PMM's Mikell Knights posed the following questions to John Engle, staff engineer, North American Purchasing Tool Center — Plastics Group, for Honda of America Mfg. Inc.
How confident is Honda with aluminum tooling today? Where does aluminum tooling work best?
ENGLE: Our confidence level is high, and we continue to explore uses with different resins. We don't dictate to our supplier base that they must do everything in aluminum. Since our Tier 1 suppliers have responsibility for all tooling needed for the production of a part, the selection of mold material is up to them and their mold maker. The ones that champion use of aluminum typically look at non-textured parts first, then light stipple textured parts, then leather grains last. With acid etching, textured parts molded in aluminum have a slightly different appearance than the same part molded in steel due to the difference in the way the acids etch each material. Due to this, application has been limited on the interior plastic to low and medium visibility parts for texture harmony considerations. With the advent of laser texturing, that difference has been eliminated. Laser gives the same result consistently regardless of material.
What role do tool life, part volume, part size and maintenance play in the decision? What parts are manufactured only with aluminum tools?
ENGLE: We have proven over and over that for our applications, the items you mention should have no bearing on the decision. The biggest consideration is part geometry. If there are features on a part that would render it a poor candidate for aluminum, a knowledgeable
mold designer can advise you of it, and whether or not it would eliminate the part from consideration. Often, a problem area can be inserted with suitable metal, but if there are too many the cost/benefit comes into play.
How many interior, exterior and under-the-hood projects and what parts are made for Honda with aluminum tools today?
ENGLE: I can't put an absolute number on it, but it can be said that most North America-developed models have aluminum in the mix. Instrument panel parts and pillar garnishes have not been done in aluminum due to the aforementioned texture harmony issues. As laser texturing becomes more readily available, that will be a moot point. Outside of that, there aren't too many of our parts that haven't been done in aluminum at some point in the last 10 years. The notable exception to that would be bumper fascias. To my knowledge, none of the aluminum companies can forge the high strength aluminum in a large enough block to get the thickness required for the cavity block due to the physical limitations of the forging presses available.
Compared to estimates presented in the Honda study of 2008, is Honda today using PP, PE or thermoplastic olefin materials more than 75 percent of the time for automotive assembly and construction when plastic materials are applied? Are most of these plastic part designs brand-new components or are they the polymer replacement of an existing metal part?
ENGLE: The percentage of various plastic resins used in our cars stay pretty consistent, with polypropylene being the largest at about 70 percent of the parts. Most of these parts replaced metal stampings years ago, so in all but a few instances a polymer part is replacing the previous iteration of a polymer part.
Is Nissen Chemitec a qualified supplier of both aluminum and steel tools to Honda? Does Honda only source its aluminum tooling from that company?
ENGLE: We have a dozen suppliers that are running or have run aluminum tools. There is no exclusive source. The final decision of using aluminum or steel is theirs. As previously stated, since the supplier is responsible for the purchase and upkeep, they decide who they go to for a mold build.
Has an aluminum tool been able to deliver a part function or feature through its rapid cooling capability that a steel tool cannot?
ENGLE: In addition to the cycle time, there is a demonstrated improvement in the dimensional stability, e.g., flatness. The part is measurably cooler upon ejection, thus it is closer to a fully cured state.
Does Honda specify the type of aluminum to be used in the tool (are you asking for 7000 series aluminum), and if so why?
ENGLE: Honda does not specify a certain type of aluminum; it is up to the Tier 1 or the mold shop to whom they award the business to match part and volume to the best aluminum. Typically, everyone starts out with the high strength forged alloys, which are all 7000 series products. Once they become more comfortable with aluminum, there is greater savings on the mold build with some of the 2000 and 5000 series alloys for parts that won't be running in the 500K and up range.
What specific adjustment(s) to the process machinery is required in order to produce an excellent part on an aluminum tool?
