Equipment advances and innovative-technology partnerships are driving light-weighting opportunities for the MuCell process in new automotive, packaging and consumer product applications.
MuCell microcellular physical part foaming technology — a patented process and equipment technology commercialized 15 years ago by Trexel Inc., Wilmington, Mass. — involves delivering precisely metered quantities of atmospheric gases (nitrogen or carbon dioxide) in a supercritical state to a molding machine's plasticizing unit to create an end product with a microcellular material structure.
Although MuCell is widely recognized as an alternative to exothermic or endothermic chemical blowing agents for light-weighting parts while retaining mechanical properties, certain barriers have kept significant market segments from investing in the technology, according to Steve Braig, Trexel president.
But the company is extending MuCell into a number of new applications, including automotive, packaging and consumer product projects, for injection molding and blow molding.
Other firsts are flow simulation modules that model the flow behavior of a MuCell part and the ability to use finite element analysis to conduct a structural analysis of the foamed part.
NEW DOSING UNIT
Some 98 percent of applications currently use nitrogen. Trexel hardware controls the generation of the gas into a supercritical fluid (SCF) and its dosing into the primary equipment. The equipment comprises an SCF metering system and a processing machine fitted with an SCF injector, non-return valves at the front and rear of the injection unit, and a shut-off nozzle on the injection barrel.
With Trexel's new equipment development, called the T-Series, an SFC dosing and delivery system replaces the Series II system, which required a continuous flow of SCF production. In the T-Series, the SCF delivery system converts gaseous CO2 or nitrogen into a supercritical fluid and then, on demand only, precisely injects the fluid into the injection press. In doing so, the T-Series technology reduces energy consumption, and it extends the seal life on the booster pumps by eliminating the need to mount an interface kit on the injection unit.
Also new, the T-Series' simplified controls require only the shot weight and percentage of SCF content to be entered; the system calculates all other parameters and optimizes SCF delivery during screw recovery.
Unlike the Series II control, which is static, the T-Series control is dynamic, automatically responding to changes in molding parameters for consistent delivery of the exact dose of SCF. T-Series is offered in four models, which handle shot sizes from 10 grams to more than 12 kilograms, or 26.5 pounds.
Here are a few of Trexel's new applications:
BLOW MOLDING:
AUTOMOTIVE
Following two years of developmental work, ABC Group, a Tier 1 automotive supplier based in Toronto, has started commercial production of a reinforced polyethylene air duct for an under-the-hood application. The air duct, produced on an accumulator blow molding unit, has a shot weight of 11.5 ounces. Wall section thicknesses range from 1.5mm to 2mm.
The Mucell process achieves a 41 percent reduction in material density, resulting in a 34 percent net weight savings for the finished part. Non-disclosure agreements prohibit Trexel from divulging the number of MuCell-ready blow molding machines in commercial production; however, two blow molded automotive parts will appear in 2016 model-year vehicles.
LIGHT-WEIGHTING:
MUCELL AND GLASS BUBBLES
Combining 3M's Glass Bubbles iM6K and the MuCell process reduces cycle times 15 to 25 percent, leads to predictable and repeatable part geometry and allows for the use of lower-cost resins without the loss of critical performance requirements.
A conventional part can typically be light-weighted to about 10 percent, separately using either the 3M Glass Bubbles or MuCell foaming technology. However, when combined, the two technologies complement each other, allowing for part weight reduction up to 20 percent.
An automotive program with MuCell and Glass Bubbles iM6K is currently underway in Europe, with development initially targeting an engine cover.
THIN-WALL PACKAGING
WITH 3D IML
"Many people are not aware that MuCell can also be used in thin-walled packaging for reduction in material use," says Braig. Early last year Trexel commercialized its MuCell 3-D in-mold labeling process for packaging applications.
The process creates the look of embossed labeling on the package and does not require additional tooling.
In injection molding packaging, nearly 90 percent of the part cost is derived from the material cost. A 6 percent to 7 percent decrease in material use draws an immediate piece price reduction, says Braig.
Mikell Knights, senior correspondent
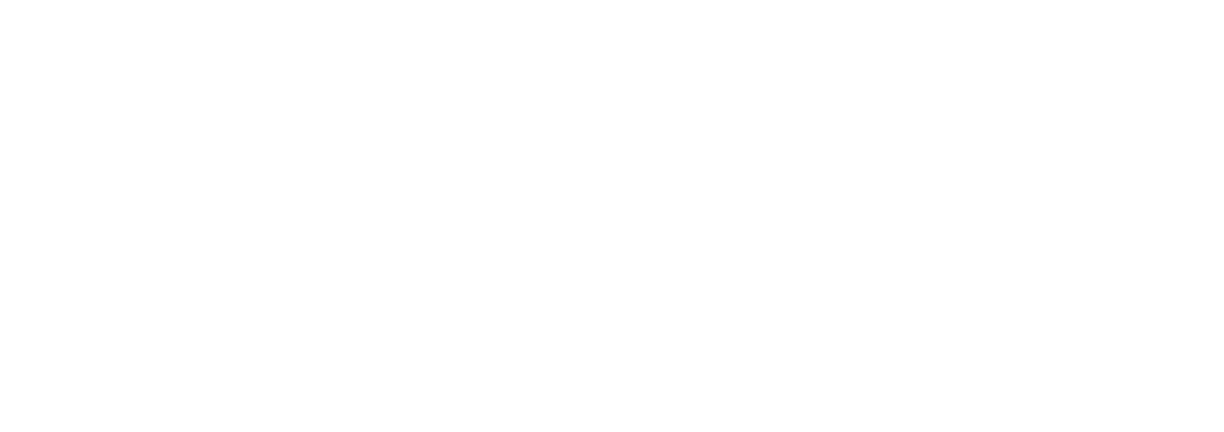