Uniloy innovates blow molding through parent firm's expertise
Uniloy Milacron Inc., the Tecumseh, Mich., blow molding division of Milacron LLC, is leveraging the parent company's extensive know-how in injection machinery, hot runner designs, high-cavitation molds and co-injection processes and combining that with its own blow molding expertise to develop new technologies and applications including those for multilayer barriers and extended shelf life.
Uniloy is the world's largest manufacturer of injection blow molding and reciprocating screw, continuous and accumulator extrusion blow molding machines. Its latest activities reflect Milacron's overall strategy to focus on new, unique combinations of equipment and complete turnkey systems by revamping product development programs and reorganizing and retraining sales and marketing staff to sell any of the equipment in its arsenal. That arsenal includes hot runner systems manufacturer Mold-Masters Ltd., Georgetown, Ontario, acquired in 2012, and Kortec Inc., a Rowley, Mass.-based supplier of co-injection systems acquired in 2013.
Milacron also redesigned its global marketing and sales strategy to encourage technology crossover (see PMM November 2014, Page 80).
Last year, Milacron partnered with Big 3 Precision Products Inc., Centralia, Ill., a toolmaker and manufacturer of injection blow molds, to develop high-cavitation tooling based on the collaboration of technologies from Uniloy, Kortec, Mold-Masters and DME Co., Madison Heights, Mich. Big 3 Precision established a technical center at its Millville, N.J., facility to create turnkey Uniloy UIB injection blow systems.
David Skala, group VP for Uniloy Milacron, says the combined efforts have been fruitful. A co-injection, injection blow molding system featuring technology from Uniloy, Mold-Masters and Kortec, including a Mold-Masters E-Multi auxiliary injection unit, became commercially available last year.
The turnkey co-injection work cell produces small personal care and medical bottles while operating with high cavitation (16- to 30-cavity) molds. The cell has tested barrier applications that proved successful using combinations of cyclic olefin copolymer/nylon/COC, PC/nylon/PC, and PP/EVOH/PP.
Turnkey work cells for monolayer applications are also available that include Mold-Masters' Axiom hot runner system featuring its iFlow balancing brazed manifold technology with high cavitation molds from 16 to 40 cavities, says Eric Hallstrom, sales manager for new business development.
Turnkey injection blow molding work cells can also include all of the requisite auxiliary equipment, including a Mold-Masters TempMaster hot runner controller and Milacron-branded dryers, mold water heaters and oil-heating units, as well as downstream bottle inspection, leak-testing and conveying systems.
MACHINERY AND PROCESS
DEVELOPMENTS
Milacron's injection molding machinery segment offers various drive technologies for the injection unit, mold carriage or clamping unit that are currently being evaluated for blow molding, says Hallstrom.
"All-electric systems with direct drive or ball screws, or hybrid designs that utilize servo-driven hydraulic pumps or feature separate electric and hydraulic drive technologies are candidates for every blow molding machine model," says Hallstrom. "We have numerous technologies within Milacron to select from, and we will carefully evaluate each type and match it with an appropriate blow molding application."
In injection blow molding, new developments stem from the co-injection of bottles for medical and pharmaceutical rigid packaging that replace glass. Emerging multilayer applications include multilayer injection blow molded structures that deliver barrier performance, hide lower-cost materials in middle layers, or extend product shelf life.
Uniloy is adapting multilayer barrier co-injection nozzles and manifolds from Mold-Masters and Kortec for its injection blow molding machines. Processors can purchase a machine from one source with the technology fully integrated.
"Co-injection is a tremendous opportunity for a three-layer container to displace a glass container. The approach opens up applications we would not have had without the Uniloy, Kortec and Mold-Masters technologies," says Skala. "The proven technology gives us the confidence that we can hold extremely tight tolerances."
Uniloy's clean-blow sterilization technology for longer product shelf life, its three-layer bottle blowing technology for light barrier and its neck-to-neck high-cavitation technology are being used in combination with each other or applied to different blow molding machine types for the very first time.
"Uniloy three-layer capability for HDPE dairy light-blocking applications is now available for use with bottles produced on our reciprocating extrusion machines," Skala said.
Clean-blow, Uniloy's three-layer bottle blowing technology and its neck-to-neck technology are suited to drinkable yogurts and other liquid food applications, Hallstrom says.
The clean-blow process yields a small sterile container (about 8.5 ounces and under) that is sealed after molding and then delivered to the aseptic filling line. Clean-blow sterilization can extend shelf life 40 to 60 days.
Sterile air is used to blow the bottle, which is then sealed. The sealed bottle can be shipped to the bottler, which automatically trims the sealed container in the aseptic area just prior to filling it. This sealing process that takes place directly after blow molding the container keeps bacteria and contaminants from getting into it before filling, and does not require a separate process for sterilizing the inside of the extended-shelf-life bottle before filling it.
MACHINERY UPDATE
The UMIB line of three-station injection blow models (45 to 200 metric tons) being manufactured in 2015 by Uniloy Milacron srl, Magenta, Italy, will adopt the UIB name used for the U.S.-made injection blow molding machine models. Controls and drives for both the Italian- and U.S.-made machines will resemble each other more closely in type and capability.
Uniloy has expanded its lineup of injection blow machines with the introduction of the UIB 100.EZ, its first all-electric injection blow machine that offers an electric rather than a hydraulic screw drive and an all-electric clamp unit.
