Manufacturers of plastics sheet extrusion lines and their processor customers are constantly figuring out how to serve the wildly diversified and ever-growing variety of end-use markets and applications for extruded sheet. Major consumers of plastic sheet include cars, trucks, planes and trains, along with medical technology, building and construction and technical products. The lion's share goes for packaging, which accounts for roughly half of all extruded plastics sheet, and much of that is thermoformed into the packages found at the supermarket.
Each of those market segments is actually a gallery of many different extruded sheet applications. They vary by end use, material (or multiple materials), surface texture, being more or less rigid, appearing crystal clear, totally opaque and every gradation in between — the differences are endless.
Along with that, the processors are searching for ways to differentiate themselves from commodity suppliers. When an idea strikes, the first thing they do is call the extrusion machinery supplier: "How can we do this?"
Sheet extrusion machinery suppliers don't merely cope with this overload; they thrive on it. It drives their product innovations, and with the demand for extruded sheet growing in many end markets, the innovations are about as varied as the processors and end markets.
Capacity utilization points to growth
"At the onset of the recession plastic products production dropped 17 percent, and capacity utilization hit a low of about 60 percent," said Gina Haines, VP and chief marketing officer at Graham Engineering Corp., York, Pa., which acquired sheet extrusion machinery maker Welex in 2013. "As of September 2014," she adds, "capacity utilization is back up to about 80 percent, a level that indicates general overall health for the industry."
During the recession, Welex lines were a more global mix with good activity in Asia Pacific, the Middle East and Latin America. With the domestic recovery, the mix is once again shifting. North America had a significant uptick in the second half of 2014 and Haines feels the industry is in an up cycle that will continue in 2015. Haines said the Welex brand is seeing increasing activity in the industrial sector. Rowmark LLC, Findlay, Ohio, a leading maker of highly engineered plastic sheet, recently bought a Welex Hercules large-format industrial line for making signage sheet. (See this month's On the Factory Floor feature, Page 21.)
Welex is using various technologies to help customers drive differentiation. One example is its coextrusion feed block technology. This technology enables the nine-extruder system running the striped sheet pictured on the previous page for a processor in Europe.
Another example of market-driven innovation is the Welex Converge CTS sheet line, a dryer-less conical twin-screw technology for processors running PLA and PET.
"Converge provides energy savings potential and superior IV [inherent viscosity] retention versus parallel twin-screw designs due to its higher pressure and torque capability resulting in reduced dwell time," said David Schroeder, president and CEO of Graham. "In NatureWorks' trial of the Welex Converge CTW system, they measured virtually no loss of molecular weight through eight passes."
The system can process material with moisture content to 2,500 parts per million. A Converge line running at a rate of 2,000 to 2,500 pounds per hour will pull about a gallon of water an hour out of the material. It is done through venting and by creating a dewpoint in the extruder before a high vacuum is applied through a hole to pull both water and volatiles from the material. Additionally, vacuum is used to pull surface moisture off the material while it is in the hopper.
"Many of the significant technology advances we are making are in the area of controls," said Robert Deitrick, VP of global sales at Graham. "This relates directly to customers asking for better quality and lower cost." It also relates to one of the synergies that has resulted from its acquisition by Graham.
Justin Kilgore, engineering manager with Graham, said his group has worked to adapt the XBM Navigator control system, which Graham has used on its blow molding systems for nearly a decade, and to apply its concept to Welex sheet lines. The result is the XSL Navigator, which now offers intuitive navigation on a Welex line that makes it easy for the operator to set up quickly and work easily with the machine; for example, clear alarm messaging and pop-up diagnostics when there is an issue.
Kilgore said the XSL Navigator's ability to keep people out of the wiring cabinet when they are troubleshooting does even more than minimize a safety issue.
"We're pushing more information to the operator interface, so that what's going on is not only very clear to the operator but also to us so when we need to remotely connect to a piece of equipment, we can clearly see what's happening with the machine," he said.
Kilgore said the XSL Navigator, built on an industrial PC, also satisfies processors that want to take data from a piece of equipment using a client-server architecture and send it directly into the company's enterprise resource planning system.
Multiple markets mean multiple technologies
Steve De Angelis, VP of sales for sheet and foam systems at extrusion and converting systems supplier Davis-Standard LLC (D-S), Pawcatuck, Conn., sees the sheet extrusion business expanding both globally and domestically.
"The bulk of growth from packaging is driven both by new products and increased demand for existing products," he said. Also, D-S is experiencing a rebound in automotive with both new capacity and replacing outdated machinery. The medical sector has seen incremental growth that should continue in 2015.
Other trends De Angelis is watching include the growth of in-line thermoforming, spurred on by ever-larger thermoforming machines that need more sheet.
"Where previously we had 42-, 52- and 56-inch widths we're now seeing 72-inch-wide thermoformers," he said. D-S is addressing this with new and larger extruders and specific feed-screw designs and multiple nipping roll stacks for increased cooling.
