-electric Venus II with integrated hydraulics for molders with hydraulic core pulls, slides, carriage and ejectors.
Also at NPE, Absolute Haitian will introduce new smaller sizes of the Jupiter II servo-hydraulic line. Previously available from 1,349 to 4,496 tons, the five new Jupiter II models range from 440 to 1,069 tons.
Extrusion energy-savings, many opportunities
Extrusion and converting systems supplier Davis-Standard LLC, Pawcatuck, Conn., believes developing and making equipment that is environmentally sustainable is more than a trend; it's the present and the future of plastics extrusion. Machine technology that reduces energy, improves efficiencies and limits waste is how to get there.
Three examples highlight the company's progress: advances in direct drive extrusion, optimized feed screw designs, and new heating systems that minimize convective heat losses. A series of recent side-by-side tests compared the direct drive to its AC- and DC-drive counterparts based on energy consumption, drive systems, extruder speeds and sound levels.
The direct drive was found to be quieter by as much as 70 percent and its energy savings were as much as 15 percent. The direct drive's permanent magnet synchronous motor (PMSM) needs no mechanical gear reducer to multiply the torque needed to rotate the screw. Direct drive technology is available for several application areas in sizes up to 5 inches/130mm.
Davis-Standard says feed screw technology has a vital role in energy efficiency. To prove it, two screws, one optimized and one standard, were tested side-by-side. The optimized screw increased throughput by 11 to 13 percent, and decreased the extrudate melt temperature by about 20 degrees Fahrenheit, so less energy is needed downstream for cooling. The cherry on top is that the optimized screw costs about $15,000 and saves more than $20,000 in energy per year. Payback is only eight to nine months.
Davis-Standard says extruder heating/cooling systems are critical for holding the precise process temperatures demanded by today's high line speeds. Research in the company's technical center on how to minimize convective heat losses in an extruder's air-cooling system has led to a patent-pending active air damper system, which effectively minimizes the convective heat losses seen on current designs. This new development, including increased barrel heater insulation, creates a system yielding energy savings up to 18 percent. Combining that system with an optimized screw design can drive convective process heat losses to a minimum.
Rob Neilley, senior correspondent
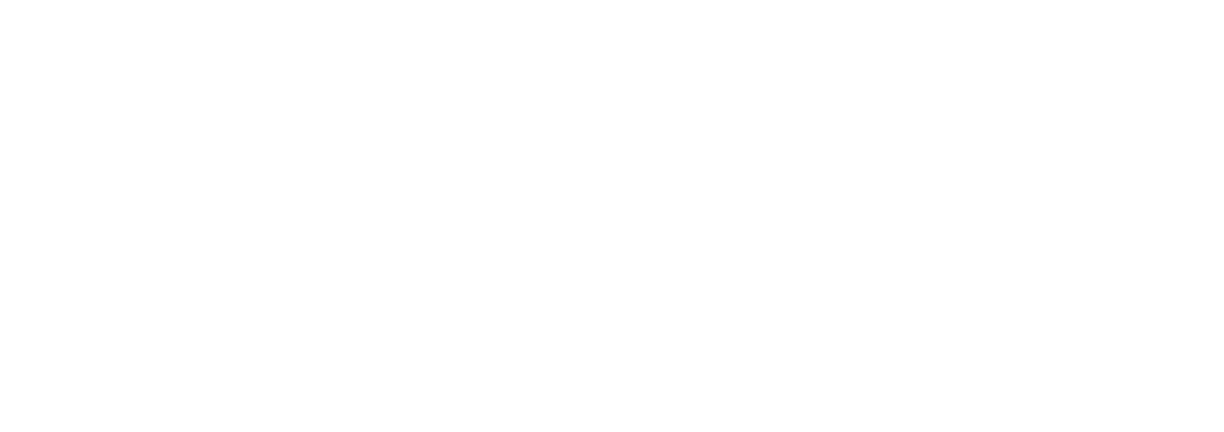