Robin Kent, the founder and managing director of Tangram Technology Ltd., Hitchin, England, is passionate about energy efficiency. His style is to go straight to the point at high speed and to pull no punches. PMM talked with Kent recently about his views on the subject of energy efficiency in plastics processing operations.
Kent knows that a fearless and honest analysis of the equipment you're running can make a huge difference to every aspect of your daily operation. If you don't think you have the time for such an analysis, read on … and you might change your mind.
The big picture
A leading plastics processing consultant, Kent has worked with hundreds of processing firms around the globe and is a frequent speaker at plastics industry conferences, most often discussing energy costs and efficiency.
"My view is that energy efficiency is a battleground for machinery manufacturers, but processors are still focused primarily on purchase price, not on whole-life cost.
"It's absolutely stunning to learn how many companies consider their energy costs a fact of life. They pay the utility bill automatically, often without anyone actually looking at it, never mind analyzing it. It's incredible but many don't know what energy is costing them."
Overall, energy efficiency is just good management.
Kent has analyzed somewhere north of 400 factories and, he says, the most energy-efficient of them also turn out to be the most efficient overall.
"Management makes the difference. When you see good energy efficiency you also see good materials control, good maintenance, good purchasing, good sales and financial control. Good management is the ability to manage everything."
Two decades of developments have made a huge difference.
Over the last 20 years there has been, on average, a 20 percent improvement in the deliverable energy efficiency of plastics processing machinery — some processes more, some less. A 1990s machine is less energy-efficient than a current machine.
"Technology has moved on. Would you drive a 24-year-old car or use a 24-year-old phone? If the answer is no because they do less and are less efficient and less consistent, then why do you have a factory full of 24-year-old machines?"
The numbers at the pump may be decreasing, but …
The current relatively low U.S. energy costs are not helping to drive energy efficiency.
"In fact, they are a real handicap to overall improvement of the industry. Processors can say, well, energy prices are coming down, so I don't have to do anything about my energy costs. I don't need to worry about that anymore."
Energy efficiency is not like fuel efficiency in a car.
You can make your car more fuel-efficient by driving slower. This does not apply to machinery, however.
"With most plastics machinery, running it hard actually improves your overall energy efficiency. None of the energy-efficiency processing things I talk about mean running your machine slowly. Energy efficiency and fast processing are the same thing. If I want to be energy efficient do I have to increase my cycle time? No. Decrease the cycle time. Run those puppies hard!"
Control technology can cut energy costs.
Each and every motor, pump or energy-drawing device in the plastics production process should either be actively making something or not running at all.
"When your all-electric molding machine stops, energy uptake drops to zero, and the same goes for electric screw drives and servomotors. But with a conventional hydraulic machine, pumps and motors are always running.
"How do we make it so that when any process component isn't actually involved in making the plastic product it's also not using electricity? One big thing that's not being attacked is controls. The machine makers could do more in the way of interfaces to all the auxiliaries and peripherals—robots, conveyors, all of them. They are not being proactive in this, but one big reason for that is the processors are not asking for it, or not asking for it enough."
All-electrics
Injection molding — probably the most vibrant plastics processing sector for machine energy efficiency innovation — mainly revolves around motor choices and control technology. The all-electric press, which came to market in Japan during the late 1970s and early 1980s, is still taking off in Europe and the U.S., owing to the size of the machine — up to 400 or 500 tons — and higher cost.
"The all-electrics are a no-brainer, but injection molding energy innovations extend also to hydraulic machines and the hybrids of electric and hydraulic technology."
For injection, it's about motors and pumps.
Fixed speed motors (FSM) and fixed displacement pumps (FDP) are old technology that should be gone. Anyone using them, in any process, is paying a lot of money to run them when nothing is being made. The options are many. They include using FSMs with variable displacement pumps, variable speed motors (VSM), and servomotors. The coming thing for larger machines seems to be hydraulic pumps with either variable speed drives (VSD) or servomotors to get a variable flow of hydraulic fluid. The VSDs tend to be valuable with cycle times over 20 seconds and long operational hours. As a bonus, he says, the electric screw drive gives the processor the option of downsizing the main hydraulic pump and motor for more energy savings.