ENGLE: While I'm hardly a process expert, I can pass along some information from some folks who are that have identified a few of the major ones.
There is less pressure required to fill an aluminum mold. I can hear some folks saying "BS!" but I have seen it myself. What those knowledgeable people tell me is that with aluminum it has to do with the rapid transfer of heat from resin to the molding surface, instead of the resin taking on the lower temperature of the steel prior to the heat transfer to the mold. This creates a thinner "skin" of set plastic on the molding surface. Let's say you have a part 2mm thick and steel gives 0.25mm thick skin. With the fountain effect of the resin flow, that leaves 1.5mm for the plastic to pass through. If that same part is molded in aluminum, the skin will be about 0.1mm thick, leaving 1.8mm for the flow. Less restriction, less pressure required. Start with low injection pressure and raise until there are no short shots.
Another difference is pack and hold time is practically eliminated. Once the cavity is filled, it's filled; the time required for solidifying the resin is short. Due to this, the screw recovery time can be a bottleneck. It is better to have a barrel that will give additional residence time to help with this.
And of course, the 40 percent or so of the cycle time devoted to cooling the part sufficiently for ejection is where the greatest time reduction takes place. I'm sure there are process engineers well-versed in aluminum who can provide more information, but some companies look on that as proprietary knowledge that gives them a competitive edge, and they may not be willing to share.
What would Honda like to say regarding the use of aluminum tooling in high-volume part production?
ENGLE: As time progresses and improvements continue to be made, it is an idea that is increasingly viable. When plastic was in its infancy, the aluminum available then was too soft for production use, which is the way many people still perceive it. The alloys available today weren't in existence. Had they been available, aluminum would be the preferred material today and no one would want to give up the cycle time advantage to use anything else.
As such, you would think it would be an easy sell, but people like to stick with the familiar. Change is unsettling. It is up to management to help foster the changes that lead to real progress. The learning curve isn't too steep — start small to help manage the transition, and expect a bump or two along the way; if there isn't, nobody's learning anything. Aluminum is not a cure-all that works for everything, but it's a valuable tool to help a company's bottom line, and that's what every business wants to do.
Mikell Knights, senior correspondent
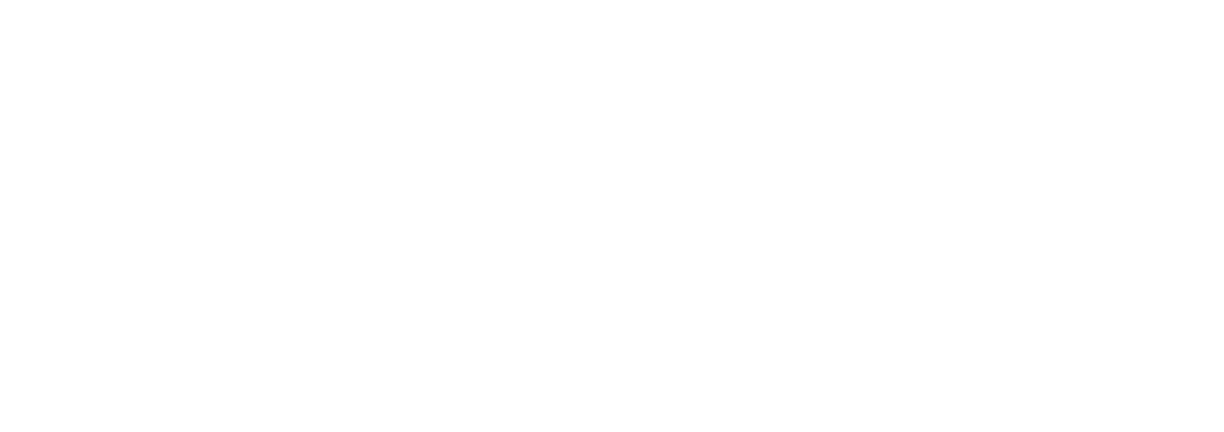