Recycling of expanded polystyrene packaging is a challenge unto itself, and relatively few recyclers, even of other plastics materials, are willing to take on EPS. Special equipment and technology setups are required to deal with this unusual material. Even conventional equipment, such as conveyors, granulators and extruders, must be adapted to the specific characteristics of EPS.
For one thing, EPS (which is not synonymous with Dow Chemical Co.'s Styrofoam high-insulation building product) is variously described as 95 to 98 percent air, by volume. Dart Container Corp., Mason, Mich., an assertive proponent of recycling EPS, reports that a standard 48-foot-long semi trailer could hold about 1,000 pounds, a mere half a ton, of EPS before it is compacted or, as it is known in the business, densified. At a compression ratio of approximately 40-1, the same vehicle can hold about 40,000 pounds (20 tons) of the material.
The initial problems with recycling EPS are not technical as such, but are in the realm of politics and economics. It is not easy to convince municipalities or other waste-collection entities that it is worthwhile to collect EPS, especially in a single stream, or even in mixed waste. The stuff is bulky, takes up a lot of space in collection containers, and is prone to flying away and creating debris during handling. Recycling EPS is not for the faint of heart. You've got to want to do it.
One significant motivation to recycle EPS is to be a major producer of the cups, plates, containers, and numerous other products for which EPS is ideal. Dart Container meets that description, in spades. One of the best ways to protect its business from aggressive anti-plastics proponents is to offer tangible proof that recycling is not only possible, but worthwhile.
After used EPS material is gathered, by whatever means, the next problem, since not much of it comes in pre-sorted, is to sort it out of the stream of mixed waste. The initial step can be done by the patently low-tech means of having it taken off a moving conveyor by workers, who pull EPS off the stream as the conveyor moves along. Don't laugh. The first step of some EPS reprocessing is done exactly this way. The work is well-lit, and requires no heavy lifting.
After that, things get a bit more complicated. The EPS scrap is thrown directly or moves by conveyor into a granulator, which need not be burning up energy and making noise by being on full time. A sensor on the hopper can determine when the hopper is full and trigger the granulator's operation, which, with the appropriate rotor, blades, and rotor speed, can literally grind the EPS waste to bits.
At that point, the need for more sophisticated magnetic and/or optical technology kicks in. Magnetic equipment is used to separate the ferrous (iron-based) and non-ferrous contaminants, such as aluminum, brass, or copper.
Optical sorting also can be used to sort out metals along with other plastics materials or undesirable colors. The sorting is not a matter of making multiple piles of this and that, but rather leaving desirable EPS material in the stream, and getting the other stuff out.
Magnetic sorting
John Collins, manager of plastics and PolyMag products for Eriez Magnetics, Erie, Pa., supplied a review of magnetic equipment appropriate for use in EPS recycling systems:
• Suspended, manual or self-cleaning permanent or electromagnets that remove larger ferrous contaminants and are especially useful with deep material burdens or materials that are easily entangled.
• AIP (axial interpole permanent) magnetic head pulley for the discharge end of a conveyor that removes ferrous material at the bottom of the product burden and are self cleaning.
• Plate magnets — well-suited for chutes with burden depths of less than a few inches.
• Ceramic or rare earth magnetic drum separators that remove small ferrous contaminants and are self cleaning.
• Metal detectors mounted below a conveyor belt to protect granulators and shredders from all types of metals.
• Vibratory feeders and screeners to convey and screen cleaned plastic flakes or pellets.
• Metal detectors/separators to remove tiny metal contaminates encapsulated in the reprocessed plastic pellets. This should be the last step in the metal removal process to minimize plastic loss.
Optical Sorting
Optical and magnetic approaches are not mutually exclusive. Both can be used in the same line. For one thing, optical equipment can sort out non-EPS plastics materials, and magnetic equipment normally can't. One line at Titus Maintenance & Installation Services Inc., Concord, Calif., uses a combination of a conveyor, an optical detector, and air jets to blow PS and EPS upward, and blow downward heavier materials, notably high density polyethylene, PET and aluminum.
Eagle Vizion, Sherbrooke, Quebec, says the success of an optical sorting system depends on the ability of the near-infrared (NIR) optical technology (see diagram, Page 30) to do material identification. Eagle gave this general description of the process:
The material to be sorted is fed onto an acceleration conveyor to spread it to a single layer. A vibratory feeder is typically used to feed the high-speed belt. This is done for the following advantages: Material reaches stability on the acceleration conveyor faster due to the smaller transition drop between the vibratory equipment and the conveyor. The vibratory feeder helps spread the material to the full width of the acceleration conveyor, which helps in producing a single-layer material for the optical sorter.
What is the tangible outcome of going to all this trouble to recycle EPS?
One intermediate result for Dart Container's process is 40-pound recycled EPS "bricks," which are ready for the ultimate transformation. They are reincarnated as chips, and converted to products such as attractive multi-color picture frames.
Thus the EPS has come full cycle, from pellets to cups to chips to "bricks" to chips again to picture frames. If I see one somewhere at a decent price, I'll probably buy it.
Merle R. Snyder, senior correspondent
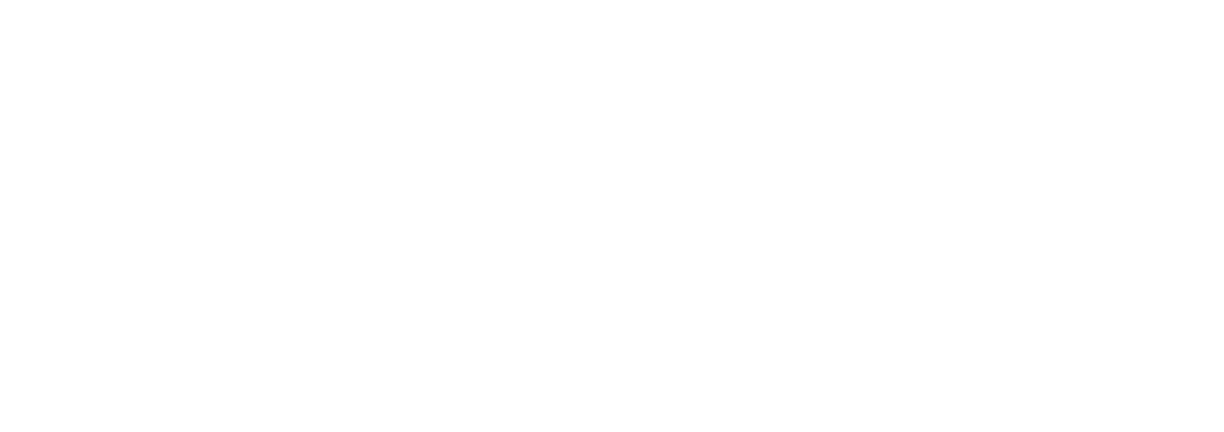