"For new hydraulic machines, processors should be looking at pre-fitted VSDs for long cycle times and servomotors for shorter cycles. For those who need hydraulic machines with standard motors, generally large machines with high-tonnage clamps, look at electric screw drives, either with a new machine or as a retrofit on an older press. Get the hydraulics out of the screw drive."
Adding a retrofit variable speed drive to an older machine can have good results.
Done right, Kent says it brings a 1990s machine effectively to the level of a 2010 machine. He knows a number of molders getting good results with the SyncroSpeed retrofit VSD.
"It works best on 600-ton or larger machines with long cycle times (greater than 20 seconds), motors of 37 kilowatts (50 horsepower) or more and fixed displacement pumps. It slows the motor and pump when fluid isn't needed to save energy and money; just don't think you can take any VSD or variable frequency drive or inverter and plug it into your injection machine. The interface is critical."
On barrel insulation
Many molders like it, as do many extruders, but forward of the screw tips only. Some molders heat their factories with their machine barrels then pay for air conditioning in warm weather to get the heat out. Gas is about a quarter the cost of electricity for space heating, and costly process heating should stay in the process.
"Insulation is easy to fit, machines heat up quicker, cool down faster and safety problems go away. It reduces the heating energy an injection molding machine uses by about 25 percent and it's relatively low cost. What's not to like about barrel insulation?"
Extrusion motor technology now
Current technology is an AC or DC motor rotating at 3,000 rpm using a gearbox to get the right torque for a screw running at 20 to 60 rpm. Most extruders built prior to 2010 had DC motors, and around 2005 the DC motors began giving way to AC motors controlled by a variable speed drive. Some processors have reported 30 to 40 percent energy savings with the new technology.
"I know people who made the change because, compared to DC motors, AC motors with VSD have reduced their maintenance costs incredibly. Anyone still using DC motors should start looking at AC/VSD technology. Less maintenance, lower purchase and replacement cost for the motor, energy savings: There are a lot of benefits."
Direct drive emerging
The beauty of direct drive — more formally called a permanent magnet synchronous motor (PMSM) and direct torque drive — is eliminating the gearbox. The drive, which is connected to the back end of the screw, generates the torque directly. PMSMs are smaller and simpler than AC or DC drives, quieter. Some say they need less maintenance.
"The technology is just emerging. It's likely to be the standard in 15 years but today the situation resembles all-electric molding machines in the mid-1980s."
Rob Neilley, senior correspondent
More Energy Management Special Report stories:
Machinery makers take different routes to save energy
Don't overlook utility, government incentives
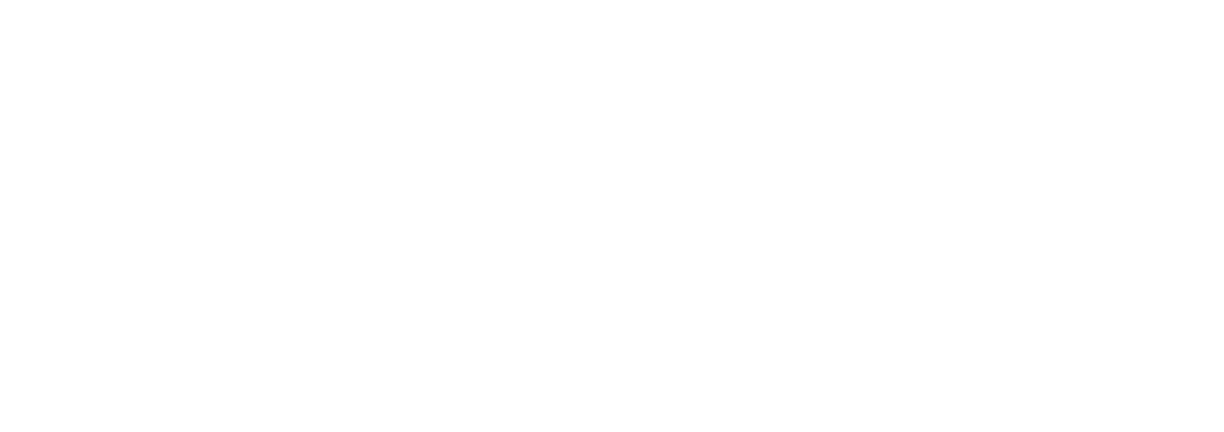