The machine, constructed from aircraft aluminum and polycarbonate windows, allows an object to be printed directly from plastic pellets via FLEX technology. FLEX is an acronym for fused layer extrusion. When this issue of PMM went to press, CEO Slade Simpson said that Sculptify was not yet taking pre-orders but hoped to open them up soon on the company's website.
"We have gotten a lot of interest from a diverse range of parties, with the majority of them being businesses [ranging from startups to large corporations]," Simpson told PMM. "The material selection and reduced cost of ownership our technology provides will really help introduce 3-D printing to many new sectors and industries and also change how 3-D printing is used in existing ones. Businesses really see the value in this, and are very excited about what we are doing."
The materials that have been used by David include ABS, ethylene vinyl acetate, thermoplastic polyurethane and polylactic acid. Sculptify even sells 1-kilogram bags of these resins on its website. Shipping of resin begins in March. Sculptify also is testing HDPE, HIPS, wood composites and nylon.
For the machine, here are some nitty gritty details: Its build volume is 7.8 by 8.6 by 7.3 inches and 496 cubic inches. It has a hopper capacity of 1.25 pounds. Its extruder max temperature is 626 degrees Fahrenheit. For PLA, just for example, its layer resolution is 100 microns but that varies, depending upon the material. The print speed is 10 to 150mm per second. Nozzle diameters are 0.3mm, 0.4mm and 0.5mm, all included. David weighs just 64 pounds and its connectivity is through USB.
Simpson says David's cost is not yet solidified but the projected MSRP is $3,195.
According to the company, using high-quality, high-tolerance parts allows David to print smoothly, quietly and accurately. A unique lead screw design allows for excellent print resolution and consistency. Using a steep-threaded lead screw system provides a great balance between speed, precision, and durability.
Sculptify is bent on using current technology, from releasing its press announcement on YouTube to holding a crowd-funding campaign on Kickstarter Inc. The Kickstarter campaign raised $110,567 on an initial goal of $100,000 with 192 backers.
Crowd-funding may be the latest way to get public attention for 3-D printing, according to a recent analysis by Canalys, a market research firm based in Palo Alto, Calif. In the first quarter of this year, 26,800 3-D printers were shipped worldwide. Of those, 46 percent were purchased by consumers — an increase from 43 percent for full-year 2013.
For information about the technology, contact Sculptify, 740-624-0184, www.sculptify.com.
Angie DeRosa, managing editor
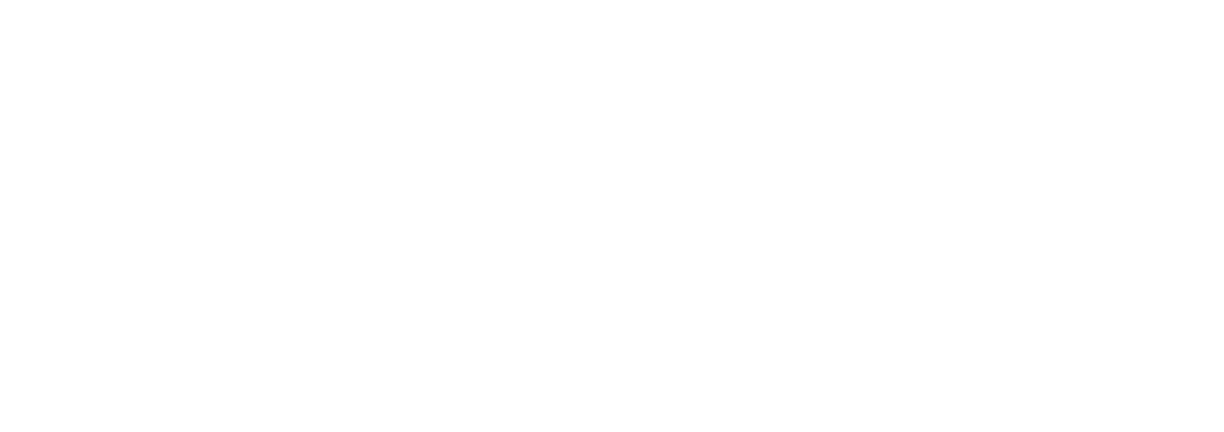