Marglen Industries Inc., Rome, Ga., is a specialist in manufacturing fibers used in carpet, fiber fill, needle punch nonwoven and other textiles products, using 100 percent post-consumer PET flake derived mostly from recycled beverage bottles. Besides an array of bottle washing equipment, granulators, extruders and screens, Marglen's in-house recycling operations use eddy current separators to remove virtually all the aluminum — originating from beverage cans and other non-ferrous materials — from its PET flake.
Originally a carpet manufacturer, Marglen began producing a polyester fiber after purchasing recycled PET flake from an outside merchant. It subsequently added a bottle washing and grinding plant and provides annual PET recycling capacity of about 90 million pounds. Recently Marglen began providing about 30 million pounds of LNO food-grade resin per year.
To meet heavy demand for its polyester fiber, Marglen still purchases some recycled PET flake from outside vendors to complement its in-house bottle processing operation. All the PET flake, of whatever origin, that is to be put through Marglen's fiber extrusion operation undergoes a rigorous cleansing and decontamination system designed to ensure clean flake. To do that, Marglen relies on Model REA eddy current separators (ECS) from Eriez Magnetics, Erie, Pa.
Marglen has several ECS machines and added a 60-inch concentric ECS unit during its recent plant expansion.
The ECS machines are considered an integral part of the PET cleaning and recycling system. This is one of the final steps before the flake goes through quality control testing and then into storage silos.
Removing aluminum is very important because it eliminates problems in the downstream extrusion process. Too much aluminum scrap in the system requires frequent screen changes at the extruders and that causes down time issues. An internal quality control lab checks for contamination to ensure that the flake has low levels of metal contamination following processing on the ECS machines.
Marglen purchases baled bottles from material recovery facilities and recycling centers throughout the United States. The bottles are washed in a chemical solution that removes the labels and glue. The bottles pass through an ECS to remove larger pieces of non-ferrous metal (aluminum, brass and copper). The clean bottles are then transported via conveyors to automatic sorting equipment and separated by color and type. They are manually processed one final time to ensure that they have been sorted correctly.
The sorted bottles are conveyed to granulators and ground into three-eighths-inch raw flake. An additional process removes any lingering paper, labels closures, seals and tabs, though the PET flake may contain some fine aluminum particles. The flake is transported by conveyor through either a 48-inch or 60-inch ECS unit.
Through the induction of eddy currents and the resulting repelling forces, the magnetic field repels the aluminum and physically separates it from the plastics regrind, minimizing PET flake loss. When the polarity of the magnetic field generated in the aluminum by the ECS is the same as the rotating magnets, the aluminum is repelled from the high-speed rare-earth magnetic rotor. This causes the trajectory of the nonferrous metal to be different than the PET flake. The two streams of material are separated by an adjustable splitter in a simple, high-volume, and effective manner.
The eddy current rotor is the heart of the separator. Eriez offers several eddy current models that are ideal for removing aluminum contaminants from PET bottles and flake, the application that is critical at Marglen.
In this case the Eriez concentric rotor uses powerful rare-earth magnets curved to fit for maximizing the magnetic field strength. The powerful, high-frequency rotor is effective at removal of small and medium nonferrous metals from PET flake.
The ECS units have helped Marglen obtain a single-pass aluminum reduction of up to 93 percent and achieve a clean PET yield of 97 to 99 percent. Most of the flake has an aluminum content of zero to 50 parts per million after it comes through the ECS system.
Eriez' latest ECS machines also feature a new high-speed bearing design that creates a 30 percent higher rotor speed for added PET flake purity. The bearings can last up to 15 years with proper maintenance.
Merle R. Snyder, senior correspondent
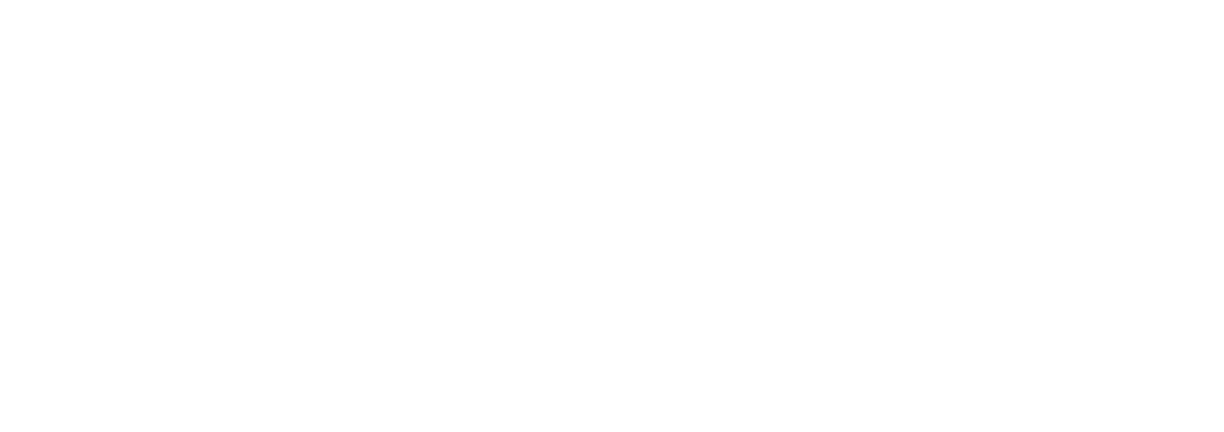