Aluminum molds are gaining ttraction in high-volume injection molding of automotive parts due to the cost, process and production benefits they offer. Honda has been the most visible user of this alternative to traditional steel but the industry can expect to see more activity from GM, Volkswagen and Tesla.
Injection molders producing automotive interior, exterior and under-the-hood parts are turning to aluminum tooling as a route to significant productivity gains, typified by cycle time savings that free up plant capacity. Although the rate of adoption remains low compared to steel, nearly every major automotive manufacturer in North America in the last four years is involved or pursuing an interest in the technology beyond its traditional use for prototype tools, says Darcy King, president and CEO at Unique Tool & Gauge Inc., Windsor, Ontario.
"For many, but by no means all automotive applications where rigid polyolefins are utilized, production aluminum tooling offers the potential for cycle time reduction up to 50 percent or more versus traditional P20 steel, lighter weight, reduced clamping requirements and a higher quality finished product," says King. Unique Tool specializes in the production of injection molding tools for automotive programs and has been involved with aluminum tooling for prototype and production applications since the early 1990s. The company considers itself a leading toolmaker in the sector.
What to expect
with aluminum tooling
Compared with steel, aluminum is softer, exhibits a different rate of thermal expansion and has higher thermal conductivity, yet is well-suited to serial injection molding production if designed correctly, says King. Lead times to build an aluminum tool are about 10 to 15 percent shorter than build times for a similar-sized steel tool. Tools with more mechanical actions that require additional machining, spotting, drilling or benching can be accomplished in less time with aluminum, says King.
Aluminum tooling may cost more than steel but the cycle time savings alone can make it worth the investment. A program requiring 150,000 cycles to hit the target number of parts would need a steel tool to operate for 95 days on a 50-second cycle, processing 1,584 shots per day. The same part run on an aluminum tool of the same size would operate on a 35-second cycle — due to the faster cooling and other factors — requiring 66 days on the press.
"The 30 percent cycle savings equates to 638 hours saved," says King. To some molders the savings can mean the equivalent of 29 shifts of molding time gained, or more.
In addition, lighter aluminum tools require less clamp tonnage than steel. There is less wear and tear on the molding machine and supporting equipment (i.e., a crane), and less mold weight provides an opportunity to the molder to shift production to a smaller press, taking advantage of more favorable machine hour rates. And despite lingering industry skepticism regarding tool longevity, the performance of aluminum tooling can match that of steel, depending on the polymers being processed. Unique Tool has designed and built production aluminum tooling for an automotive application that has already eclipsed 2 million cycles without failure.
"Aluminum has a compressive strength of 77,600 psi, and we know that the maximum attainable injection pressure at the front of the injection screw is 33,000 psi, regardless of screw size. Therefore, injection molding at its highest possible pressure requires 42.5 percent of aluminum's maximum compressive strength," says King. Aluminum tooling is ideally suited to non-abrasive polymers, such as PE, PP and thermoplastic olefin materials. Contrary to beliefs, aluminum tooling has successfully molded glass-filled nylons and other engineered materials, but frequent maintenance requirements make steel the better choice.
King, who presented a paper on aluminum tooling for high-volume automotive applications last October at the Society of Plastics Engineers' TPO Automotive Engineered Polyolefins Conference, says Unique Tool has produced thousands of steel molds for automotive projects compared to hundreds of hybrid aluminum tools — defined by an aluminum core and cavity with a steel mold base, back plate, rails and ejector plate.
Reasons to mettle
with this metal
Four high-volume tooling programs contracted between Unique Tool and automotive molder Nissen Chemitec America of London, Ohio, for Honda of America Mfg. Inc.'s Marysville, Ohio, plant in the last five years demonstrate the effectiveness of hybrid aluminum tooling.
• A PP wheel liner for the Honda Civic measuring 44 inches by 13 inches by 24 inches was produced in a two-cavity 13-drop tool manufactured by Unique from the largest block of forged Alumold from Alcan ever cut for a production injection mold (70 by 52 by 31 inches). The tool project has run 290,000 cycles since October 2013 while trimming cycle times by 50 percent compared to the steel backup tool.
• A PP kick panel with a leather texture for the Accord model has run 2.18 million cycles on a QC-10 aluminum/steel tool as of September 2014. It achieves a 20 percent cycle time reduction over the all-steel backup tool, with minor production issues (flash) similarly seen with a steel mold.