The machine, unveiled at K Show in 2010, found its first buyer last year, a European customer, says Skala. Uniloy plans to expand its lineup of all-electric machines, but the pace of the rollout will be based upon performance and upon customer needs and payback.
Uniloy also developed a hybrid approach for larger-sized machines in the UIB line — the UIB 199-3, introduced in 2014 and featuring a direct drive electric AC motor for screw recovery and a hydraulic clamp. This allowed the company to reduce the motor size from 125 horsepower to 30 HP, and trim the size of the hydraulic reservoir from 375 gallons to 100 gallons for the hydraulic power pack. Energy savings are approximately 30 percent for a 200-gram (7-ounce) shot size compared to the previous hydraulic model. Injection control on the UIB 199-3 has been improved by adding servo valve controlled injection versus the previous proportional valve control.
The design resulted in highly repeatable shot control desired for lightweight applications, says Skala.
The UMS line of continuous extrusion shuttle blow molding machines — produced in Italy and in Germany — is being evaluated with an eye for integrating the best technologies from each line into a more consistent product offering. Uniloy's blow mold operation in Tecumseh is central to its turnkey strategy for shuttle machines built currently in the Czech Republic, Italy and India.
Three-layer container production is new to the company's reciprocating extrusion blow molding line, but Uniloy offers multilayer shuttle machines capable of producing parts with up to seven layers. Such a machine operates at the new 15,000-square-foot technical lab at Uniloy's Tecumseh headquarters. The machine is used for light-blocking, oxygen-barrier applications, and customer container development.
Uniloy's UA line of accumulator blow molding units for large-part applications — intermediate bulk containers up to 330 gallons — previously comprised two product lines, one mainly focused on European customers, and one on North American customers, says Skala.
"With the globalization of Uniloy over the past year we are in the midst of combining the best technologies in accumulator head machines supplied through our Magenta, Italy, location," says Skala. "Multilayer applications for intermediate bulk containers and other large-barrel applications is a focus."
A servo-hydraulic version of a UA is likely the next step in the machine's design but the payback has to be confirmed in order to justify the higher machine cost, says Skala.
ADVANCING ESL, STRUCTURAL FOAM
Uniloy launched its UR65 reciprocating screw extrusion blow molding unit with multilayer technology in 2010 for a dairy customer making a container with three layers of HDPE for a light-blocking, extended shelf life application.
"It can be combined with our clean-blow technology to give a sealed sterilized bottle directly to a dairy filling line. Uniloy has sold just a few of these units, but in 2014 the market seemed to be growing," says Hallstrom.
The first application for UR65 spurred development of the first multilayer head for a reciprocating screw machine.
In dairy bottle production, there was a drive for material savings by using calcium carbonate in compounded form as a low-cost approach to displace HDPE. Calcium carbonate concentrate mixed with the HDPE, which made the container slightly heavier, reduced plastic consumption by 7 percent, says Skala. Calcium carbonate in concentrate form acts as a lubricant and lowers energy consumption while providing a cycle time benefit, says Skala. Uniloy has done testing with Heritage Plastics, Atlanta, and Omya North America, Cincinnati, he said.
Uniloy's latest development for structural foam molding is its Smooth Gate nozzle tip technology introduced in 2014 to improve gate quality by minimizing gate vestige or stringing.
Smooth Gate is used with Uniloy's structural foam, external modular valve gate hot runner system that provides a surface finish at the gate that was not previously possible. The nozzle tip helps improve the look of the part with better cosmetics in gate areas.
At least six customer trials of the nozzle tips in different applications are showing vast improvements, says Hallstrom. The nozzle tips are now available for new machines and as an aftermarket product for existing customers.
Mikell Knights, senior correspondent
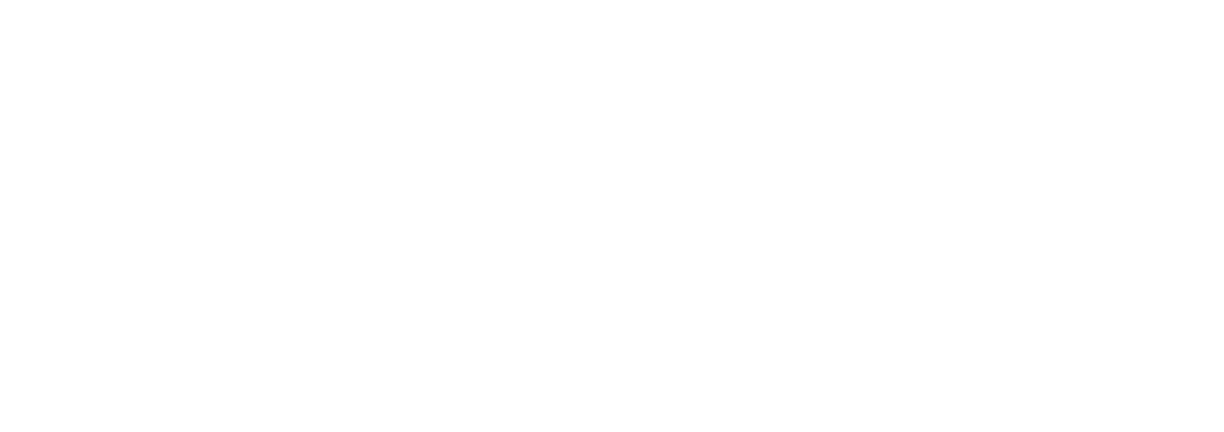