Another result of machines growing larger is they become harder to operate from a single point. So D-S is automating things that made operators walk from one side of the line to the other. With its hands-free roll gap feature, an operator cannot only set the roll gap without leaving the control station, but also can be sure the system will maintain that gap.
De Angelis also sees more calls for energy-efficient extruders, to which D-S has responded with direct drive motor technology, low-energy heaters and high-speed extruders.
"The largest trend we see is customer demands for equipment that will run multiple resins without extensive changeovers," he said. "This lets processors move with the resin market to lower their costs."
D-S has customized machinery to handle multiple polymers without extensive changeovers. Sometimes it may need a screw change, but the same length-to-diameter and the same vent location can handle multiple materials. The processor can take advantage of price moves in the resin markets without the machinery being a limiting factor. This flexible machine design gives processors alternatives in uncertain resin markets.
In developing technologies to address current industry trends, D-S has established what John Christiano, VP of technology, says is a filter called "fitness for use." It means the production system has to match up well with the end product, and that entails matching many specific elements.
Taking high-speed extrusion as an example, Christiano says it fits very well into particular market segments, most notably packaging, and it works almost exclusively with PP and HIPS. So high-speed extrusion is not the choice for flexibility. De Angelis says it is like a high-performance race car — it's great at what it is made for but don't take it off the road and into the sand.
High-speed extrusion basically means higher output from an extruder of a given size. Benefits include reduced materials residence time, faster changeovers, energy efficiency from a direct drive motor, and the absence of a gearbox. Screw diameters are 65mm, 75mm and in a few cases 90mm, though the latter has slower rotational speed, with the sweet spot being the 75mm screw. Throughput tops out around 2,500 pounds an hour.
The high-speed extruder is much more compact than a conventional extruder with a similar output. Though it is overall shorter than a comparable normal extruder, a high-speed extruder can be a "long machine" in terms of its L-D ratio, some having an L-D up to 45. They are more expensive than conventional machines but for the right application, the return on investment is there.
Fit-for-use thinking also applies to Davis-Standard's co-rotating twin-screw systems, which work for certain packaging applications: for non-dried materials, high filler content, and in-line compounding when the processor wants different product formulations over a number of runs. The machine is an excellent fit for roofing membrane manufacturers that compound flame retardants and TPO. It gives them tight quality control. A smaller processor will likely do better buying pre-compounded material.
D-S stopped making twin-screw machines years ago and today buys the basic unit from Leistritz Extrusionstechnik GmbH, Nuremberg, Germany, and integrates it into a D-S line.
The MRS multi-rotational screw is another specialized product from D-S. D-S integrates the technology, made by Gneuss Kunststofftechnik GmbH, into its extrusion systems. It works very well for processing non-dried polyester. An ideal application would be running only polyester with a focus on bottles and recycling.
Christiano puts it this way: "There are technological hurdles and economic hurdles. We'll fit them together and make a system that works for the customer." In the sheet business, custom is standard.
Rob Neilley, senior correspondent
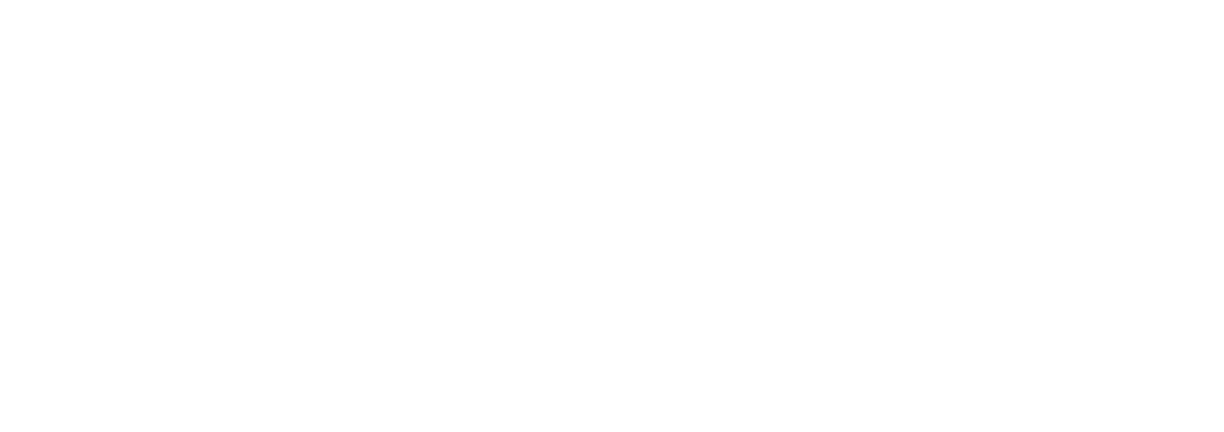