• A PP instrument panel cover for the CRV model successfully completed its four-year project run of 875,000 cycles, concluding production in May 2013. Basic maintenance and repair were required for the scope of production, which trimmed cycle times 30 percent.
• Honda's first major foray into aluminum tool production was for a PP rear deck tray with a leather texture for the Accord. The part has run more than 886,000 cycles over five years on a QC-10 aluminum/steel tool with a 20 percent cycle time reduction versus an all-steel mold.
Honda's confidence in aluminum tooling as a way to improve part quality while saving money has grown significantly. Since 2007, every car Honda has built in North America includes a current or concluded program for parts built on a hybrid aluminum tool, says King. The company has commissioned aluminum tooling for additional products from Unique and other toolmakers. (See related Q&A with Honda's John Engle on Page 25. Unique Tool says other automotive OEM companies are climbing on board.
"GM is now moving forward with aluminum tooling and Nissan started a program with aluminum tooling in 2013. Several parts for a Chrysler minivan model in production on hybrid aluminum tooling from Unique have already surpassed several hundred thousand shots of material over the last few years," says King.
John Caccese, Unique's marketing director, says aluminum is poised to assume a larger piece of a market "tremendously reinvigorated" with numerous tooling programs associated with the release of new models.
"There has been a dip in programs from 2009 through 2013 but many new programs are now active or scheduled to come on line. Auto builds are now beyond 2008 levels," says Caccese. The majority of the programs will be steel due to the industry's comfort with it, but aluminum has a place.
Different not difficult
Unique developed new ways of designing tools specifically for aluminum, taking into account the expansion and conductivity difference to steel. Parting lines, the periphery of the part, locks and other considerations — such as cooling lines that need to be designed and placed in the tool differently — impact the life of the tool, says King.
Unique Tool also developed proprietary welding techniques that allow the molders to perform maintenance in their own shops. Tools with damaged textured surfaces can be repaired/re-textured successfully with a freeze plug process that does not leave a witness line. Laser welding can be used for larger repairs.
Aluminum tooling can be used with existing hot runner technology, and simulation software suppliers have no difficulty modeling material flow with such tooling. Unique Tool has partnered with suppliers of both technologies. It has worked with its clients to test and set the operating guidelines for presses that normally use steel molds.
"The higher thermal conductivity and rapid heat transfer means resins flow and set up faster, and you inject faster but with reduced pressures. There are fewer hot spots in the tool, cycle times are shorter, and the parts come out with fewer stresses. Aluminum tools should not be over-clamped, which can close up parting lines and vents. The tool should be opened and wiped down after each shift to remove any residue that might build up due to gases," says King.
Mikell Knights, senior correspondent
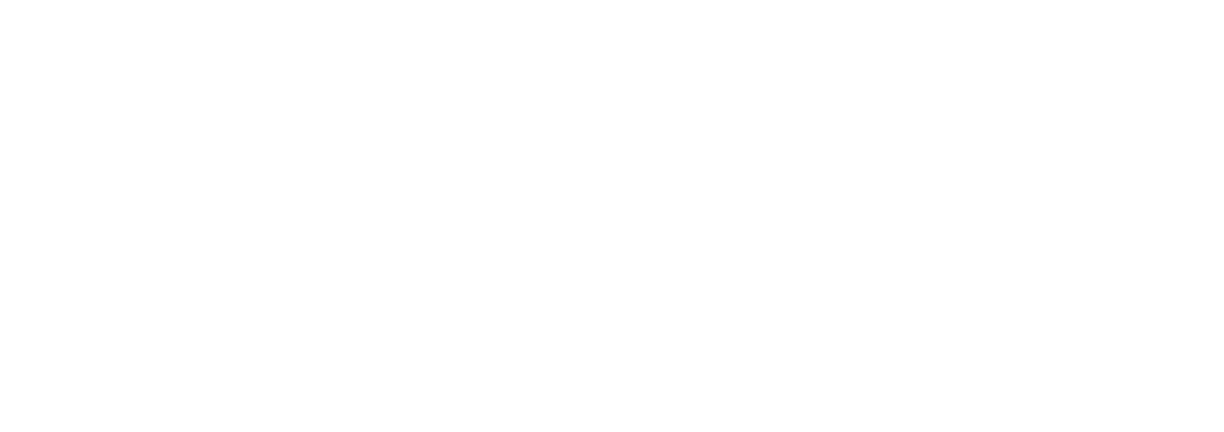